Some of the following companies that manufacture(d) photographic material have already passed by in other parts of the site. Here you will find an overview of companies that marketed photographic material in the nineteenth and twentieth centuries. More is usually known about the best known or the most influential companies than about the lesser known ones; therefore they will be discussed more extensively than others.
The emphasis in this part of the site is more on the ups and downs of the company as such, while in other chapters the emphasis was on the product or on the man or woman who founded the company. The order of all companies is alphabetical.
Below are the names of the companies as will be discussed in this or any other chapter. By clicking on a name (so not on the bullet in front of it), you go directly to that part on this page where the manufacturer in question is located. Scrolling is also possible of course, but this service helps you to get to the desired manufacturer in question much faster.
Due to the fact that this introductory page has become much longer than originally planned and desirable due to the large number of manufacturers, we strongly advise you to use the name service below to go to the manufacturer of your choice on this or any subsequent page.
- General Introduction
- ADOX
- Agfa (see also Gevaert)
- Altissa
- Amaloco
- Ansco Camera Co (see also GAF)
- APM/APeM (see also Soho)
Amalgamated Photographic Manufacturers Ltd - Argus Camera Co, Ann Arbor Michigan
- Arsenal (see Kiev-Arsenal)
- Artima Export Ltd (see also Truvox)
- Asahi Pentax
- Bencini
- BOLCo and E Elliott Ltd
(abbrev. for The British Optical Lens Company) - Carl Braun Kamera-Werk
- Canon Inc.
- J.T. Chapman, Manchester
- The Chicago Cluster of Companies
(consisting of 56 companies ) - Chinon
- Concord Camera Corp.
- K.G. Corfield & K.G. Corfield (Sales) Ltd.
- Coronet Camera Company
- Cosina Company, Ltd.
- Dacora
- Dixons
- Durst
- EHO-Altissa company (See Altissa)
- E Elliott Ltd and BOLCo
(abbrev. forThe British Optical Lens Company) - Ellison Kamra
(see also QRS Devry Kamra Company) - ELOP
- Ensign Ltd.
(distribution Company of Houghton-Butcher) - Ernemann-Kamerawerke AG
- Expo Camera Company
- The FED Company
- Ferrania
- Fisher-Price
- Fodor
- Foitzik-Kamerawerke
- C.F. Foth
- Fototecnica
- Franka Kamerawerk –
- Fujica (Camera Division of Fujifilm)
- Fujifilm (brief history)
- Futura
- GAF (see also ANSCO)
(abbrev. for General Aniline & Film) - Louis Gandolfi
- Herbert George Company
- Gevaert Photo-Producten N.V. (see also AGFA)
- Girard et Cie
- GNOME
- GOERZ
- GOMZ (LOMO)
- Graflex (Folmer & Schwing)
- Great Wall Plastics Co
- W. Haking Enterprises Ltd.
- Hanimex
- Hasselblad
- Healthways
- Houghton–Butcher Manufacturing Co (See also Ensign Ltd. and Ross-Ensign Ltd.)
- R.F. Hunter Ltd.
- ICA AG
- Ihagee (Exakta)
- Ilford
- Imperial Camera Corporation
(see the Herbert George Company story ) - Jos-Pe
- Kamera-Werkstätten Guthe & Thorsch
- Keystone
- Kiev Arsenal
- KMZ
- Kochmann
- Kodak USA (incl. Australia, Canada, France, Germany & the UK)
- Konica-Minolta (Konishiroku)
(see also Minolta) - Kowa
- Krügener
- Kürbi & Niggeloh (Bilora)
- Kyocera (Yashica, Contax)
- Lancaster
- Leitz
- Lensless Camera Manufacturing Company
- Linhof
- Lipca (see also Richter-Tharandt)
- LOMO (see GOMZ)
- Loreo
- Mamiya
- Meopta Optotechnica
- Mimosa AG
- Minolta (see also Konica-Minolta)
- Minox Company
- Miranda (Orion)
- MMZ-BeLomo
- Motodori (Condor)
- Dr. August Nagel Kamera Werke
- Neidig Kamerawerk
- Nemrod-Metzeler (See Healthways)
- Nettel
- Nikon Company
- Nimslo Corporation (see also Nishika)
- Nishika Optical Systems (see also Nimslo)
- Noblex (See also K-W Guthe & Thorsch)
- Olympus Company
- ORION (see Miranda)
- ORWO
- Ottico Meccanica Italiana (OMI)
- Paterson Products Ltd.
- VEB Pentacon Dresden
- Pentax (See Asahi Pentax)
- Petri
- Photavit (Bolta)
- Plaubel
- Polaroid
- Photo Porst
- Karl Pouva – VEB Fototechnik Freital (see also Woldemar Beier)
- Purma Cameras Ltd.
- QRS Devry Kamra Company (see also Ellison Kamra)
- Foto-Quelle
- Rectaflex
- VEB Rheinmetall Büromaschinenwerk
- Richter-Tharandt (see also Lipca)
- Ricoh
- Rollei Germany
- Rollei Singapore
- Ross-Ensign
(continuation from Ensign Ltd.) - Ro-To Company
- Sea&Sea-Sunpak
- Shanghai Seagull
- Sida-Fotofex
- Sigma
- Soho Ltd (see also APM)
- Standard Cameras
- Steinheil
- Stenopeika
- Thornton-Pickard
- Topcon (Tōkyō Kōgaku)
- Tougodo Company
- Traid Corporation
- TRUVOX (see also Artima Export)
- Tura AG
- Universal Camera Corp.
- Vivitar
- Voigtländer
- Vredeborch
- Welta
- Werra (C. Zeiss Jena)
- Wirgin
- Kamera-Fabrik Woldemar Beier (see also Karl Pouva)
- Hermann Wolf GmbH
- Wünsche
- Yashica (see also Kyocera)
- Zeiss Ikon AG
- Zion
- Zunow (Teikoku Kōgaku)
FOUNDERS: August Nagel and Carl Drexler
COMPANY NAMES:
1908: Drexler & Nagel; 1909: Contessa Camera Works Stuttgart; 1919: Contessa-Nettel AG; 1926: Contessa-Nettel merged with three other firms: Ernemann, Goerz and Ica to form Zeiss Ikon; 1928: Nagel left to form Dr.-August Nagel-Werke; 1932: sold his company to Eastman Kodak forming Kodak AG;
COMPANY ADDRESSES:
1908: Stuttgart; 1928: Ulmer Straße Stuttgart-Wangen;
August Nagel was a German camera manufacturer and designer. He was among the founders of Zeiss-Ikon, which he left later to form Dr.-August Nagel-Werke, which he subsequently sold to Eastman Kodak. His most notable legacy is the Kodak 135 film cartridge which remains the world standard for 35mm still-cameras.

Contessa-Nettel AG and Zeiss Ikon
After the war the company grew through innovation and acquisition and acquired the Nettel-Kamerawerke and renamed the combined operation Contessa-Nettel AG.
With this merger the company further expanded and opened additional production locations in the area. This expansion was financed by taking more and more shareholders on board, which eventually led to August Nagel finding himself with less than a controlling interest in the company.
The Carl Zeiss Stiftung (Foundation) held some debts related to lens deliveries and during the economical and financial crisis of 1923 other shareholders sold their shares to the Stiftung, which thus became the controlling entity.
In 1926 Nagel merged Contessa-Nettel with three other firms: Ernemann, Goerz and Ica, and with financial backing from Zeiss, formed Zeiss Ikon. Zeiss Ikon continued to produce camera series of Contessa-Nettel’s and others before merging. Zeiss Ikon used the Contessa name until 1960’s.
August Nagel was director of manufacturing. However, that liaison was short-lived and only two years later, in 1928, he left Zeiss Ikon to form his own firm, Dr.-August Nagel-Werke. By selling his remaining shares he bought the former Schwäbisches Presswerk, renovated the industrial site in Stuttgart-Wangen, and hired many of his former employees.
The inauguration of the new Nagel-Werke took place on April 5th, 1928, and camera sales started in November of that year. With affordable but high quality cameras like the Librette, Recomar, Vollenda, and Pupille, he succeeded in the market even during difficult economical times. Production grew constantly by double-digit growth rates for several years, and thus further expansion was necessary.
August Nagel was born on June 5th, 1882 as the oldest of 9 siblings in Pfrondorf/Tübingen, Germany. Even at a young age he had started constructing cameras. In 1908, together with his friend Carl Drexler, he founded his first company Drexler & Nagel in Stuttgart, to produce photographic equipment. In 1908 they produced the Contessa No. 1 in the 4 ½ x 7 cm format. By 1909, after some quick market success, this would become Contessa-Camerawerke GmbH.
The ever-growing plant developed 23 different models by 1910, to be exported around the world. As a passionate sportsman and balloon enthusiast, Nagel pioneered the development of cameras for cartographic, geographical and military areas. He developed a special balloon camera.
Within a few years the company grew to a few hundred employees; during the First World War the Nagel factory contributed with 500 employees with some aerial cameras and other military equipment.
In recognition of the work on the balloon and aviator cameras, in 1918, the University of Freiburg awarded the 36-year old inventor the honorary title of Doctor.
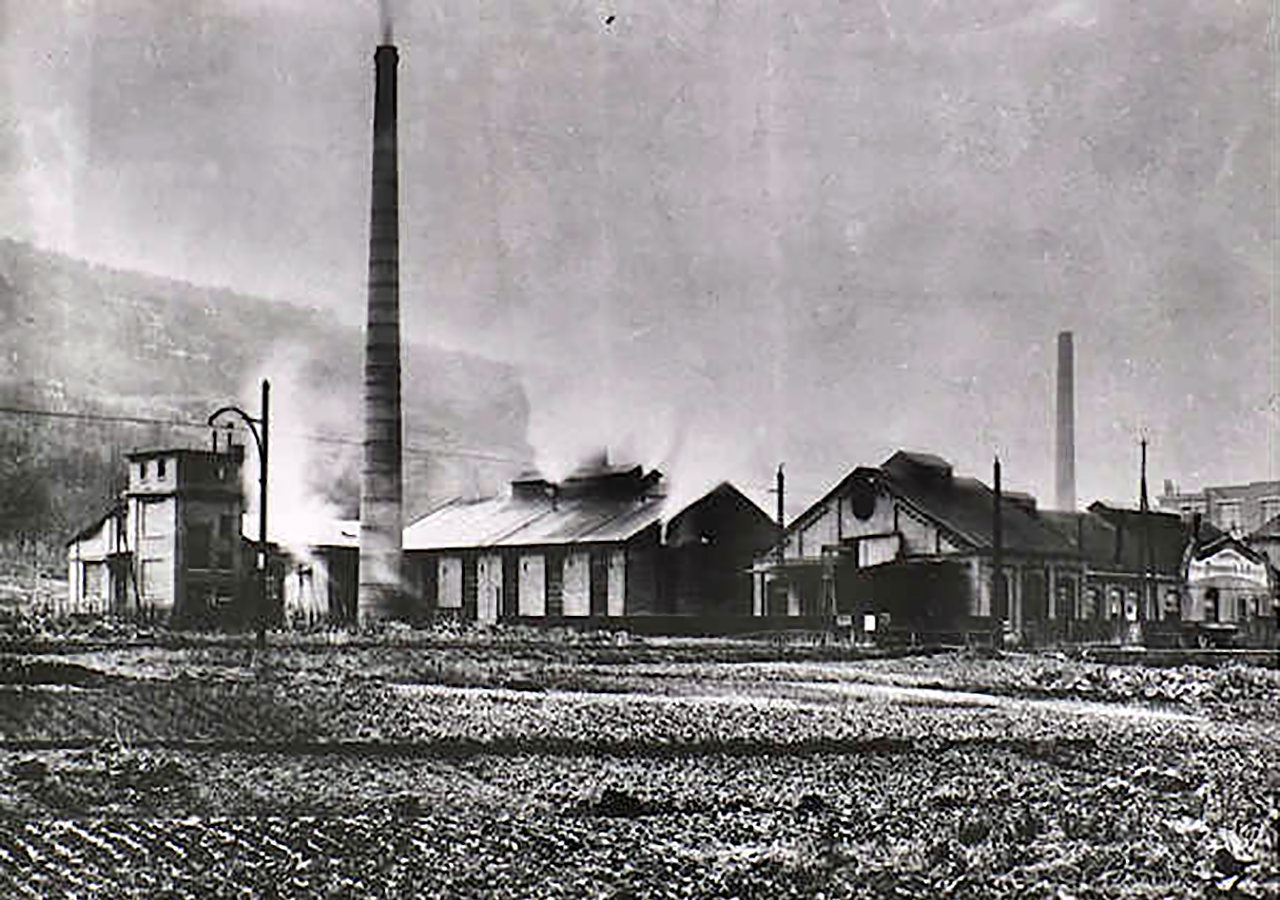
In 1928, Dr. August Nagel acquired an old pressing plant, the former Schwäbisches Presswerk.
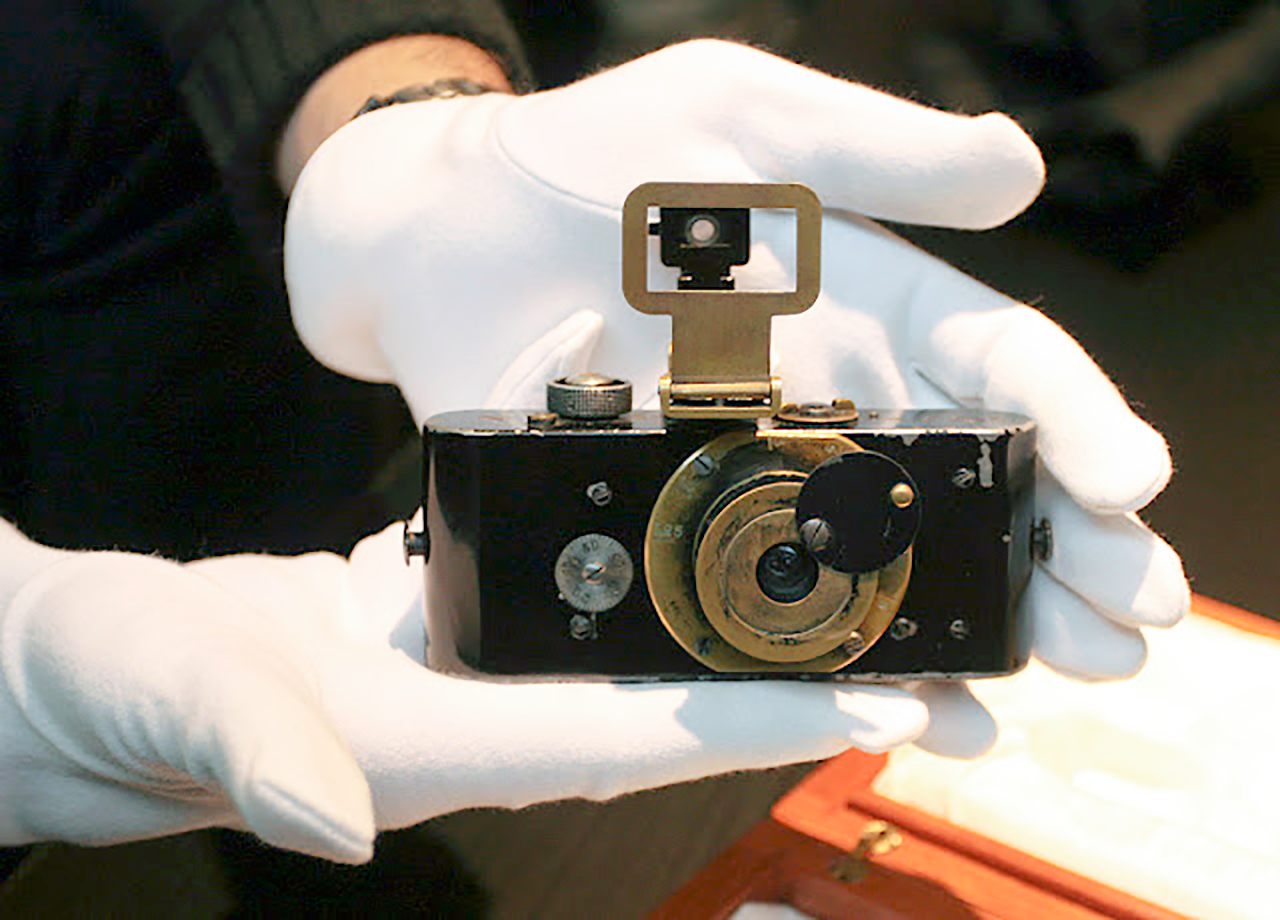
becoming Kodak AG
As a result of this success, at the age of 49 Dr. Nagel got an offer from Eastman Kodak that he could not decline. George Eastman was looking to expand Kodak’s German operations from a simple distributor (since 1896 in Berlin), as well as local film making (through acquisition of Glanzfilm AG, Berlin-Köpenick, in 1927), to also include local camera production.
German cameras at this time were regarded as top of the line, and Mr. Eastman would rather acquire an existing company with a reputation for high quality than establish a new production line with American or UK models. The offer to August Nagel included allowing him to stay as General Manager of the company and continue to develop and produce affordable high quality cameras.
The contract between Kodak and Nagel was signed in December 1931, and from early 1932 on (at the time of the greatest depression in Germany) August Nagel was proud that he was able to continue his expansion, while others had to let go of employees.
The first camera launch with the new Kodak logo was the Vollenda 52, a small folder for 4×6.5 cm images on 127 film. Some existing designs were continued and some new cameras were launched (e.g. the Kodak Vollenda 620 and Duo 620).
The road to smaller film formats
In the early 1930s, the Leica Camera developed by Oskar Barnack became increasingly popular. However, their price still limited the number of pieces. It is reported that up to 1933 only about 16,700 Leicas could be sold worldwide. In 1933, therefore, 35mm photography was still the domain of a number of wealthy amateur photographers and professional photographers.
Dr. August Nagel had been an early adopter of downsizing to exploit the emerging finer grained emulsions. He had produced the Recomar quarter plate cameras while these were still favoured by advanced European amateurs, but he was quick to recognize the advantages of designing cameras around the new roll films.
The Pupille, using 127 roll film and available with a fast f /2.0 Schneider Xenon lens in a helical lens mount, could be seen as a capable alternative to the Ermanox. It also mounted slower Xenar, Elmar and Tessar lenses.
Kodak AG also made at the same time a bellows design for 127 film usually described as the Kodak Vollenda No. 48 with slower Schneider or Zeiss lenses and a more modest No. 52 with only a metal frame eye-level finder and a similar lens selection. The slower lenses were front-cell focusing, while the others had helical mounts.

Dr. August Nagel sold his company to Kodak in 1932
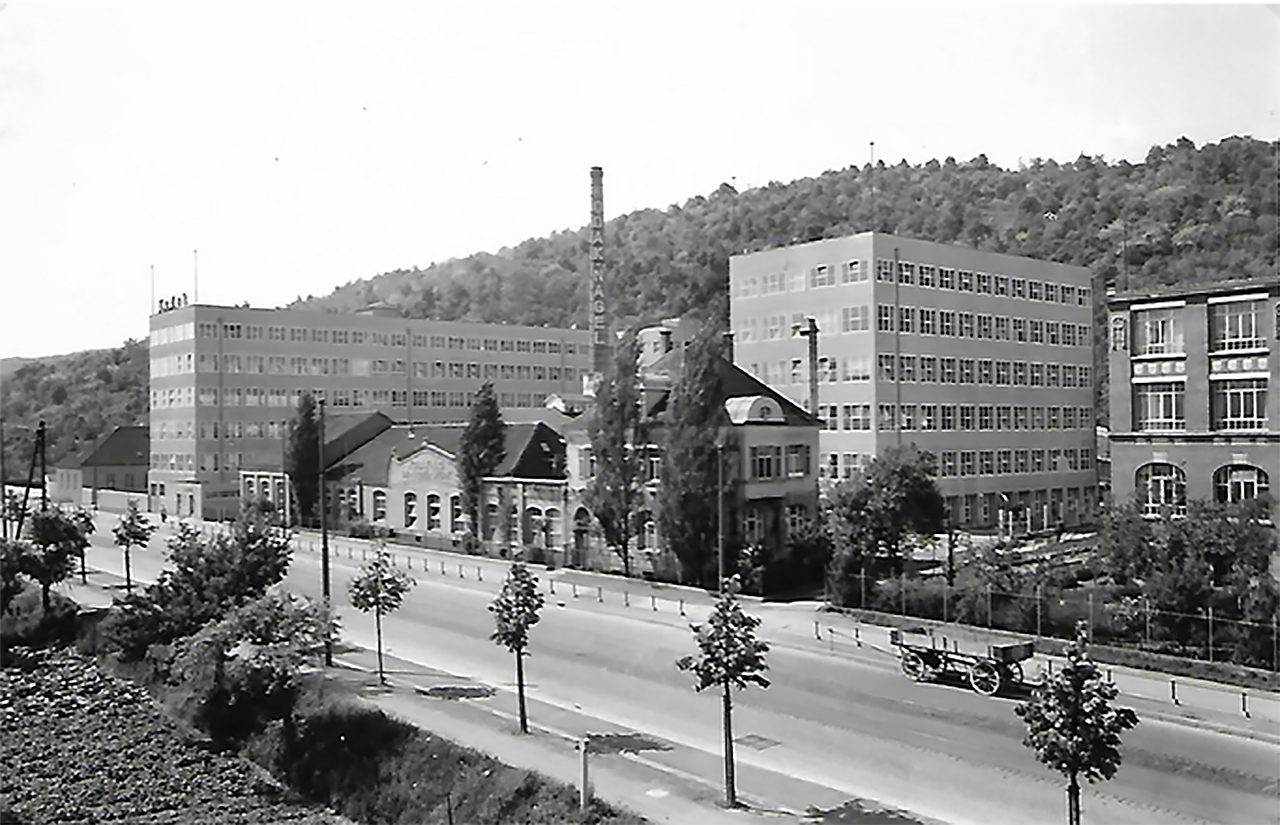
The Kodak August Nagel works in Stuttgart-Wangen, 1942.
Wartime and following decades
In 1941 the camera production stopped and the site switched to arms production for the war.
August Nagel died on October 30, 1943 at age 61. He was spared experiencing the destruction of his work on the night of March 2nd to 3rd, 1944. However, camera production already resumed in 1945 after the war and was the work in Stuttgart- Wangen headquarters of Kodak Germany. The following decades until the late 1960s were even more successful for Kodak AG in Stuttgart.
The biggest inventions that August Nagel contributed to Kodak’s global success, though, were the Retina and the universal 135-film cartridge that became the 35mm film standard that is still used today. From 1953 to 1979 his son Helmut Nagel was Kodak-Werke’s CEO in Germany.
Retina cameras continued to evolve and diversify through the late 1950s when Japanese competition crushed the German camera industry. Though in decline, Kodak AG offered single lens reflex cameras with interchangeable lenses into the 1960s. Later products declined in quality and features, with the last of the Retinas being simple viewfinder cameras with modest fixed lenses. Though not branded as a Retina, the Kodak Instamatic Reflex of 1968 – 1972 was essentially a Retina Reflex with interchangeable lenses, but using the Instamatic film cassettes.
The birth of the Retina
August Nagel took the ambitious plan to develop a 35mm camera for a wide range of buyers. According to his idea, such a popular 35mm camera should be technically as high quality and solid as possible, but should be simply in handling.
Last but not least, the sales price should be significantly below that of the previous 35mm cameras. Due to the financial strength gained and the powerful distribution of Kodak AG, Kodak Retina was presented to the public in July 1934 to the sensational and popular price of 75 marks, which contributed significantly to the success of the 35mm photography.
The comments of the professional world showed that this camera was generally considered as fully constructed. It is all the more astonishing that in the following years Nagel, in the event of an unchanged basic concept, a whole series of important improvements in the construction of the camera and also developed inexpensive versions of the Retina – which came onto the market in 1939 under the name Retinette.
In 1939, the production of a broad camera program at Kodak in Stuttgart was at its peak. In addition to ongoing improvements by the “Retina”, he was able to produce his popular “Vollenda” roll film camera series in many variants, among other things. Within the 1930s production grew constantly and almost 2 million cameras were produced in Stuttgart during this time.

Kodak AG long after the war in the 1970s.
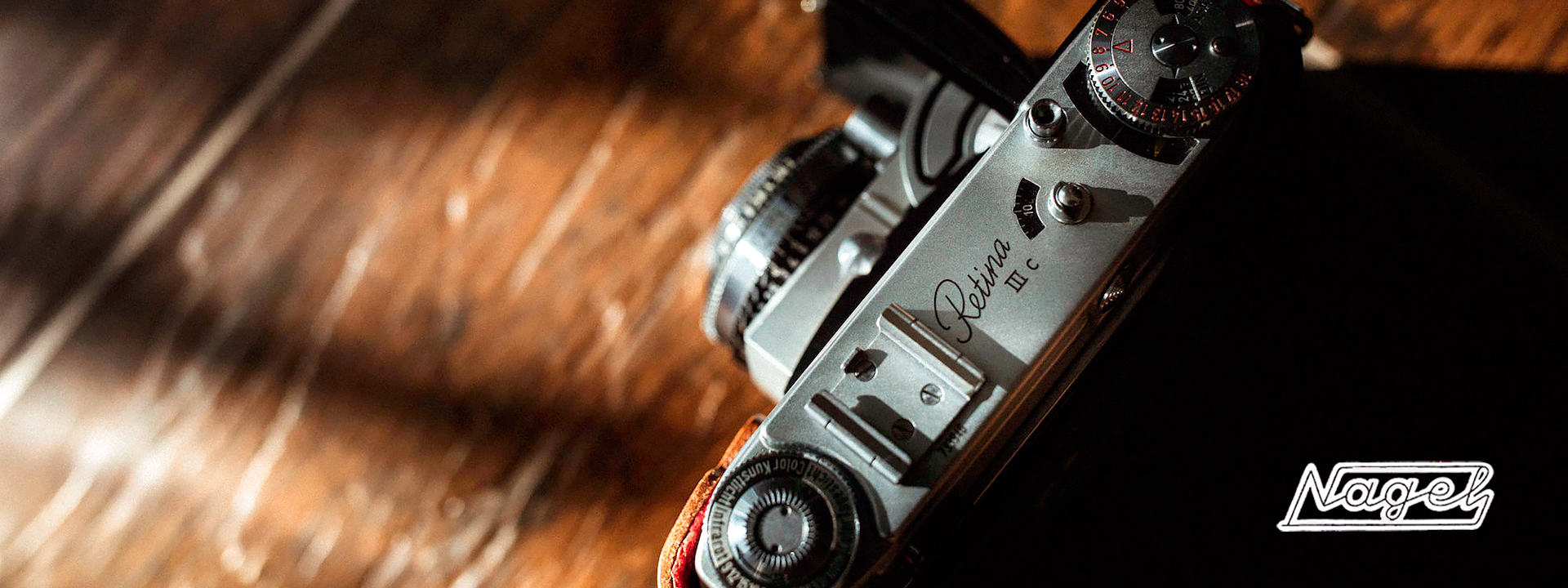
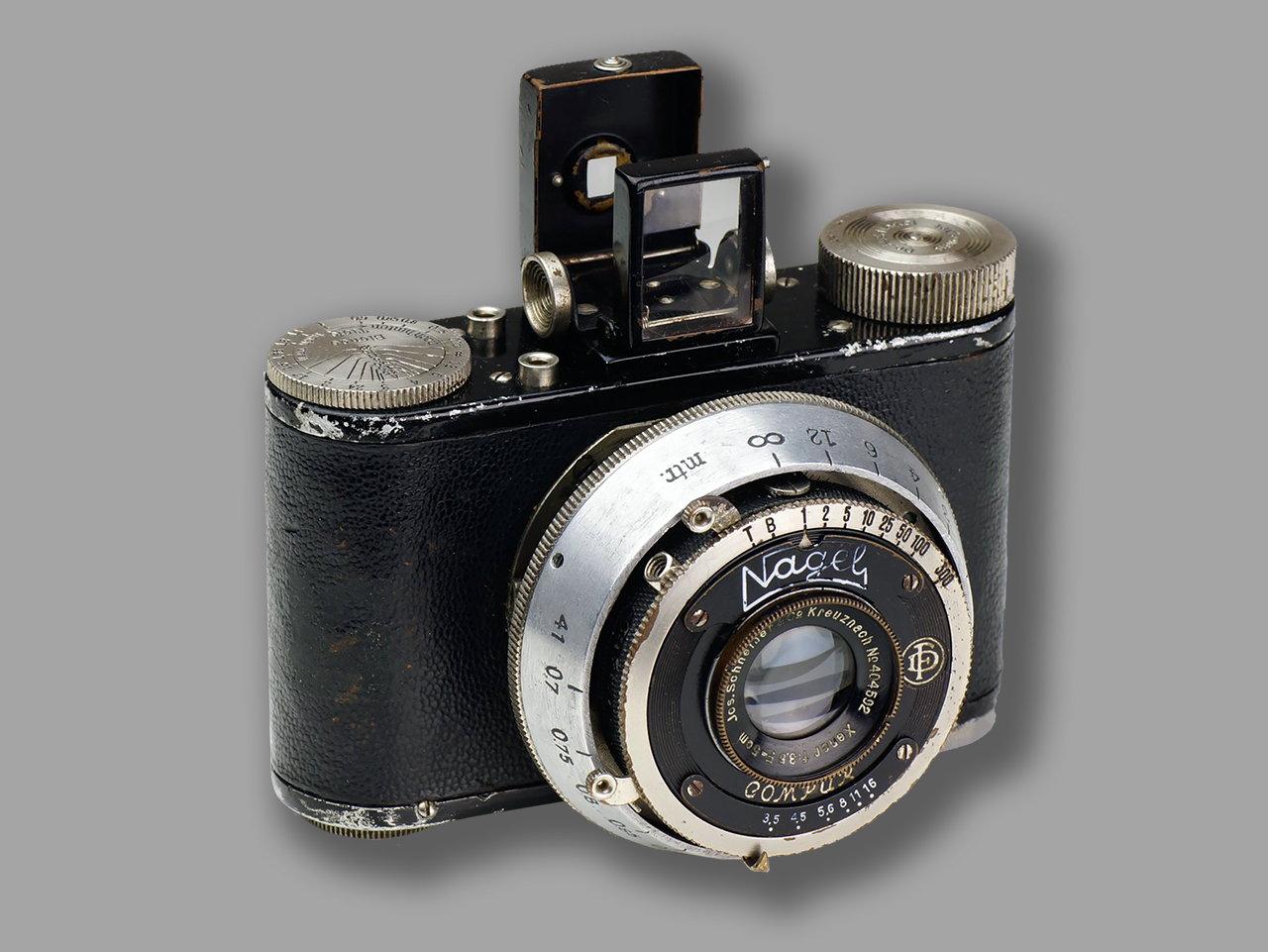
Nagel Pupille with Xenar 50mm f/3.5 lens in Compur shutter. Based on the serial number this camera was built in 1933. Curiously, it has a metal focus ring instead of a black one.

A Nagel Vollenda 48 half frame 127 camera (1929 – 1937). Schneider Radionar 50mm f 3.5 lens and Compur shutter.
127 film Folding
- Triumph
- Librette No. 65/No. 74 (6×9 on 120 film, No. depends on lens and/or shutter combination; 1928-1931; about 4000 units)
- Librette No. 75 (6×9 on 120 film, with Schneider lenses and Compur shutter; 1933)
- Librette No.79 (6.5×11 on 116 film, 1930-1931, ca. 1000 units
127 film vollenda
- The series was introduced with the models 60, 70, and 80 in early 1930. All models were available with a selection of different lenses (Nagel, Schneider or Leitz) and shutters (Nagel, Pronto-S, Compur).
- Some of them continued in production after Kodak took over the company in 1932 as “Kodak Vollenda” with the same model numbers.
- In 1934 the larger roll film types were consolidated into the newly introduced.Vollenda No. 48 (3 x 4 cm), 52 (4 x 6.5 cm), 60 (5 x 7.5 cm)
120 film Folding
- Vollenda No. 68, 70, 72 (6 x 9 cm)
120 film rigid
- Triumph
- Nagel Librette 74
116 film Folding
- Vollenda No. 80 (6.5 x 11 cm)
116 film rigid
- Pupille (3×4 on 127 film)
- Ranca (simpler version of the Pupille)
Film plates
- Anca No.10/No.14 (6.5×9 cm plates, 1928-1934, ca. 2,600 units)
- Anca No.25 (9×12 on plate, 1928-1934, ca. 1,600 units)
- Recomar No. 18 (6.5×9 cm on plate, 1928-1939, 20,250 units)
- Recomar No. 33 (9×12 cm on plate, 1928-1939, ca. 20,000 units)
- Fornidar No. 30 (9×12 cm on plate, 1930-1931, ca. 1,000 units)
- Nagel No. 10, 18, 33
FOUNDER: Richard Neidig
NEIDIG
COMPANY NAMES:
1948: Richard Neidig Kamerawerk;
COMPANY ADDRESSES:
1948: Plankstadt;
Neidig Kamerawerk in Plankstadt specialized in making viewfinder and rangefinder cameras for 35mm film. Furthermore the company produced a series of somehow strange cameras between 1949 und 1953, but partly with some interesting features.

The Townhall of Plankstadt
The various cameras
Neidig Perlux
The first Perlux reached the market in 1949 and was a fairly simple viewfinder camera with wind knob and body-mounted shutter release. It had the name Perlux on the shutter plate as well as on its back. It was available with a range of fixed lenses, but most commonly a Staeble Kataplast or Steinheil Cassar in Prontor-S shutter.
Identical versions were sold as Bower 35 and Adox 35, with the name printed on the shutter plate. It had a small pin next to the wind knob that indicated if the shutter lock was released and the camera ready to shoot.
DeJUR D-1 (Perlux Ia)
The 1952 DeJUR D-1 was a rebranded Perlux Ia, with the name DeJUR prominently visible on front of the cameras top housing. The shutter was a Pronto, which differentiates it from the Neidig Ia, which had a Prontor-S shutter with a larger range of speeds.
Neidig Perlux II
The Perlux II was equipped with an uncoupled rangefinder with a distance dial mounted at the rear. It was very similar otherwise to the Perlux IIa/DeJUR D-3 below, which had a coupled rangefinder instead. Logic tells me that this model would have been sold as the DeJUR D-2, but to be fair I’ve never heard of one.
DeJUR D-3 (Perlux IIa)
The 1953 DeJUR D-3 was similar to the DeJUR D-1 but was equipped with a coupled rangefinder. The rangefinder and viewfinder were separate, the rangefinder provides an enlarged image for accurate focussing, and the viewfinder was used for framing. The camera had therefore two eyepieces at the back. Like on the D-1, the shutter was a Pronto. It was a rebranded Perlux IIa.
Richard Neidig Kamerawerk was a camera manufacturer based in Plankstadt, in the Northwest of Baden-Württemberg, South West and made cameras from 1949 till about 1953. The company specialized in making viewfinder and rangefinder cameras for 35mm film. The early cameras of Neidig are marked “U.S.-Zone Germany” on the back.
From start the company produced its cameras for brands of other companies, known are Adox and the U.S.-brands Bower and DeJur-Amsco. DeJur was an American brand of electronics and photographic equipment, and probably best known for their cine equipment. They sold a small range of rebranded consumer cameras.
Neidig’s own brand was Perlux with quite a distinct body design. A characteristic quality of the camera bodies was their flexibility concerning lens equipment.
The early Perlux cameras were equipped with a fixed lens of Schneider, Laack, Staeble or Steinheil. The series II used M39 interchangeable screw mount lenses which were alike those for Braun’s Paxette M39 screw mount, not usable on Leicas. In 1953 the cameras got a film advance lever. The Perlux II rangefinder cameras had an uncoupled rangefinder, the later Perlux IIa had even a coupled one. The cameras were also sold as DeJUR and Bower in the USA.
the “Revolette”.
It is a combination of two camera bodies with two Prontor SVS shutters and two Objectives. Here shown with two Staeble lenses the Kata 2.8/45mm and the Telexon 5.6/85mm.
In the middle of the camera there are two Galilean finders for both focal lengths. The assembly can be used for taking pictures simultaneous or independently with twin perspectives. When equiped with equal lenses could also be used for stereo vertical pictures.
This camera was shown at 1954 Photokina Köln and was specially prepared for DeJur-Amsco Corporation of New York U.S.A. by Karl Neidig Kamerawerk in Plankstadt Germany, the maker of Perlux cameras.
brief survey of neidig cameras

Perlux Ia with Staeble-Kata 45mm f/2.8 lens, which appears to be the standard lens this camera was sold with. Note the peculiar wind lever.
35mm cameras
- Perlux (1949) (also called DeJur, Adox 35 or Bower 35) in 24×24 and from 1950 in 24×36 format; finder tube on top; with Vario, Prontor or Prontor S Shutter
lens variations: Staeble Kata 2,8/35; Laack Tegonar 3,5/35; Steinheil Sassar 2,8/38; Steinheil Cassar 3,5/37,5; Xenar 2,8/38; Radionar 3,5/38
- Perlux II (1952) (also called DeJur D-1, used Braun M39 lens mount) in 24 x 36 format; uncoupled rangefinder; from 1953 rapid lever advance; with Prontor/Prontor S shutter
interchangeable lenses: Perlux Elan 2,8/45; Tegonar 3,5/45; Staeble Kata 2,8/45; a.o.

A DeJUR D-3. The leatherette around the lens mount is missing, as it still needs some work, including rangefinder adjustment.
FOUNDERS: Robert E. Mayer and Max Körner
NETTEl
COMPANY NAMES:
1902: Süddeutsches Camerawerk Körner und Mayer; 1904: Camerawerk Sontheim; 1908: Nettel Camerawerk; 1919: Nettel was merged with Drexler & Nagel into Contessa-Nettel AG Stuttgart; 1926: the company became part of Zeiss Ikon.
COMPANY ADDRESSES:
1879: Sontheim am Neckar;
Nettel was famous for its patented Nettel strut folding cameras, with focal plane shutters.

Sontheim-am-Neckar
- Adoro
- Alino
- Altura
- Argus
- Ballonkamera Atlanta
- Box Contessa
- Citoskop (stereo TLR)
- Contessa-Nettel Stereo / Capi
- Cocarette
- Contiskop (stereo)
- Costa
- Deckrullo
- Deckrullo-Nettel
- Donata
- Duchessa Stereo
- Duroff
- Duroll
- Ergo
- Fiduca
- Luca
- Minar
- Miroflex
- Multum Panorama
- Multum Reflex
- Multum Stereo
- Nettix
- 533
- Onito
- Onix
- Piccolette
- Recto
- Renata
- Rollco
- B.
- Sonnar
- Sonnet
- Sonny
- Sonto
- Spido
- Stereax (stereo)
- Steroco (stereo)
- Suevia
- Taxo
- Tessco
- Toska
- Trona
- Tropen Adoro
- Tropen Deckrullo-Nettel
- Tropen Sonnet
- Tropen Stereo
- Unitak
- Volupa
- Westca
- Westentaschen Sonnet
Nettel Camerawerk was a cameramaker in Sontheim am Neckar, in southern Germany. The company was founded by Robert E. Mayer and Max Körner in 1902, as Süddeutsches Camerawerk Körner und Mayer. It was renamed Camerawerk Sontheim in 1904, and again to Nettel Camerawerk in 1908. One of the company’s specialties was its wide range of stereo camera models.
It was also famous for its patented Nettel strut folding cameras, with focal plane shutters. When such a camera is unfolded the extension of the scissor struts can be adjusted with a knob or lever for focusing.
The Deckrullo-Nettel strut folders were an improvement on this range of cameras, with a focal plane shutter, which is self-capping, i.e. light tight during tensioning. However, some of the cameras with these shutters were marketed under the type name “Deckrullo”.
(Deckrullo; a combination of the German words decken = to cover and Rouleau=roller blind (original form of Rollo, derived from French: rouleau = roll). The Deckrullo-Nettel and other camera models were continued when Nettel was merged with Drexler & Nagel into Contessa-Nettel AG in 1919; some models were still produced after Contessa-Nettel was merged into Zeiss Ikon in 1926.


Deckrullo Tropical. Tropical version (871 series) was produced in all but the smallest size. Body was polished teak, with nickel re-enforcements on the corners, and had brown leather belows. The Deckrullo-Nettel is a series of wooden-bodied strut-folding plate cameras with focal-plane shutters. They were first made by Nettel Kamerawerk from about 1909, and was continued both by Contessa-Nettel from 1919-26, and after that by Zeiss Ikon until 1938. The Deckrullo was one of the most popular of the ‘press’ camera designs of the pre-1940 period.

A circa 1921-26 Contessa Nettel Altura Nr. 70 9×12 Quarter-Plate Folding Plate Camera. Negative cassettes for 3¼x5½”, 9×12 and 10x15cm plates/filmpacks. The camera has a Compur shutter and Donar Anastigmat 1:4,5|135mm lens.
Focussing: via ground glass or meter scale on the barrel floor, brilliant finder with bubble level. The lens standard can be moved vertically and horizontally. The housing is made of leather-covered wood.
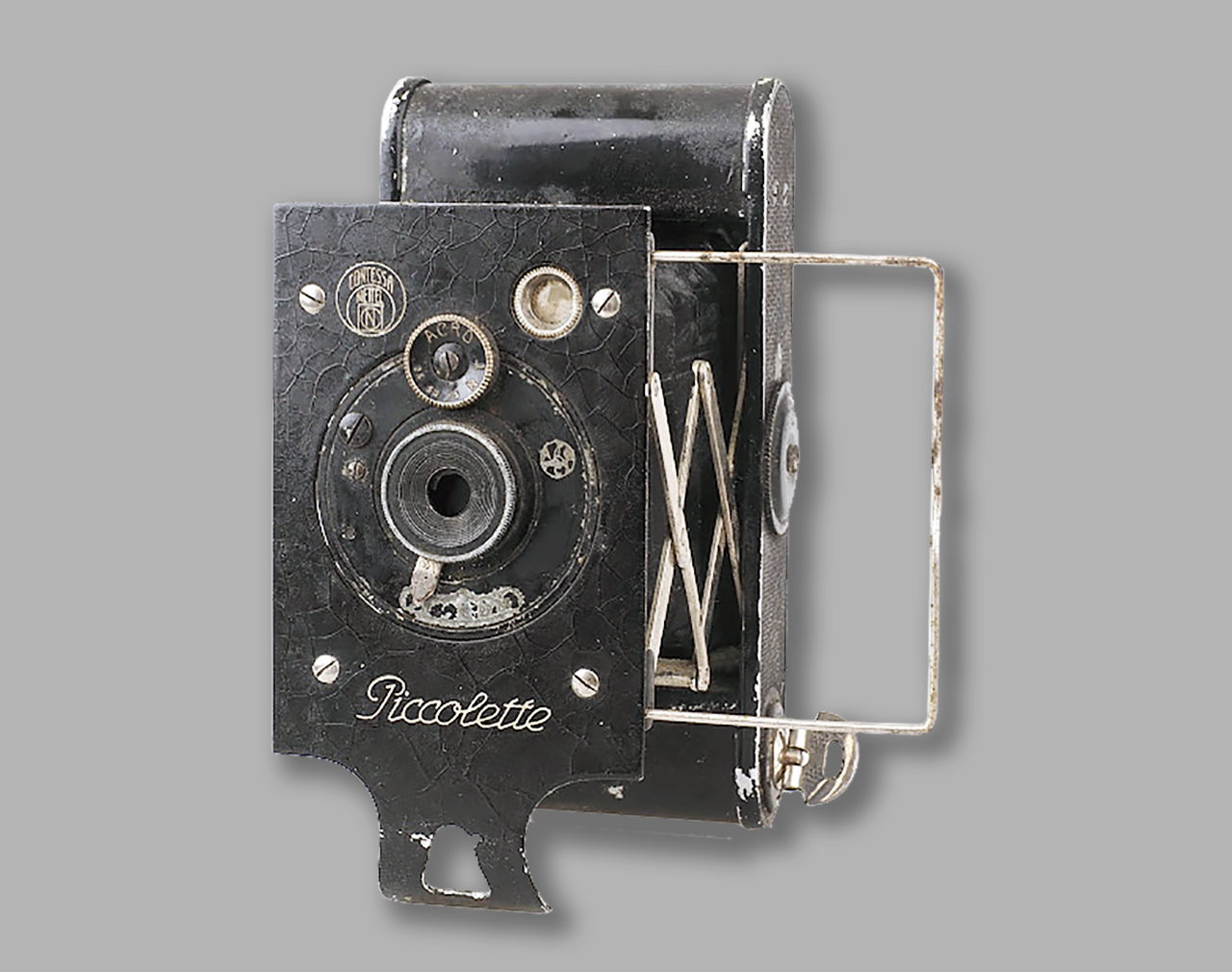
The Piccolette is range of cameras made by Nettel in Stuttgart and its successor companies Contessa-Nettel and Zeiss Ikon. The Piccolette was first made by Nettel as a folding-bed metal camera with leather bellows for 4×6.5 cm exposures on rollfilm, from 1914.
This camera was available with brilliant view-finder, frame finder and various lenses, including Nettel’s own Anastigmat or Rapid Aplanat, and Pronto or Compound shutter. It has radial lever focusing on the bed.

Nettel, Sontheim, Sonnet (Tropical Model).The Sonnet is a range of strut-folding plate cameras made by Nettel Camerawerk from about 1908, and later by Contessa-Nettel and Zeiss Ikon until about 1930. It is a wooden-bodied vertical folder, similar to the metal-bodied Kibitz. The Sonnet was made in several sizes: 4.5×6 cm,[3] 6.5×9 cm, 9×12 cm and 10×15 cm. Standard black and tropical models were made. Most examples have a wire frame finder, with the wire frame hinged on the front standard, and a folding eye-pointer on the body.
FOUNDER: Koyata Iwasaki (president of Mitsubishi)
COMPANY NAMES:
1917: Nippon Kogaku K.K. (Japan Optical Industries Co., Ltd.); 1988: Nikon Corporation;
COMPANY ADDRESSES:
1917: 120 Haramachi, Koishikawa-ku ,Tokyo (present-day Hakusan 4-chome, Bunkyo-ku) in Tokyo;
Nikon Corporation (Kabushiki-gaisha Nikon), also known just as Nikon, is a Japanese multinational corporation headquartered in Tokyo, Japan, specializing in optics and imaging products. Nikon’s products include cameras, camera lenses, binoculars, microscopes, ophthalmic lenses, measurement instruments, riflescopes, spotting scopes, and the steppers used in the photolithography steps of semiconductor fabrication, of which it is the world’s second largest manufacturer.

NIKON IN THE 20s and 30S
In September 1923, the company’s glass research facilities were damaged in the Great Kanto Earthquake and their operations had to be suspended. Recovery was completed by February of 1924, and glass research was then resumed. By March of 1927, 70 major melts and 220 trial melts had taken place. Through such research and much hand work, the company became able to manufacture optical glass of a quality equal to that made outside of Japan.
In 1931, an 8-inch astronomical equatorial refracting telescope was installed in the roof observatory dome on the newly completed Ueno wing of the Tokyo Science Museum.
This was the first full-fledged model of its kind to be produced in Japan. It boasted the largest caliber compared to other Japanese-made telescopes of the time. The telescope is now on permanent display in a zone called the Exploring the Universe located on basement level 3 of the Global Gallery at the National Museum of Nature and Science.
NIKKOR lenses were born of the strong desire of Japanese designers to domestically produce photographic lenses, for which the nation had up till that point been reliant on other countries. Designers went to Europe to observe its optical industry. Finally, after obtaining samples, the designers returned to Japan, which is when the real struggle began.
The company engaged in research by means of disassembly, measurement and assembly experiments following precision aberration measurement testing. After these exercises in trial and error, the company produced its first lens in 1929, the Anytar 12cm F4.5.
Then followed the successful development of a range of lens models, while considering a brand name for these products.
Hence, combining the “NIKKO” abbreviation of the “Nippon Kougaku” company name with the letter “R” often used as a suffix for photographic lens names at the time, the company settled upon the NIKKOR brand name. This name was registered as a trademark in 1932.
As Japan began to modernize in the early 20th century, the challenge was to catch up with Europe. Developing Japanese industry was the pressing need in every field, and it was an especially urgent issue in the optical industry where high technology was crucial.
Nikon began as Nippon Kogaku K.K. (Japan Optical Industries Co., Ltd.) on July 25, 1917, at 120 Haramachi, Koishikawa-ku in Tokyo, starting domestic production of optical instruments such as rangefinders and microscopes.
During that era, the production of advanced optical instruments was a matter of national urgency for Japan. Hence, plans were made to establish an optics company by combining the optical instruments division of the Tokyo Keiki company and the mirror division of Iwaki Glass with Fujii Lens Manufacturing. This merger gave rise to Nippon Kogaku K.K. and, subsequently, the Nikon of today.
In 1918, the company began researching optical glass but suspended operations when it could not fully address several technical difficulties. Thus, in March 1923, to enable parallel research of both the theoretical and the practical, the company built glass research including a 500 kg melting furnace, four cooling kilns and two test furnaces (20 kg and 7 kg capacities).
With advances in optical technologies, eight engineers were invited by the company from Germany in 1921. These specialists included Professor Max Lange, who was a world authority on lens design, Heinrich Acht, who had rich experience in microscope design, Ernst Bernick, a leader in precision instrument technology, and Hermann Dillmann, a specialist in lens design and computation.
The guidance of these engineers had a dramatic effect on improving the company’s technologies.
They also initiated design for development of Nikon’s photographic lenses. To catch up with the level of optical technologies of developed countries, the company started out by imitating, and named its series of lenses “Anytar,” which were designed following the example of the Tessar lens that was the main lens type at the time.
The Japanese designers made improvements after Heinrich Acht returned to Germany. The Anytar 12cm F4.5 prototype was initially completed in 1929. It was then further modified, and by 1931 reached a level where it was no longer standing in the shadow of the original Tessar.

A 500 kg Glass furnace (approx. 1918)
Nikon’s reputation was created after WorldWar II
During World War II the company operated thirty factories with 2,000 employees, manufacturing binoculars, lenses, bombsights, and periscopes for the Japanese military.
After the war Nippon Kōgaku reverted to producing its civilian product range in a single factory. Less than two years after the completion of blueprints in September of 1946, the first Nikon camera, the Nikon Model I, was launched in March of 1948. As Japan experienced post-war restoration and growth at miraculous speed, many of its products were disseminated to the rest of the world.

The first Nikon camera and the first product to bear the “Nikon” name. It was first sold as “Nikon”, but “Model I” was added to the product name to distinguish it from subsequent cameras.The original Nikon I, as introduced in 1948, had no flash synchronization, but was otherwise a fully-fledged up-to-date 35mm rangefinder camera.

Binoculars for the war.
The New York Times article reported:
On December 10, 1950, the New York Times published a special article commending the excellence of Nikon cameras and NIKKOR lenses.
LIFE magazine photographers who had travelled to the Korean War battlefields based this on high acclaim. On the bitterly cold Korean Peninsula, while other cameras were frozen and unusable, Nikon’s worked well and recorded how the severe battles were fought.
“NIKKOR lenses are extremely precise, with high efficiency, and better than German lenses” and “Previous Japanese cameras had only beautiful exteriors, while internal performance was inferior, however, this Nikon camera is intricate and provides beautiful results.“
Because of this, NIKKOR lenses which were equal to German lenses pre-war, achieved the world’s highest class and completely renewed the image of “Made In Japan” which had previously been “cheap and bad quality”. As a technology-intensive nation, Japan started here.
The legendary SP-series
The signature and legendary Nikon SP was a flagship of rangefinder cameras made in Japan. The most important feature of this camera, a built-in universal viewfinder that supports six interchangeable lenses was highly acclaimed by professional photographers. The Nikon SP, together with the NIKKOR lens and optical glass, won the grand prix at the 1958 World Expo held in Brussels.
The Nikon SP and other 1950s and 1960s rangefinder cameras competed directly with models from Leica and Zeiss. However, the company quickly ceased developing its rangefinder line to focus its efforts on the Nikon F single-lens reflex line of cameras, which was successful upon its introduction in 1959.
For nearly 30 years, Nikon’s F-series SLRs were the most widely used small-format cameras among professional photographers, as well as by the U.S. space program.
However, as auto focus SLRs became available from Minolta and others in the mid-1980s, Nikon’s line of manual-focus cameras began to seem out of date.
Canon introduced a new type of lens-camera interface with its entirely electronic Canon EOS cameras and Canon EF lens mount in 1987. This prompted many professional photographers (especially in sports and news) to switch to the Canon system through the 1990s.
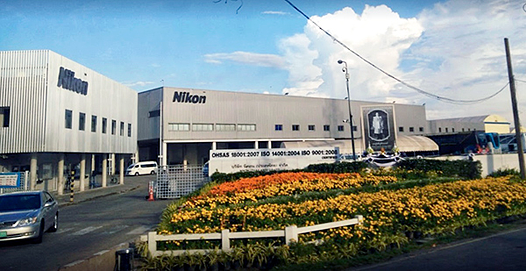
The Nikon factory in Ayutthaya, Thailand.
Nikon has shifted much of its manufacturing facilities to Thailand, with some production (especially of Coolpix cameras and some low-end lenses) in Indonesia. The company constructed a factory in Ayuthaya north of Bangkok in Thailand in 1991. By the year 2000, it had 2,000 employees. Steady growth over the next few years and an increase of floor enabled the factory to produce a wider range of Nikon products. By 2004, it had more than 8,000 workers.
As of 2009, all of Nikon’s Nikon DX format DSLR cameras and the D600 camera, are produced in Thailand, while their professional and semi-professional Nikon FX format (full frame) cameras and the retro-styled Df are built in Japan, in the city of Sendai. The Thai facility also produces most of Nikon’s digital “DX” zoom lenses, as well as numerous other lenses in the Nikkor line.
In January 2006 Nikon announced the discontinuation of all but two models of its film cameras, focusing its efforts on the digital camera market.
It continues to sell the fully manual FM10, and still offers the high-end fully automatic F6. Nikon has also committed to service all the film cameras for a period of ten years after production ceases.
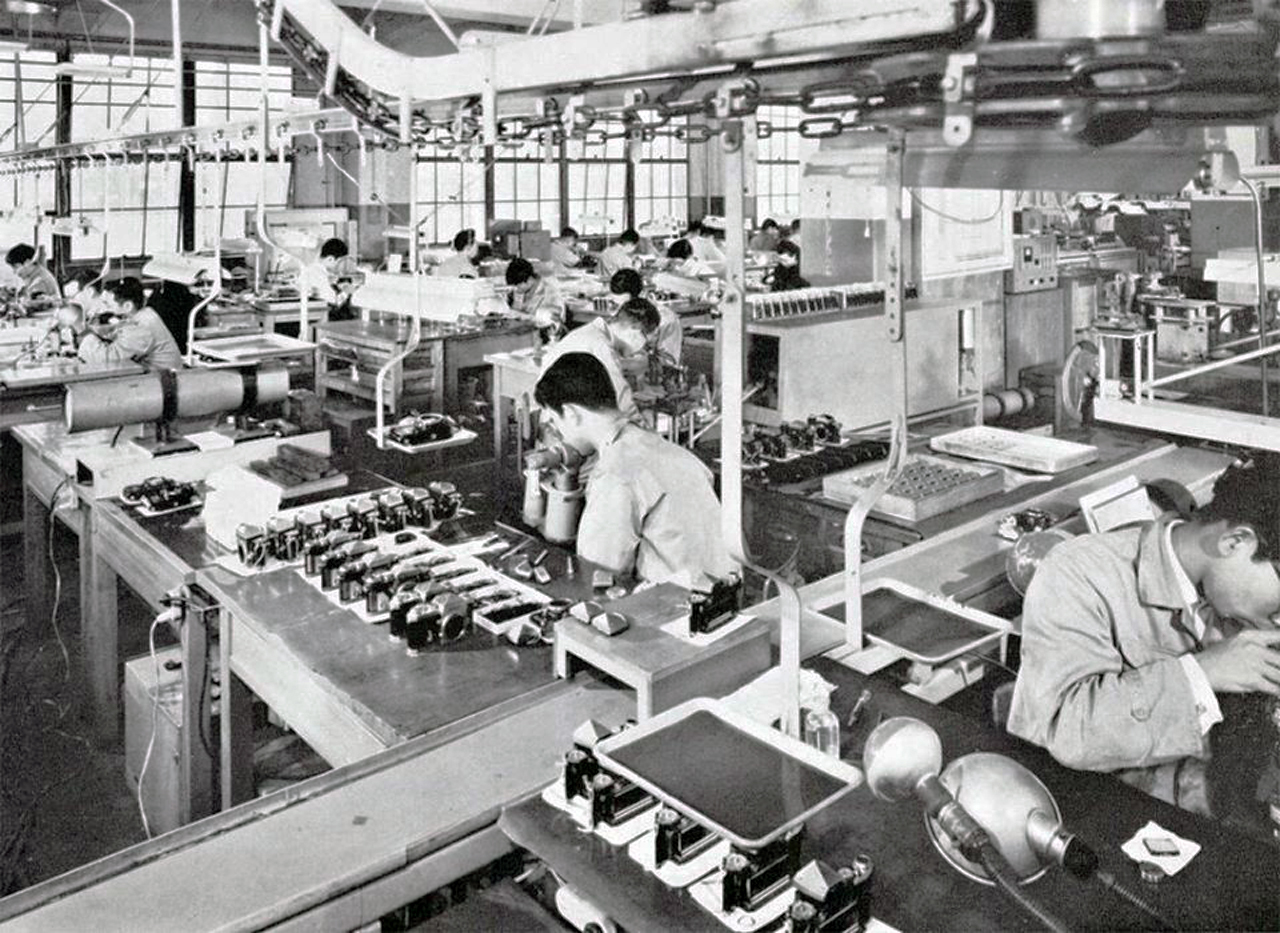
The Nikon Assembly Department
NIKON Going digital
Nikon created some of the first digital SLRs for NASA, used in the Space Shuttle since 1991. After a 1990s partnership with Kodak to produce digital SLR cameras based on existing Nikon film bodies, Nikon released the Nikon D1 SLR under its own name in 1999.
The D1 was among the first digital cameras to have sufficient image quality and a low enough price for some professionals (particularly photojournalists and sports photographers) to use it as a replacement for a film SLR.
The company also has a Coolpix line which grew as consumer digital photography became increasingly prevalent through the early 2000s.
Once Nikon introduced affordable consumer-level DSLRs such as the Nikon D70 in the mid-2000s, sales of its consumer and professional film cameras fell rapidly, following the general trend in the industry.
In January 2006, Nikon announced it would stop making most of its film camera models and all of its large format lenses, and focus on digital models. Contrary to other brands, Nikon never attempted to offer projectors or their accessories.

The Nikon D1 (Front and Rear).
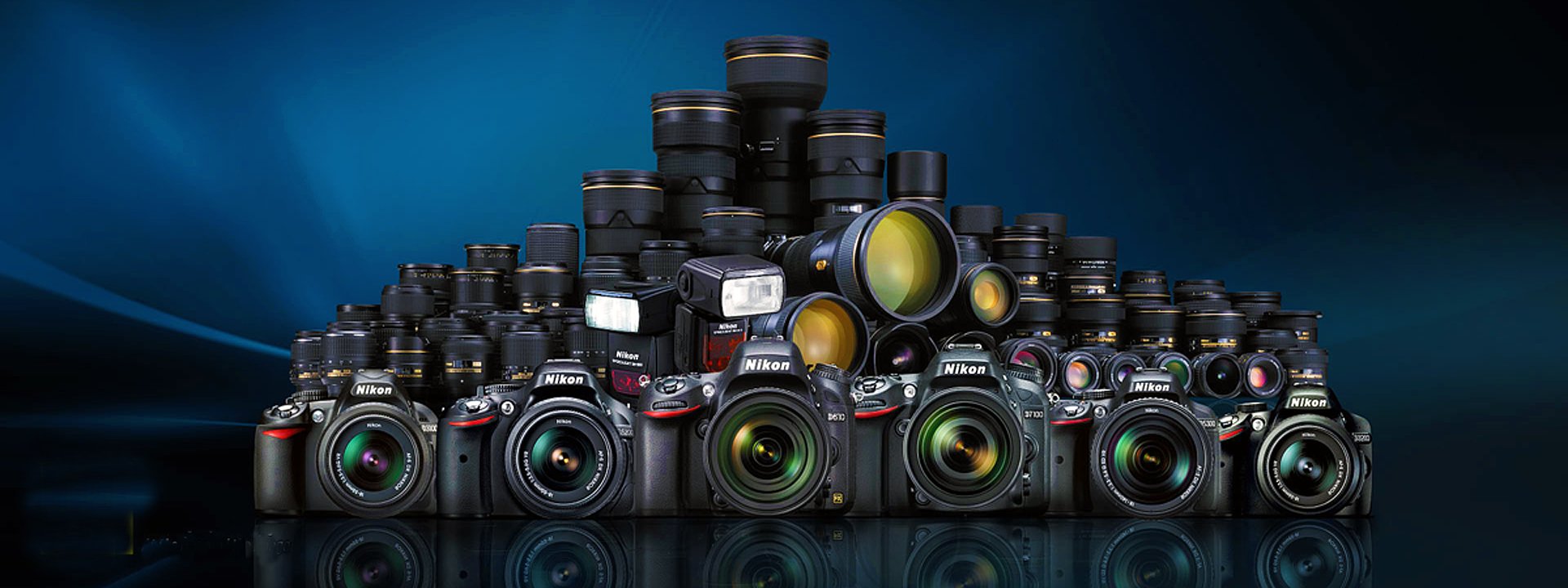
NIKON made these FILM cameras OVER THE YEARS
- Nikon F series (1959, known in Germany for legal reasons as the Nikkor F)
- Nikon F2 series (1971)
- Nikon F3 series (1980)
Midrange
- Nikkorex series (1960)
- Nikkormat F series (1965, known in Japan as the Nikomat F series)
- Nikon FM (1977)
- Nikon FM2 series (1982)
- Nikon FM10 (1995)
Midrange with electronic features
- Nikkormat EL series (1972, known in Japan as the Nikomat EL series)
- Nikon EL2 (1977)
- Nikon FE (1978)
- Nikon FE2 (1983)
- Nikon FA (1983)
- Nikon F-601M (1990, known in North America as the N6000)
- Nikon FE10 (1996)
- Nikon FM3A (2001)
Entry-level (Consumer)
- Nikon EM (1979)
- Nikon FG (1982)
- Nikon FG-20 (1984)
- Nikon F-301 (1985, known in North America as the N2000)
35mm SLR with autofocus
- Nikon AC-2E Data Link System (1993)
- NIKKOREX 8 (1960)
- NIKKOREX 8F (1963)
(Professional – Intended for professional use, heavy duty and weather resistance)
- Nikon F3AF (1983, modified F3 body with Autofocus Finder DX-1)
- Nikon F4 (1988) – (World’s first professional auto-focus SLR camera and world’s first professional SLR camera with a built-in motor drive)
- Nikonos RS (1992) (Professional when reviewed in underwater conditions) – (World’s first underwater auto-focus SLR camera)[54]
- Nikon F5 (1996)
- Nikon F6 (2004)
(Intended for pro-consumers who want the main mechanic/electronic features of the professional line but don’t need the same heavy duty/weather resistance)
- Nikon F-501 (1986, known in North America as the N2020)
- Nikon F-801 (1988, known in the U.S. as the N8008)
- Nikon F-801S (1991, known in the U.S. as the N8008S)
- Nikon F90 (1992, known in the U.S. as the N90)
- Nikon F90X (1994, known in the U.S. as the N90S)
- Nikon F80 (2000, known in the U.S. as the N80)
- Nikon F100 (1999)
- Nikon F-601 (1990, known in the U.S. as the N6006)
- Nikon F70 (1994, known in the U.S. as the N70)
- Nikon F75 (2003, known in the U.S. as the N75)
Entry-level (Consumer)
- Nikon F-401 (1987, known in the U.S. as the N4004)
- Nikon F-401S (1989, known in the U.S. as the N4004S)
- Nikon F-401X (1991, known in the U.S. as the N5005)
- Nikon F50 (1994, known in the U.S. as the N50)
- Nikon F60 (1999, known in the U.S. as the N60)
- Nikon F65 (2000, known in the U.S. as the N65)
- Nikon F55 (2002, known in the U.S. as the N55)
- Nikon I (1948)
- Nikon M (1949)
- Nikon S (1951)
- Nikon S2 (1954)
- Nikon SP (1957)
- Nikon S3 (1958)
- Nikon S4 (1959) (entry-level)
- Nikon S3M (1960)
- Nikon S3 2000 (2000)
- Nikon SP Limited Edition (2005)
APS SLR cameras
- Nikon Pronea 600i / Pronea 6i (1996)
- Nikon Pronea S (1997)
Between 1983 and the early 2000s a broad range of compact cameras were made by Nikon.
Nikon first started by naming the cameras with a series name (like the L35/L135-series, the RF/RD-series, the W35-series, the EF or the AW-series).
In later production cycles, the cameras were double branded with a series-name on the one and a sales name on the other hand. Sales names were for example Zoom-Touch for cameras with a wide zoom range, Lite-Touch for ultra compact models, Fun-Touch for easy to use cameras and Sport-Touch for splash water resistance.
After the late 1990s, Nikon dropped the series names and continued only with the sales name. Nikon’s APS-cameras were all named Nuvis.
The cameras came in all price ranges from entry-level fixed-lens-cameras to the top model Nikon 35Ti and 28Ti with titanium body and 3D-Matrix-Metering.
- Nikonos I Calypso (1963, originally known in France as the Calypso/Nikkor)
- Nikonos II (1968)
- Nikonos III (1975)
- Nikonos IV-A (1980)
- Nikonos V (1984)
- Nikonos RS (1992) (World’s first underwater Auto-Focus SLR camera)
some nikon cameras

Nikon F50 Champagne-Silver camera
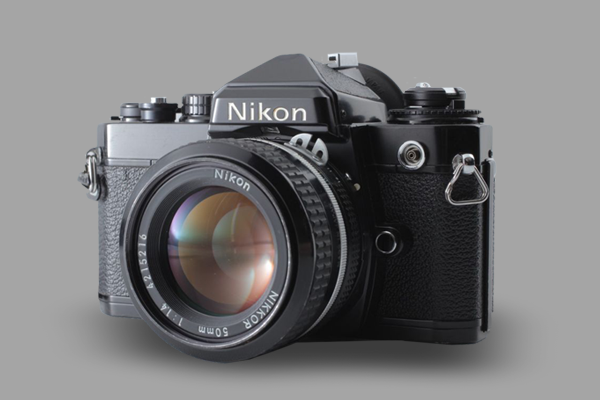
Nikon SLR FE camera

Nikon Coolpix 3100 camera

Nikonos 5 underwater camera
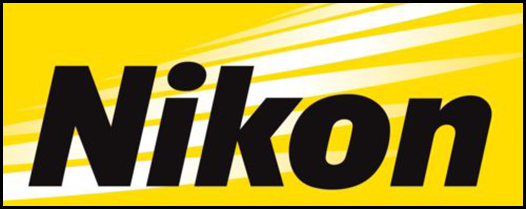
FOUNDERS: Jerry Nims and Allen Kwok Wah Lo
COMPANY NAMES:
1970: Nimslo Corporation of Atlanta the wholly owned subsidiary of Nimslo International, Ltd.; 1980: Nimstec of Atlanta;
COMPANY ADDRESS:
1970: Nimslo Corporation, One Nimslo Park, Atlanta, Georgia 30338;
The Nimslo is a stereo camera with a bright field viewfinder that produces 3-D pictures that can be viewed without glasses. This is done using lenticular printing. It uses common 35mm film in 135 film format cartridges. It was manufactured in the 1980s by Timex in Dundee, Scotland.
Across the myriad of toy cameras and varied forgotten photographic castoffs, there’s always been an array of weird and wonderful cameras that never quite took off. One of the stranger and fleeting trends has to be quadrascopic cameras, led by the Nimslo 3-D, and its twisted cousin, the Nishika 8000.
It’s a story that involves more than just an odd-looking camera. During its short rise and subsequent fall, there was a host of misguided tech, bankruptcies and federal investigations – all in the name of uncovering ‘the next Polaroid’.
The camera’s premise hinged on a four-lens design that captured four simultaneous images from slightly different perspectives, which would then be used to create 18 oscillating 3-D prints from a 36-exposure roll of film.
Founded in 1970 by Jerry Nims and Allen Kwak Wah Lo, Nimslo, former employees of the giant Japanese conglomerate Asahi, the world’s leading manufacturer of 3-D postcards, Nimslo became the leading brand behind quadrascopic cameras.
Three-dimensional camera tech had slowly begun to grow in popularity, and Nims and Lo had the prerequisite experience to start such a venture having met eight years earlier researching 3-D photography for the Asahi Optical Company. Launching to considerable fanfare, in 1982 Nimslo showcased their ‘Nimslo 3-D’ to audiences at the Photokina exhibition in Cologne, Germany.
Nimslo Corporation of Atlanta has released a new camera into the test market of southern Florida. Originally priced at $250, flash extra, this 35mm automatic camera embodied several unique features. Although utilizing normal 35mm colour-print film, it exposed four vertical negatives simultaneously through four lenses arrayed horizontally across the face of this otherwise innocuous looking camera.
People really believed it could be the next Polaroid. Thanks to a range of glossy magazines pushing the brand and its technology, Nimslo managed to raise millions from British venture capitalists, who backed the camera’s 3-D prints to be the next great leap forward in photographic technology.

The Nimslo-system
Fred Olsen comes to the rescue…
The shares of the Nimstec were bought by Eagleville Company in October 1980, controlled by the Ptarmigan Trust that at the same time gained control over Timex Corporation. The operation was controlled by billionaire Fredrik Olsen, head of the Fred Olsen & Co. shipping company. Olsen was a technological and industrial visionary and believed strongly in the Nimslo product. He wanted the Timex factory in Dundee in Scotland to produce the cameras, as they had already produced cameras for Polaroid. He established a guarantee of US$25 million for the acquisition of the Nimslo shares and a comprehensive camera-to-print system was developed.
The Nimslo was originally built in a Timex factory in Dundee, Scotland. A massive strike in Dundee, as the U.S. rollout was gaining strong momentum, caused Nimslo to miss the delivery dates on all cameras sold. This led to the cancellation of the Timex contract.
Sunpak in Japan built later cameras. After the Dundee strike, the sales team, led by former top Polaroid executive, Corvin Cianci, could not regain the top position with the replacement camera manufactured in Japan by Sunpak Company.
Since 1984 Nimslo did go out of business. 3-Dx processed the Nimslo film. Other lenticular systems using a three lenses have been introduced but have not become very popular. In fact, 3d-it, the producer of 3 lens cameras and film processor, went out of business on 3/31/99.

Nimslo 3-D Camera assembly at the Timex factory in Dundee. (1980s).
High hopes and expectations
The beginning of 1982 saw the camera grace the front page of the Sears catalogue and become the fastest selling 35mm camera in the United States. By year’s end, projected quarterly sales of half-a-million units turned out to be as little as 50,000 as the company squandered millions.
With an advertising budget of $25-million, Nimslo Corporation lost $18-million in 1982 (ostensibly, wildcat strikes in Scotland severely reduced expected production, and dealers were not able to meet the need generated by the massive publicity). So, the original campaign was dropped. This was an expensive miscalculation. The short sightedness of their design and marketing has also been characteristic of their investigations of potential application and consequent benefits.
The meteoric rise of Nimslo Corporation exemplifies certain dynamics which would normally be masked through the long growth curve of organizations like Kodak and Polaroid.
Nimslo makes one product, provides one service, and has done so for less than three years.
Other comparable examples of large-scale, ingénue industry can be found in the computer realm, where the instant success and instant demise of Osborne Computer Corporation serve as a study in contemporary tech no-lifecycle pathology (as in post-mortem).
In some respects, Nimslo’s prehistory is similar. The company was founded by astute engineer-designers, Jerry Nims and Allen Lo, former employees of the giant Japanese conglomerate Asahi, the world’s leading manufacturer of 3-D postcards. They perceived the possibility of extending the difficult technology of lenticular stereography into the popular market by simplifying, standardizing, and producing quantities sufficient to make costs affordable.
Unlike Osborne, however, key elements of the Nimslo system are patentable, proprietary, and relatively difficult to replicate anyway. Thus Nimslo stands, as of that moment, as a neat monopoly; the only aspects of their system outside of their control were choices of colour print film and batteries.

Cover of a paperback about the Nimslo 3-D system.
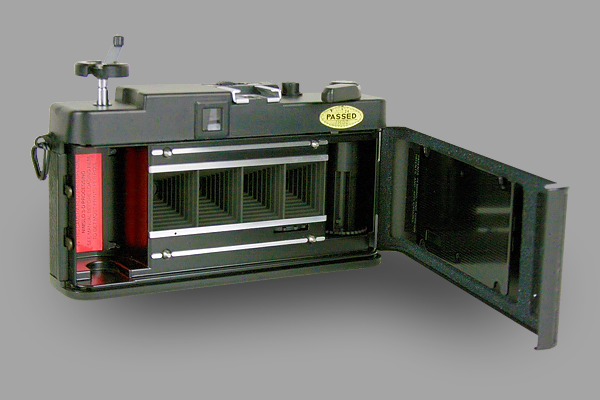
Open back of the Nimslo camera
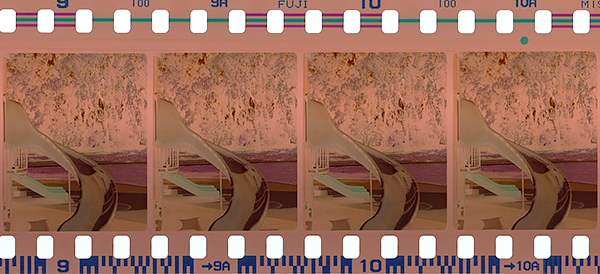
Negative strip of the Nimslo camera
Camera Type | 35 mm viewfinder lenticular stereo camera |
---|---|
Film | 135 cartridge |
Size | 137 x 74 x 43 mm (W x H x D) |
Weight | 325 grams without case, 423 grams with ever ready case |
Lens Separation | 18.50 mm, 37.00 mm, 55.50 mm |
Image Format | 17.50 x 21.90 mm (W x H) |
Image Window Separation | 18.70 mm, 37.30 mm, 56.00 mm |
Lenses | triplets (glass, matched), 1:5.6/30 mm |
Diaphragms | Double lamellar type (diamond shaped) behind the lenses, continuously adjustable f/5.6 to f/22 |
Focusing | Fixed focus |
Shutter | Double lamellar type shutter behind the lenses. Cocked with film transport. Same as diaphragm |
Shutter Speeds | continuously from 1/30 to 1/500 sec., electronically controlled |
Viewfinder | Newton viewfinder (approx. 0,6x), with bright-line frame |
Rangefinder | Not applicable |
Film Loading | Manual |
Film Transport | Manual, with rapid-wind lever by 16 ½ sprocket holes (= 68.00 mm), sprocket wheel on bottom |
Film Rewinding | Manual. By pressing film rewind button, with crank |
Frame Counter | Additive, 1 to 18, self-resetting |
Flash Contact | Hot shoe |
Tripod Socket | ¼“/ 20 TPI |
Selftimer | Not applicable |
Special Features | Double exposure prevention, cable release socket |
Accessories | Operating instructions, ever ready case |
Notes | Automatic Exposure can bet set to be used with 100 ASA / 21° DIN and 400 ASA / 27° DIN film |

Nimslo advertising in the USA.
FOUNDER: James Bainbridge
COMPANY NAMES:
1989: Nishika Corporation, Henderson Nevada and Nishika Optical Systems, Hong Kong; 1996: The company and the owner went bankrupt and went out of business.
COMPANY ADDRESSES:
1989: Nishika Corporation, Henderson Nevada and Nishika Optical Systems, Hong Kong;
Nishika may not seem to have the same interesting background as the Nimslo but as a family member, the story of Nimslo is the story of Nishika and many see the Nishika as the continuation of the Nimslo project.
James Bainbridge in the Las Vegas suburb of Henderson, Nevada founded Nishika sometime around 1989 when he purchased the remnants of Nimstec, an Atlanta-based camera company that had gone bankrupt.
After acquiring Nimstec, Nishika introduced the N8000 and then the smaller N9000, both of which were heavily based on the Nimslo camera. The two models were manufactured in Hong Kong and are the only cameras known to bear the Nishika name.
“Nishika” sounds Japanese but the Nevada company apparently was not Japanese at all, just named to sound like it. Which probably to this day makes some people think it’s a Japanese camera when it’s actually made in Hong Kong for a company based in the USA. Needless to say, both the Nimslo and Nishika companies folded and went out of business.
The Nishika N8000 was also a quadroscopic stereo 3-D camera, and was introduced in 1989 by this company. Though the Nishika N8000 appears quite different from the Nimslo 3-D camera in many ways, they are in fact “blood relatives”. Quite logical, because Nishika Corporation acquired part of the Nimslo Company, as well as their parts and patents, so the N8000 was in many ways a continuation of the Nimslo experiment.
The number of Nishika cameras manufactured seems to greatly exceed the number that were sold while the company was still in business. To this day the camera is widely available in new condition even though it hasn’t been made for over 20 years!
Fraudulent acts
Despite being a camera company that sold inexpensive plastic stereo cameras, Nishika is perhaps best known for being investigated by the United States Federal Trade Commission for fraud.
Unfortunately, Nishika didn’t become famous for its 3-D cameras or for its relatively clever lenticular prints but for conning people out of their money.
In 1992, Nishika began running a prize promotion scheme in which the victims were promised prizes in exchange for paying up to $700 for a Nishika camera. Any one of the prizes, if really what it was represented to be would be worth far more than $700, yet they were told they would receive two of them.
What they actually got, of course, was worth nowhere near what they were promised, or what they paid. It is entirely possible that Nishika had already ceased production of the N8000 as early as late 1991, and that this prize scheme was an attempt to unload a bunch of unsold cameras.
Then, after taking their money, Nishika would send them a camera and/or travel vouchers that came with so many restrictions and extra fees that they were all but useless.
Despite essentially being a copy of a failed product, Nishika falsely claimed that their cameras were the product of “15 years of research by hundreds of engineers and technicians and over $50 million” and even went so far as to hire legendary horror actor Vincent Price to star in a short series of vaguely disturbing promotional videos.
In the end, karma caught up to Nishika and the United States Federal Trade Commission launched an investigation, resulting in the company being forced to refund up to $11.3 million to their victims in 1996. The ruling unsurprisingly bankrupted the company (and its founder) in the process.
Though the settlement against Nishika is usually blamed for its demise, it is likely they would have soon gone out of business even if the FTC had never investigated them. It is even possible that the prize promotion scheme may have actually postponed the bankruptcy!


The inside page of the instruction manual of the Nishika N8000.
N8000 & N9000 specs
SPECS N8000 N9000
Manufacturer Nishika Nishika
Type N8000 N9000
Year release 1989 1990
Camera type Stereo camera Stereo camera
Film type 135 (35mm) 135 (35mm)
Lens Four fixed 30mm plastic lenses Four fixed focus lenses of 1.2m (5-1/2 feet) to infinity
Shutter speed Single speed of 1/60 sec. Single speed of 1/70 sec.
Aperture f/19, f/11 and f/8 f/11 and f/16
ISO from ISO 100 onwards from ISO 200 onwards
Battery 2 AA batteries Not required
Dimensions 7 x 3 x 8 inches 3 x 4 x 6 inches
Weight 916 gr 255 gr
FOUNDER: John Noble
COMPANY NAMES:
1990: Kamerawerkstätten Charles A. Noble; 1998: Kamera Werke Dresden GmbH; 1999: Optics development no longer takes place.
COMPANY ADDRESS:
1990: Bismarckstraße 56, 01257 Dresden.
The Noblex panoramic camera with a rotating lens must be described as the last new construction of the Central German photo industry.
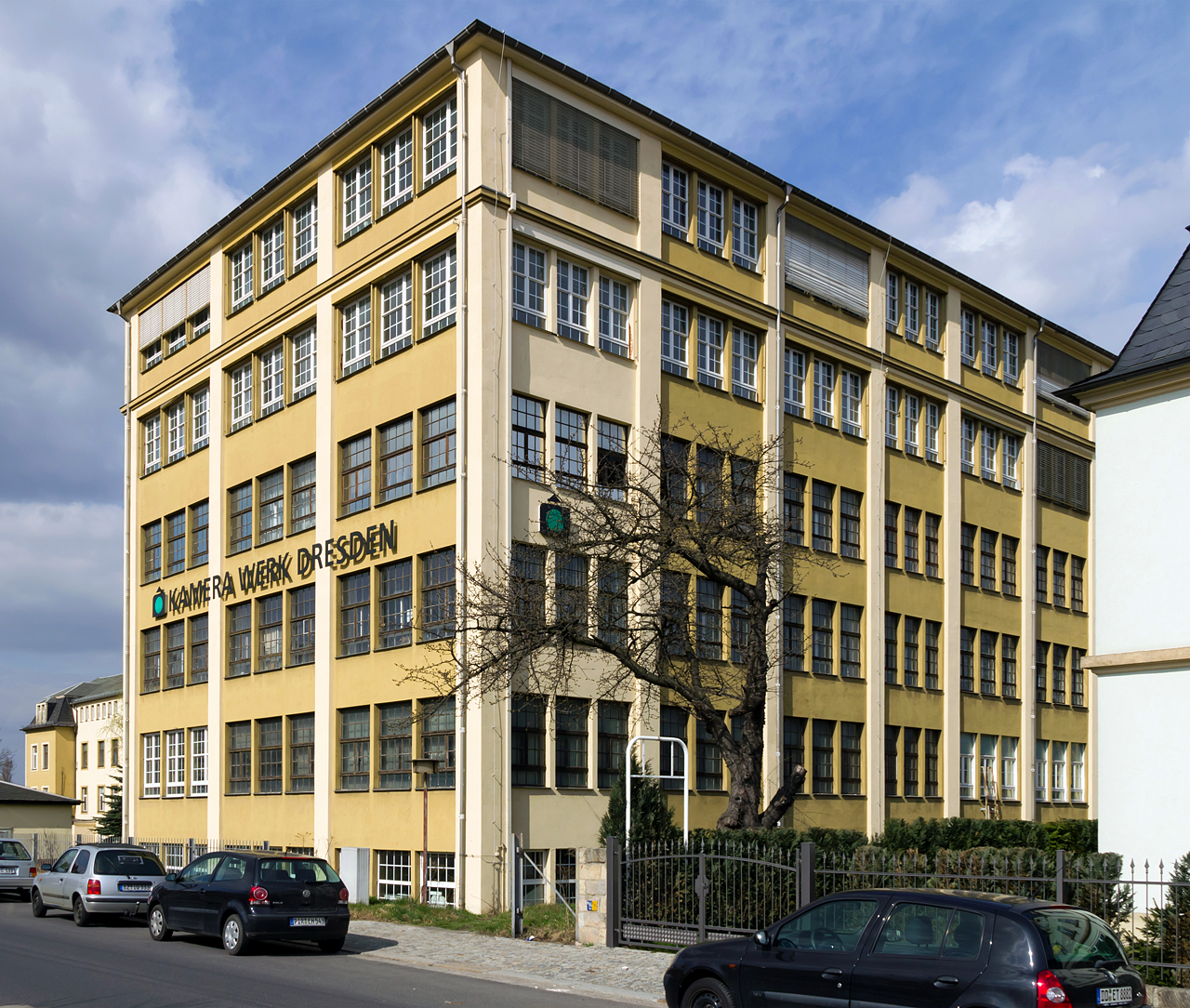
Kamerawerkstätten Charles Noble, Bismarckstrasse 56, Dresden
The start of Noblex’ panorama camera
Little is known: The development of the Noblex panorama cameras began with a model for roll film type 120. The much more widespread 35mm variant with an image format of 24×66 mm was only created afterwards. There were two different basic models in the medium format: the Noblex 6/150 allowed six shots in an image format of 50×120 mm, while the Noblex 175 allowed four shots in the size 50×170 mm. In addition, there were sub-variants in the 150 model, which differed in terms of the shutter speed ranges, the possibility of setting the distance, the ability to shift the lens and other details.
However, the 35mm version of the panorama camera only came onto the market in 1994. As already stated above, the development started on the basis of the 120 roll film.
The basic idea came from an American named Cornelius Schorle, which was picked up in Dresden in 1991 and took shape in the course of 1992 in the form of the first panoramic camera with a rotary lens, in which the lens barrel made a full rotation of 360 degrees. Despite all the innovations, this Noblex 150 medium format camera was difficult to sell due to its high price.
Panorama cameras with a rotating lens are just a niche product in the camera market anyway. The special image impression that results from the functional principle wears off quickly. It is also not easy to always find good motifs for the very long format.
In 1990, John Helmuth Noble, the son of the in 1946 expropriated Charles Noble, returned to Dresden with his brother Georg Noble, where he applied to the Treuhandanstalt for restitution of his former camera factory Kamerawerkstätten Charles A. Noble and the rights to the name.
He received the restitution of the Niedersiedlitz plant from the trustee in 1990, and was astonished to find that he had gotten back the buildings of this Pentacon division, but not the patents and the trademark rights to the cameras.
The Treuhand had already sold this to Heinrich Manderman, the former Pentacon representative in the Federal Republic. The trust instead sold the naming rights to Heinrich Manderman. A resumption of the Praktica production (BX 205) with 122 employees, initially planned by Noble, therefore did not materialize. So John Noble couldn’t build Prakticas.
So a new product was needed. In retrospect, that seems very surprising, why a panoramic camera. In fact, bringing out a camera so geared towards very special purposes was actually quite a fix. Nevertheless, many components of this new product are reminiscent of the Praktica BX205: the shutter speed button, the rewind crank, the sprocket and some more. In 1991 he started work on a panorama camera with 36 employees.
Of course, the fact that many components of this new product are reminiscent of the Praktica BX205 shouldn’t come as a surprise – it’s just the outward sign of the fact that the Noblex cameras were developed by former Pentacon designers, some of whom had been working on the Praktica cameras since the 1970s. Among them Hans-Jörg Schönherr, Hans Zimmet and Siegfried Hainy, some of whom have already been mentioned on our website in relation to other technical contexts.

The Noblex Pro 6/150U and the box of the first Noblex Pro 6/150E in one shot.
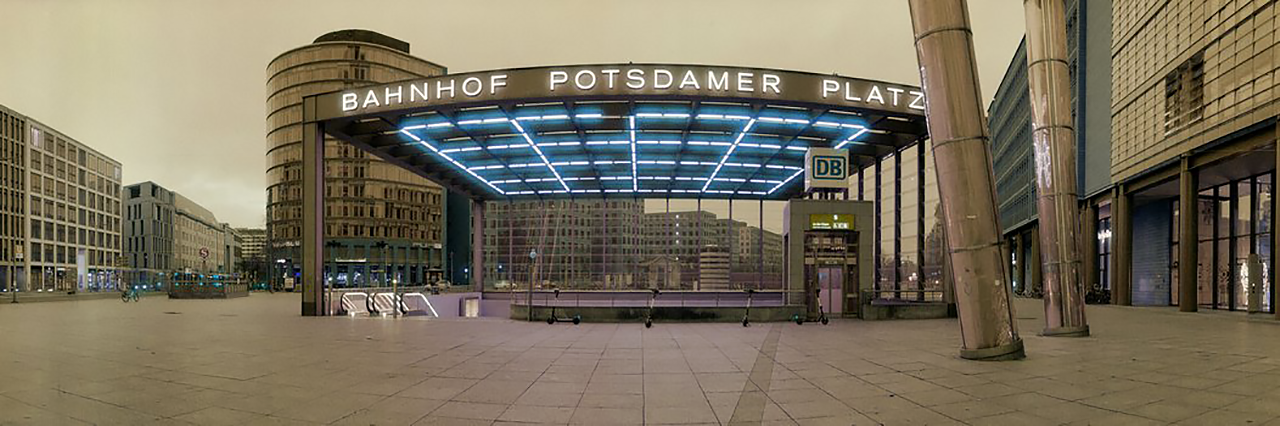
An example of a shot made with a Noblex panorama camera.
a closer look at the cameras
35mm film
Fixed, rotating-lens panoramic cameras, all for 24×66 mm format on 35 mm film (a 127° angle of view). All the 35 mm models are fixed-focus, relying on the aperture control to give adequate depth of field.
135 U | 135 UC | 135 S | 135 C | 135 N | Pro Sport | |
---|---|---|---|---|---|---|
Multiple exposure | YES | YES | YES | YES | YES | NO |
Level | YES | YES | YES | YES | YES | NO |
Lens shift | YES | YES | YES | YES | NO | NO |
Shutter Speeds | 1, 1/2, 1/4, 1/8, 1/15, 1/30, 1/60, 1/125, 1/250, 1/500 | 1, 1/2, 1/4, 1/8, 1/15, 1/30, 1/60, 1/125, 1/250, 1/500 | 1/30, 1/60, 1/125, 1/250, 1/500 | 1/30, 1/60, 1/125, 1/250, 1/500 | 1/30, 1/60, 1/125, 1/250, 1/500 | 1/30, 1/60, 1/125, 1/250, 1/500 |
Pano lux meter | YES | YES | YES | YES | NO | NO |
Some of the 35 mm cameras have shutter speeds 1/30 – 1/500 second, essentially all suitable for hand-held use; others (the 135U and UC) have speeds down to 1 second. All except the Pro Sport allow 3 mm of front rise.
Medium Format
Fixed, rotating-lens panoramic cameras for 120 film. Most models (certainly the UX and FS) have three-position zone focusing, at infinity (actually 17.2 m for the FS model), ‘medium’ (6.5 m for the FS) and ‘near’ (2.8 m for the FS; the exact focus distances differ for other models). Closer focus is possible with add-on close-up lenses.
6/150E | 6/150E2 | 6/150HS | 6/150U | 6/150UX | 6/175U | 6/175UX | |
---|---|---|---|---|---|---|---|
Film | 120 | 120 | 120 | 120 | 120 | 120 | 120 |
Format | 50 x 120 mm | 50 x 120 mm | 50 x 120 mm | 50 x 120 mm | 50 x 120 mm | 50 x 170 mm | 50 x 170 mm |
Exposures | 6 | 6 | 6 | 6 | 6 | 4 | 4 |
Lens | Rotar T 4,5/50S | Rotar T 4,5/50S | Rotar T 4,5/50S | Rotar T 4,5/50S | Rotar T 4,5/50S | Rotar T 6,5/75 | Rotar T 6,5/75 |
Lens shift | NO | NO | NO | 5 mm | 5 mm | 5 mm | 5 mm |
Focus | Fixed | Fixed | Fixed | Zone | Zone | Zone | Zone |
Shutter Speeds | 1/15, 1/30, 1/60, 1/125, 1/250 | 1/15, 1/30, 1/60, 1/125, 1/250 | 1/60, 1/125, 1/250, 1/500, 1/1000 | 1/60, 1/125, 1/250 | 1/60, 1/125, 1/250 | 1/60, 1/125, 1/250 | 1/60, 1/125, 1/250 |
Slow exposure module | x | x | x | x | 2, 1, 1/2, 1/4, 1/8 | x | 2, 1, 1/2, 1/4, 1/8 |
Pano lux 150 meter | YES | YES | NO | YES | YES | YES | YES |
Weight | 1750g | 1750g | 1750g | 1840g | 1840g | 2350g | 2350g |
Battery | 4x AA / LR6 | 4x AA / LR6 | 4x AA / LR6 | 4x AA / LR6 | 4x AA / LR6 | 4x AA / LR6 | 4x AA / LR6 |
entering a niche market
In addition, at the beginning of the 1990s, Dresden camera construction entered a market segment in which several manufacturers were already active. Therefore, an attempt was made to set the camera apart from the competition with special features of the camera: mainly, these were the particularly large angle of rotation of the drum, which led to even wider images, and its electric drive.
With an additional 35mm model, the hope was obviously to appeal to larger groups of buyers and thus to be able to utilize camera operation more solidly.
Because of the success of the camera, 96 people were employed again in 1996. After that, however, there was a financial crisis, as a result of which Noble sold the company in 1997 (among others to the Noblex developer Hans-Jörg Schönherr).
From May 25, 1998, the company operated under the name of Kamera Werke Dresden GmbH. In 1999, Hans-Jörg Schönherr and Matthias Richter left the company and initially set up a company for special cameras (KST-Dresden) in Pirna. Optics development no longer takes place in the camera factory in Dresden.

This is a Noblex 135 S, a 35mm swing lens panoramic camera made in 1992. All Noblex cameras have a unique electronically controlled rotating slit shutter that spins a complete 360º for each exposure. With an optional Noblex Panolux 135 Exposure Control Module the camera is capable of automatic exposure. The Panolux automatically controls the exposure time of the camera. There are two measuring methods for this: reflective metering and subject-oriented metering of incident light.
Large-format prototype
A prototype 4×5-inch monorail SLR camera, the Prestoflex 4×5 was offered for sale at Westlicht in June 2017. The metal-bodied camera comprises a box body with a manually-raised mirror for reflex viewing/focusing from above, and mounted on a short rail projecting from the front standard, to which it is also linked by a bellows.
The auctioneer’s notes state that the bellows and viewfinder are interchangeable (supposing alternate parts exist). The camera offered for sale was fitted with an incomplete lens and electronic shutter unit. It appears to have only limited front camera movements.

Another example of a shot made with a Noblex panorama camera.
FOUNDER: Yamashita Takeshi
COMPANY NAMES:
1919: K.K. Takachiho Seisakusho; 1935: Mizuho Kōgaku Kenkyūjo; 1942: Takachiho Kōgaku Kōgyō K.K. (Takachiho Optical Co., Ltd.); 1949: Olympus Kōgaku Kōgyō K.K. (Olympus Optical Co. Ltd.); 2003: Olympus Corporation.
COMPANY ADDRESSES:
1919: Toyotama-gun Yoyohata-chō Hatagaya, Tokyo; 1948: Shibuya plant; 1950: headquarters in Hatagaya – commercial department in Ginza; 2003: global headquarters are located in Shinjuku, Tokyo.
Olympus is a Japanese company making cameras and other optical products. In recent years, Olympus Corporation has focused on “Opto-Digital Technology” as its core competence, technological strengths that competitors cannot easily imitate, to maximize corporate value and to become one of the top optical instrument manufactures. Olympus holds roughly a 70-percent share of the global endoscope market, estimated to be worth approximately US$2.5 billion.
The company was founded on October 12, 1919 under the name K.K. Takachiho Seisakusho (meaning Takachiho Works Co., Ltd.) by Yamashita Takeshi. The address was Toyotama-gun Yoyohata-chō Hatagaya in Tokyo.
Takeshi Yamashita became an attorney after graduating from Tokyo Imperial University Law school in 1915. After one year of military service, he joined Tokiwa Shokai, a trading company. He brought considerable profit to Tokiwa Shokai through sugar trading.
Tokiwa Shokai then compensated his effort by allowing Mr. Yamashita to establish his own firm, Takachiho Seisakusho with Shintaro Terada, a friend from his lawyer days. The objective of Takachiho Seisakusho was to launch domestic production of microscopes.
The chief engineer of the new company was Terada Shintarō, who previously worked for M & Katera Kōgaku Kikai Seisakusho, and the first products of Takachiho Seisakusho were microscopes and thermometers. At that time, Japan imported all its microscopes (and other instruments), mainly from Germany. The company had the clear ambition to rival, and even surpass, these high precision foreign imports. Olympus has been renowned to this day for its research on medical equipment.
Yamashita encouraged his engineers by saying that mere imitations of imported products wouldn’t suffice and that it would be necessary to create something truly original.
In June 1920, just six months after the company’s founding, Yamashita’s dream of making a domestic microscope came true with the introduction of the Asahi, the first microscope manufactured by Takachiho and was sold by Tokiwa Shōkai under its own Tokiwa brand. The trade name Olympus was applied for on the same year 1920 and granted in early 1921.
Mr. Terada was the first Japanese to build microscopes using industrial techniques in the 1910s. A microscope built by Mr. Terada was exhibited at the Taisho Expo held in 1914 and won the bronze prize.
Mr. Matsumoto of Iwashiya, a long-established medical equipment firm, financially supported him to produce “M&KATERA” microscopes. This name was created by combining the names of the three people involved in the development of this microscope: Mr. Matsumoto, Mr. Kato, and Mr. Terada.
Mr. Terada had been mainly making thermometers in Hongo, Tokyo. He gained sufficient experience in microscopes through building the M&KATERA model.
Mr. Yamashita revealed his dream of building microscopes to Mr. Terada and asked him to come work for Takachiho Seisakusho. The manufacturing equipment of Terada Seisakusho was transferred to Takachiho Seisakusho, and Mr. Terada became the chief engineer of the company.
In 1923, the thermometer business was sold off. And most of the proceeds were invested in the microscope business. The company that purchased the thermometer business was authorized to use Olympus as its brand name.

All 12 Olympian gods resided in the mountain; Zeus and his wife Hera, Athena, Artemis, Poseidon, Apollo, Hester, Demeter, Aphrodite, Hermes, Ares, and Hephaestus. They would meet daily in Zeus palace in the Pantheon, to discuss the fate of the mortals. Below the Pantheon was Zeus’ Throne – known today as Stefani – from where he would rule both gods and men, hurling thunderbolts to those who disobeyed him.

Overview of the Taisho Exhibition, Ueno Park, 1914. The Tokyo Taisho Exhibition was held from March 20 to July 31, 1914 in Ueno Park, Tokyo. The level that Japanese industrial technology had reached just prior to the outbreak of the First World War is reflected in the survey report of the industrial machinery products displayed, which noted that 5,717 machines were shown at the exposition.
In Greek mythology, Mount Olympus is the home of the twelve supreme gods and goddesses. Olympus was named after this mountain to reflect its strong aspiration to create high quality, world famous products. “Olympus” has been used as a trademark since the time of Takachiho Seisakusho, the predecessor of Olympus Corporation.
In Japanese mythology, it is said that eight million gods and goddesses live in Takamagahara, the peak of Mount Takachiho. The name “Olympus” was selected as the trademark because Mount Olympus, like Mount Takachiho, was the home of gods and goddesses. This trademark is also imbued with the aspiration of Olympus to illuminate the world with its optical devices, just like Takamagahara brought light to the world.
The Olympus Tokyo logo was applied for in mid-1931 and registered a little later. The company supplied microscopes to the Japanese Navy and became a “Navy approved factory” (kaigun shitei kōjō) in late 1933. It offered an apparatus to take pictures with a microscope, consisting of a prism, a basic shutter and a dark box taking a ground glass or 56×93mm glass plates.
The company underwent research in camera lenses from about 1934, to diversify its activities. In October 1935, a dependent company, called Mizuho Kōgaku Kenkyūjo (meaning Mizuho Optical Research Institute), was set up for this purpose. It was located in the same factory ground, and it was declared as a separate company only because of the rules for the allotment of electric energy. The research on camera lenses was transferred to a new plant in Shibuya, Tagoto-chō in 1936.
The company first tried to sell camera lenses alone. Prototypes of a 105/4.5, a 75/4.5 and perhaps a 75/3.5 were assembled in mid 1936. Their design was copied on the Tessar, with four elements in three groups, and their designer was Pr. Miyata under the supervision of Mr Suzuki, chief of the optical department. The name “Zuikō” was adopted after a contest open to the company employees; it is a contraction of the first characters of “Mizuho Kōgaku”.

Back in autumn 1936, Takachiho received a subsidy of ¥9,000 to develop high aperture camera lenses from Japanese optical glass. This money was invested in the purchase of optical instruments, including an Askania optical bench installed in 1937.
Three lens designs emerged from this research: the Zuiko 65/2.7 and Falcon 65/2 advertised in 1937 for the Olympus Standard, and the Olympar f/1.5, which would be produced as the Zuiko 50/1.5 and sold to Shimazu Seisakusho for X-ray cameras around 1940.

The first camera to bear the Olympus name (only around 400 made) this Semi-Olympus (Model I) from circa 1936 is fitted with an early Zuiko 75mm f4.5 lens and is very rare with its’ Compur shutter configuration. The Deckel nameplate at the top of the shutter assembly has been covered by having an Olympus plate fitted over it. A folding camera for 16 6×4.5 exposures on 120 film. Olympus did not actually make the camera, their first Zuiko lenses were mounted on a Semi-Proud body supplied by the Japanese company Proud. In turn, the Semi-Proud was copy of the German Balda Baldax camera.

Zuiko is a brand of optical lenses that was used up to and into the Four Thirds system era. The name Zuiko means ‘Light of the Gods’, using a character from the Mizuho Optic Research Laboratory, where the lens was developed, and a character from Takachiho Corporation, which would eventually become the Olympus Corporation. With the introduction of the Micro Four Thirds system in 2008, new lenses for that system started to be branded as M.Zuiko Digital.
The company wanted to sell the lenses alone but did not find any client, so it decided to make a camera around them, under its own “Olympus” brand. It is said that this was suggested to Takachiho officials by Miyazaki Shizuma, founder of Proud-sha, who offered to supply the camera bodies.
This is how Takachiho launched its first camera, a 4.5×6 folder called Semi Olympus, said to be released in September 1936. The body was the same as the Semi Proud and the lens was the only part produced by Takachiho.
The company soon began to make its own Koho shutter and its own camera bodies. The bodies were made in the same Shibuya plant as the Zuiko lenses, and the shutters were made in the Hatagaya plant.
The Olympus Standard and the Semi Olympus II were the first cameras entirely made by Takachiho, whose prototypes were pictured in advertisements dated 1937. The former, an ambitious project led by Sakurai Eiichi, was abandoned after ten prototypes were made; the latter, designed by Mr Kitakawa, was sold until 1940.
It seems that the founder Yamashita Takeshi wanted to emulate the German company Carl Zeiss, which made microscopes and camera lenses, among the best of the time, and had entered camera production with the creation of Zeiss Ikon.
It is said that he already wanted to make cameras when he engaged Sakurai Eiichi in 1935. The Tessar was chosen as a model for the Zuiko lens, and the Semi Olympus II and Olympus Standard were positioned as rivals of the Ikonta and Contax.
However, the company chose to develop its own camera designs instead of copying the German models, unlike most other Japanese companies of the time. In Sakurai’s own words, “to make cameras the same as the others was not interesting”.

Olympus 1940 new camera camera was first announced as the Semi Olympus III and the name Semi Olympus III was probably dropped before the camera entered serial production. The Olympus Six was first advertised under that name in the December 1940 issue of Asahi Camera, and was featured in the April 1941 issue of the same magazine.
The Olympus Six was launched in 1940 in 6×6 format. It was the first of a line of 6×6 folders that would last until about 1957 with the Olympus Chrome Six series. Some of these cameras received a five-element lens called S Zuiko.
Takachiho fell under the control of Ataka Shōkai in 1939, and Chatani Yasusaburō became the CEO of the company, whereas Yamashita Takeshi resigned on the following year. In 1942, the company name became Takachiho Kōgaku Kōgyō K.K., meaning Takachiho Optical Industries Co., Ltd.
Because of the war, dispersal plants were opened in Suwa, 1943 and Ina, 1944, both in Nagano-ken (Central Japan). The Shibuya plant was evacuated to Suwa, in a former textile factory. The Hatagaya plant was not evacuated, and it was destroyed by an aerial bombing on May 25, 1945, with all the archives and the microscope production line. The production line of the Koho shutter was also located in Hatagaya and was destroyed as well; this is why Olympus stopped the production of camera shutters for a number of years.

Launched in 1952, the Olympus Flex I was the first twin-lens Medium format reflex camera manufactured by Olympus. It was developed in response to a sudden rise in the popularity of twin-lens reflex cameras in postwar Japan. Though Olympus modeled the Flex I on the Rollei Flex, it targeted an even higher level of performance, and the camera incorporated numerous unique Olympus features. A typical starting wage at this time was 7,000 JPY a month, so the 47,000 JPY price tag was equivalent to over six months’ income for an average worker.

The Olympus Chrome Six is a series of dual-format folders, taking 6×6cm and 4.5×6cm exposures, made by Takachiho and later Olympus from 1948 to 1956. The Olympus Chrome Six are horizontal folders, whose design is essentially an evolution of the previous Olympus Six. Unlike the latter, the Chrome Six has a wholly diecast construction. All the models have the ability to take 4.5×6cm pictures using a mask. No model of the Olympus Chrome Six is marked as such, and the inscriptions on the camera identify it as an “Olympus Six” instead. The name “Olympus Chrome Six” and the various model numbers only appear in the advertising material and user documentation.
The production of the Olympus Six camera was resumed in early 1946 in the Suwa plant. It is said that officials from Mamiya visited the Suwa plant on the same year, to sign contracts about the supply of Zuiko lenses for the Mamiya Six bodies.
In 1948 was launched the Olympus 35, a 35mm camera with a lens shutter, and the Olympus Chrome Six, an evolution of the Olympus Six with a die cast body.
The company headquarters at the time were in the Shibuya plant, and the logo was the same OLYMPUS TOKYO as in the pre-war period.
On January 1st, 1949 the company adopted the name Olympus Kōgaku Kōgyō K.K., meaning Olympus Optical Industrial Co., Ltd.; the official English name was Olympus Optical Co., Ltd.
An OLYMPUS OIC logo was used for some time after that date, where “OIC” stands for Optical Industrial Company. In the early 1950s, the headquarters moved back to Hatagaya, and the commercial department settled in Ginza.
In the 1950s there was a TLR vogue in Japan, and Olympus followed the trend from 1952 to 1956 with the 6×6 Olympus Flex. In 1959, after the Rolleiflex Baby Grey had initiated a short revival of the 4×4 format, the company announced the Eye 44 auto-exposure TLR, but it remained at prototype level.
During the same year 1959 Olympus launched the Pen half-frame camera, designed by Maitani Yoshihisa, the first of a long series. Its compactness and sleek lines were revolutionary at the time, and it could take 72 shots without reloading on a standard 35mm cassette. This time it was Olympus that was setting the trend, and after the Pen many other camera companies began to produce their own half-frame cameras. Olympus was the only one to make a half-frame SLR system, the Pen F, released in 1963. The Pen cameras are still popular today among enthusiasts.
1967 Olympus launched the Trip series, ingenious 35mm viewfinder cameras with automatic exposure thru lens-surrounding selenium meter. 10 million were sold until 1984.
1972 saw the launch of the OM 35mm SLR system. At a time when the large and relatively heavy Nikon F was still the workhorse of professional photographers, the compact OM system was once again revolutionary. The system incorporated a large line of highly-regarded Zuiko lenses, interchangeable focusing screens, winders and, later, advanced flash units.
While never quite challenging Nikon and Canon as the leading choice of professional photographers, Olympus did have a loyal and dedicated following for the OM system, including David Bailey and Lord Lichfield. The OM system has also kept a good reputation among astronomers, macro and micro photographers; this is related to the company’s involvement in medical and research equipment.
In 1978 Olympus launched its XA line of compact cameras. The XA is probably the smallest true rangefinder camera ever sold and was very popular among photographers as the pocket camera to carry.
During the mid-to-late ’80s Olympus lost ground to its competitors in the SLR field as autofocus took off. Research and development spending was focussed on high-selling compact point and shoots. Although the company did eventually release an autofocus SLR system it was not a serious challenge to Minolta, Nikon or Canon.

Olympus has finalized the sale of its imaging division to Japan Industrial Partners (JIP) effective January 1, 2021. OM Digital Solutions, a corporation under JIP, will take over the imaging business from Olympus. In a press release, Olympus states that the final transfer of the Imaging Business to JIP, based on the agreement both parties signed on September 30, 2020, has concluded, which included details of the arrangement. With completion of the transfer, OM Digital Solutions Corporation takes over the Imaging business from Olympus.

A trio of cameras with which Olympus competed with other Japanese companies such as Nikon and Canon.
Olympus changed its orientation and pioneered the concept of the “bridge” camera (an auto-everything SLR with fixed zoom lens) with the IS series. In the early ’90s, Olympus had significant success with the compact autofocus Stylus (or µ[mju:]) line. It carried on this success at the turn of the century into the digital field, as film camera production was ended in 2005.
When the digital market took off with the launch of reasonably affordable, compact 2.3 megapixel cameras for consumers, there were only two real options for photographers — the Nikon Coolpix or the Olympus Camedia ranges. Before the availability of affordable (sub-$5k) digital SLRs, Olympus’ E series of fixed-lens SLRs, evolved from the earlier analogue bridge cameras, was very popular among serious photographers. The launch of cheaper digital SLRs saw Olympus lose ground again among serious photographers, but in 2003 the E series was developed into an innovative interchangeable-lens SLR system.
Without the huge autofocus lens catalogue of Nikon and Canon, Olympus was free to build its system without concessions to an older 35mm-based system. Olympus is the champion of the Four-Thirds lens mount system with smaller sensor rather than the APS-sized sensors Konica Minolta, Canon and Nikon put into their DSLR bodies, which are derived from 35mm film cameras. This allowed Olympus to design its bodies and lenses specifically for digital use.
The first model of its Four-Thirds E-series of DSLRs was the Olympus E-1. It was the first professional model of the modern type compact DSLRs for interchangeable lenses. Olympus is slow in evolving its professional DSLR line but fast in delivery of new consumer DSLRs of its E-line.
Olympus has also created the Micro Four-Thirds compact camera system, which has half the focal flange distance for Four-Thirds, 6mm smaller throat size, and enables compact cameras with DSLR image quality. Therefore, it revived its famous Olympus Pen brand.
The new Pens are finder-less compact digicams for Micro-Four-Thirds lenses, having an accessory shoe where an electronic finder can be attached instead of a flash. Olympus name is also diversified to online game gates of Olympus which popular in Asia.
The company took its present name of Olympus Corporation in 2003, and it continues to innovate and to challenge other manufacturers to do so by the incorporation of features such as ‘Live-View’, tilt/swivel LCDs and full user control over the noise filter on its ‘E-System’ range of DLSRs.
In recent years, Olympus Corporation has focused on “Opto-Digital Technology” as its core competence, technological strengths that competitors cannot easily imitate, to maximize corporate value and to become one of the top optical instrument manufactures.
OLYMPUS made these FILM cameras and lenses OVER THE YEARS
Since this site is mainly concerned with analogue photography, we limit ourselves here to the list of analogue Olympus cameras and we will not consider the digital ones.

35mm Full Frame
- Olympus OM-X prototype camera
- Olympus M-1 (1972)
- Olympus OM-1 (1973–74)
- Olympus OM-1MD (1974–79)
- Olympus OM-1n (1979–87)
- Olympus OM-2 (1975–79)
- Olympus OM-2n (1979–84)
- Olympus OM-2SP / OM-2S (1984–88)
- Olympus OM-3 (1983–86)
- Olympus OM-3Ti / OM-3T (1995–2002)
- Olympus OM-4 (1983–87)
- Olympus OM-4Ti / OM-4T (1987–2002)
- Olympus OM-10 (1979–87)
- Olympus OM-10 Quartz (1980–87)
- Olympus OM-20 / OM-G (1983–87)
- Olympus OM-30 / OM-F (1983–87)
- Olympus OM-40 / OM-PC (1985–87)
- Olympus OM-707 / OM-77 (1986–91)
- Olympus OM-101 / OM-88 (1988–91)
- Olympus OM2000 (1997–)
- Olympus IS series
120 film – 4.5×6 folders
- Semi Olympus
- Semi Olympus II
120 film – 6×6 & 4.5×6 folders
- Olympus Six
- Super Olympus
- Olympus Chrome Six I and II
- Olympus Chrome Six III f/3.5 and f/2.8
- Olympus Chrome Six IVa and IVb
- Olympus Chrome Six V A and B
- Olympus Chrome Six RII A and B
120 film – TLR
- Olympus Flex I
- Olympus Flex BI
- Olympus Flex BII
- Olympus Flex A3.5
- Olympus Flex A2.8
- Olympus Flex A3.5 II

- Olympus Ace and Ace-E
35mm Half Frame
- Pen S 2.8 and 3.5 (1960–65)
- Pen W (1964–65)
- Pen D (1962–66)
- Pen D2 (1964–65)
- Pen D3 (1965–69)
- Pen EE and Pen EE (EL) (1961–68)
- Pen EE.S and Pen EE.S (EL) (1962–68)
- Pen Rapid EE.S (1965–66)
- Pen Rapid EE.D (1965–66)
- Pen EM (1965–66)
- Pen EE.D (1967–72)
- Pen EE.2 (1968–77)
- Pen EE.S2 (1968–71)
- Pen EE.3 (1973–83)
- Pen EF (1981–)
- Pen F
- Pen FT
- Pen FV
127 film – Interchangeable lens rangefinder
- Olympus Standard prototypes
127 film – TLR
- Olympus Eye 44 prototypes (f/3.5 and f/2.8)
126 film
- Olympus Quickmatic EE S, EE M, 600
APS film
- Olympus Centurion / Olympus Centurion S (SLR with fixed zoom lens)
- Olympus Newpic XB
- Olympus Newpic XB AF
- Olympus Newpic Zoom 600
- Olympus Newpic Zoom 90
- Olympus Newpic Zoom 60
- Olympus Newpic AF 200
- Olympus i Zoom 75
- Olympus i 100AF
- Olympus i snap
- Olympus 35-S/K/S II
- Olympus Wide (II)/E/S
- Olympus Auto and Auto-B Electro-Set
- Olympus Auto Eye and Auto Eye II
- Olympus 35S Electro Set and 35 SC
- Olympus 35 LE (Rangefinder)
- Olympus 35 EC, EC2, ECR (View- and Rangefinder)
- Olympus 35 ED (Rangefinder)
- Olympus 35 DC (Rangefinder)
- Olympus 35 RC (Rangefinder)
- Olympus 35 RD (Rangefinder)
- Olympus 35 SP, SPn and UC
- Olympus 35 C-AF (Olympus’ first autofocus compact)
- Olympus Accura/Superzoom series (80 Wide, etc.)
- Olympus AFL Quick Flash AFL-S & AFL-T
- Olympus AF series (AF-1, AF-10, AF-10 Super)
- Olympus AM-100 (Infinity S).
- Olympus Écru (Limited edition with retro-styling)
- Olympus Infinity AZ Super Zoom/IZM series
- Olympus LT series (LT-1, LT zoom panorama)
- Olympus O-Product
- Olympus mju Stylus Epic series II and III, Stylus/Epic and V)
- Olympus Trip 35 (metal body, 1967-1984)
- Olympus Trip Fixed Focus series (1984-2000)
- Olympus Trip (autofocus) series (plastic Trip AF MD etc.)
- Olympus XA, XA 1, XA 2, XA 3, XA 4 (1979–86)
Olympus traditionally brands all its lenses with the name Zuiko, a system begun with the very first Olympus camera released, and carried on throughout the various camera formats and systems since then.
The company sold some Zuiko 7.5cm lenses to other camera manufacturers. It also made two lenses for a third-party lens mount in the early 1950s: the Zuiko 4cm f/2.8 for Leica and the Zuiko 4cm f/3.5 for Exakta.
some OLYMPUS cameras
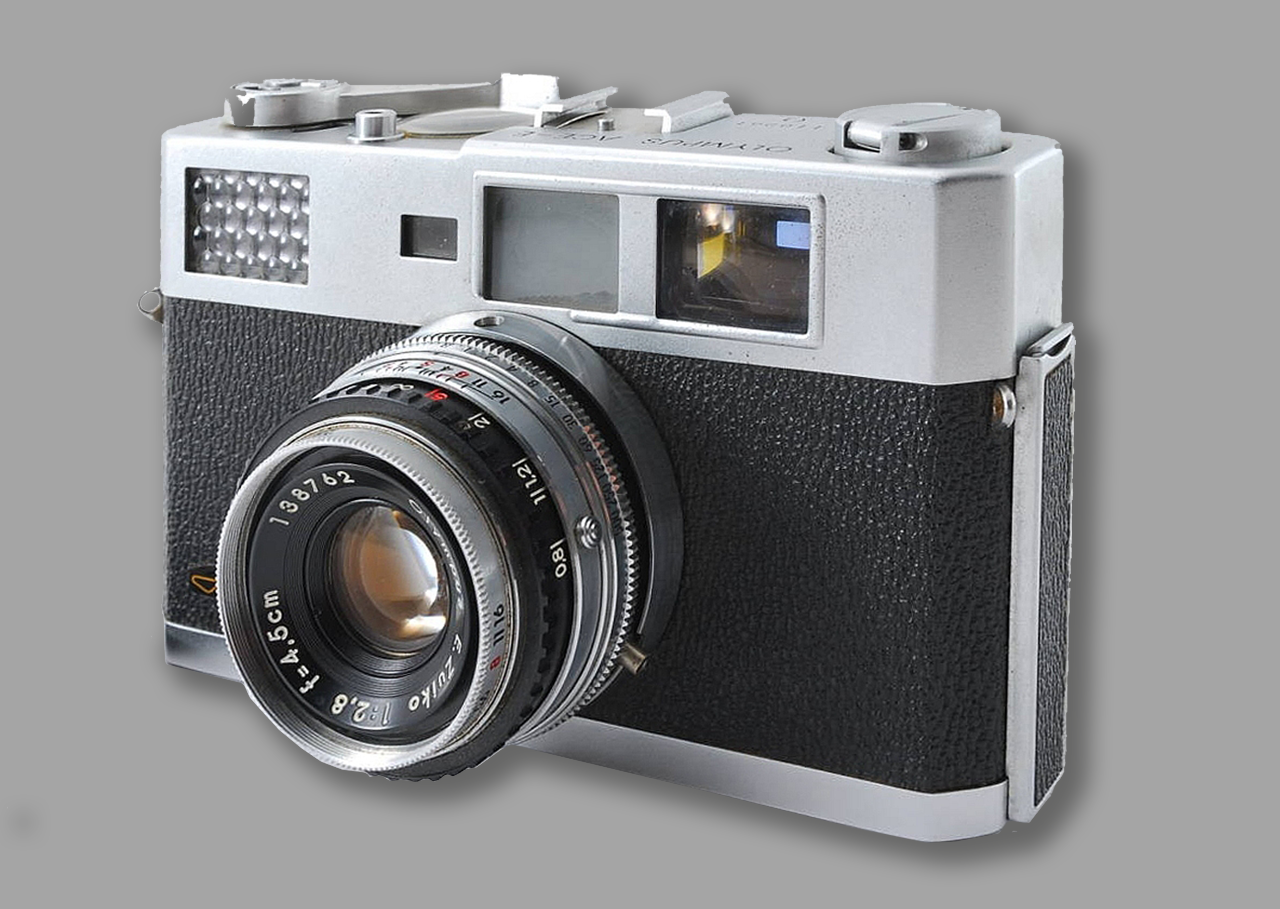
The Ace series were rangefinder cameras introduced in 1958 by Olympus, as their first and only rangefinder cameras with interchangeable lenses. There were two models, the Ace and the Ace E, introduced in December 1959, with built-in uncoupled selenium meter. During this time, Olympus wanted to enter the market as a contender to the popular Leica M3. The Ace-E had the same body with restyled top cover and featured a circular meter reading window. Its production lasted until April 1961.

In 1959, Olympus released the first of the Pen half-frame viewfinder cameras, a beautiful example of 1950s camera design. The ultimate iteration of the Pen family was the F, essentially a scaled-down SLR in a beautifully minimalist body, with a suite of fantastic Zuiko lenses. The Pen F was not only a thoroughbred amongst half-frames, it was also a beautiful object, showing the nascent genius of its designer, Yoshihasa Maitani.

The Olympus µ[mju:] (US: ∞ Stylus) was a fully automatic 35mm compact camera introduced by Olympus in 1991. The Stylus was the first model in the hugely successful Olympus mju/Stylus series, selling 5 million on its own. Evolved by camera designer Maitani Yoshihisa from his Olympus XA design, the µ[mju:] was very small and curvy, with an integrated lens cover. It is switched on by shifting the lens cover to one side. The original mju/Stylus was generally available in black, but a LIMITED edition model (50,000 examples) with a metallic silver finish was also released.
FOUNDING DATE: 1964 (1953)
FOUNDER: AGFA AG
COMPANY NAMES:
1873: AGFA (Actien-Gesellschaft für Anilin-Fabrikation); 1945: VEB Film und Chemiefaserwerk Agfa Wolfen; 1953: Agfa Wolfen was returned to the GDR by the USSR; 1964: 1970: VEB Fotochemisches Kombinat Wolfen; 1990: ORWO AG; 1994: The Treuhand liquidated the company; 1996: ORWO films were put back on the market; 1997: declared insolvent; 1999: Lintec Computer AG; 2000: PixelNet AG enters; 2002: PixelNet AG, and its subsidiary ORWO Media, filed an application for bankruptcy.
COMPANY ADDRESSES:
1867: Rummelsburger See near Berlin; 1910: Röntgenstraße 3, Chemiepark Bitterfeld-Wolfen; 1945: Röntgenstraße 3, Chemiepark Bitterfeld-Wolfen East-Germany;
ORWO (for ORiginal WOlfen) is a registered trademark of the company ORWO Net GmbH, based in Wolfen and is also traditionally known for black and white film products, made in Germany and sold under the flag of the ORWO brand.

Aerial shot of the Agfa-Filmfabrik Wolfen GmbH in 1929 on the Chemiepark Bitterfeld-Wolfen
The Agfa-Wolfen plant after WWII
On 20 April 1945, following the defeat of Nazi Germany in World War II, the Wolfen plant was taken over by US forces, and important patents and other documents regarding the Agfacolor process were confiscated and handed over to Western competitors, such as Kodak and Ilford.
As the plant was located in what was to become the Soviet zone of occupied Germany, the US forces then handed it over to the Soviet military administration, which dismantled large parts of the plant and moved it, with key German staff, to Svema in Shostka, Ukraine, where it formed the basis for the Soviet colour film industry.
AGFA was split into two companies each with one of the two plants: Agfa AG, Leverkusen in West Germany, and VEB Film und Chemiefaserwerk Agfa Wolfen in East Germany, which later adopted the brand ORWO.
Agfa AG (Leverkusen), by then a subsidiary of Bayer was subsequently merged with Gevaert based in Mortsel, Belgium in 1964 to form Agfa-Gevaert.
A color dye factory was established at the Rummelsburger See near Berlin in 1867, its name was changed to AGFA (Aktien-Gesellschaft für Anilin-Fabrikation) in 1873.
AGFA in 1910 and its original Leverkusen works around the same time established the Wolfen plant. In 1911, the first casting plant at Wolfen for polymer films (nitrocellulose) was built by AGFA.
By 1925, with AGFA now part of the industrial conglomerate I.G. Farben, Wolfen was specialising in film production and Leverkusen was specialising in photographic paper. In 1932, the process of making Triacetate Cellulose (TAC) film was patented at the Wolfen facility.
The Agfa Wolfen plant developed the first modern colour film, which incorporated colour couplers, Agfacolor Neu, in 1936, which simplified processing compared to its contemporary Kodak Kodachrome from 1935.
The Agfacolor Neu film from1936 invented by Wilhelm Schneider and Gustav Wilmanns Filmfabrik Wolfen, was based on the subtractive 3 color principle: Chromogenic monopack, reversal (from 1936), negative/positive process (from 1939).

American infantrymen of the U.S. 11th Armored Division supported by an M4 Sherman tank move through a smoke filled street, April 1945.

The post-war confusion summarized in one photo: Agfa and Orwo materials brotherly united.
continued
ORWO-branded 35mm colour slide film became available in the United Kingdom in the 1970s through magazine advertisements for mail order suppliers. It was a cheaper alternative to the mainstream brands available at the time.
ORWO prepared the changeover from AgfaColor to C-41, similar to considerations in the USSR, but had not completed until the end of the GDR, which led to decreasing sales figures in the western countries, where the Kodak C-41 process dominated the market.
In 1989, at its peak, a total of 14,500 employees were employed at the Wolfen site, encompassing an area of 165 hectares.
- They produced 40 million square meters of base material, of which 50 percent was processed to raw film.
- There were 2,500 assemblies, producing a total of 200 different film types.
- The production height of magnetic recording materials was 2 million square meters, and in the chemical fibre sector, around 100,000 tons of various pulp, viscose products and special products were delivered.
The birth of a film brand
On the last day of 1953, Agfa Wolfen was returned to the GDR by the USSR as one of the last reparations companies. At this time the company still shared the AGFA trademark with Agfa Leverkusen and both companies produced films under the AGFA brand with the same names, such as Isopan F. To distinguish them, the film edge markings were L IF for Agfa Leverkusen, and W IF for Agfa Wolfen. Trading of materials however continued between plants.
In 1953 in a trade agreement it was agreed that VEB Film und Chemiefaserwerk would have the sole rights to the AGFA brand in Eastern Europe and Agfa AG, would retain sole rights to the AGFA brand in the rest of the world. This hampered Wolfens exports and therefore after 1964 films from Wolfen were rebranded ORWO (ORiginal WOlfen).
After the formation of the Combine VEB Fotochemisches Kombinat Wolfen in 1970 the VEB ORWO Filmfabrik Wolfen became its headquarters.
Founder members of the new Combine were:
- Fotopapierwerke Dresden,
- Fotopapierwerke Wernigerode,
- Gelatinewerke Calbe,
- Fotochemische Werke Berlin and
- the Lichtpausenwerk Berlin.
The now Kombinat also began developing and producing other information recording materials, such as magnetic, video and computer tapes.

Electronics, photo / film / video, packaging examples from ORWO, produced by Kombinat Filmfabrik Wolfen, GDR, since 1963 / 1964.
Privatisation and Breakup
Following German reunification in 1990 the holding company was privatised as ORWO AG with Folienwerk Wolfen GmbH an early spin off. The Treuhand liquidated the company in 1994 and film production ceased.
Attempts were made to revive the company and in 1995, Berlin-based photo merchant Heinrich Mandermann joined ORWO, and on April 1, 1996, ORWO films were put back on the market. However, they were no longer produced locally, merely assembled from products from other manufacturers such as Forte and Ilford. Due to the owners illness the company was again insolvent in 1997.
A number of separate successor companies emerged from the remnants of the former industrial behemoth;
- Folienwerk Wolfen GmbH founded 1991, PET films for packaging, printing, medical and industrial uses.
- Organica Feinchemie GmbH Wolfen, founded in 1995, organic fine chemistry.
- FEW Chemicals GmbH, founded 1997, speciality and fine chemistry.
- Island Polymer Industries GmbH, founded 1998, Triacetate Cellulose (TAC) film production using former ORWO Wolfen facility, for photographic (film base) and optical markets, largest cast film manufacturer in Europe.
- ORWO FilmoTec GmbH, founded 1998, Cine films and related technical films.
- ORWO Net AG ,founded 1999, Digital photo supplies, photofinishing.
All suppliers for the optical, electrical and film industries
The ORWO Net GmbH retained the rights to the ORWO trademark for a variety of photographic products.
filmotec
The FilmoTec GmbH was formed in 1998 to continue to manufacture a range of Black and white camera and technical films for motion picture use under the ORWO brand. Film coating was contracted out, to Ilford and later InovisCoat. In 2020, twenty employees work in the areas of research, development, production, configuration, and distribution of ORWO black and white films.
Products are particularly aimed towards the technical needs of the world’s archiving, motion picture, and holographic industries. FilmoTec is with Kodak now one of only two companies still producing black and white films for motion picture use.
In partnership with ORWO North America, ORWO film currently supplies all US Library of Congress black and white industrial films, in addition to high-profile archival clients like the Smithsonian and MOMA. For example, black-and-white movies that have been selected by the US Library of Congress for archival copy preservation in the last five years have been most likely reprocessed onto ORWO film.

ORWO-Filmotec in 2012.

The ORWO family
In 2020 FilmoTec was brought under common ownership with film coating company InovisCoat, based in Monheim am Rhein, Germany to offer products for the film industry under the traditional brand “ORWO”, both companies sharing AGFA heritage.
In particular the new ownership structure with Filmotec and InovisCoat together with a number of other companies unites the ORWO brand, its Intellectual Property, Recipes and Research & Development with film manufacturing capabilities for the first time since ORWO AGs liquidation in 1994.
Former employees of the consumer film division of Agfa-Gevaert founded InovisCoat, with its film coating plant based at Leverkusen, Germany which was spun off into a new company Agfa-Photo in 2004. The company (Agfa-Photo GmbH) folded a year later in 2005, although a separate holding company still retains the license rights to the Agfa-Photo brand.
InovisCoat brought together technical expertise in film emulsions and coating with acquisition of one of the former Leverkusen wide coating machines for film production, and a smaller narrow coating machine for testing, relocated to new premises in Monnheim on Rhein, the new smaller scale facility capable of multi-layer film coating for both photographic and other applications. It undertakes the manufacture of coated films for a number of companies including Polaroid B.V., Adox, Bergger, Lomography and more recently ORWO Filmotec.
The companies being brought together under the ORWO name; holding company Seal 1818 GmbH, FilmoTec GmbH and InovisCoat GmbH underwent an organised restructure in 2022, to enable the introduction of new working practices and products, which due to legacy issues would otherwise prevent the company being able to quickly launch new products under the licensed ORWO name and Logo. The ORWO Net GmbH is holding all brand rights and they sell personalized photo products under the brand ORWO.
Filmotec announced the introduction of two new films to the market in 2022, a new black & white film for still camera use (expected April 2022) and a new colour cine film stock using ECN-2 development process (expected July 2022), which would provide cinematographers with an alternative to the Kodak vision 3 colour camera stocks.

- NC color negative (e.g. NC16, NC19, NC20);
- NI infra red black and white negative film (NI750);
- NP black and white panchromatic negative film (e.g. NP15, NP20, NP22) or high speed superpanchromatic film (NP27);
- UK color slides for tungsten light (e.g. UK17, UK20);
- UP black and white panchromatic slides (UP15);
- UT color slides for daylight (e.g. UT16, UT18, UT20, UT21);
The numbers in film designations indicated gamma value available for a given film (1 = soft, 5 = very hard). F-type materials were available first as plates, then as sheet films from 9×12 cm to 29.7×42 cm, as well as 68 mm and 105 mm wide roll films.
- DK (Dokumentenfilm) – hard black and white orthochromatic film for reproducing line drawings and text documents (e.g. DK3, DK5);
- FO (Fototechnischer Film Orthochromatisch) – orthochromatic film for reproductions (e.g. FO1, FO4, FO5);
- FP (Fototechnischer Film Panchromatisch) – panchromatic film for reproductions (e.g. FP1, FP2, FP3, FP4);
- FU (Fototechnischer Film Unsensibilisiert) – color blind film for reproductions (e.g. FU1, FU2, FU3, FU5);
- PF (Positiv Feinkornfilm) – small grain color blind film for projection purposes (PF1);
Current Products
B & w camera film
- UN54, Universal Negative Film 100 ISO, Panchromatic medium speed black-and-white negative camera film for both outdoor and indoor usage. Formats: 16mm/35mm, 122m/400ft (16mm/35mm) on core and 305m/1000ft on core (35mm).
- N75, Negative film 400 ISO, High speed black-and-white panchromatic camera film for both outdoor and indoor usage. Formats: 16mm/35mm, 30.5m/100ft, 122m/400ft (16mm/35mm) on core and 305m/1000ft on core (35mm).
- Their motion picture camera films UN54 and N75 are also widely re-packaged by third parties as still camera film.
Current Products
Colour Camera film
- NC500, 400 ASA, Colour film. Formats: 16mm (100ft & 400ft) & 35mm (400ft, 1000ft, 2000ft)
Current Products
Other products
- Laboratory films
- Duplicating films
- Sound Recording Film
- Holographic films
- Leader films
- Special films
Discontinued products
- Still camera film
- Magnetic tape
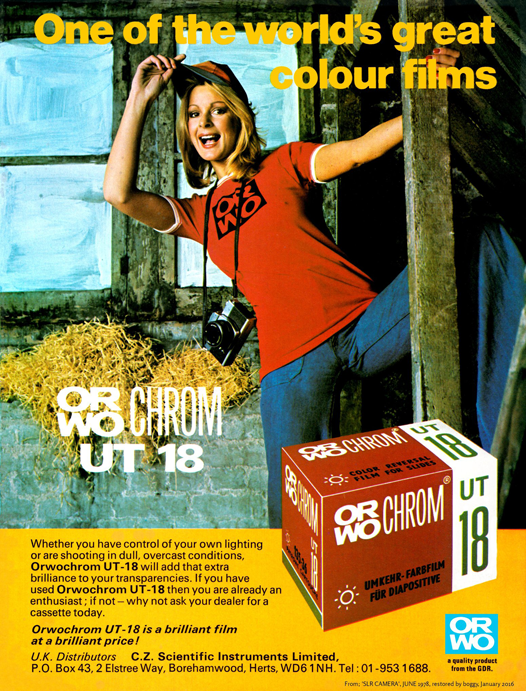
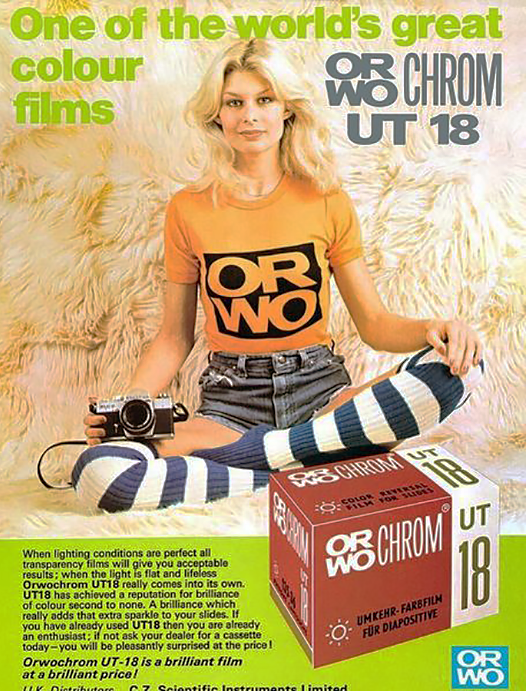
FOUNDER: Umberto Nistri

1926: Società Anonima Ottico Meccanica Italiana (OMI); 1937: S.A. Ottico Meccanica Italiana e Rilevamenti Aerofotogrammetrici; 1981: purchased by the aircraft company Agusta and the photography business was split into S.A.R.A. Nistri (air photography) and Aerofotogrammetrica Nistri;
COMPANY ADDRESSES:
1926: Rome;
OMI in short
From one surprise to another …
The Ottico Meccanica Italiana (OMI) from Umberto Nistri has launched two cameras in the past, namely the Sunshine and the Rollina. Not something to surprise you about, but then it turns out how you can be mistaken..
I should have been warned when I found out that the Sunshine (a very very tourist name) was a special camera. With this 35mm camera with accompanying, linked projector, Umberto designed a method to project color photos. At that time – we speak from 1947 – the use of color film was still rare and precious. I will come back later on the precise construction of this camera combination.
Together with his brother Amedeo, he designed a number of cameras for taking aerial photos and equipment for photogrammetry, and later they produced more general aviation instruments. They also designed a machine gun camera for training purposes.
At the beginning of the Second World War (1939-1940), OMI secretly produced an electromechanical coding machine that was used by the Italian army (ErSetico region), the Air Force (Regia Aeronautics) and the Navy (Regia Marina). The machine was called Cryptograph Alpha and was based on the same principle as the German Enigma coding machine.
Umberto Nistri died on 24 April 1962 and was followed by his son Rafaello, who led the company for another 20 years. Following Rafaello’s death in 1981, the Italian helicopter manufacturer Agusta acquired the company.
During his long and impressive career, Umberto Nistri won numerous awards, received honorary degrees from universities around the world, and was an honorary member of the most prestigious societies and academic institutions.
In his hometown Rome, a street nearby the historic headquarters of the OMI Company has been named after him.
Umberto Nistri was born in Rome on 16 September 1895, the eldest son of Raffaello and Letizia Nistri. The father, whose family was of peasant origin, embarked on a military career as a young man and moved to Rome in today’s Prati district. Umberto was the first of the family to undertake regular studies, followed by his parents in the hope that with his brothers he could achieve a better social position.
As the family grew – there were six children – the Nistris moved to the Monte Mario area, inside the Forte Trionfale, in a service accommodation to which their father, assistant at the military engineers, was entitled. Nearby, in the area that now houses the Astronomical Observatory, once stood Villa Mellini, then the headquarters of the photographic section and the balloonists of the Battalion of Military Engineering Specialists. The more rigorous ban on approaching the villa for safety reasons and the curiosity that those bans aroused in him, it must have stimulated the vocation for aerial photography.
In 1913 he graduated as a surveyor (land surveyor expert). Despite his desire to become an engineer, the need to bring financial help to the family made him desist from continuing his studies to accept the first topographical works.
The outbreak of the Great War and Italy’s entry into the conflict in 1915 marked his life and career. As a soldier he would have liked to enter the air force, but the promise made to his mother not to devote himself to the then pioneering flying activity made him opt for a course as cadet officers of field artillery.
He returned home briefly in 1916 when his mother’s health deteriorated, leading to her death. So, feeling released from the promise to give up the flight, he asked for a transfer to the air force. In May 1917 in the Centocelle field, in Rome, he participated in the course for the function of airplane observer, or technician assigned to travel with the pilots to observe the territory and photograph the enemy positions. Destined for the 35th squadron stationed in Santa Giustina di Belluno, on the Piave, he deserved two silver medals for military valour for war actions.
At the end of the conflict, following the death of his father in 1918, he took on the task of looking after his younger brothers, with the help of his brother Amedeo, and to meet the needs of the family, he decided to remain in the Air Force. In 1919 he married Lola, an elementary school teacher, who bore him two sons: Paolo Emilio and Raffaello.
Having had the opportunity to fly, photograph, map in military action, he returned to it, with great results, once the war was over.
The war events had allowed him to gain the necessary experience to design a tool capable of describing in detail the plan metric and morphological aspects of the territory, obtaining topographic plans from stereoscopic aerial photographs.
In 1919 he obtained his first patent with the rudimentary prototype of the ‘photo cartographer’, i.e. the aero-photogrammetric restorer of which he prepared the definitive version in 1922.
Already in 1919, as commander of the Air Force’s Aerial Observation School, he carried out the photogrammetric survey of a short stretch of the banks of the Tiber for the Office of the Roman Agro, for the reorganization of the riverbed.
This first operation, carried out by an airplane with a semi-automatic camera, a war remnant, from which metric elements linked to a network of benchmarks previously arranged and surveyed on the ground were obtained, undoubtedly constitutes the official birth certificate of the Italian aero photogrammetric experience.
The following year, thanks to a not yet definitive version of the photo-cartographer, it was possible to experiment with the ‘Nistri photogrammetric method’ at scale 1:1250, demonstrating the remarkable practical application of the system. Other patents for the following models of the photo-cartographer were dated 1925 (model II) and 1929 (model III); to finance studies in the field of aero-photogrammetry, Nistri also designed and built the first air navigation instruments.

The Model II Photocartographer built in Rome by “Ottico Meccanica Italiana” (O.M.I.).

Aerial photography in the very beginning
In 1921, with his brother Amedeo, he founded the Società Anonymous aerial photogrammetric surveys (SARA-Nistri), the first industrially organized company for the production of topographic maps through aerial photographs and the use of photogrammetry tools. In July 1923, the first nucleus of the Italian optical mechanics and aerophotogrammetric surveys (OMI) was established.
In 1930 the order of engineers enrolled him in its register, in 1932 he was recalled to the Air Force with the rank of captain with the aim of designing an air navigation system in the absence of reference points on the ground. The instrument, called the ‘artificial horizon’, was used by the planes that carried out the historic Atlantic cruise led by Italo Balbo, who in recognition promoted Nistri major for special merits. He retired with the rank of lieutenant colonel.
Despite the recognitions and certificates of esteem, which earned him great fame, including internationally, the first years of OMI were not easy, due to the great competition from foreign companies and, above all, due to the difficulties encountered in making the goodness of the new method understood by sceptical operators in the sector, still tied to traditional topographic survey systems.
Gradually, again thanks to the help of the Air Force, which guaranteed the adoption of Nistri instruments, the company began to establish itself both in Italy and abroad. With the success of the 1930s, the first factory proved too small for the growing number of job orders and employees, so in 1937 OMI moved near the basilica of S. Paolo, in a large building built specifically in Via della Vasca Naval. The first commercial cartographic works date back to the 1930s, such as the maps of the centre and of the municipal territory of São Paulo in Brazil (1929-32) which decreed the definitive success of the method and gave Nistri great international visibility.
The premature death of his brother Amedeo, in 1936, and the outbreak of the Second World War, led to a sudden interruption of the activities of SARA and to a block in the production of OMI, with the risk of losing all the equipment supplied. After the war, after an initial period of slow recovery, the cartographic restitution tools produced by OMI turned out to be the most widespread machines on the markets all over the world. In 1961, with the advent of the computer, OMI created the world’s first numerical photogrammetry instrument using the concepts and patents of Uki Helava.
During his long and prestigious career as an industrialist, Nistri obtained numerous honours, starting with the knighting of his work in 1938, «for having created an industry of national interest and created an innovative technology of international importance».
He was professor in charge of air navigation instrumentation in the engineering faculty of the University of Rome La Sapienza; he was awarded an honorary degree from the Milan Polytechnic; he was an honorary member of the International Photogrammetry Society and a founding honorary member of the Italian Photogrammetry Society. Furthermore, he received various certificates and recognitions from academic and state bodies in Brazil, Argentina, the United States, Great Britain, France, Greece and the Netherlands.
Nistri died in Rome on April 24, 1962. A street in Rome was named after him near the historic headquarters of the OMI.
The figure and character of Nistri cannot be fully assessed if one does not refer to his sensitivity to social problems, mentioning those initiatives which, in advance of the laws of the State, made him well liked by his employees: he was the first Italian industrialist to spontaneously guarantee salaries to employees on national holidays (religious and state), the health insurance and the company’s internal medical service and to finance, with great generosity, the most diverse sports activities for workers. At his funeral, managed entirely by his employees as a sign of gratitude, he attended the guard of honour of the Air Force, reserved only for the highly decorated Arma.

An Italian officer drawing a “trench map” from an aerial photo image through a graphic method.
OMI-Products and innovations
So much for the life story of Umberto Nistri. What now follows are his remarkable inventions in the field of aerial and color photography, the construction of an electrical/mechanical encoding machine and a jukebox with video tapes on the principle of that with gramophone records. First of all it is the turn of the cameras to be described, followed by the other two topics.
Aerial cameras
OMI designed and made equipment for surveying and photogrammetry, including aerial cameras and later more general aeronautical instruments. Not surprisingly, given the period the firm was active, the products included military ones, including a machine-gun camera (for training gunners by filming the target ‘shot’ with a gun-shaped cine camera in exercises).

The exact relationship between SARA and OMI seems to have varied; patents up to about 1935 are in the name of ‘Ottico Meccanica Italiana S.A.’, while later ones are in the name ‘S.A. Ottico Meccanica Italiana e Rilevamenti Aerofotogrammetrici’, suggesting the two companies may have merged for a period, but this distinction is not consistent in all patent filings. Many patents were filed in the name of Umberto Nistri himself.

Early OMI aerial camera (±1930)

This camera was used for taking aerial photographs or for filming in flight. This device was held in the photographer’s hand using the two wooden grips. The photographer framed the subject through the viewfinder, adjusted the aperture and inserted, if necessary, the yellow filter (to underline the contrast, especially in the presence of fog or clouds). Finally, he pressed the shutter button. When the shot was finished, he would turn the film advance wheel.
This film camera (measurements: 36cm x 43cm x 23cm) is mainly made of metal and has an approximately trapezoidal shape. Laterally there are two large wooden handles and a leather strap for transport and grip. The film holder (12x17cm format) is housed in the rear part. On the side of it is a large wheel which allows the film to advance and which has a frame counter consisting of a small window which allows the reading of the exposure number (from 0 to 79). The actual camera is inserted in front of the film holder, on which a foldable Newtonian viewfinder and the shutter device are mounted. The camera ends with the objective holder covered by a metal cap, with a diaphragm adjustment device (possible positions 4.5 – 6.3 – 9) and a lever for inserting a yellow filter. Inside the lens holder is the fixed focus lens with the filter connected via a flip-up device.
OMI APR 87A (± 1940)

The OMI APR 87A is an aerial camera 6.5x9cm exposures on 70mm film.
OMI APR3 (± 1940)

The OMI APR3 is a military camera for aerial shots, it has a roll film or 13x18cm film format. This camera is still one of the first models supplied to the Armed Forces, to be used by hand and not those attached under the bridge of the plane and controlled from the cockpit.
The structure is in light alloy, die-cast with a truncated pyramid shape and curtain shutter. The APR3 has a curtain shutter that fires at 1/100sec. at 1/500sec. To quickly arm the shutter after taking the photo, the APR3 has a quick charge via a lever located near the shutter button, so you never take your hands off the camera. The lens is a Koristka 250mm f4.5. Insertion of the yellow contrast filter using a lever located on the side of the camera.
In the photo, an Italian airman looking out the window of an airplane, holding the camera. He was probably in charge of the machine gun that can be seen next to him and, in his “lost” time, he took some souvenir photos.
OMI AP 57 (± 1940)

The OMI AP 57 is a small military camera for aerial photography, it has a roll film format of 6.5x9cm. This model was not attached to the aircraft but was used manually by someone on board. The structure is in die-cast light alloy with a truncated pyramid shape and curtain shutter. The lens is an Officine Galileo Aerostigmat 135mm f3.5. Complete with its black and white filters from Officine Galileo.
the two types of photo cameras
OMI is known for two cameras beside its aerial products as described before. OMI tried to find a civilian market after making a great deal of military goods during the War. These civilian products were compulsory under post-War administration. Two 35mm cameras were born after the Second World War: the Sunshine color separation camera and the perfectly normal Rollina, made for everyday use. Below is a detailed description of both camera types.
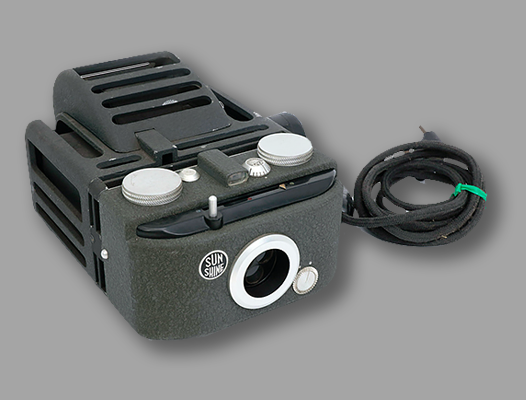
The OMI Sunshine Model-I with coupled projector.

The OMI Sunshine Model-II with separate projector.
OMI Sunshine
At the 1946 Milan Fair, a Milanese trading company, SIRCE presented a special photographic device called SUNSHINE whose production was entrusted to OMI. The Sunshine was composed of two parts: the actual camera to be used for shooting and a projector to be combined with the camera to perform projections with it.
The camera was fitted with a fixed focus lens (Omiterna 35/3.5) which was composed of three small lenses arranged in a radial fashion; behind each lens was positioned a coloured filter of a different colour and corresponding to one of the three basic colours (blue, red and yellow).
At each take the three objectives produced three small 8×11 mm frames each filtered through one of the fundamental colours. After having developed the film and obtained triads of black-white slides, these were introduced again in the Sunshine which, however, was used as a projector and the three frames projected simultaneously so that each one was filtered by the same objective that had generated it, gave rise to a colour image.
It was possible to adjust the diaphragm between two positions: the maximum aperture was used in projection while the smallest aperture was used for shooting to obtain greater depth of field; there was a third regulation in which the coloured filters were excluded and each lens had a different aperture, thus obtaining three black-white frames with different exposures.
The camera is rather simple. The shutter has speeds 1/25 and 1/50 second, plus ‘B’. There is a sliding aperture control above the lens, giving f/3.5, f/6.3 and f/9. There is a Reverse-Galilean viewfinder on the top, and film advance and rewind knobs, with a frame counter. There is no focus control. Two different models of Sunshine were built which differed only in the different shutter potential: one model allowed a single speed (1/50) plus bulb while a second model, introduced in 1947, allowed two speeds (1/25 and 1/50) and the usual pose B.
As the very low serial numbers of the cited examples suggest, few of the cameras were made. It is a curious product for its time, when several color films were already in production in 35 mm size. Therefore, Sunshine’s production lasted only a few years because the possibility of using the new colour films presented in those years, such as Ferraniacolor, made trichromatic devices obsolete, if not useless, decreeing their death.
OMI Rollina

Subsequently, around 1950, OMI presented a more traditional simple 35 mm viewfinder camera called ROLLINA.
The Rollina was equipped with a 50 mm 1:6.3 objective, called Lunar, and a three-speed shutter from 1/25 to 1/100 plus ‘B’, and an optical viewfinder.
In the meantime, the new political conditions that had consolidated in Italy allowed OMI to return to produce military apparatus and equipment and the brief parenthesis in the world of photography for civilian use came to an end.
Another strange development of Umberto Nistri:
The Cinebox was a device which, loaded with a hundred lire coin, offered songs with a view. In 1959 it was presented as “the cinematic bomb of the century”. It was the Cinebox, in short a video jukebox that contained 40 original short films (3 minutes each) in colour of songs from the time. Thus the first video clips were born.
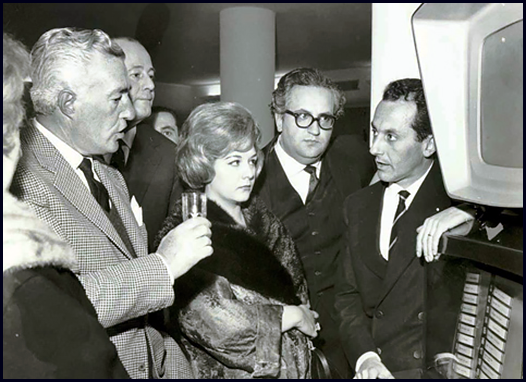
Rome, May 1959. The great actor and film director Vittorio De Sica with chief executive of OMI Paolo Emilio Nistri present Cinebox at the Rome Trade Fair.

In the 60s the Cinebox and Scopitone devices with similar characteristics, distributed in public places tried to steal the show from the more widespread and popular jukeboxes, challenging them on the same ground as musical entertainment. In addition to the songs, they also allowed you to select the related color music videos.
The Cinebox was a coin-operated Italian 16mm film projector jukebox type machine invented in 1959 that appeared in Europe to rival the French made Scopitone that appeared in 1960. The Cinebox was manufactured in Rome by Ottico Meccanica Italiana.
This device with the size of a two-door wardrobe, conceived as a driving force for the song market was born from the business agreement between Pietro Granelli, an inventor by profession, and Paolo Emilio Nistri, managing director of OMI.
A year later Nistri handed over the project to Angelo Bottani, a Milanese entrepreneur who collaborated with the president of Inter Angelo Moratti who, through the SIF (International Phonovision Company) with headquarters in Milan and branches throughout Europe and the United States, proposed the appliance on markets around the world.
In the meantime, Mi-Val, the motorcycle factory in Gardone VT, replaced OMI in the assembly and the Di Giuseppe Marai company in Salò began to take care of distribution.
In 1963 it appeared in the USA and was retitled Colorama in 1965. In 1961 Cinebox machines were placed on ocean liners of the American Export Lines with Cineboxes showing cartoons and short subject comedies in on board nurseries whilst on board lounges showed musical and travelogues. Each of the Cineboxes held five 40 minute films.
In the United States the Cinebox musical juke box provided three minutes of sound film for 25 cents with 40 titles available at a time on the machine.
However, the Cinebox was short-lived due to the high management costs, partly due to the censorship that kept the appeal low, and finally because the monotheism of the television screen would soon become dominant. In the United States, the network of devices fell into the hands of the mafia, decreeing the end of the adventure.
In Canada, the Cinebox became the first e.commerce website (cinebox.net), founded by Loïc Berthout, to sell movies (DVD) online in 1998. It then proposed video games and reached an international scope. It was also selling through cinebox.com until 2010.


Last but absolutely not least:
At the outbreak of WWII, OMI’s and sister company SARA-Nistri’s regular business came to a halt, and the company had a hard time surviving. The company survived as they had secretly developed a high-end electromechanical cipher machine for the Italian Armed Forces. The machine was called Cryptograph Alpha and was based on the same principle as the German Zählwerk Enigma. It was used by the Italian Army (Regio Ersetico), the Air Force (Regia Aeronautica) and the Navy (Regia Marina) during WWII.
At present we know of the existence of four different models of cipher machines made by OMI-Nistri during and after WWII. Although very little information about these machines is available in the public domain, we have tried to give a detailed description of each model.
This was only possible with the article on this machines of the cryptomuseum and the kind cooperation of collector Günter Hütter in Austria, who has acquired a Cryptograph-CR Mk II in 2013 and allowed the cryptomuseum to photograph it and measure the wiring. Other information has been taken from an NSA report that was declassified in 2014.
Cross-sections of the various cipher machines

Controls of the Cryptograph-Alpha.

The image above shows the complete drum of the Cryptograph-Alpha with the entry disc on the right and the reflector on the left.
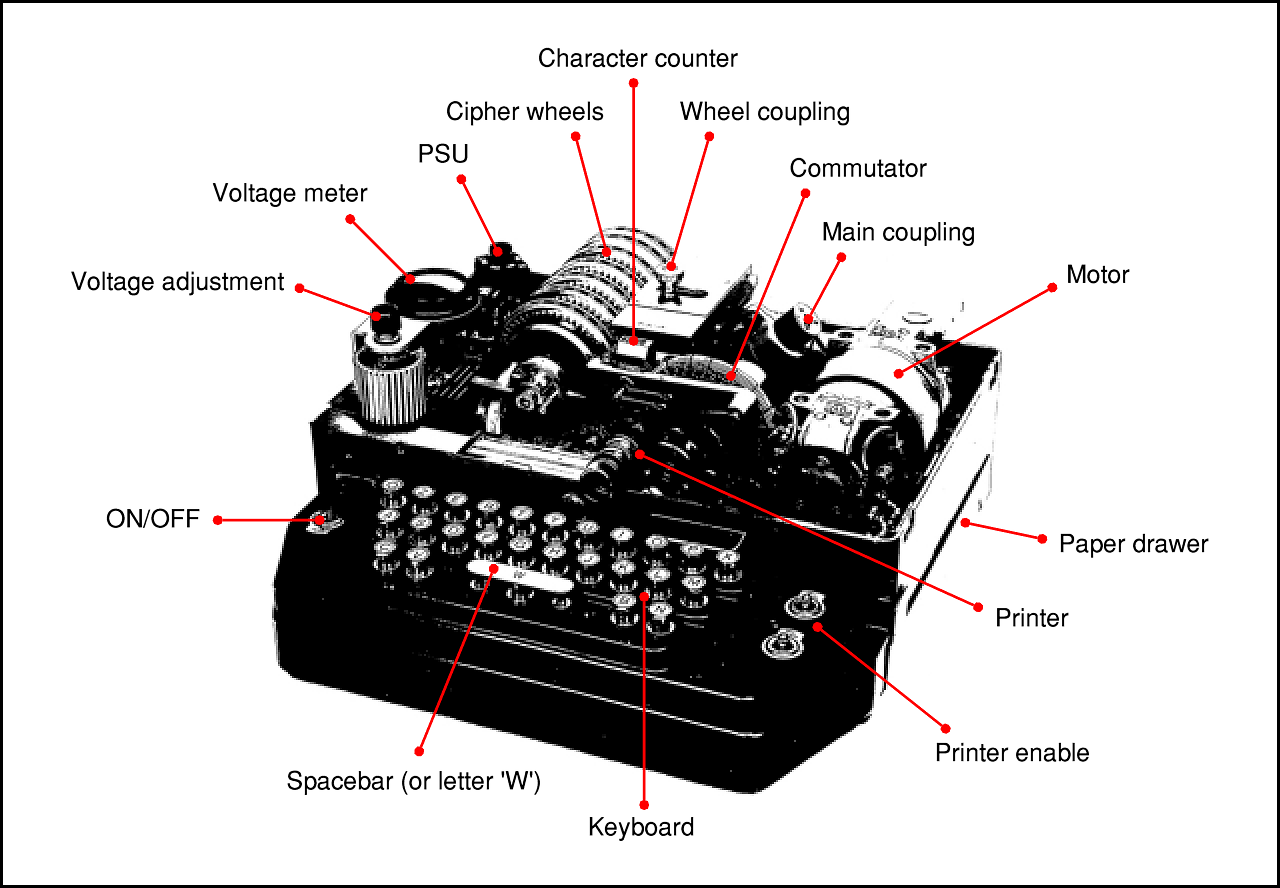
Controls of the Criptograph.
The OMI Cryptograph-Alpha
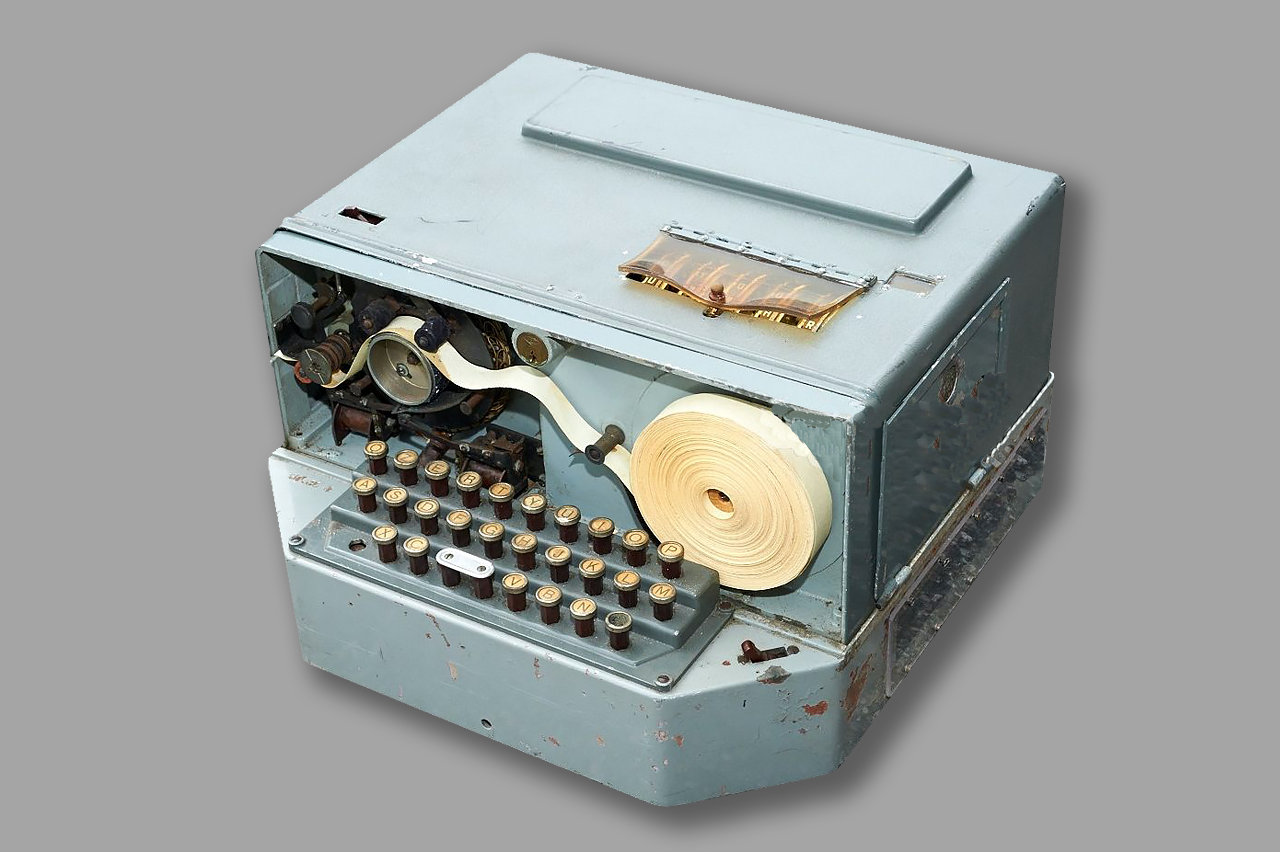
The image shows a typical Alpha cipher machine in Naval grey colours. The machine is very similar to the German Zählwerk Enigma.
The Cryptograph-Alpha, is a wheel-based electromechanical cipher machine, developed and produced around 1939, at the start of WWII. Little information about this machine is available in the public domain. Only a small number of machines have survived.
The Alpha had 5 moving cipher wheels of which the leftmost one was the reflector. The machine features irregular stepping of the cipher wheels, controlled by stepping pins, or notches, at the circumference of each wheel, similar to the stepping of the Zählwerk Enigma.
The difference with the Enigma however, is that the Alpha has one more cipher wheel and that it is motor-driven, making it faster in operation. Furthermore, it prints its output directly onto a paper strip, allowing the machine to be operated by a single person. The keyboard has 26 keys, representing the 26 letters of the Latin alphabet, of which the letter ‘W’ is used as the spacebar. Each key controls the electrical contacts of the coding circuit. The main supply was 120 – 160 – 220 – 260 Volt 42 – 50 Hz or 12 Volt DC.
The diagram on the left shows the various controls and features of the OMI Alpha. The mechanism is built on a raised chassis, with the keyboard at the front. The keys are in the QZERTY order. An extra paper advance key is present at the bottom right. At the front left is the built-in printer that produces its output on a paper strip that is fed in from the right. The five cipher wheels are located at the right, immediately behind the paper supply, and protrude the top cover of the machine, so that they can be set without opening the machine.
OMI Criptograph
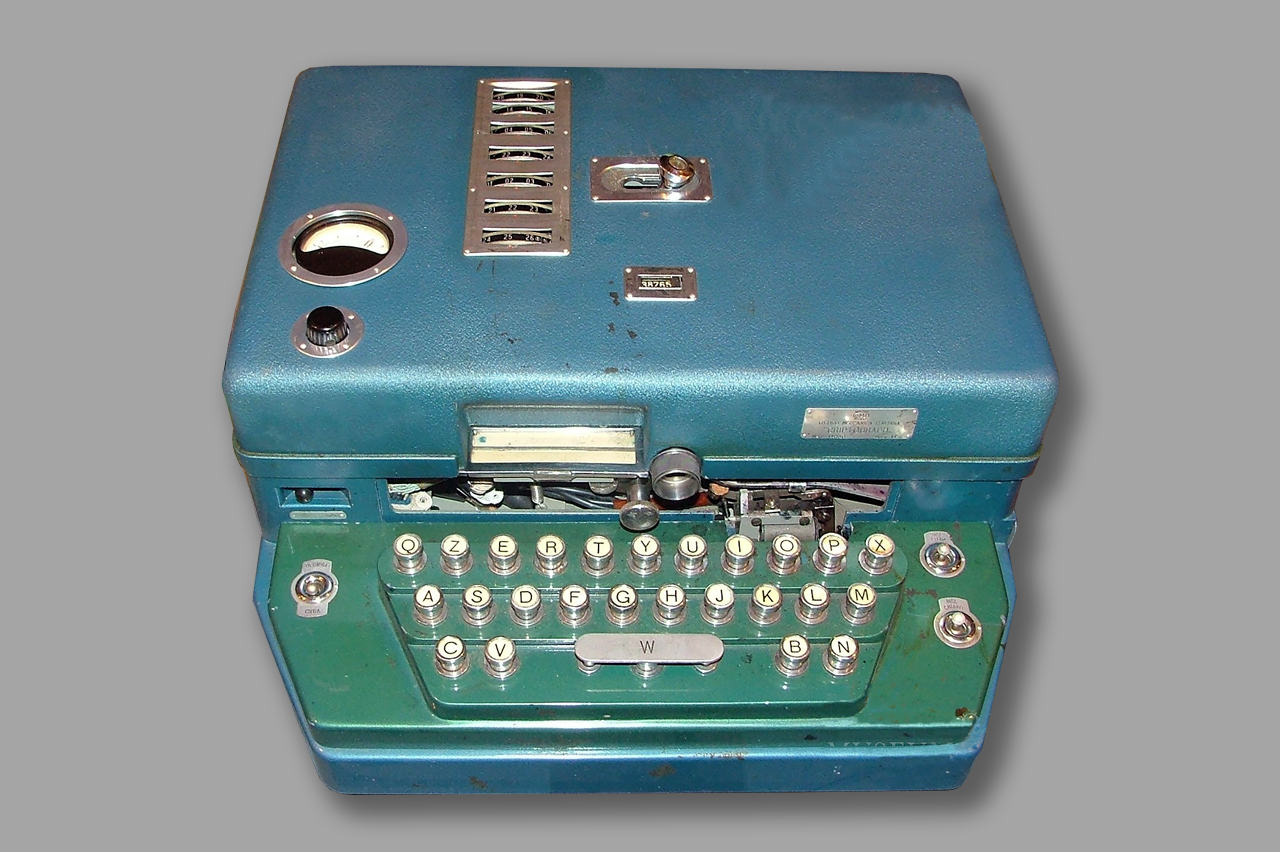
An original OMI Criptograph, manufactured around 1954, in a blue hamerite enclosure with a green hamerite keyboard.
In 1954, after OMI had recovered from the war, the successor to the OMI Alpha was developed: the Criptograph (note the ‘i’), again primarily intended for use by the Italian Armed Forces, but also offered to other users. It was larger than its predecessor and contained an improved 7-wheel drum, consisting of 5 cipher wheels with 2 wiring cores each, a settable cipher wheel and a settable reflector. Like the Cryptograph Alpha, this machine featured irregular wheel stepping.
Unlike the German Enigma however, the Criptograph is driven by an electromotor, and prints its output directly onto a paper strip, making it much faster in operation than the Enigma. The design is clearly based on the wartime OMI Alpha, which had a simpler construction but similar features. In the late 1950s, the Criptograph was succeeded by the somewhat improved Cryptograph-CR.
The diagram rougly shows the position of the various controls and features of the OMI Criptograph. At the front is the keyboard with the 26 letters of the Latin alphabet organised in the QZERTY order. Note however that the letter ‘W’ is used as the spacebar. Immediately behind the keyboard is the printer, printing directly onto a paper strip, that is fed in from a supply drawer at the right.
The cipher wheels are placed to the left of the centre of the machine, with the longitudinal axis of the drum running from front to rear. The cipher wheels are driven by a set of cogwheels that are part of the wheel coupling at the centre. The entire mechanism is driven by an electromotor at the rear right.
Cross-sections of the various cipher machines

The various controls and features of an OMI Cryptograph-CR.

The image above shows the complete drum with the entry disc on the right and the reflector on the left of the Criptograph, the Cryptograph-CR and the Cryptograph-CR Mark II. The advantage of this mechanism is not only that it features irregular wheel stepping, but also that it can be used to make corrections.

Controls of the Cryptograph-CR Mark II.
The OMI Cryptograph-CR
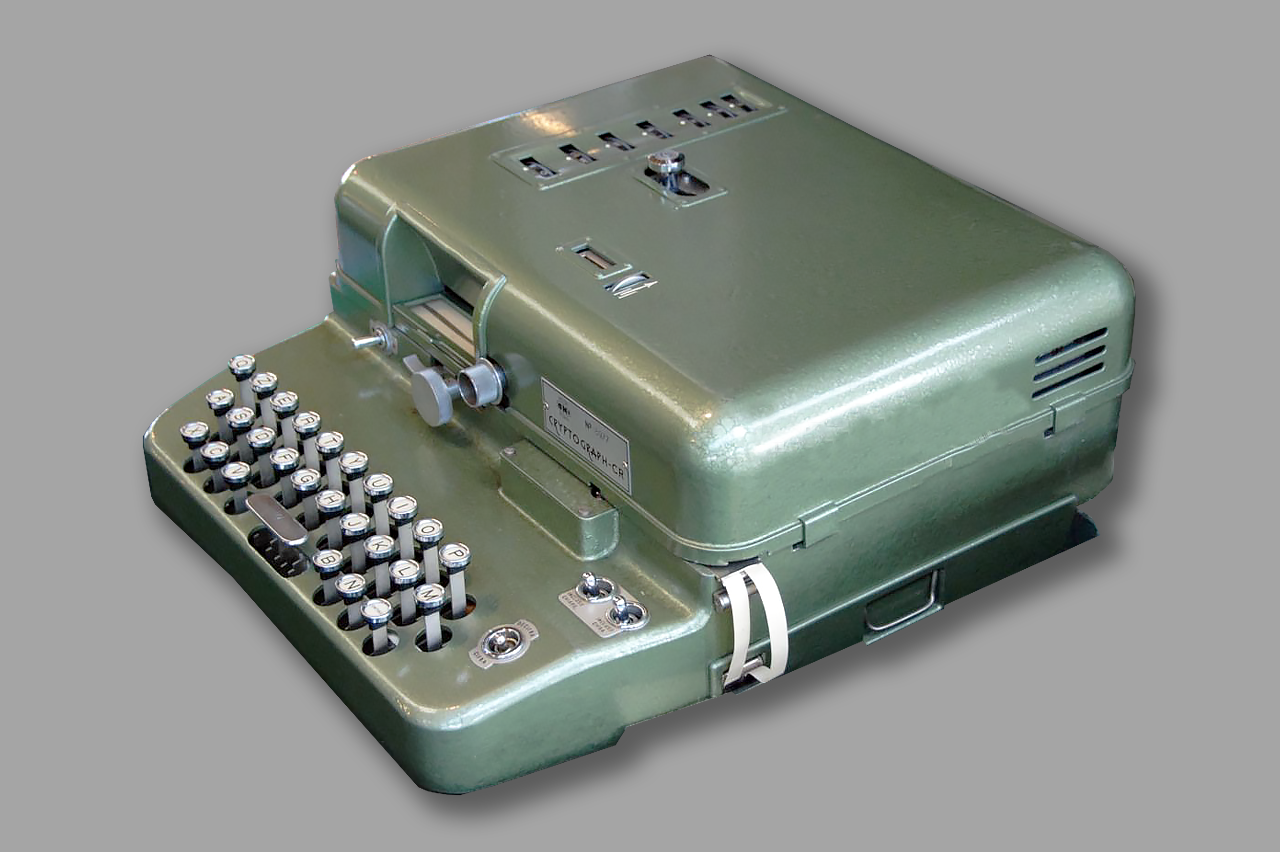
The image above shows a typical example of a Cryptograph-CR. The machine is painted in green hammerite.
The Criptograph evolved into the Cryptograph-CR, probably in the late 1950s. It was also intended for use by the Italian Armed forces (in particular the MMI 2) and probably some foreign users.
Its case was more rounded and was painted in green hammerite. Furthermore, it was given an improved power supply unit (PSU), a slightly different printing mechanism and a different keyboard. As a result, the motor had to be rotated by 90° (left to right rather than front to back). The wheels were identical.
At the front is a 27-button keyboard on which the letter ‘W’ is missing. This was done as the ‘W’ isn’t used in the Italian language. It is replaced by the space bar. The arrow-key at the bottom right is used for continuous paper transport. A resettable counter is visible through the top lid. It shows the number of entered characters.
The Cryptograph-CR is similar in operation to the German Enigma, in that it has a set of electromechanical cipher wheels with 26 contacts at either side, an entry disc (called Eintrittwalze or ETW on Enigma) and a reflector (Umkehrwalze or UKW).
Unlike Enigma however, the OMI Cryptograph-CR has a built-in printer that produces the output on two paper strips at the front of the machine, just behind the keyboard. One strip shows the plaintext; the other one the cipher text. The paper strip is supplied from the right side of the machine, passes the printer at the front centre, and leaves the machine on the left. The empty paper reels are stored in a drawer at the right side of the machine.
The diagram on the left shows the various controls and features of an OMI Cryptograph-CR of which the top lid has been removed. The cipher wheels are at the left, with its axle running from front to rear and the entry disc closest to the operator. The stator and the reflector are at the rear.
The cipher wheels are driven by a series of cogwheels that are located at the centre of the machine, just below the wheel coupling. An electric coupling (i.e. a solenoid) ensures that the entire mechanism makes one full revolution on each key-press. At the front of the machine is a double printer. The two print heads are identical and are mounted on the same axle. A double commutator ensures that each of the print hammers is released at exactly the right moment.
The OMI Cryptograph-CR Mark II

The grey hammerite Cryptograph-CR Mark II, or CR-2, produced in the early 1960s, is an upgraded version of the earlier OMI Cryptograph-CR.
As the Cryptograph-CR was a complex machine with high electric currents flowing through the contacts of the switches of the keyboard, the Cryptograph-CR had reliability problems. Some of the machines were therefore upgraded in which the mechanical keyboard parts were replaced by 26 electric relays. Furthermore, the spacebar was removed and the letter ‘W’ was added, resulting in a completely new keyboard.
After the upgrade, the machines were re-painted grey hammerite. This was typically the case for the Italian Navy machines. To avoid confusion, we will call the upgraded machine Cryptograph-CR Mark II. The unused holes of the keyboard are covered by a new panel that is mounted over it.
The two switches that enabled plaintext and cipher text printing were also dropped, and their holes were covered. As a result, the machine now always prints both plaintext and cipher text.
Inside the machine, parts of the Power Supply Unit (PSU) were modernised and each of the 26 electric relays is connected to one of the switches on the keyboard. In order to accommodate these relays, the paper supply drawer at the bottom right has been given up as well.
The diagram at the left shows the various controls and features of the OMI Cryptograph-CR Mark II. The upper section of the interior is largely identical to that of the original Cryptograph-CR, but the keyboard section is completely different. It now carries all 26 letters of the Latin alphabet (A-Z) plus a paper-advance key.
Furthermore, the keys are placed closer together, making it easier to operate. The print-enable switches at the right (plaintext and cipher text) have been removed. The motor compartment is at the rear right. Note that the motor is missing from the machine shown above.
The paper strip printer is placed just above/behind the keyboard. The cipher wheels are at the left, with a mechanical (cogwheel) coupling to their right. The cipher wheels can be released by unlocking two levers: one at either end of the axle.