Some of the following companies that manufacture(d) photographic material have already passed by in other parts of the site. Here you will find an overview of companies that marketed photographic material in the nineteenth and twentieth centuries. More is usually known about the best known or the most influential companies than about the lesser known ones; therefore they will be discussed more extensively than others.
The emphasis in this part of the site is more on the ups and downs of the company as such, while in other chapters the emphasis was on the product or on the man or woman who founded the company. The order of all companies is alphabetical.
Below are the names of the companies as will be discussed in this or any other chapter. By clicking on a name (so not on the bullet in front of it), you go directly to that part on this page where the manufacturer in question is located. Scrolling is also possible of course, but this service helps you to get to the desired manufacturer in question much faster.
Due to the fact that this introductory page has become much longer than originally planned and desirable due to the large number of manufacturers, we strongly advise you to use the name service below to go to the manufacturer of your choice on this or any subsequent page.
- General Introduction
- ADOX
- Agfa (see also Gevaert)
- Altissa
- Amaloco
- Ansco Camera Co (see also GAF)
- APM/APeM (see also Soho)
Amalgamated Photographic Manufacturers Ltd - Argus Camera Co, Ann Arbor Michigan
- Arsenal (see Kiev-Arsenal)
- Artima Export Ltd (see also Truvox)
- Asahi Pentax
- Bencini
- BOLCo and E Elliott Ltd
(abbrev. for The British Optical Lens Company) - Carl Braun Kamera-Werk
- Canon Inc.
- J.T. Chapman, Manchester
- The Chicago Cluster of Companies
(consisting of 56 companies ) - Chinon
- Concord Camera Corp.
- K.G. Corfield & K.G. Corfield (Sales) Ltd.
- Coronet Camera Company
- Cosina Company, Ltd.
- Dacora
- Dixons
- Durst
- EHO-Altissa company (See Altissa)
- E Elliott Ltd and BOLCo
(abbrev. forThe British Optical Lens Company) - Ellison Kamra
(see also QRS Devry Kamra Company) - ELOP
- Ensign Ltd.
(distribution Company of Houghton-Butcher) - Ernemann-Kamerawerke AG
- Expo Camera Company
- The FED Company
- Ferrania
- Fisher-Price
- Fodor
- Foitzik-Kamerawerke
- C.F. Foth
- Fototecnica
- Franka Kamerawerk –
- Fujica (Camera Division of Fujifilm)
- Fujifilm (brief history)
- Futura
- GAF (see also ANSCO)
(abbrev. for General Aniline & Film) - Louis Gandolfi
- Herbert George Company
- Gevaert Photo-Producten N.V. (see also AGFA)
- Girard et Cie
- GNOME
- GOERZ
- GOMZ (LOMO)
- Graflex (Folmer & Schwing)
- Great Wall Plastics Co
- W. Haking Enterprises Ltd.
- Hanimex
- Hasselblad
- Healthways
- Houghton–Butcher Manufacturing Co (See also Ensign Ltd. and Ross-Ensign Ltd.)
- R.F. Hunter Ltd.
- ICA AG
- Ihagee (Exakta)
- Ilford
- Imperial Camera Corporation
(see the Herbert George Company story ) - Jos-Pe
- Kamera-Werkstätten Guthe & Thorsch
- Keystone
- Kiev Arsenal
- KMZ
- Kochmann
- Kodak USA (incl. Australia, Canada, France, Germany & the UK)
- Konica-Minolta (Konishiroku)
(see also Minolta) - Kowa
- Krügener
- Kürbi & Niggeloh (Bilora)
- Kyocera (Yashica, Contax)
- Lancaster
- Leitz
- Lensless Camera Manufacturing Company
- Linhof
- Lipca (see also Richter-Tharandt)
- LOMO (see GOMZ)
- Loreo
- Mamiya
- Meopta Optotechnica
- Mimosa AG
- Minolta (see also Konica-Minolta)
- Minox Company
- Miranda (Orion)
- MMZ-BeLomo
- Motodori (Condor)
- Dr. August Nagel Kamera Werke
- Neidig Kamerawerk
- Nemrod-Metzeler (See Healthways)
- Nettel
- Nikon Company
- Nimslo Corporation (see also Nishika)
- Nishika Optical Systems (see also Nimslo)
- Noblex (See also K-W Guthe & Thorsch)
- Olympus Company
- ORION (see Miranda)
- ORWO
- Ottico Meccanica Italiana (OMI)
- Paterson Products Ltd.
- VEB Pentacon Dresden
- Pentax (See Asahi Pentax)
- Petri
- Photavit (Bolta)
- Plaubel
- Polaroid
- Photo Porst
- Karl Pouva – VEB Fototechnik Freital (see also Woldemar Beier)
- Purma Cameras Ltd.
- QRS Devry Kamra Company (see also Ellison Kamra)
- Foto-Quelle
- Rectaflex
- VEB Rheinmetall Büromaschinenwerk
- Richter-Tharandt (see also Lipca)
- Ricoh
- Rollei Germany
- Rollei Singapore
- Ross-Ensign
(continuation from Ensign Ltd.) - Ro-To Company
- Sea&Sea-Sunpak
- Shanghai Seagull
- Sida-Fotofex
- Sigma
- Soho Ltd (see also APM)
- Standard Cameras
- Steinheil
- Stenopeika
- Thornton-Pickard
- Topcon (Tōkyō Kōgaku)
- Tougodo Company
- Traid Corporation
- TRUVOX (see also Artima Export)
- Tura AG
- Universal Camera Corp.
- Vivitar
- Voigtländer
- Vredeborch
- Welta
- Werra (C. Zeiss Jena)
- Wirgin
- Kamera-Fabrik Woldemar Beier (see also Karl Pouva)
- Hermann Wolf GmbH
- Wünsche
- Yashica (see also Kyocera)
- Zeiss Ikon AG
- Zion
- Zunow (Teikoku Kōgaku)
FOUNDER: Carl Schleussner
1860: Dr. Carl Schleussner Fotochemie Aktien-Gesellschaft für Anilin-Fabrikation; 1897: Trockenplattenfabrik auf Aktien vorm. dr C. Schleußner AG; 1923: Aktiengesellschaft Doktor C. Schleussner; 1938: ADOX Fotowerke Dr. C. Schleussner GmbH; 1962: The Schleussner family sold its photographic holdings to DuPont, USA for its subsidiary company Sterling Diagnostic Imaging for X-Ray Films; 1962: Dupont licensed the film technology to a Yugoslavian manufacturer known as Fotokemika; 1992: the license expired and fotokemika sells the films now under the name Efke; 1992: Fotoimpex, a Berlin distributor, registered the ADOX brand name; 1999: Agfa buys Sterling; 2023: the name ADOX lives on in the Fotoimpex plant in Bad Saarow, Germany.
1860: Frankfurt am Main; 1927: Neu-Isenburg; 1938: Wiesbaden.
ADOX was created by Dr. C. Schleussner and founded in 1860. May 7, 1860 to be precise, being world’s first photochemical factory. Before 1860 and the move into film making, Dr. C. Schleußner produced sealing waxes from the Römerberg in Frankfurt am Main.
Since 1880, Schleussner made silver bromide gelatin dry plates. They were much easier to handle than the wet gelatine emulsion plates that were prevalent at the time. In 1884 the first and oldest dry plate casting machine was put into operation. Due to the location in Frankfurt, collaboration with Wilhelm Conrad Roentgen resulted. Schleussner-Fotowerke became the first developer of X-ray films and plates for medicine and became the market leader.
In 1892, Carl handed over the management of the company to his two sons, Carl Friedrich (1864–1928) and Dr. Carl Moritz (1868–1943), who, as a chemist, decisively determined the further development of the company.
A few years later, in 1902, the first orthochromatic plate called “Viridin” was developed and marketed. In 1903 the first roll film with celluloid as the carrier material and in 1926 the first X-ray plates and X-ray paper came onto the market.
Some films, such as KB-14 and KB-17 (first single thin layer films, R-17 was KB-17 sold in rolls) were amongst the first developed, and they are still under production: their current names are ADOX CHS 25 and CHS 50. The roll films Tempo-Rot, Tempo -Gold and Olympan were manufactured and sold up to the Second World War.
ADOX was always a family-run business: founder Dr. C. A. Schleussner was granted with an Honoris Causa by Frankfurt’s Goethe University for his contributions to radiology. Two of his sons were part of the management, one as Head of the Board of Directors, and another as responsible for the technical area. Founder’s wife, Irene Schleussner, took as her duty the social aspect of the company, enabling access to a physician for employees, or creating a Foundation aimed to guarantee retirements and health care.
In the third generation under Carl Adolf Schleussner, new production facilities for the manufacture of photographic materials were set up in Neu-Isenburg. Thus, in 1927 the company moved from Frankfurt to Neu-Isenburg.
After that, three years later, the production of photographic paper in silver bromide and contact paper was started and implemented. The roll films R 14, R 17 and R 21 were legendary being the world´s first thin layer films. These made ADOX famous inside and outside of Germany. In the USA the KB 14 and the KB 17 were called “the German wonder film”. The X-ray film production segment remained strong to the end in 1962.
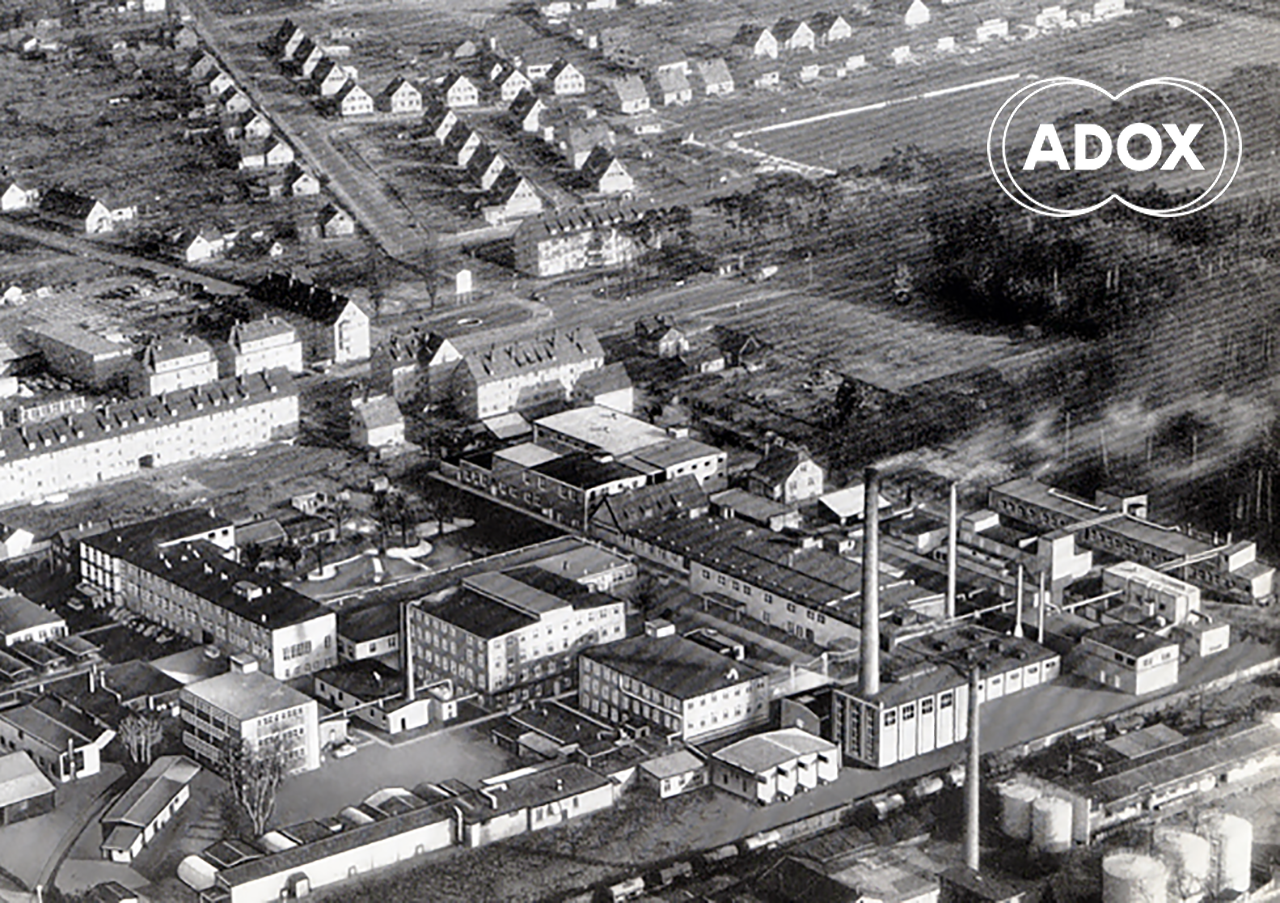
ADOX Fotowerke Frankfurt
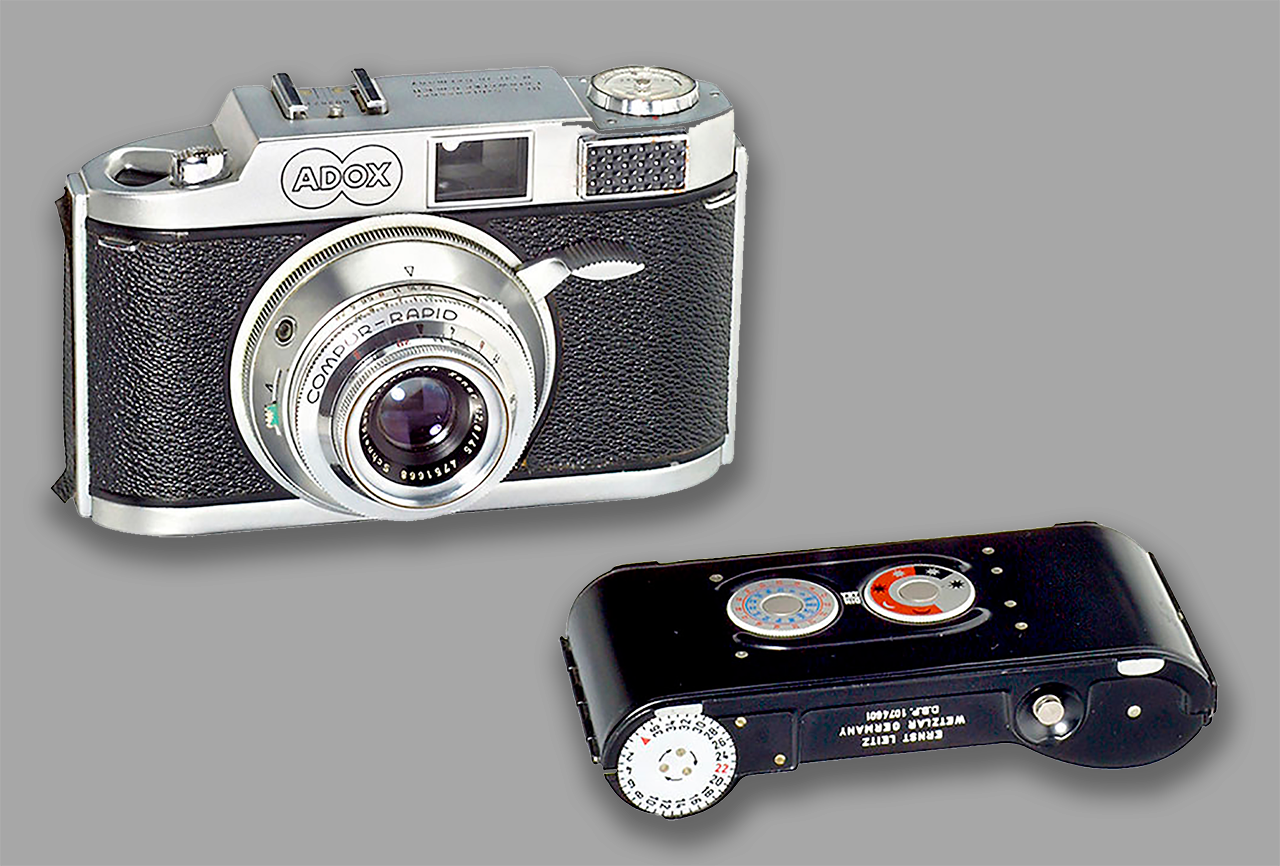
The ADOX 300, World’s first camera with interchangeable cassettes for film.
During and after World War II
When the company had nearly 500 employees, factory was completely destroyed in the night of December 22, 1943. Whatever was left with some value was rescued from beneath the ruins, and moved to Dresden. Bad luck once more: by the end of 1944 and when everything was again almost ready for resuming production, the city was bombed. Again, the few machines and parts that survived were rescued and moved again, this time to the Thuringia, a region situated in the centre part of Germany.
Resources were few, raw materials not enough, but against all odds they managed to resume production, initially with X-Ray film, one of the priorities of that after-war time. Meanwhile in 1945, around 80 people – mostly old employees – rebuilt the previous facilities at Neu-Isenburg.
Meetings between Hesse, East Germany and Russian authorities allowed for three Russian technicians to travel to Neu-Isenburg, managing to build some machines even with the few resources available. Again a drawback, when on January 9, 1947, one of the machines took fire, fortunately controlled without too much trouble. By then, the company employed 2000 people, 300% more than 10 years before.
In 1938 Adox took over the camera factory of Wirgin when the Wirgin brothers had to leave Germany to escape from persecution by the Nazi regime of that time. After WWII Henry Wirgin bought it back. As a result, the headquarters of Adox Camerawerk GmbH was relocated to Wiesbaden. Names like ADOX 300, Golf, Polo, Polomat are cameras of that time from Adox.
The ADOX Golf (a medium format folding camera) and ADOX Polo (a 35mm camera) were two of the references for the brand. The former received glass from Will Wetzlar rebadged as “Adoxar”, whilst the latter had Schneider-Kreuznach lenses. World’s first camera with interchangeable cassettes for film was created by ADOX, their model 300.
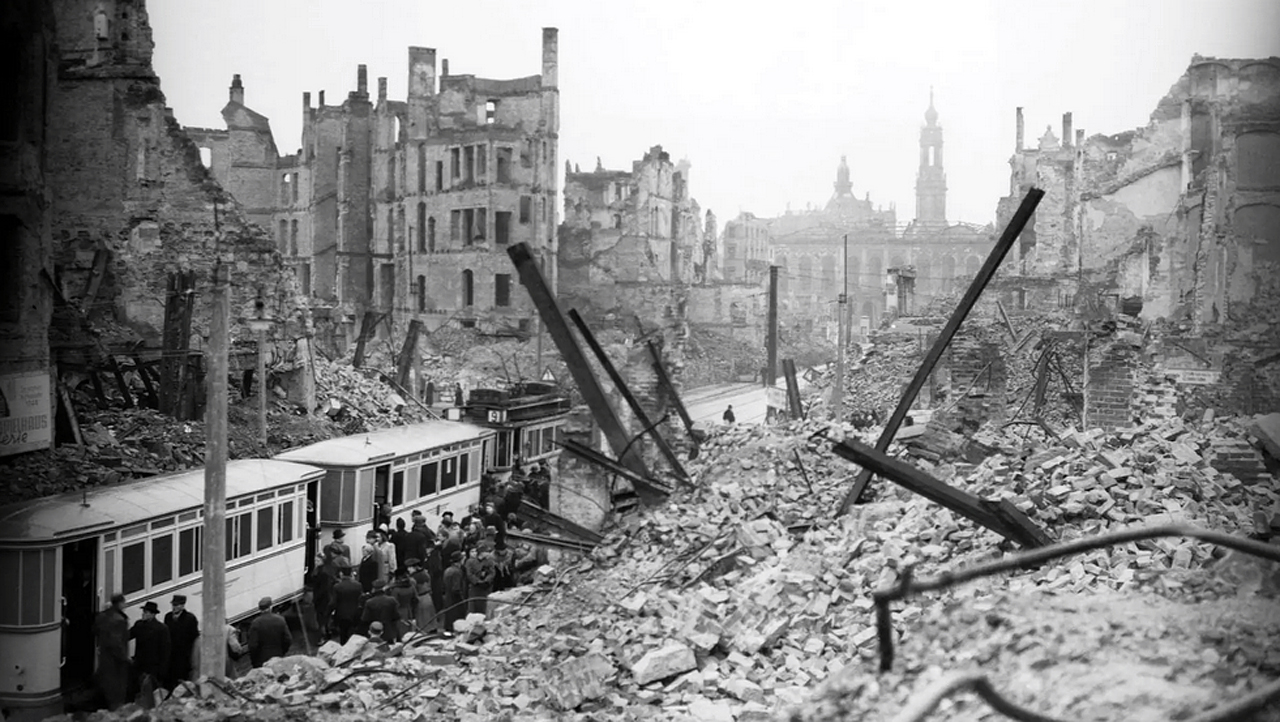
The ruins of Dresden after an heavy bombardment
ADOX was one of the targets of the Marshall Plan, and thanks to it the company was able to build new facilities and upgrade the ones at Neu-Isenburg. The factory at Köln, in charge of manufacturing plate cameras, was also rebuilt.
After the Second World War, cameras were also produced in Wiesbaden in addition to films, such as the Golf 6×6 medium format camera or the Polo 35mm camera. The ADOX 300 was the world’s first 35mm camera with a interchangeable film magazine. Polomat cameras had a coupled exposure meter and the Polomatic even had a fully automated exposure system.
Slide projectors were also made, e.g. the ADOX 300-M. Like the camera lenses, the projection lenses were sourced from other companies. Important suppliers were the companies Will from Wetzlar and Schneider Kreuznach (a Radionar lens 1:2.8/45 mm for the Polo). The lenses for the Golf came from Will Wetzlar and were called “ADOXAR”.
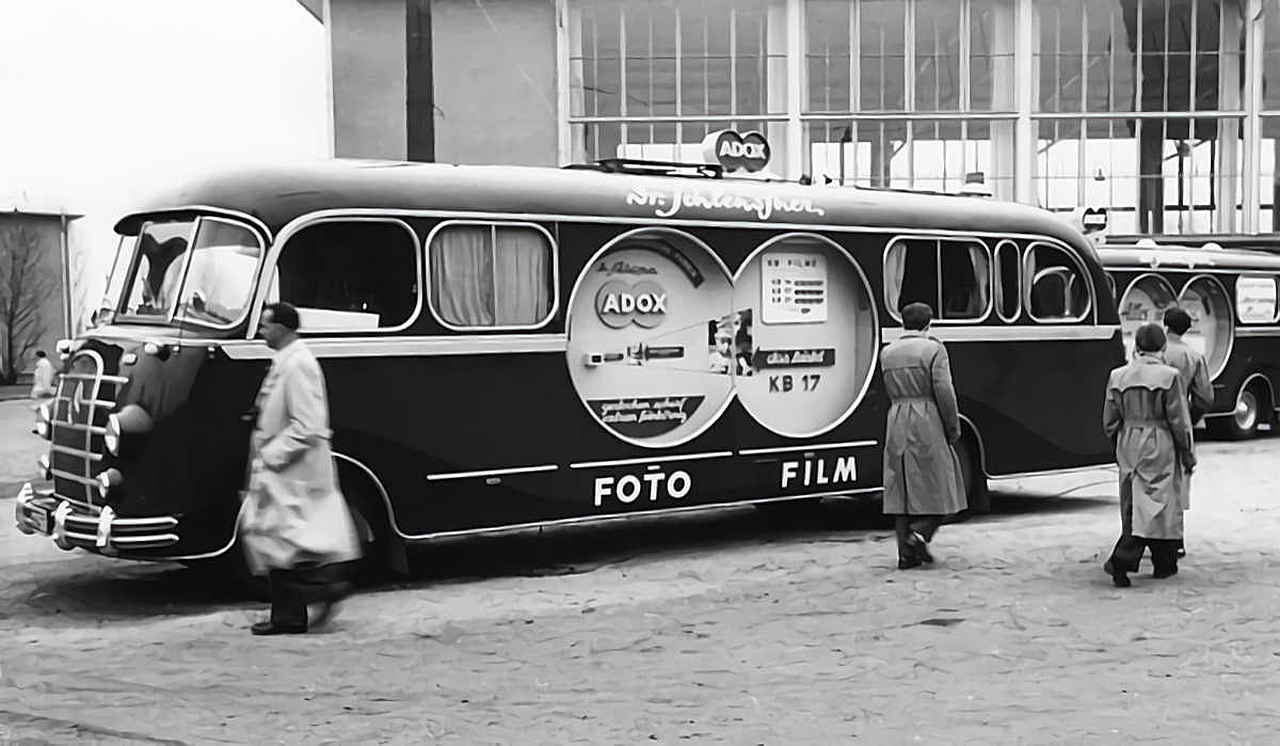
The two Adox advertising buses caused a stir in the outdoor area of Photokina 1954. In the black and white sector, the West German company of Dr. Schleussner, with its Adox brand, competed with Agfa. The film factory was in Neu-Isenburg, the camera factory in Wiesbaden. The fine-grain thin film Adox KB 17 and KB 21 became famous.
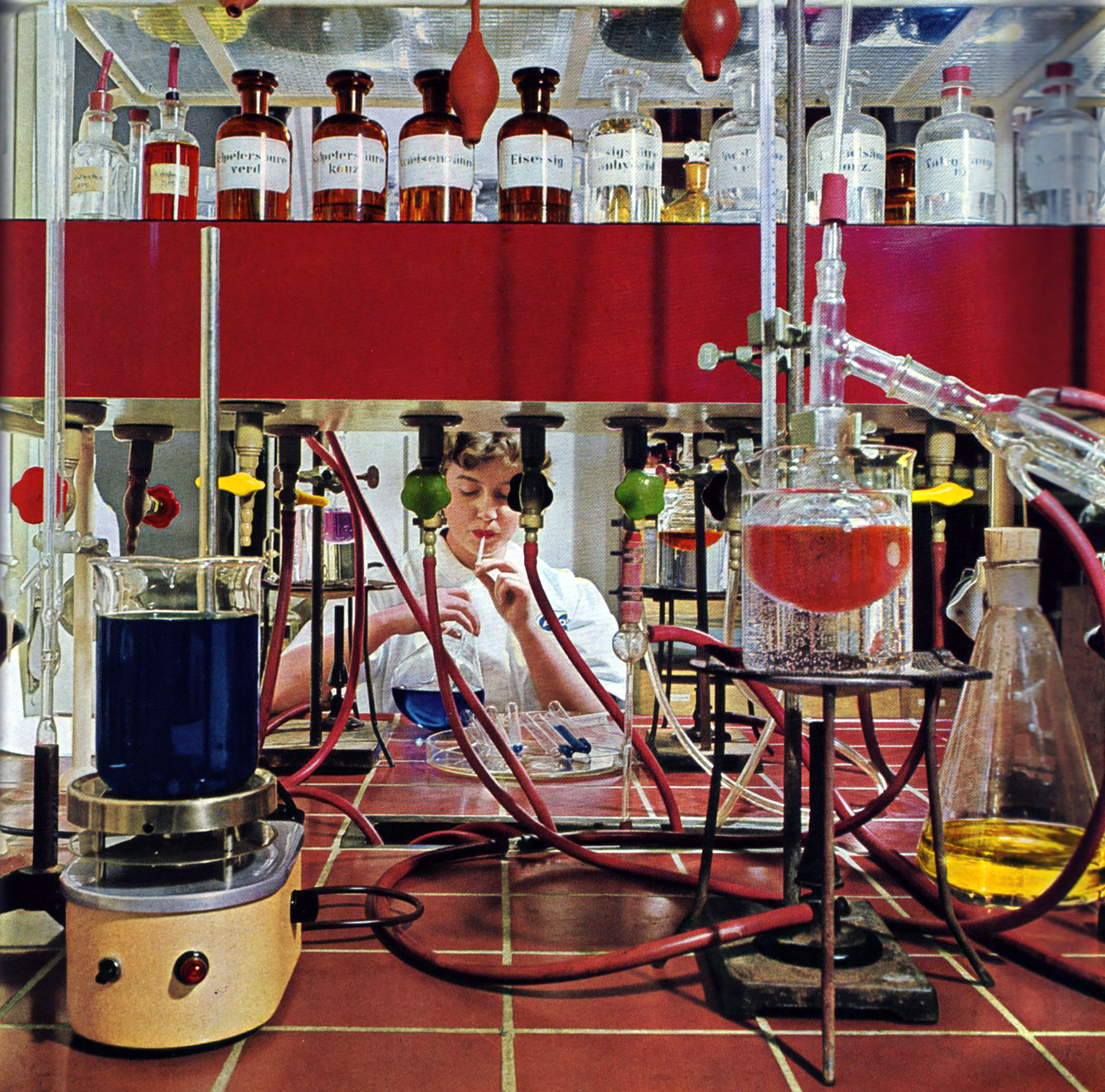
Another German wonder film
In 1956, the efforts of around 40 engineers resulted in ADOX presenting their first colour film (based upon the chromogenic development, as published by R. Fischer in 1911), and two years later the C-15, their first slide film. What was called to be the last evolution of this family sold by ADOX, the C-18, had 7 layers, 3 of them for colour management, which provides a moderately well balanced response. Processing was made at ADOX laboratories, the “ADOX Umkehranstalt”. NC-17, negative colour film, could be developed at home using the E-NC kit sold by ADOX.
ADOX held many patents for colour photographic technology. This made ADOX for years independent of the competition. The ADOX colour coupling system was based on the chromogenic development first introduced by R. Fischer in 1911. The key problem was to find colour dyes which did not mix during processing. Thousands of tests needed to be made in order to find the right dyes.
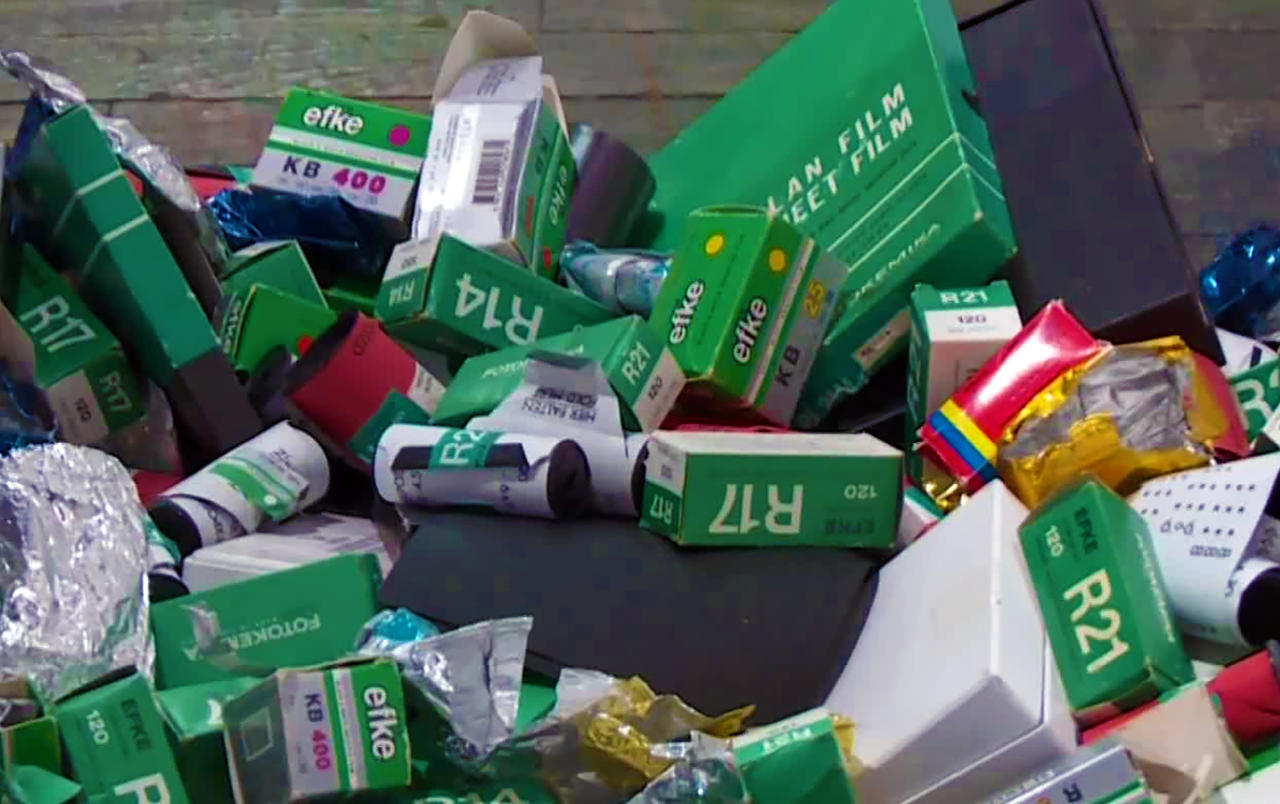
New companies for the Adox brand
Fotoimpex from Berlin, a company founded in 1992 to import photographic films and papers from the former Eastern Europe, registered the brand immediately and today ADOX is a black and white brand of films, photographic papers and photo chemicals from ADOX Fotowerke GmbH based in Bad Sarrow near Berlin.
A firm in Calgary, Alberta, also registered the name Adox for their film company in Canada, but uses the brand name Bluefire for their products. They have allowed Fotoimpex to use the Adox brand in Canada.
Although Dr. Schleussner’s original company no longer exists, the name ADOX lives on in its Fotowerke plant in Bad Saarow, Germany.
The Schleussner family sold its photographic operations and ADOX trademark to DuPont USA in 1962, and since 1965 no cameras have been produced. DuPont used the trademark for its subsidiary Sterling Diagnostic Imaging for X-ray film.
In 1999 Sterling was bought by the German company Agfa. Agfa did not use the trademark and lapsed its registration in 2003. With the closure of Agfa´s consumer imaging branch in Leverkusen in 2005, ADOX became engaged in manufacturing again trying to save as much knowledge as possible and transfer it to a smaller level of production.
In 1972, many of the machines as well as licensing rights for manufacturing the original ADOX film emulsions were granted by purchase to a (by then) Yugoslavian company, Fotokemia EFKE in Zagreb.
Agreement ended in the 90s, as did the license for using the ADOX brand. But film using those old formulations is still manufactured, under the EFKE brand. The films and papers are sold both in the Efke packaging of their Croatian manufacturer and as a trademark of their Berlin distributor and owner of the rights to the Adox brand, Mirko Böddecker, in Adox packaging. The old company logo has been modernized somewhat.
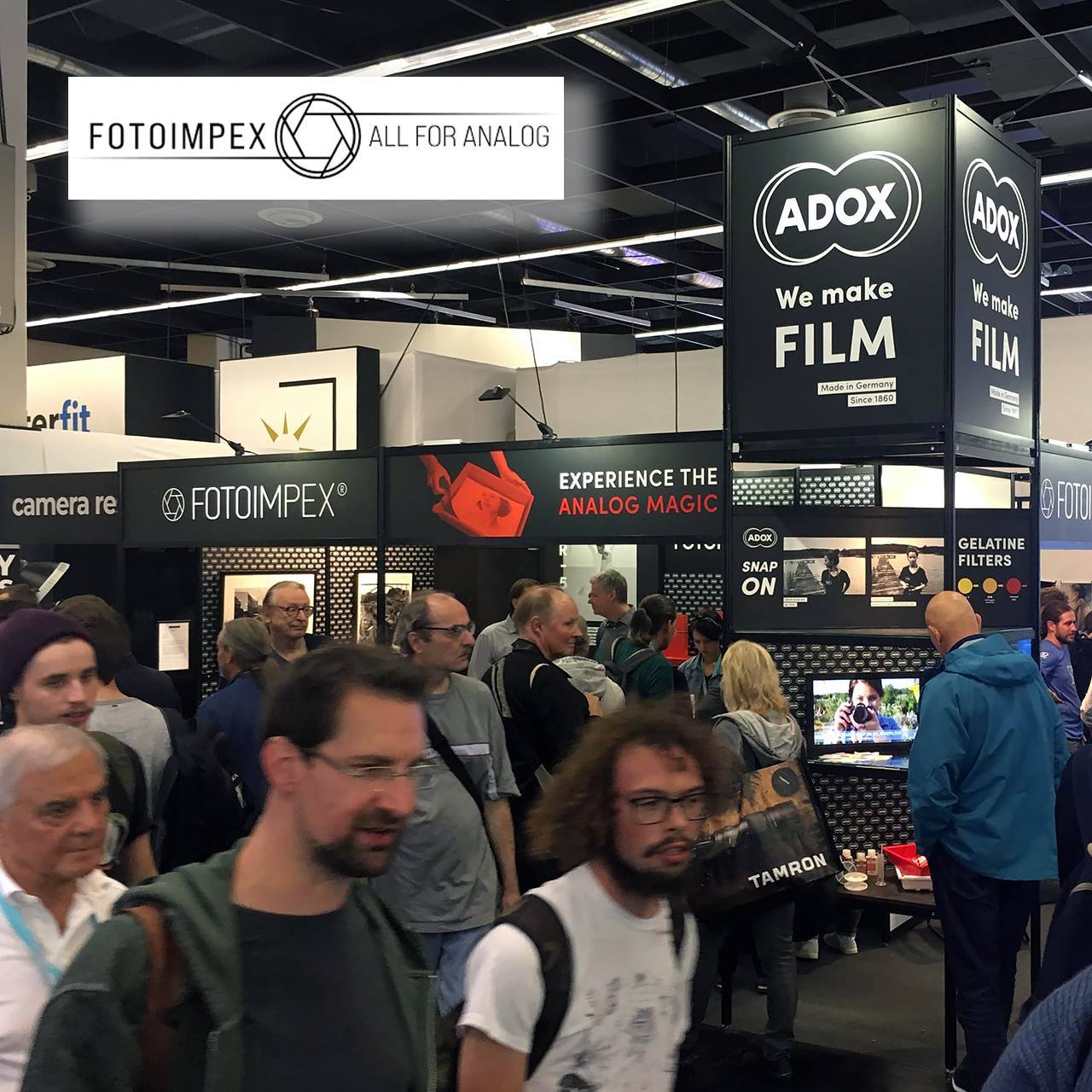
Fotoimpex was present on the Photokina, 2018-5-1 with their analog ADOX program.
Adox brand cameras
- Adrette, name variant of the Wirgin Edinex
- Adox 300
- Adox 500, prototypes
- Golf I (1964)
- Golf IA
- Golf IIA
- Golf IIIA
- ADOX Polo
- Polo 1S
- Polomat
- Polomatic
6 x 6 Folding Cameras
- Golf I
- Golf II
- Golf IV
- Mess-Golf I
- Mess-Golf II
- Mess-Golf IV
- Golf 63 (1954–59)
- Golf 63 S
- Golf 45 S
6 x 6 Box Cameras
- ADOX 66
- Adox Blitz
6 x 9 Cameras
- Adox Sport (6×9 + 6×4.5)
- Adox Start (1950)
- Adoxette 3×4, name variant of the Wirgin Gewirette
- Juka 3×4 on Juka film
The Sport 1A camera was manufactured in circa 1950. It was similar to the Sport 1 but with a Pronto shutter and the “A” series of cameras featured a moulded top plate incorporating the view finder. A vertically folding 6 x 9 cm roll film camera constructed of metal. It was fitted with a Schneider-Kreuznach Radionar f4.5 lens.
The Adoxette camera was manufactured in circa 1939. A medium format camera capable of taking sixteen 3 x 4mm exposures on number 127 roll film. It was fitted with an Adox Adoxar f3.5 lens or Triopan f3.5 among others that was collapsible and a vario shutter providing speeds of 1/25th, 1/50th to 1/100th per second plus bulb and time.
The ADOX 66 camera was manufactured in circa 1950. Constructed of Bakelite with the view finder located on the top to give the appearance of a TLR. It was made by Hermann Wolf GmbH, Wuppertal, Germany, who originally called it Luxa 66. The camera was fitted with a fixed focus meniscus f8 lens and an instantaneous and time shutter.
The Polo 1 and 1S cameras were manufactured from circa 1959 to 1964. Three versions existed: the Polo 1, 1S and 1B. The Polo 1 and 1S shared the same body so they look similar but with different lenses/shutter combinations. Namely: the Polo 1 : a 45mm f3.5 Adoxar or Isconar 45mm f/2.8 lens and the Polo 1S : a 45mm f2.8 Adoxar or Schneider-Kreuznach Radionar L lens.
FOUNDERS: Paul Mendelssohn Bartholdy and Carl Alexander von Martius
COMPANY NAMES:
1867: Gesellschaft für Anilinfabrikation mbH; 1873: Actien-Gesellschaft für Anilin-Fabrikation; 1897: the trade mark AGFA is registered;1925: Merged into Interessen-Gemeinschaft Farbenindustrie AG (IG Farben); 1928: Ansco Photo Products Inc. merged with Agfa in the United States and the name changed to Agfa Ansco Corporation; 1945: Three sites existed: Agfa Camerawerk Munich – Agfa Photopapierfabrik Leverkusen – Agfa Filmfabrik Wolfen; 1957: Agfa AG Leverkusen; 1964: Merger with Gevaert becoming Agfa-Gevaert Group existing of Agfa-Gevaert AG, Leverkusen and Gevaert-Agfa N.V. in Mortsel.; 1964: VEB Filmfabrik Agfa Wolfen as well as VEB Film- und Chemiefaserwerk Agfa Wolfen; 1981: Bayer obtained 100% ownership of the Agfa-Gevaert Group; 1999: Agfa shares were introduced to the stock markets of Brussels and Frankfurt; 2004: Agfa divested all its photographic activities to the new, independent company AgfaPhoto.
COMPANY ADDRESSES:
1867: Rummelsburg near Berlin; 1872: Lohmühlenstraße, Berlin-Treptow; 1896: Greppin; 1910: Wolfen; 1926: Schillerstraße 28, Munich and Leverkusen; 1927: Tegernseer Landstraße, Munich.
Agfa is originally a company in the chemical industry. The company became known to the general public through its photographic products. For decades, Agfa was one of the largest European manufacturers of photographic film and laboratory equipment, behind its world-leading competitors Kodak and Fujifilm. Cameras and slide projectors were also made for the mass market. The companies of today’s Agfa-Gevaert Group focus on product areas beyond chemical photography (graphics, materials, health care).
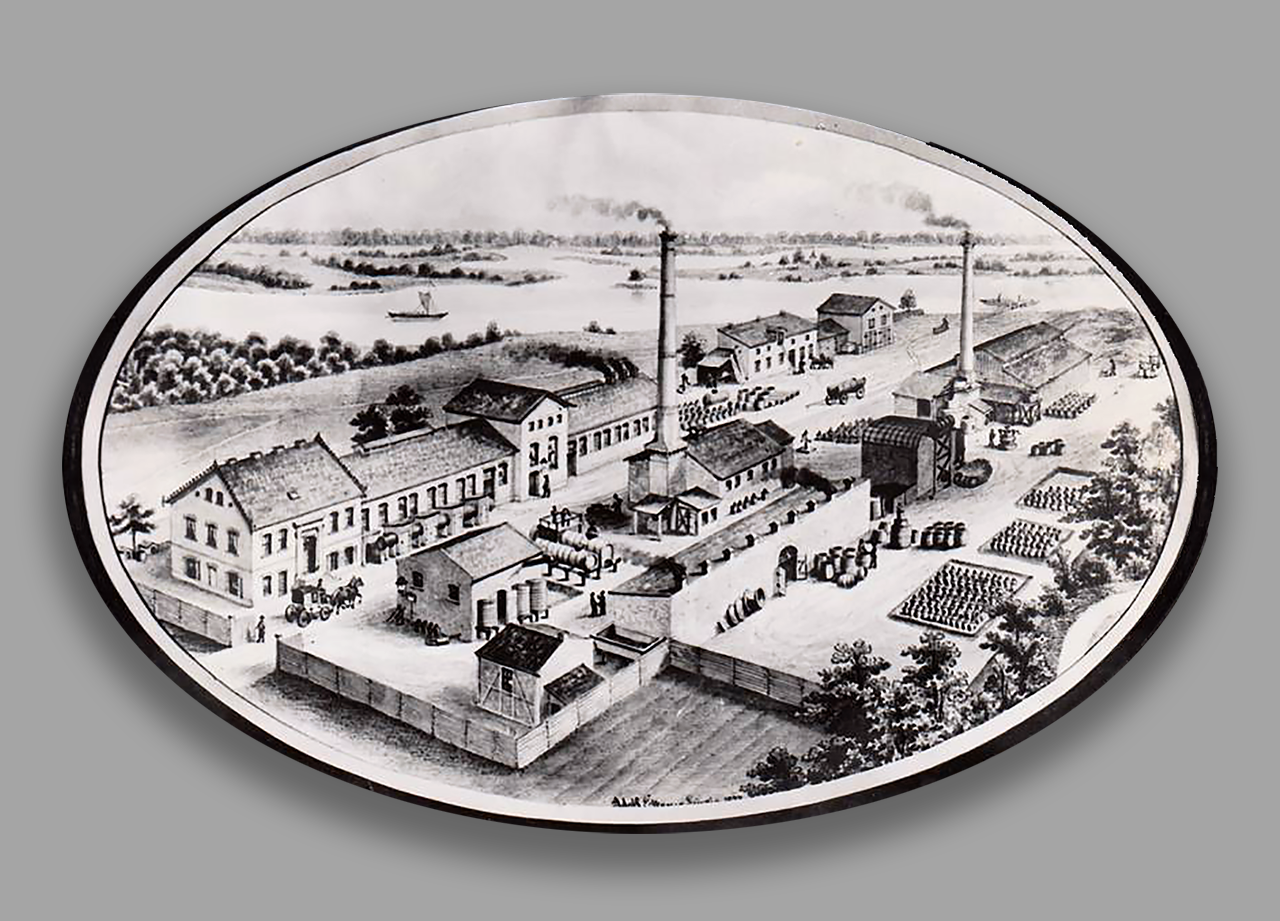
The chemical factory of Carl Alexander von Martius and Paul Mendelssohn-Bartholdy in Berlin-Rummelsburg.
The chemists Paul Mendelssohn Bartholdy (discoverer of the azo dye Bismarck brown, which is still used today in textile dyeing) and Carl Alexander von Martius founded the Gesellschaft für Anilinfabrikation mbH in Rummelsburg near Berlin in 1867.
As early as 1872, the chemical factory was bought from Dr. Jordan in Berlin-Treptow, since both companies were active in the same area. The Jordanian factory had existed since December 11, 1850, and primarily produced end products, especially dyes, while the Gesellschaft für Anilinfabrikation concentrated on intermediate products. The two companies complemented each other perfectly.
The merger resulted in the Actien-Gesellschaft für Aniline-Fabrikation on July 21, 1873. The designation AGFA followed later, it was registered on April 15, 1897 as a trademark for “chemical preparations for photographic purposes”. In 1924 the famous Agfa rhombus was added as a logo.
Three dates are available for the beginning of the company: 1850, 1867 and 1873, but the founding of the stock corporation in 1873 is usually regarded as the beginning.
The successful chemical production led to an expansion of the production facilities in Treptow in 1878. In 1882 a scientific laboratory was set up. Because the neighboring properties were all built on, a branch plant followed in Greppin, which was located in the Bitterfeld lignite mining area and thus offered a cheap energy supply. Labor costs in the countryside were also 20% lower. The Greppin-plant opened on March 17, 1896.
Because the air pollution in Berlin, especially the load from the steam locomotives of the nearby railway line, made it difficult to produce film materials there, a separate film factory was built. The Frankfurt/Mannheim area was also under discussion, but the company eventually bought 25.2 hectares of land near the Wolfen paint factory. Since most of it was in the municipality of Wolfen, the factory was finally called Filmfabrik Wolfen.
The plans for the plant were drawn up in March 1909, and on July 19, 1910 the building acceptance and permission to operate a chemical factory followed. It was the largest film factory in Europe and the second largest in the world – after Eastman Kodak in Rochester, USA. In 1908 Agfa launched a less flammable security cine film.
rodinal
The dye chemist Momme Andresen initiated the entry into photochemistry. He joined the company in January 1887 and suggested to the company management to work in the promising field of photography. Andersen was already an amateur photographer, so he was familiar with the shortcomings of the wet collodion process. He then created new developer substances and fixing baths at AGFA, above all the film developer Rodinal in 1888, which brought great progress in the darkroom.
It was a concentrate that only needed to be diluted, whereas previously you had to mix the developer yourself from different powders. Rodinal could also be used more diluted for paper development, it remained in the Agfa program until the end of photochemical production and is still manufactured today. At the beginning, F. Krüger, a former chemist at the Actien-Gesellschaft für Anilin-Fabrikation, took over the distribution of Agfa photo products in Frankfurt; In 1889 the company went over to selling it under its own management.
In 1892, Andresen suggested producing dry plates that are precisely tailored to Agfa’s developer substances and was then commissioned to do so by the management. Jo Sachs & Co (Berlin) was the first company to produce dry plates in 1879; their production required extensive development work and the necessary watering systems had to be procured from abroad.
Agfa did not get the first plates until May 1894, but there were always problems with dirt, detachments and inconsistent photosensitivity. It was not until 1898 that the dry plates turned a profit. Agfa X-ray plates also came onto the market that year, they were so advanced that they managed with a quarter of the usual exposure time.
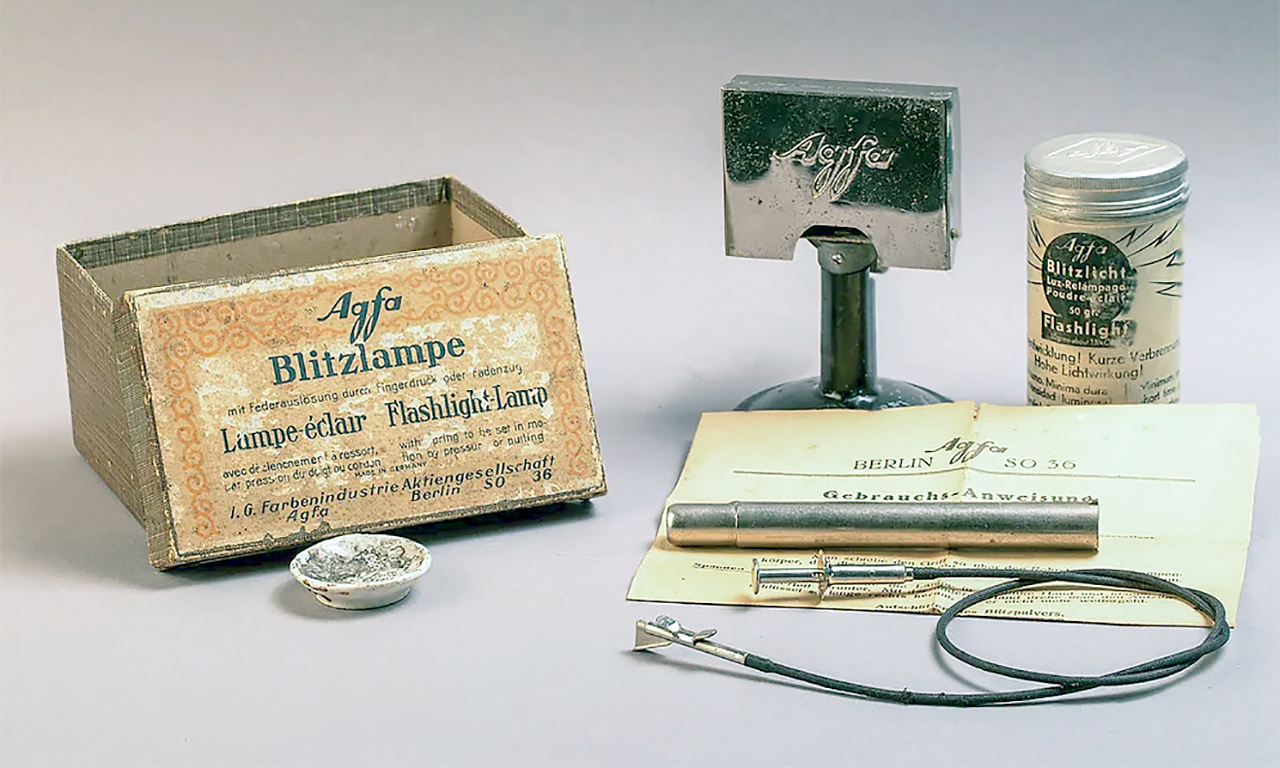
Vintage Agfa Flashlight-set
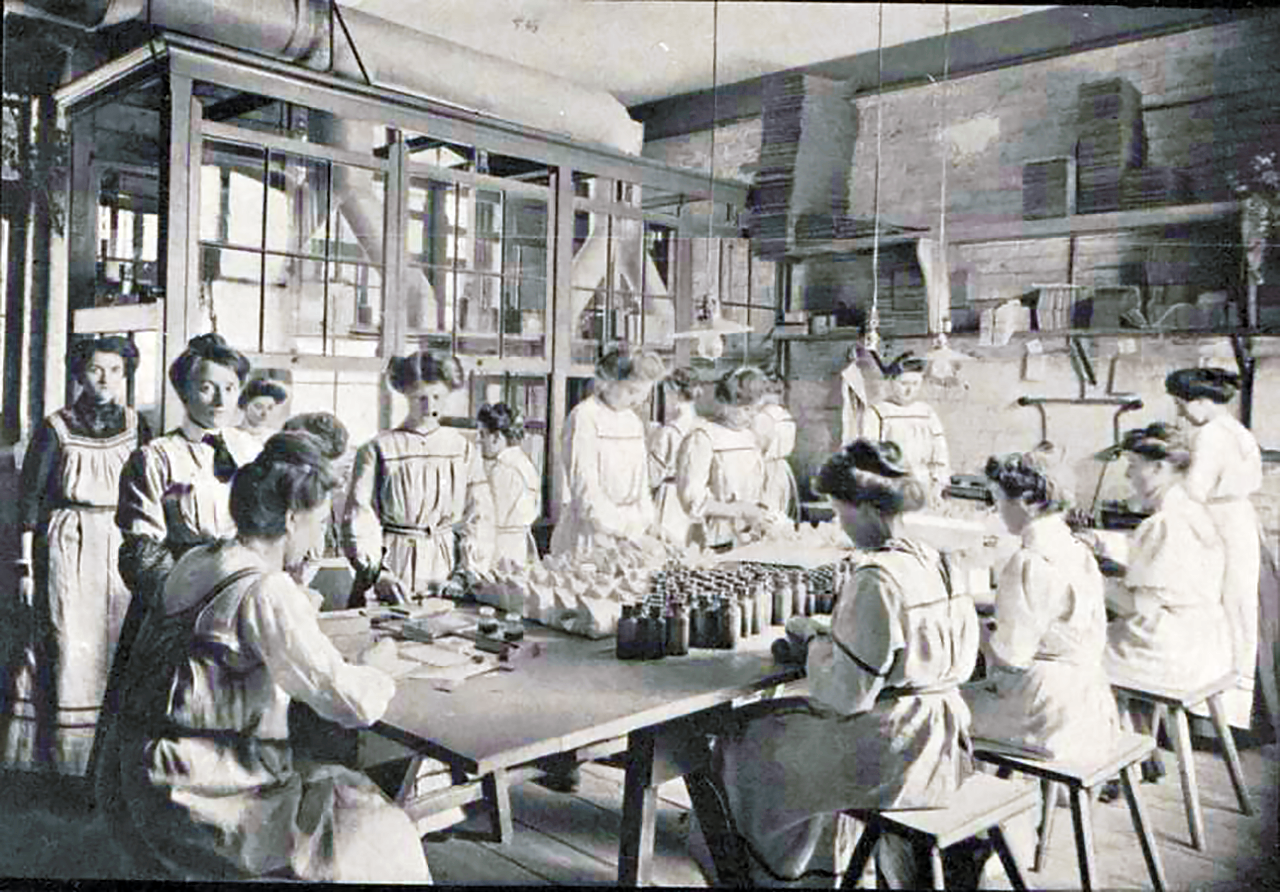
Bottling of the Rodinal solution, 800 bottles per woman.
roll film
The photographic plates were followed by sheet films, the future of which was recognized immediately at Agfa, since the only advantages of glass plates lay in their absolute flatness. On the other hand, they were very heavy, required a large amount of space for archiving, and were fragile.
The next step, to roll the films, then caused the greatest difficulties. Kodak was making roll film as early as 1888 and by 1896 had greatly improved it so that it could be supplied on daylight reels. This left them unrivaled on the market for over a decade. Behind the Kodak film was Hannibal Goodwin, who won a patent dispute with Kodak.
At Agfa, taking the patents into account, they also wanted to create a roll film, but repeatedly had to accept setbacks. Although such films were offered in 1900, there was always reduced light sensitivity and black spots, which was only noticed in the hands of customers and finally led to a temporary suspension of production in 1905.
movie film
Agfa was more successful with cinematographic films. As early as 1901, it was able to produce competitive products with a self-constructed and patented machine, which were then commercially available in 1903. A major problem with the cinema films of those days was their flammability. Agfa worked on this problem, presented the first safety film in 1908 and set up a production facility for it a year later in Berlin-Lichtenberg.
Photo accessories
Agfa also produced accessories very early on, starting in 1904 with self-filling flash bags, followed by flash lamps (Agfa flash lamp I from 1907), exposure tables and sheet film cassettes.
First World War
With the outbreak of the First World War, numerous export markets disappeared and the demand for X-ray plates and film for aerial photography, the so-called “aviator film”, increased. The field cinemas also demanded film material, and panes and filters for gas masks were also produced. The number of employees at Agfa Wolfen initially fell from 504 to 335, but then rose to well over 1,000 during the war.
Grain screening method
In 1909 Agfa started working on color photography, especially in view of its big competitor Kodak, who did not want to be left to this area alone. In 1916, for example, the first plates for color slides based on the grain screen process came out. However, these plates not only had a very coarse resolution, they also had to be exposed for about 80 times longer than the black and white materials of the time.
In 1923 new plates with improved color reproduction and increased sensitivity appeared, after which 30 times the exposure time was sufficient – in sunny summer weather you could work with 1/25 s at f/4.5. In 1932, when production was relocated to Wolfen, the name Agfacolor was introduced. Now there were not only plates, but also films based on the grain screening process. The 16 mm color narrow film based on the line screen process was also called Agfacolor. In 1936 the highly sensitive plate Agfacolor Ultra was released.
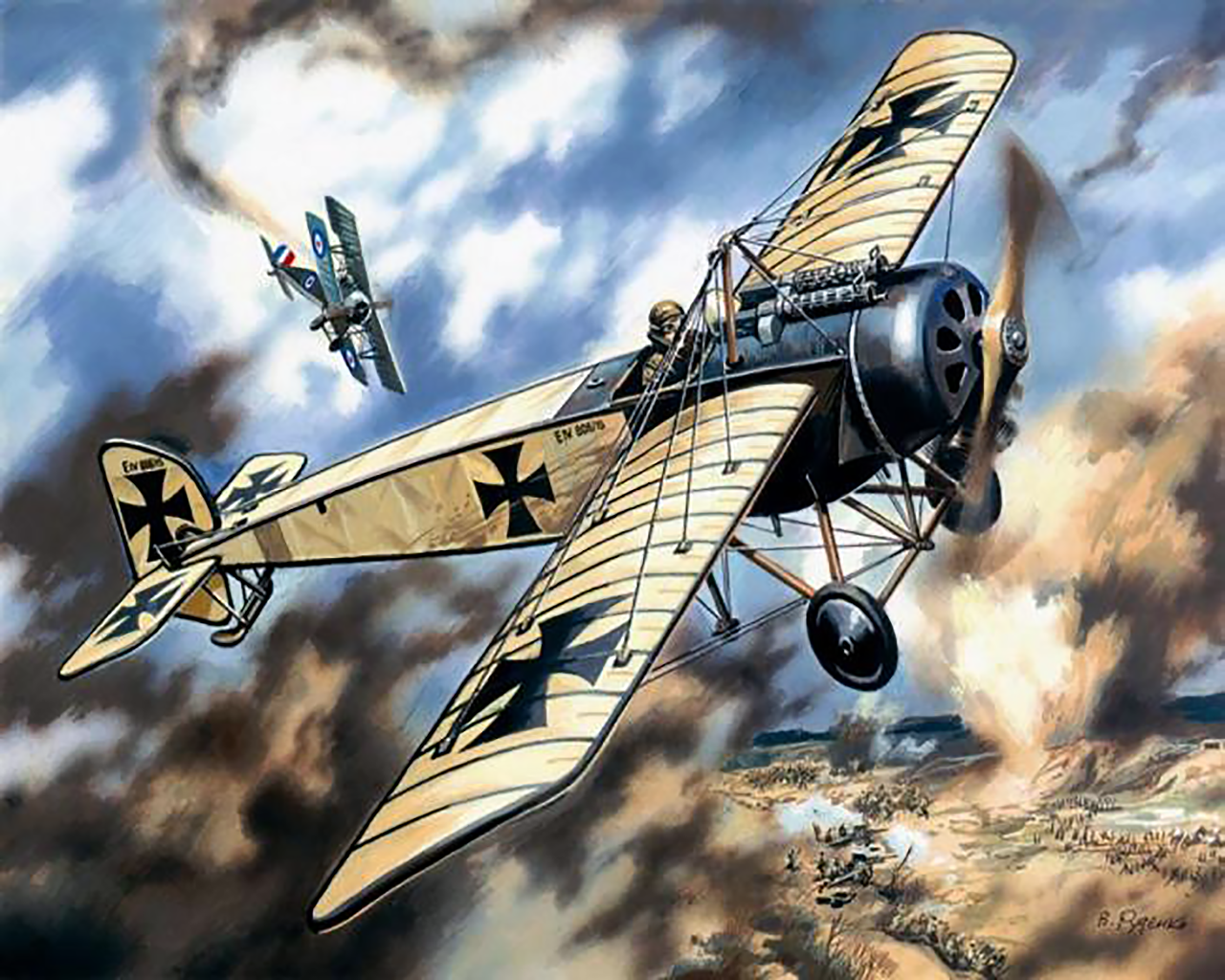
World War 1 Pfalz EIV
I.G. Farben
As early as 1885 there were patent disputes with Bayer AG about the production of the colour Congo red, after which an agreement was reached on the joint use of future patents. This collaboration resulted in 1904 in the dye chemistry interest group, the trio, to which the Actien-Gesellschaft für Anilin-Fabrication, Bayer and BASF belonged.
On December 10, 1925, this resulted in I.G. Farben AG. With the founding of the IG Farben AG interest group, the optical institute, along with Bayer, also belonged to this group. There was debate as to how best to house them, with votes for joining Zeiss Ikon, a company that was already the result of a merger, among others.
Eventually, however, all photographic activities came to Agfa, i.e. the photo factory in Leverkusen from Bayer, in which photographic paper was manufactured and the Optical Institute, which was renamed Agfa Camerawerk Munich.
This Division III of I.G. Farben had its headquarters in Berlin SO 36, namely in Treptow, Lohmühlenstraße, the address of the former factory Dr. Jordan. Paul Mendelssohn Bartholdy, the son of the company founder of the same name, became director of Division III.
In the I.G. Farben was initially organized regionally at Carl Duisberg’s suggestion. He saw parallel locations as a competition that would stimulate research and development and spoke of “ideal competition”. After that, the Camerawerk belonged with Agfa Wolfen and Agfa Berlin to the Mitteldeutschland joint venture.
However, the world economic crisis then led to the conversion according to Fritz ter Meer’s plans: Now technically related activities should be combined in order to avoid duplication of research.
Three divisions were set up and managed by scientifically trained employees. The Camerawerk came to division III production and sales of finishing products. The manager was Fritz Gajewski, who was also the works director in Wolfen.
In Berlin, Agfa Berlin SO 36 was set up, a sales association for photographic materials, artificial silk and fragrances. She was relatively independent and had the decisive voice in Camerawerk’s sales program. As a result, technical arguments were not entirely decisive; rather, photo technology was a sales tool to increase film sales.
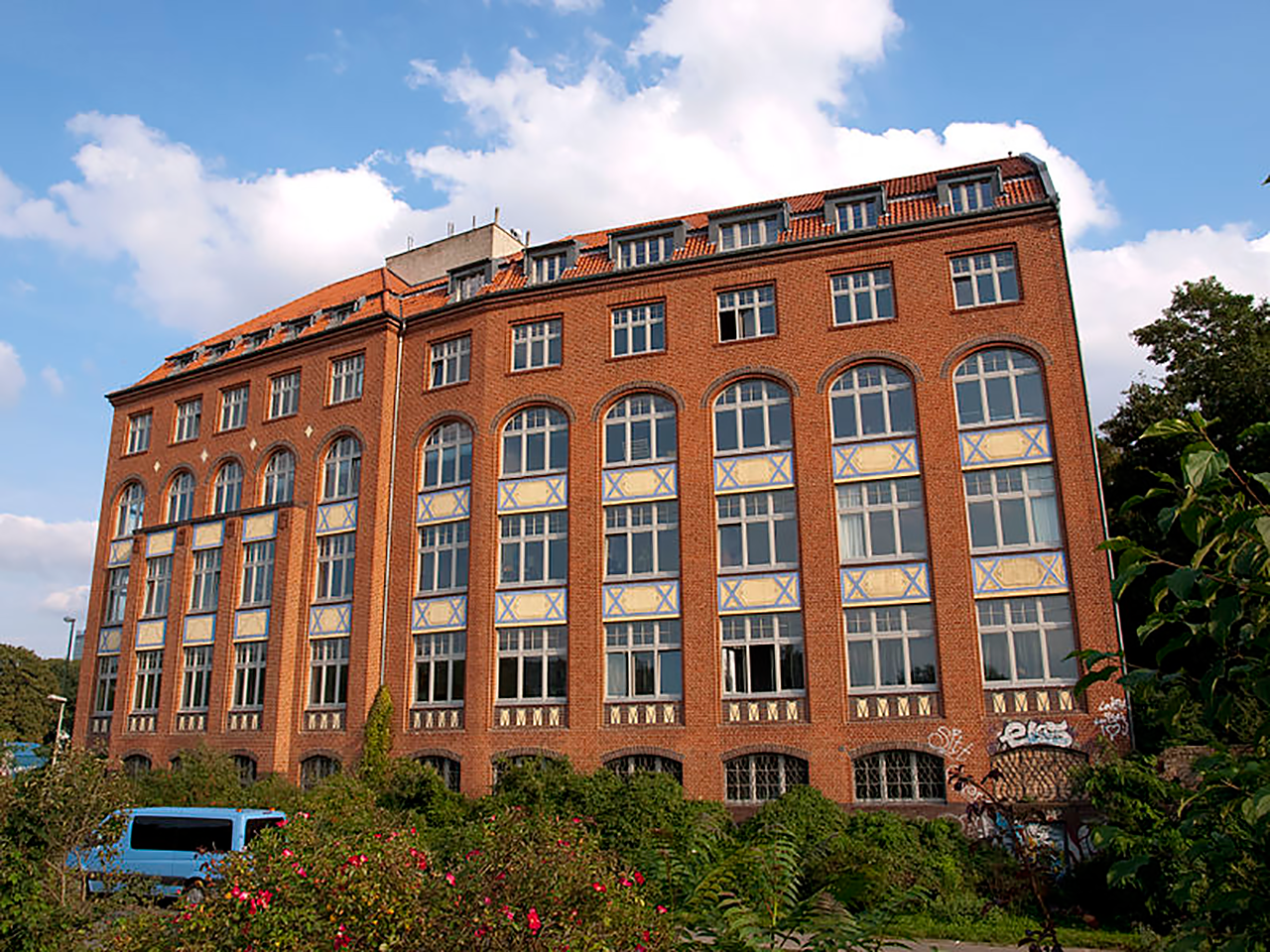
In the 1930s, in the Agfa company complex at Lohmühlenstraße 65-66 was still home to Agfa-Foto and the sales facilities of the I.G.Farben.
The time of the national socialism and wartime
In 1934 there were the first orders from the weapons departments. In 1940 production consisted almost entirely of Wehrmacht orders. Civilian cameras could only be repaired, not sold, and stocks had to be exported.
At the time of National Socialism, Agfa used large numbers of forced laborers, including concentration camp prisoners in the Munich sub camp (Agfa Kamerawerke) of the Dachau concentration camp and in the Dutch transit camp at Kamp Westerbork. Between 1943 and 1945, forced laborers were also used for Agfa AG in the “Agfa Warehouse” branch office of the Munich-Stadelheim youth prison.

Forced laborers and concentration camp prisoners at Agfa
From September 13, 1944 to April 30, 1945, the concentration camp Munich (Agfa Kamerawerke) plant at Tegernseer Landstraße 161 in Munich-Giesing was one of the 169 satellite camps of the Dachau concentration camp. A total of about 700 female concentration camp prisoners worked here, an average of 500, including 200 from the Netherlands and about 300 from Eastern and South-Eastern Europe, mostly Poles.
They did forced labor at Agfa Camerawerk, then part of I.G. Colors. There, time fuses for anti-aircraft grenades were assembled and parts for the V1 and V2 weapon systems were manufactured. The women were accommodated in the housing block Weißenseestraße 7-15 in Munich-Giesing, which was not yet completed at the time but still exists today, and which had been damaged in a bomb attack before it was completed.
About six women were housed in each room. A barbed wire fence and four watchtowers surrounded the site. The walk to the factory took about twenty minutes. The commander of the guards was Kurt Konrad Stirnweiß.
In the reports of the Dutch women, SS Untersturmfuhrer Stirnweiß is perceived as strict and conscientious, but he also stood up for the concentration camp prisoners. His deputy Alexander Djerin was seen more negatively. Little is known about the eleven female guards, with the exception of the unpopular Mrs. Richter, who frequently beat the prisoners. In Munich there were also the Munich-Neuaubing (Dornier) and Munich-Riem sub-camps, as well as more than 30 other Munich concentration camp sub-camps.
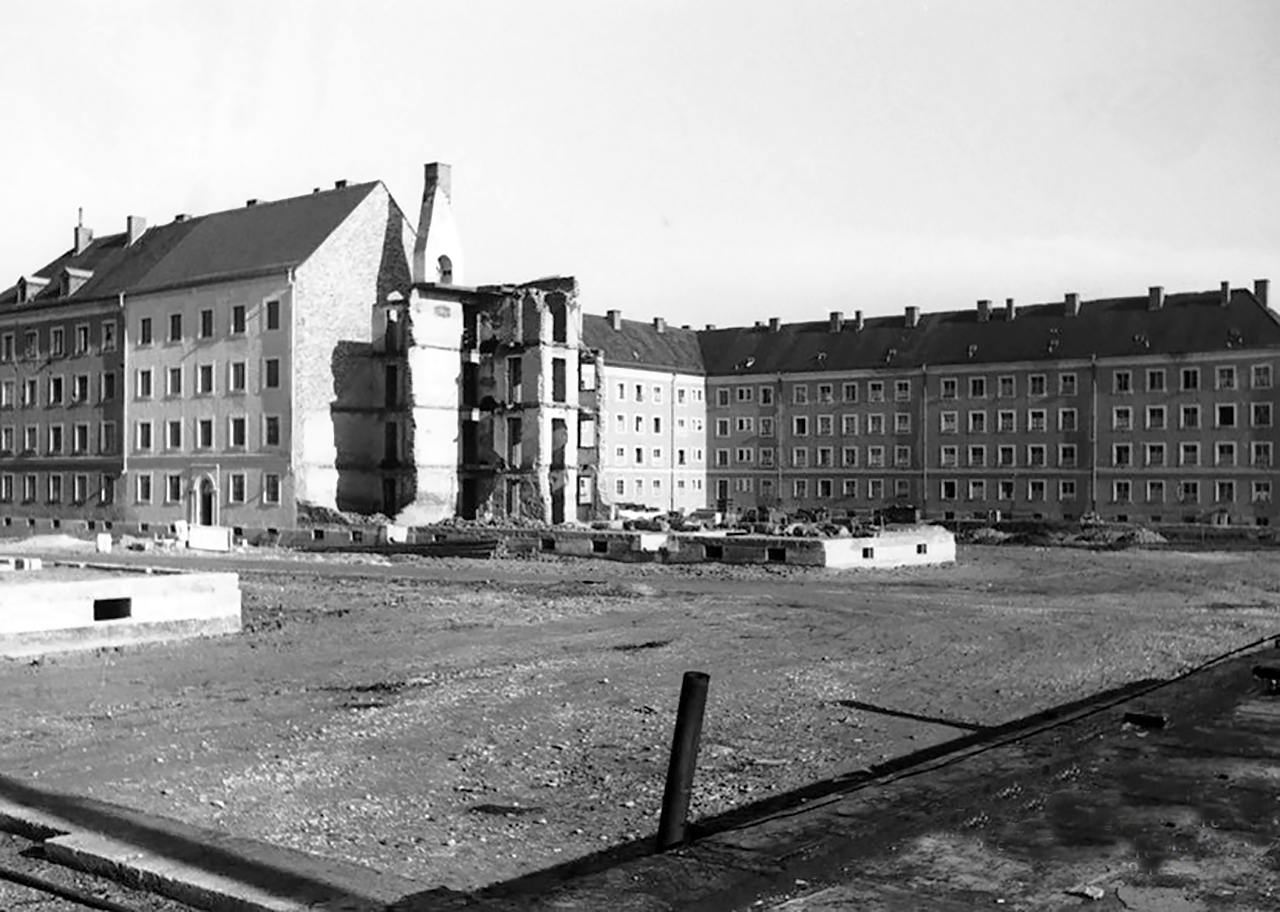
Back of the former subcamp Weißenseestraße 7-15, in November 1949
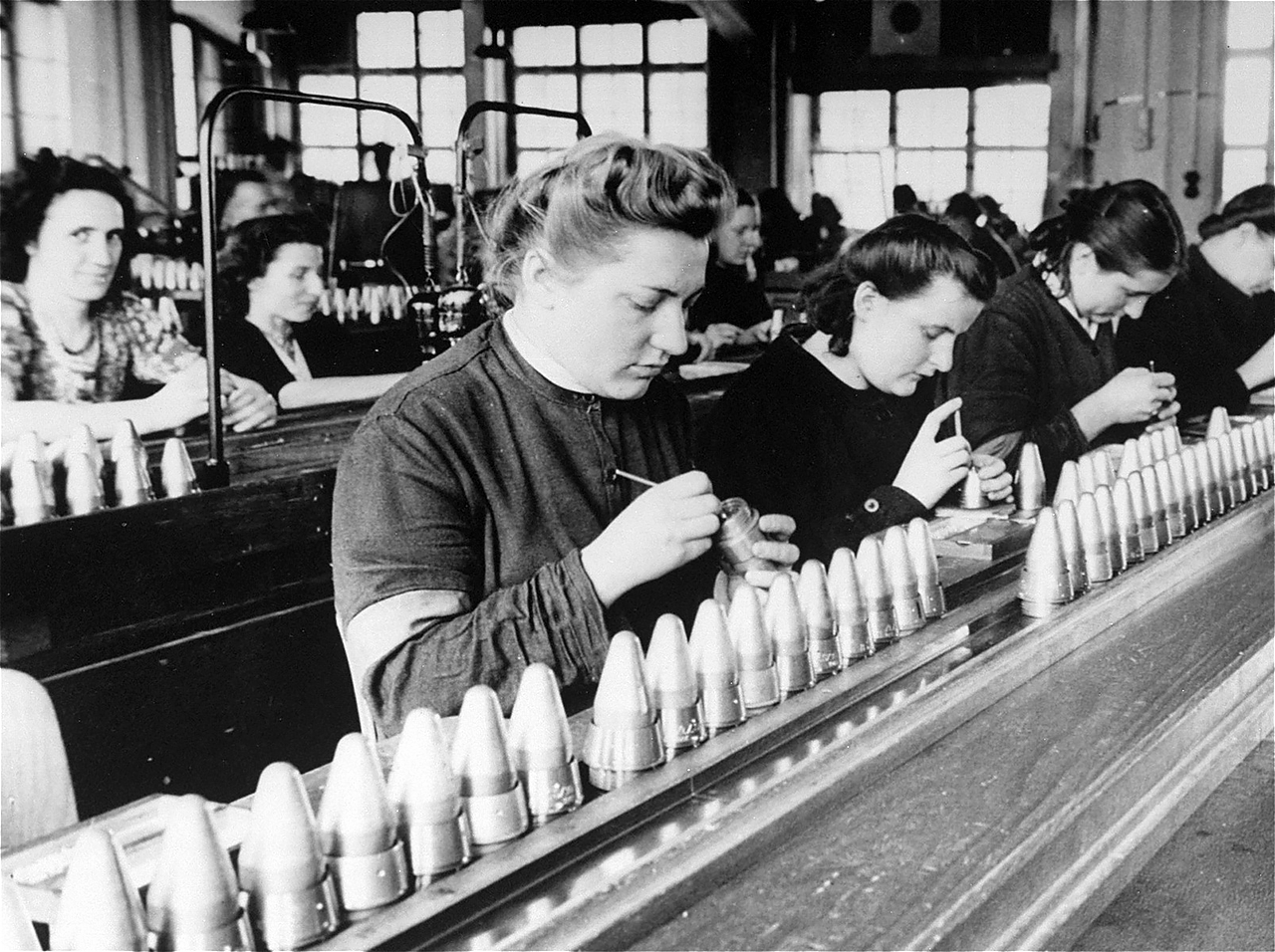
Manufacture of bomb detonators by imprisoned foreign workers at Agfa in May 1943
prisoners
193 Dutch women and ten women from other countries were arrested mainly because of their resistance activities. The same was true for the Slovenians. The Polish women had been deported to the concentration camp as a retaliatory measure for the Warsaw Uprising. The Dutch women came from the Herzogenbusch concentration camp and the Haaren prison.
As the Allies advanced, the prisoners were transported to Germany and transferred to Ravensbrück concentration camp on September 8, 1944. The approximately 250 women, including Dutch women, who arrived in Munich-Giesing from Ravensbrück on October 15, 1944, exchanged around 250 mostly Polish women, who were sent back from Giesing to Ravensbrück on the same day.
According to this, all women in the Agfa camera works sub-camp must have lived under the threat of being sent back to Ravensbrück.
On April 9, 1945, shortly before the end of production in the factory, nine forced prostitutes were transferred from the Dachau main camp to the Agfa camera works sub-camp. There were about five prostitutes among the Dutch women. About fifty of these women also came to Germany from the Herzogenbusch concentration camp. They were accused of infecting Wehrmacht soldiers with venereal diseases.

Life in the camp
Initially, the information about the Agfa camera works satellite camp came from Ella Lingens’ book Prisoners of Fear. Ms. Lingens was a political prisoner and doctor in Auschwitz and for a short time in the Agfa camera works sub-camp. Her portrayal of this satellite camp triggered violent protests from the Dutch survivors of the camp because, among other things, she portrayed the Dutch women as naïve and misinterpreted facts. As a result, some Dutch women published their own reports. The most detailed report comes from Kiky Gerritsen-Heinsius. Substantial reports from women from other nations are not known.
Torture, murder and brutal harassment were not part of everyday life in the Agfa camera works sub-camp. The women have suffered from the many air raids, the cold, poor nutrition, inadequate hygiene and poor clothing. Illnesses were the result. In addition, since the evacuation of the Herzogenbusch camp in early September 1944, the Dutch women had been completely cut off from their homeland. They received neither mail nor packages. Two Dutch women died during their stay in Munich.
According to unconfirmed testimony by Leni Leuvenberg, twenty Polish women housed on the premises of the Agfa works were killed in an air raid on February 25, 1945. L. Eiber names a forty-year-old Polish woman who died on October 7, 1944. The women worked on the assembly line with German civilians. There was always a German next to a prisoner. The civilians were forbidden to approach the prisoners. There were, nonetheless, courtesies from civilians much appreciated by the prisoners. The proximity to them also protected the prisoners from assaults by the guards.
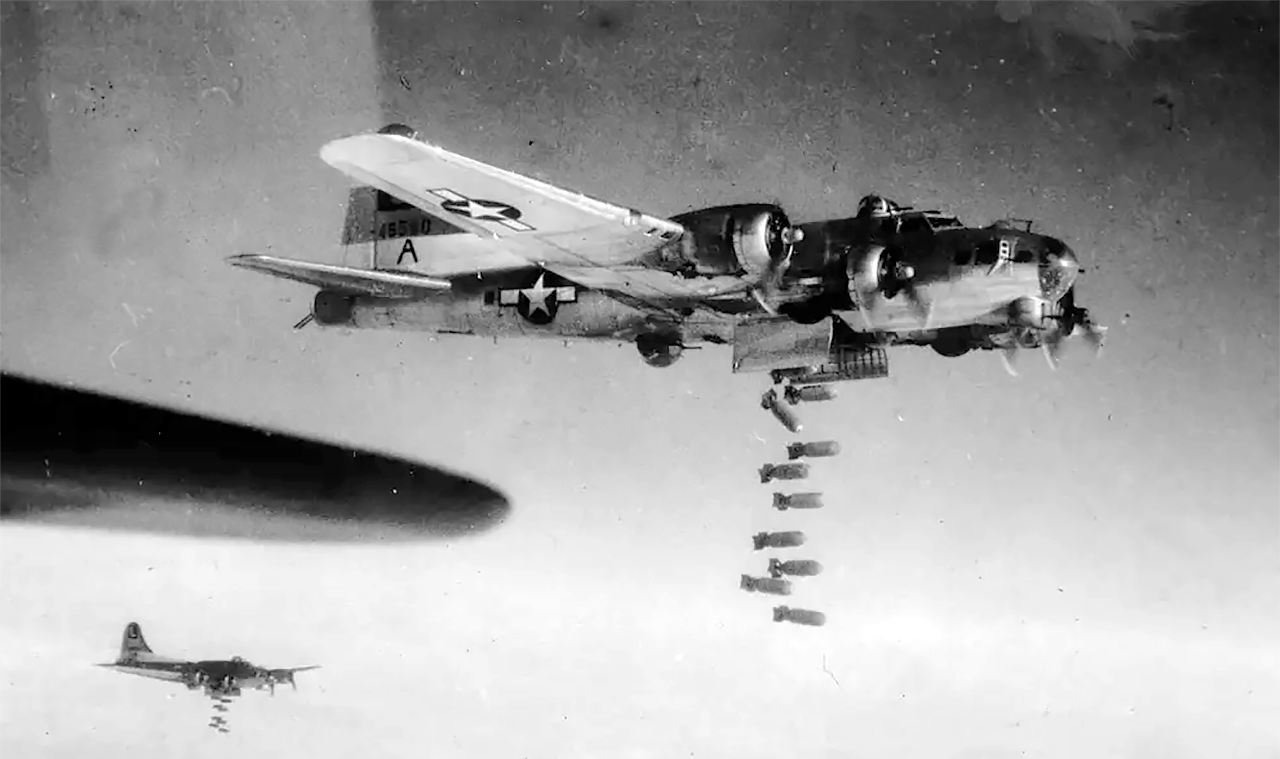
Apart from the cold, poor food, poor hygiene and inadequate clothing, the constant bombardments were also part of everyday life.
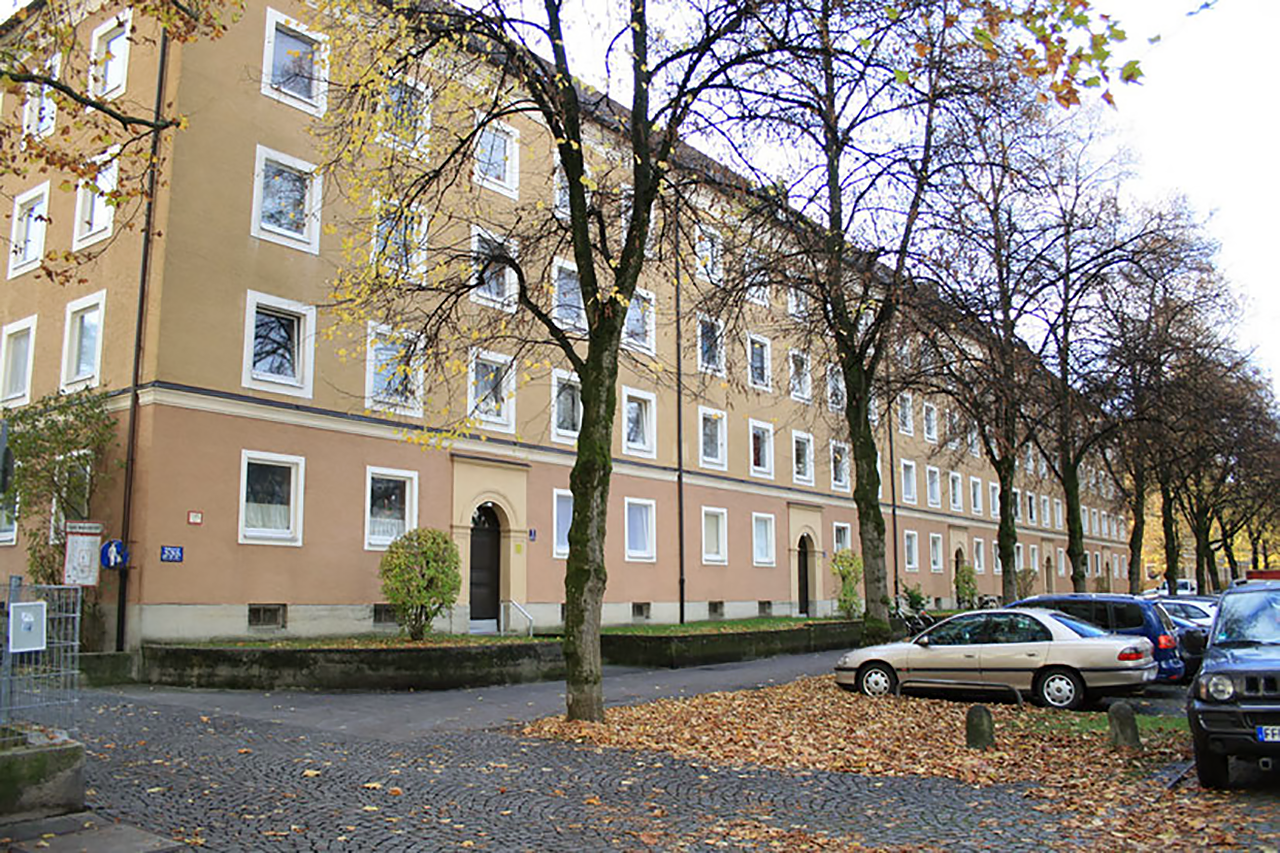
The former concentration camp subcamp Weißenseestraße 7-15 in 2017
strike
On January 12, 1945, the Dutch women went on strike, supported by the Slovenes. The women spontaneously and haphazardly refused to work together. Nevertheless, a ringleader was selected for this action, and the Dutchwoman Mary Vaders was severely punished with imprisonment in the Dachau concentration camp.
The situation was relatively mild because the women did not oppose the camp management, but the factory management. They protested against the work pressure exerted by the factory and against the food provided by Agfa.
Before that, the prisoners’ food came from the main camp at Dachau. Although it was often delivered late due to the war, it was almost sufficient, unlike the food from the Agfa factories.
The Dutch women stuck together. They made handicrafts, wrote poems and held church services. There was little free time, but during the turn of the year the factory was closed for a few days. Sabotage of production and machines is often reported.

Liberation of Wolfratshausen
On April 23, 1945, the plant was closed. The transport routes to the factory were destroyed and production came to a standstill without the supply of material. On April 26, 1945, the women received the marching orders. The majority left the Giesing camp early the following morning; only the sick and a few other women remained in the camp. It is said that the women were free to remain in the camp.
The fact that the vast majority left the camp indicates that the women trusted Commander Stirnweis and were afraid of the destruction of Munich. The so-called death march ended in Wolfratshausen. The women reached the Walserhof in Wolfratshausen late in the afternoon of April 28th. The route between Giesing and Wolfratshausen is unclear. It is said that they marched via Grünwald to Deining, then west, but then the women would have arrived in Wolfratshausen on April 27th.
On the evening of April 30, the Americans reached Wolfratshausen. On May 1, Commander Stirnweis placed the women in the care of the Allies. We have the Walser family in Wolfratshausen to thank for accommodating and caring for the approximately five hundred women on the farm. The women who stayed behind in Munich and in the Dachau infirmary were liberated by the Americans around April 30, 1945.
On May 4, the women were transferred to the Föhrenwald camp. The majority of the Dutch (and the ten relatives) were picked up by the Swiss Red Cross in Föhrenwald on May 15. From Switzerland they returned to the Netherlands with a special train via France and Belgium.
Legal processing
After the war, as part of the Dachau trials, Kurt Konrad Stirnweis was sentenced before an American military court to two years in a labor camp and his deputy Alexander Djerin to four years.
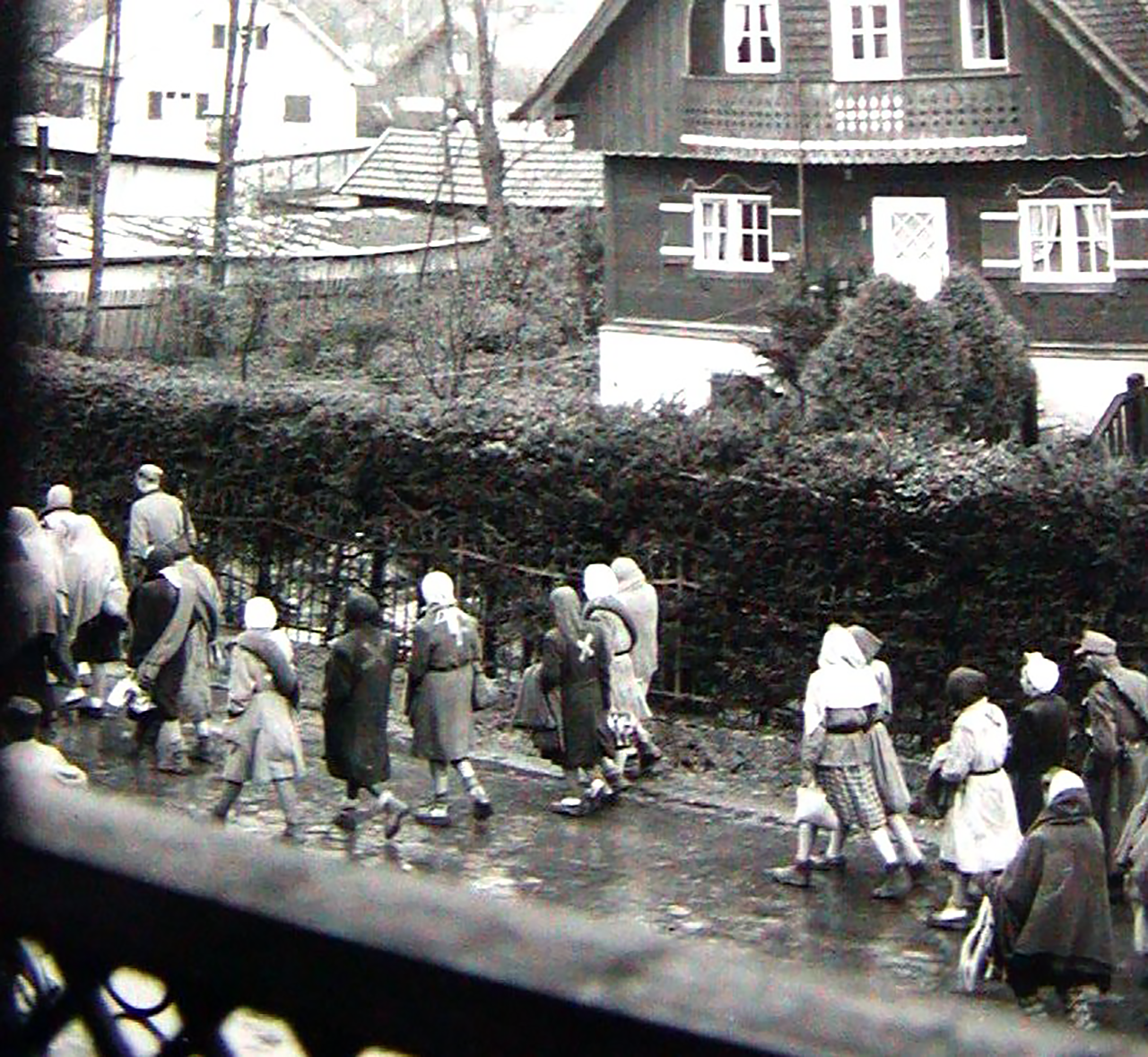
Dutch women in the Außenlager „Agfa Kamerawerk“ of the KZ Dachau, in Munich. The photo shows the women on the morning of 28.04.1945 in Percha (near Starnberg) on their way to Wolfratshausen.
Destruction
There were different reports about the bomb damage. Camerawerk management found 40% of the buildings to be destroyed, while the Bavarian Ministry of Economic Affairs found about a fifth, just slightly more than the average figure for industrial buildings in Bavaria of 15%.
The machines were largely preserved, since they had already been outsourced in the spring of 1944. The sales offices in Berlin were almost all burned out.
A lack of skilled workers, a lack of raw materials and no supplier parts from the Soviet occupation zone meant that production was slow to start. 7,500 cameras before the war faced a daily production of 60 cameras in two model series in the fall of 1945, all of which was used by the US Army.
In autumn 1946, 91% of production went to the US Army, 6% to the French Army and 3% to the German Economic Office. In 1947, Camerawerk Munich was third in Germany with a production of 60,000 cameras, after Leica and Kodak Stuttgart.
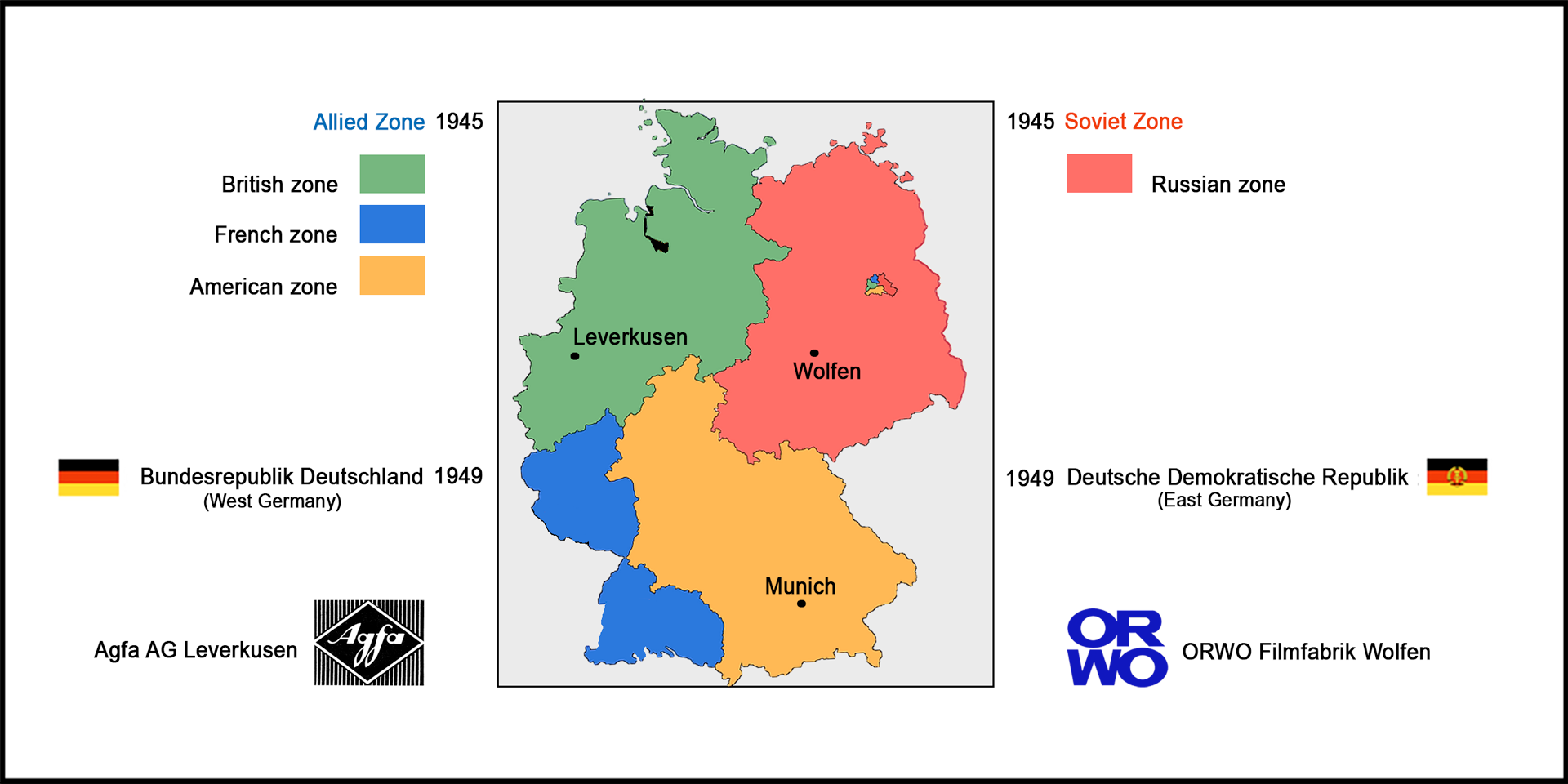
Occupation zone borders in Germany, 1947. Berlin is the multinational area within the Soviet zone.
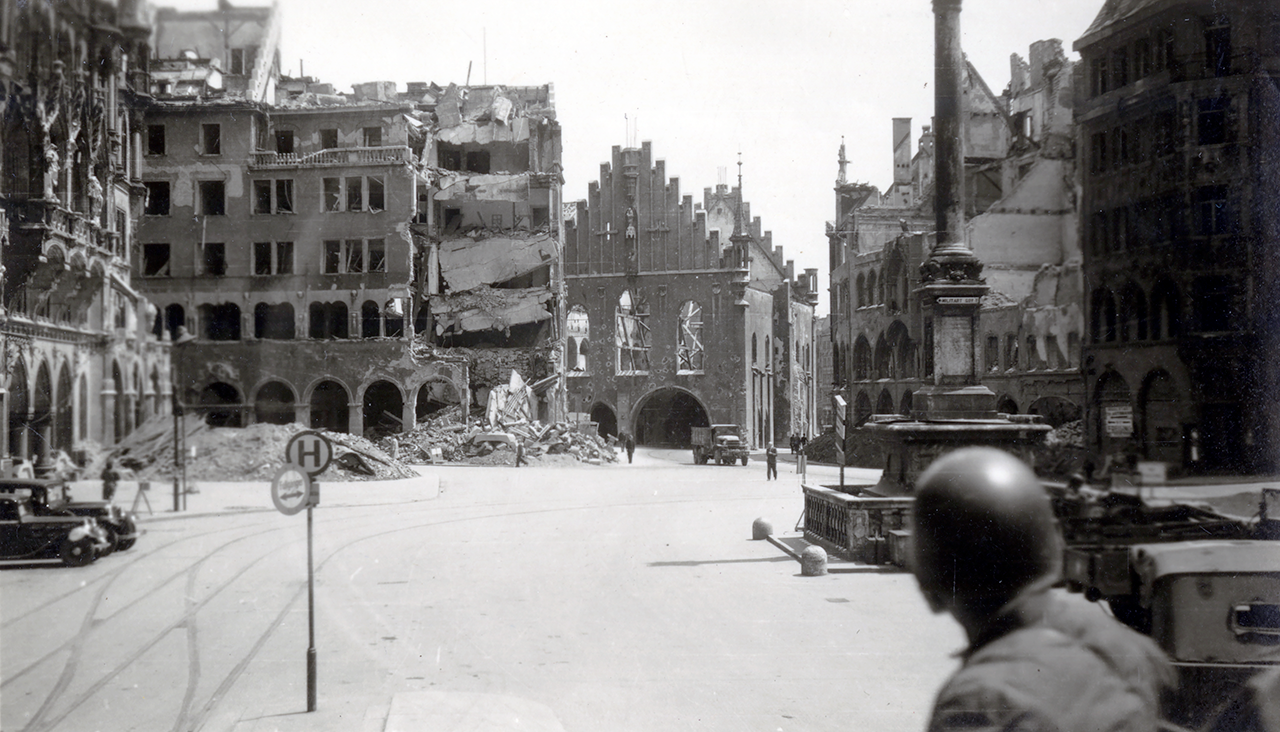
Downtown Munich square with Military Government building and soldier looking toward it. Munich. 1945
An east and a west section
After 1945, the Agfa factories were located in different occupation zones, which made it difficult to merge again. There were also forces that absolutely wanted to prevent a merger. In particular, the Belgian company Gevaert was interested in a takeover.
The Agfa camera factory in Munich was in the American zone of occupation, the Agfa photo paper factory in Leverkusen in the British zone of occupation and the Agfa film factory in Wolfen in the Soviet zone of occupation. All factories had already been able to resume production in 1945.
In the USA, the Agfa-Ansco Cooperation (Binghamton) again took over distribution. However, this did not apply to the Agfa films, since there was now an Ansco film production.
The efforts of Ulrich Haberland’s employees in particular finally led to the High Commissioners allowing him to remain at Bayer. As a result, Agfa AG for photo fabrication was founded in Leverkusen on April 18, 1952. Allied control of camera production ended on March 18, 1953, so that Agfa-Camerawerk AG was founded on March 20. In 1957 both companies were combined to form Agfa AG Leverkusen.
Agfa Wolfen in the eastern part of Germany
The photochemical production site was relocated from Treptow to Wolfen around 1909. After the Second World War, the film factory was taken over first by the US armed forces and then by the Soviet Military Administration in Germany (SMAD).
During this time, the Wolfen film factory was organized as a Soviet joint stock company to settle the reparation claims of the Soviet Union.
Although the Agfa management had transferred all important patents to Leverkusen before the end of the war, the East German counterpart caused major problems for Agfa’s West German branch:
Filmfabrik Wolfen also sold its products with the Agfa logo, which confused customers.
Initially, the East German side took the position that it was Agfa’s legal successor. However, this strategy did not stand a chance in court because a Soviet joint-stock company could not be a successor.
Surprisingly, however, the GDR government later did not insist on sticking to the Agfa brand name. Rather, she believed that the products of socialist manufacture were of such high quality that they did not need a big name to find a market.
In Wolfen, however, they did not want to do without the name. Without an agreement between the two parts of the company, however, there was a risk that the rights would fall to a third party.
In 1956, a trademark agreement was signed that was to last until 1964. According to this, the Wolfen film factory was allowed to use the brand name in the Eastern Bloc, and Leverkusen in the rest of the world with the exception of France and Yugoslavia. An international court should decide on these two countries. Nevertheless, East German Agfa products kept coming to the West German markets.
After the end of the business organization as a Soviet joint-stock company, the East German company used the names VEB Filmfabrik Agfa Wolfen and VEB Film- und Chemical Fibers Works Agfa Wolfen until 1964. After 1964 the company in Wolfen was renamed ORWO for Original Wolfen.
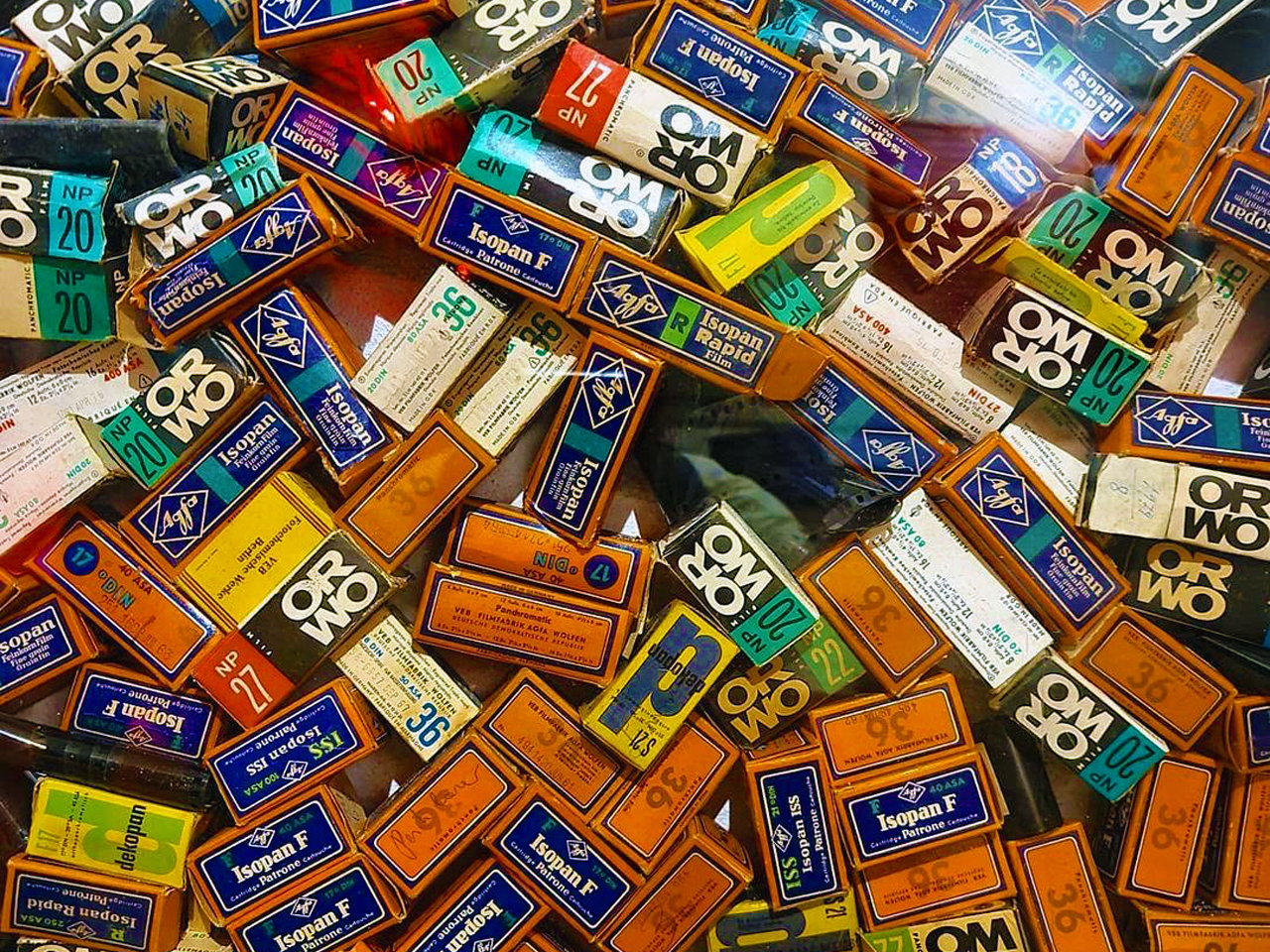
The post-war confusion summarized in one photo: Agfa and Orwo materials brotherly united.
production in the western part of Germany
As already mentioned before, production resumed in Munich after World War II under American administration. Under the leadership of the technical operations manager Willy Kisselmann, director of the Munich camera factory since 1961, a branch was founded in Rottenburg an der Laaber in 1964, another in Peiting in 1969 and a third in Peißenberg in 1970, where the coal mines were affected after the closure new jobs were created for workers.
The specialist devices for medical and print preparation technology were manufactured in Peißenberg and the large laboratory devices in Peiting. Both production sites operated their own parts production for the essential technologies of the parts spectrum, which were gradually replaced by outsourcing for cost reasons.
In 1974 a production site was added in Coimbra; a joint venture has existed since May 1960 in the former Indian capital of Baroda (now Vadodara) and contract manufacturing at Fabrique d’Horologie La Vedette SA in Saverne, France.
product range
Agfa improved its pre-war camera models and introduced the new 35mm Solinette. In 1954 it modernized its camera design with the Silette series. The pre-War Isolette was the basis of the highly successful series of medium format folders in the 50s, culminating in the Super Isolette and the Automatic 66 (a folding camera with aperture priority AE, in 1956).
In 1959 a 35mm viewfinder camera with auto-exposure button followed, the Optima. The Agfa Optima was the world’s first camera with automatic programming, and in 1968 the introduction of a uniform design line under the direction of Schlagheck Schultes Design with the Optima 200 sensor.
During the 1950s, Agfa still sold the simple cameras for roll film, type 120, first the box cameras and then the Clack, which can be counted among the box cameras, and the Click. With the advent of Kodak’s Instamatic cameras, Agfa initially relied on the Rapid system with modest success and then transitioned to Instamatic cameras as well.
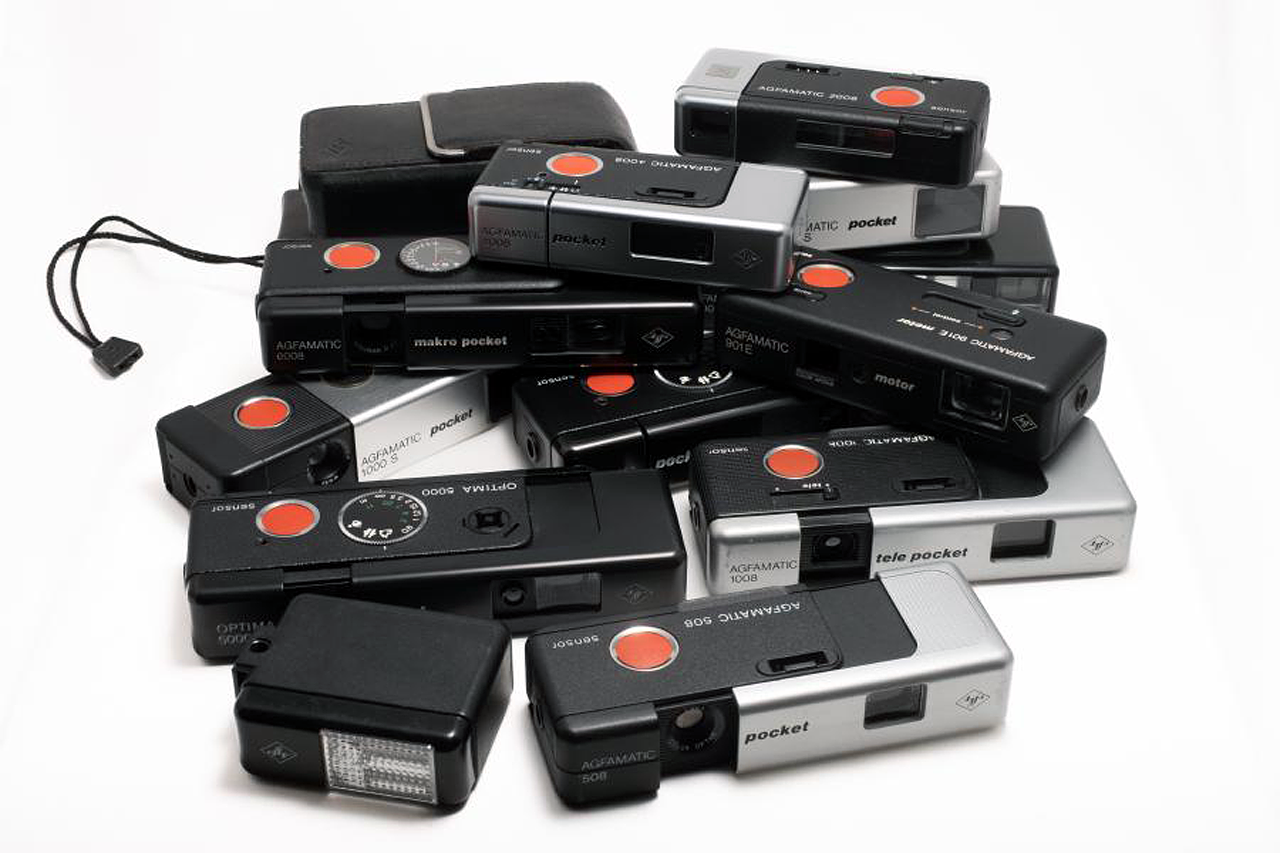
Ritsch-Ratsch-Klick: Long before mobile phones and digital cameras, taking pictures from your pocket became a popular sport. Small, handy and light, pocket cameras were everywhere in the seventies.
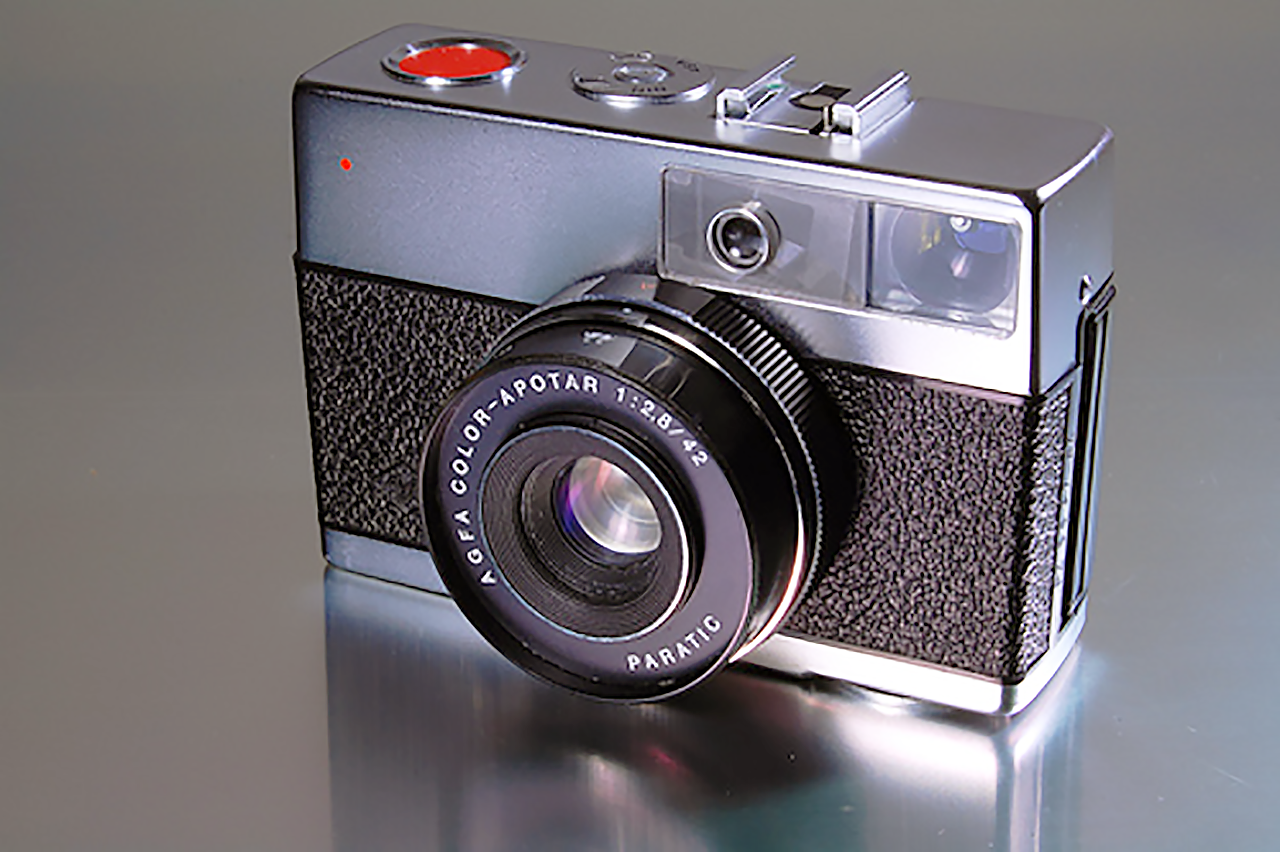
The Agfa Optima, introduced in 1969, as part of the Optima Sensor range, is a fairly eccentric 35mm film viewfinder camera with automatic exposure. Like all Agfa Sensor cameras, it has the large round orange shutter release on the top plate.
“Ritsch-Ratsch”
Agfa had a huge success with its popular “Ritsch-Ratsch” pocket cameras, which accepted 110 cartridge film. A whole series of these Agfamatic cameras was launched twice, the first series using Magicubes and the second, flipflash. Of course these cameras had the red sensor point as shutter release button.
Like almost all manufacturers, Agfa relied on the Super 8 cassette from Kodak for smallfilm cameras and was particularly quick to offer a small pocket camera with the Microflex. However, Agfa film cameras did not have nearly as high a market share in their segment as still cameras.
The last generation appeared in 1976 with the Movexoom 6 and Movexoom 10 models, which were trend-setting with their modern electronics, but encountered a sharply declining market, so that production was discontinued in 1977. The System Family was then supposed to initiate a renaissance of Super 8 film, but it was a failure. In line with the slogan everything from a single source, not only cameras were manufactured, but also projectors and accessories such as slide viewers.
Acquisition of small businesses
To expand production capacity, Agfa acquired several small companies in the 1950s and 1960s that were no longer able to offer competitive products due to their size. Due to the growing shortage of workers, all companies in Germany, including Agfa, accepted long transport routes in order to be able to produce a sufficient number of items at all.
It all started in 1952 with UCA – Vereinigte Elektro-Optische Werke GmbH in Flensburg-Mürwik, which began around 1948 to manufacture viewfinder cameras and even single-lens reflex cameras in the former marine engineering school.
In 1962 the Hamburg camera manufacturer Iloca was taken over, in 1969 the Optical Works Dr. Staeble in Altenstadt (Upper Bavaria), which produced camera and projection lenses.
In order to be able to build all camera shutters and exposure meters itself, Agfa also worked with watch manufacturers, namely from 1959 with the Fabrique d’Horologie La Vedette SA in Saverne (Alsace) and from 1960 with OSCO watches, Otto Schlud in Schwenningen.
Shortly thereafter, Agfa acquired 50.24% and 75% respectively of both companies. The chemical factory in Vaihingen and the gelatine factory in front of Agfa also came into the hands of Agfa. Koepff & Sons, Mimosa and the Leonar works in Hamburg-Wandsbek.
In 1961 Agfa AG took over 50%, and in 1964 100% of Perutz-Photowerke in Munich. Otto Perutz founded this company in 1880. It initially produced photographic plates, and from 1922 also roll films.
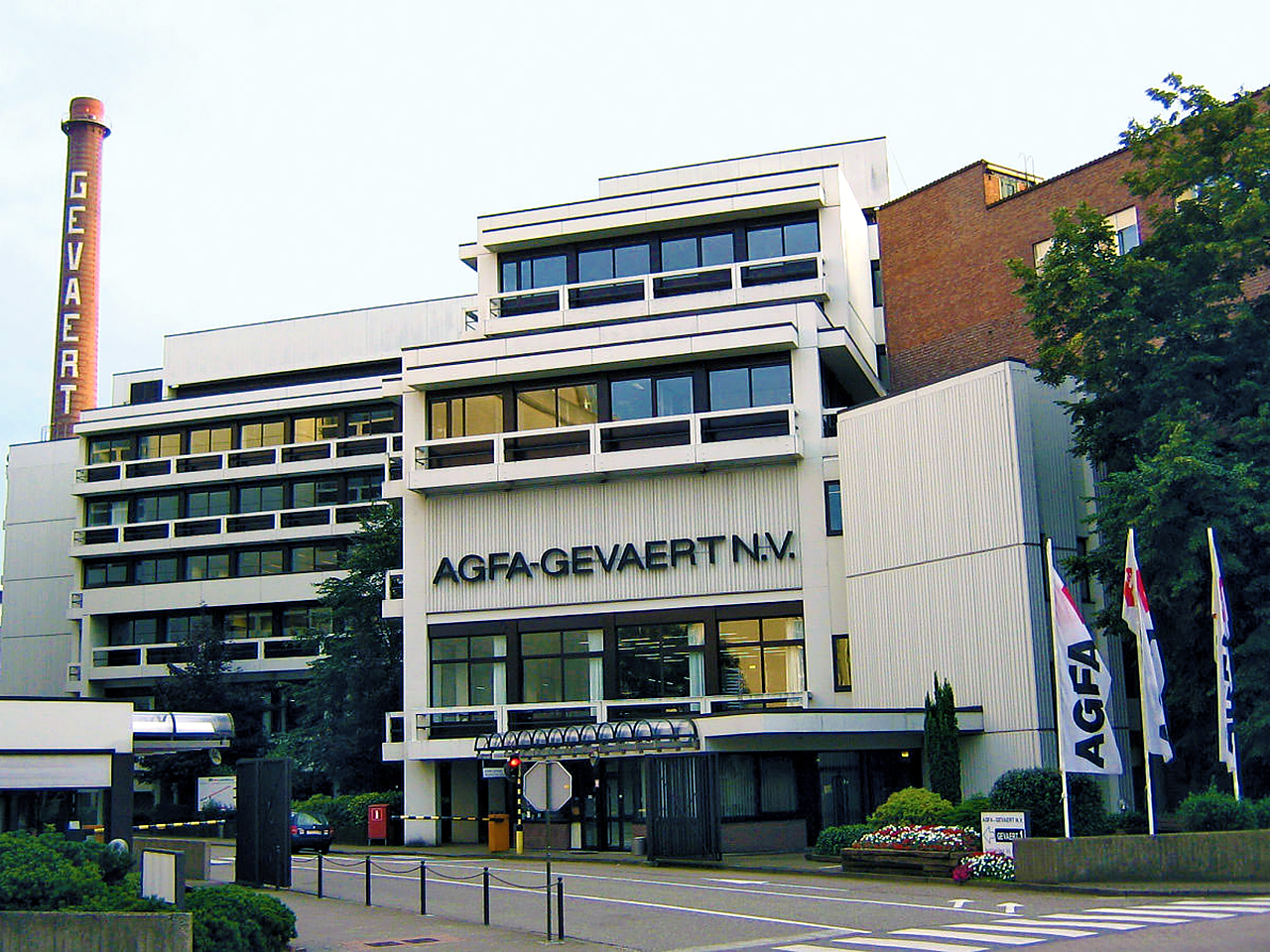
Manufacturing facility Agfa-Gevaert-NV Mortsel, Belgium
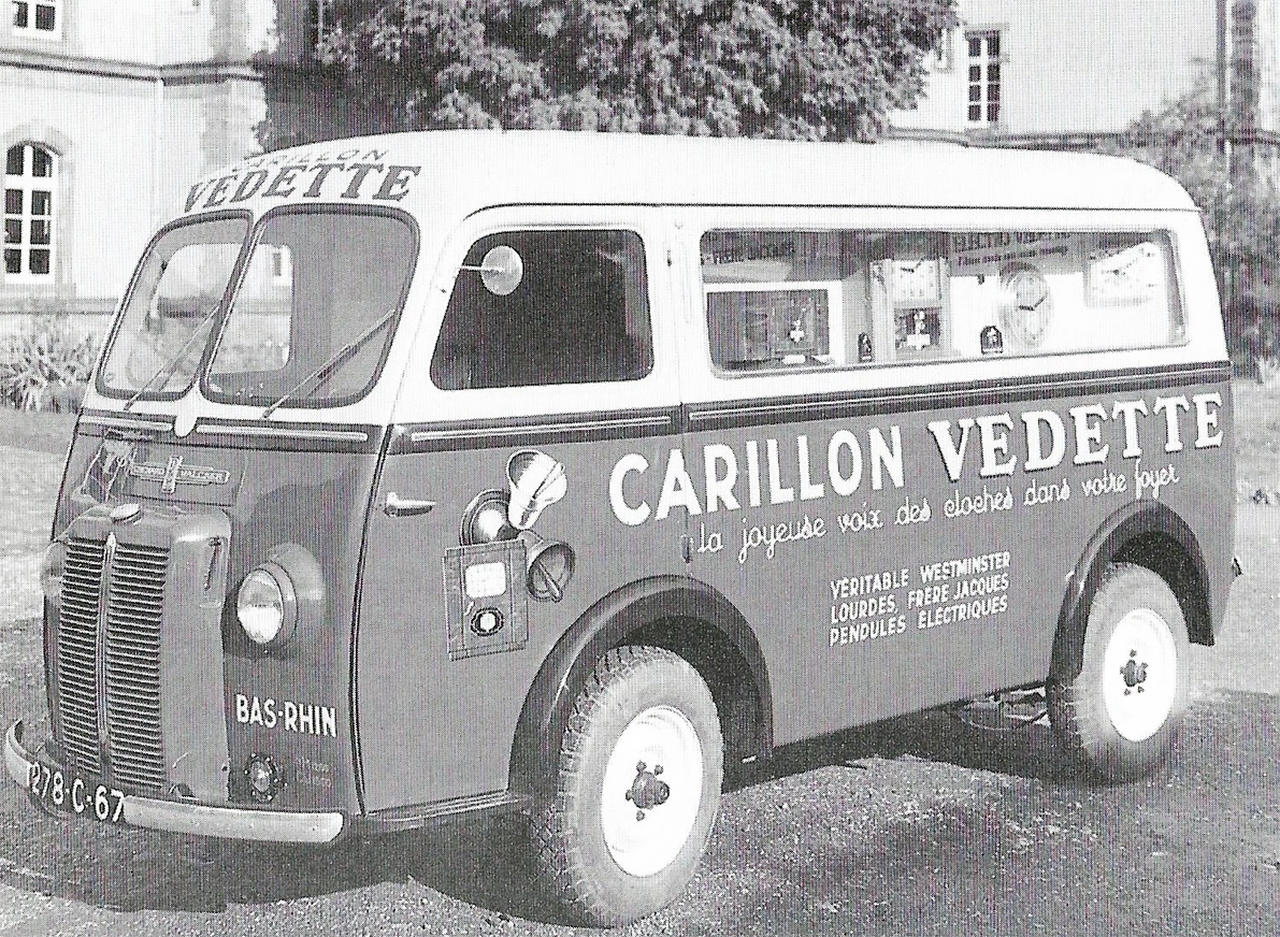
An advertising van of the French watch company Fabrique d’Horologie La Vedette SA from Saverne (Alsace), traveling all over France displaying the slogan “Carillon Vedette, the joyful voice of the bells in your home” on their sides.
Acquisition of large businesses
While Gevaert intended to take over Agfa at the end of the 1940s, a merger now took place: Agfa took over Gevaert and so the so-called big solution came about in 1964: the founding of the Agfa-Gevaert Group.
It included Agfa-Gevaert AG based in Leverkusen and Gevaert-Agfa N.V. based in Mortsel. Gevaert was founded in Antwerp in 1894 by Lieven Gevaert and initially only produced photographic paper. For this merger, Agfa had to convert all holdings in foreign companies into its own.
Schlagheck Schultes Design
Herbert H. Schultes and Norbert Schlagheck both worked as designers at Siemens. Contact with Camerawerk Munich came about through a business relationship between Siemens and Agfa. They then founded the Schlagheck Schultes Design studio in 1967 and have designed all Agfa cameras ever since. All decisions were made as a team, but Schultes was responsible for the cameras and Schlagheck for the Super 8 cameras. The success of the design office is also based on the fact that marketing, sales, engineers and designers met to discuss all aspects, including ease of repair and sales packaging.
The new line followed the Bauhaus tradition and was extremely successful. This was especially true for the successful Pocket series. Schlagheck Schultes Design also designed the sales packaging. These were often sets consisting of a camera, carrying chain, film, flash cube or device, sometimes also an ever-ready case. From 1970 the studio was also responsible for Agfa’s corporate identity.
Sensor shutter release buttons
The widespread use of the Optima with its program automatic showed more and more correctly exposed images in the photo laboratory evaluations which were continuously carried out by Agfa. However, there were still numerous blurred images, some of which seemed to be due to the long release distances of the release button. Therefore, a button was developed that moved a maximum of 0.5 mm.
In the advertisement, Agfa spoke of the sensor release button and drew attention to it through its design. Above the release lever was a circular plastic disc, a slightly pre-stressed injection molded part in orange-red, Agfa’s advertising color. Moreover, with a diameter of 16 mm, this device was extremely large for a trigger. As a side effect, the conspicuous appearance had the advantage that it gave an answer to the question “Where should I press?”.
By the end of production in 1983, Agfa equipped all photo cameras and even some film cameras with this release button design, with the exception of the entry-level model, which had to do without it for cost reasons. By 1972, 1.5 million cameras were sold with the sensor trigger.
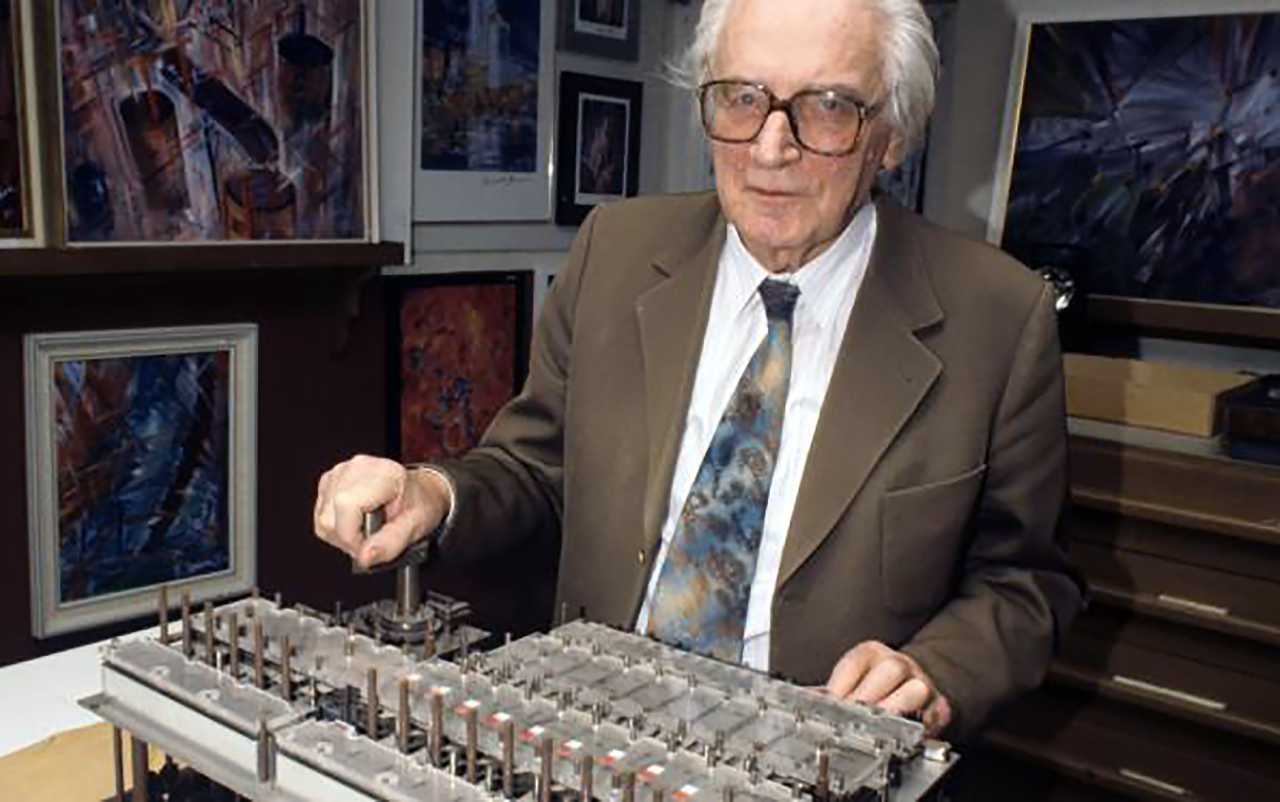
After completing his engineering studies in Berlin in 1935, Konrad Zuse (1910-1995) built the Z1, a programmable mechanical calculating machine. His company was taken over by IBM and later by Siemens. Konrad Zuse himself received eight doctorates and two honorary professorships.
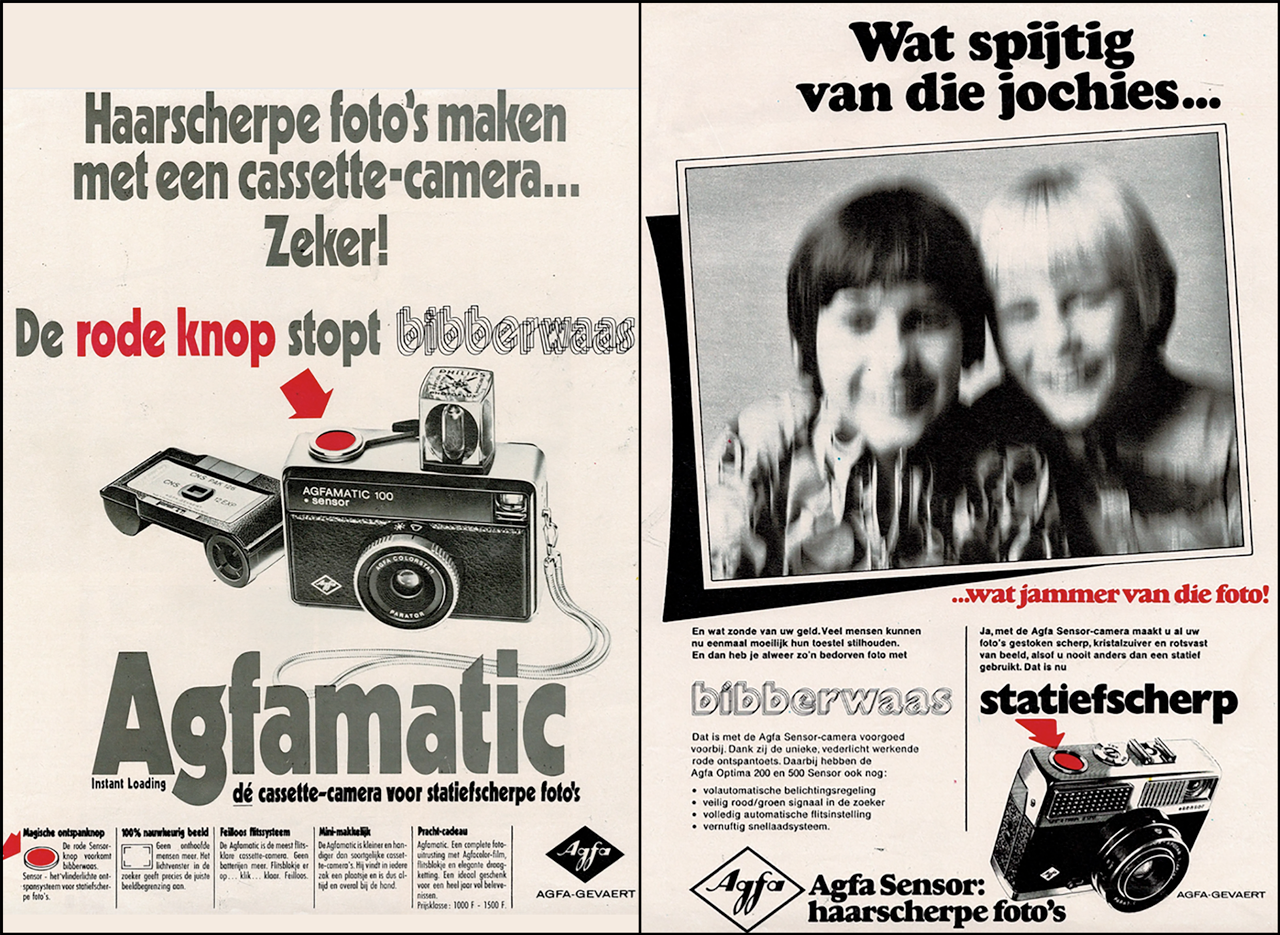
Two Dutch advertisements, in which the red sensor button puts an end to blurry photos and a “shiver haze” (1950s).
Concept
Camerawerk Munich designed and built as many components as possible itself, especially the shutters and lenses. Zuse-computers were used to calculate the latter. Because the profits of the supplier companies were saved, it was possible to produce reliably working devices at low cost. It was also possible to offer electronic exposure control early on.
In complete contrast to the innovations in design and exposure control, Agfa placed little value on adequate optical equipment and limited itself to the three-lens lenses Agnar and Apotar. For a long time it was assumed that buyers only needed pictures up to postcard size anyway and were therefore more likely to pay for eye-catching improvements such as a built-in exposure meter.
The advent of Japanese cameras with their four, sometimes even five, standard f/2.8 lenses was countered only late with the Solinar, which had four lenses. Even then, there were clearly visible savings from inferior coatings and omitted blackening of the ground lens edges inside the lens.
End of camera production
In the course of the 1970s it became increasingly difficult to produce in Germany at a reasonable price, so that hardly any cameras designed from scratch appeared. The Family System also brought in large losses.
In 1982, CEO Andre Leysen wanted to close Camerawerk Munich. For cost reasons and because of a loss of around 226 million DM in 1981, the company’s own camera production in Munich, Rottenburg an der Laaber and Coimbra was given up, but the device production continued because there were still good products in the product pipeline.
The new models of the Selectronic series were manufactured by Chinon. Bayer AG took over 100 percent of the group in 1981. In 1983 the company achieved global sales of DM 5.9 billion (EUR 3.0 billion) and pre-tax profits of DM 291 million (EUR 149 million). Agfa gave up camera production in 1983; all later Agfa film cameras were OEM products.
Around 3,800 employees were affected, 3,200 of them in Munich. The tools of the last Optima with a folding flash ended up in Qingdao, China, in order to continue producing the Optima there in a slightly modified form as “Qingdao-6” with the Solitar lens for a while.
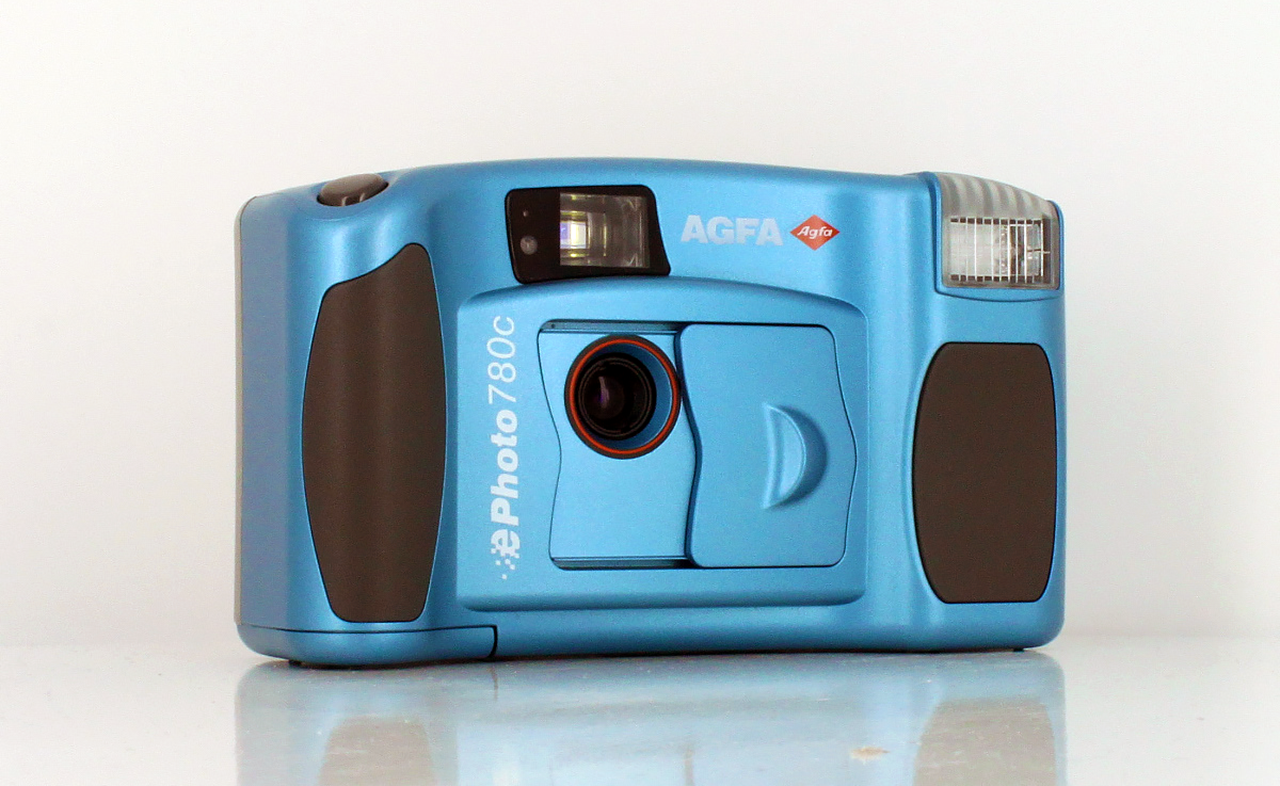
The ePhoto 780 is a digital camera made in Taiwan for Agfa, introduced c.1998. A variant in blue color, the ePhoto 780c, was released a year later in 1999
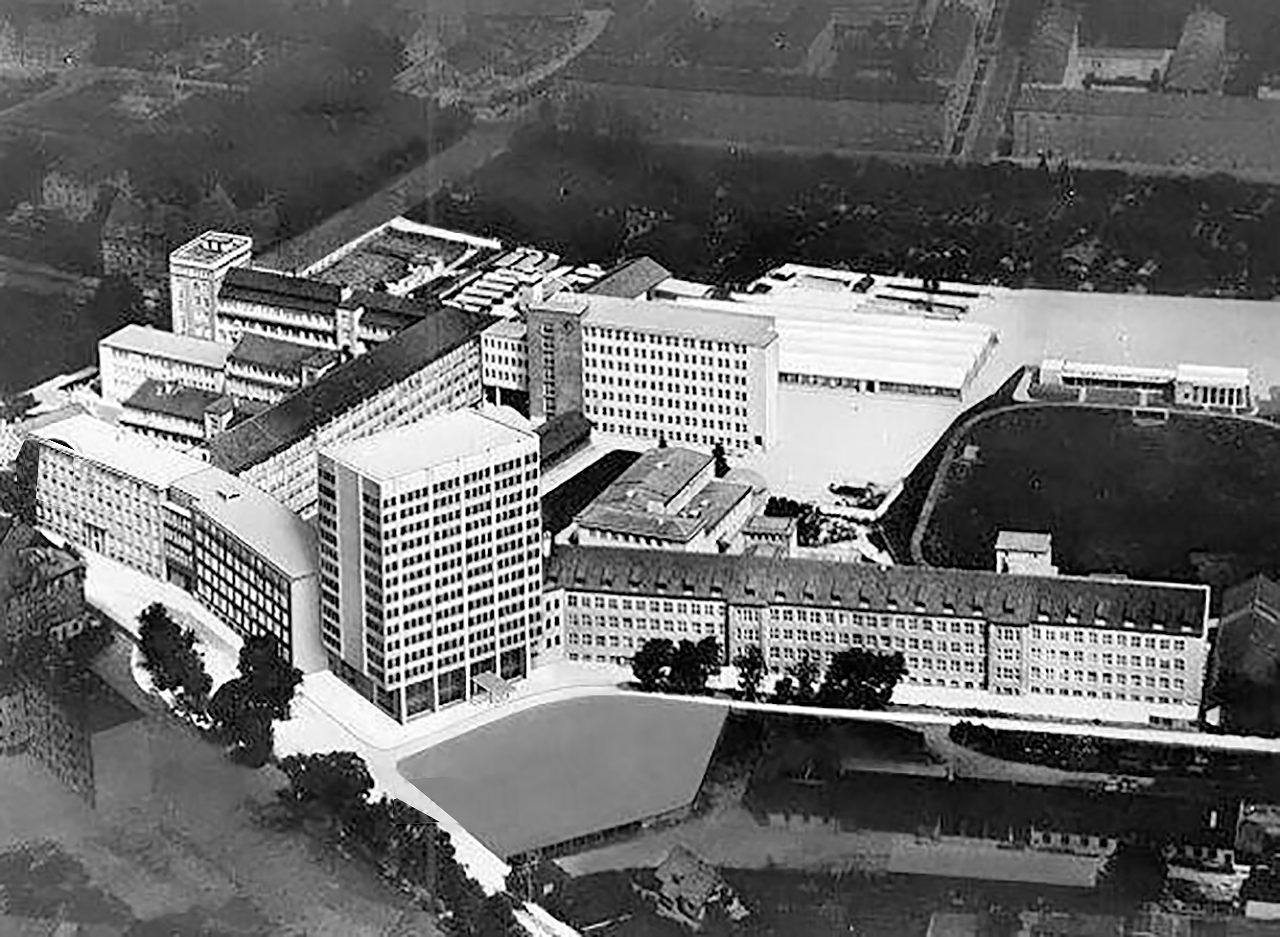
Camerawerk in Munich-Giesing on Tegernseer Landstrasse, 1962
Agfa goes digital
In the mid to late 1990’s Agfa sold low end compact digital photography cameras under the AgfaePhoto name, while their desktop scanners were called Agfascan. In 1997, it had acquired Dupont’s printing and graphic arts film business. In 2001, they stopped production and ended support for both their consumer scanners and digital cameras.
In 1999, Bayer AG took the company public; since then, Agfa-Gevaert AG, Leverkusen, has been a subsidiary of Agfa-Gevaert N.V., Mortsel/Antwerp (Belgium); Major shareholders are Bayer AG (30%) and Gevaert N.V. (25%).
In 2004, consumer film production ended. A management buy out of the consumer imaging division was made to form the company named AgfaPhoto, soon after AgfaPhoto files for bankruptcy. Some of the factories and machinery from Leverkusen were sold. AgfaPhoto is now a holding company and licences branding to other manufactures.
The Agfa brand
The AgfaPhoto brand is licensed by German photographic company Plawa which sells a modest line of AgfaPhoto Sensor compact digital cameras. Lupus Imaging is another licence holder of the name AgfaPhoto, they produced the Vista line of 35mm colour film that are Made in EU, by Ferrania.
In about 2010, they have also distributed APX black and white films in 100 and 400 ISO in 35mm format that was from older master rolls. These were also used by Maco as Rollei Retro 100.
By August 2013 the older rolls were used up and they began marketing a new version of the film now with a “New Emulsion” badging and marked Made in EU.
Currently (2012), Agfa-Gevaert (Belgium) is still producing industrial film for the medical, semiconductor and graphic press industry. A couple of companies like Maco using the Rollei brand and Fotoimpex using the Adox brand continued production on some of the film and paper products.
In Japan, Powershovel has licensed the AgfaPhoto brand for Vista print and CT Precisa slide film. The films are sold and manufactured in Japan.
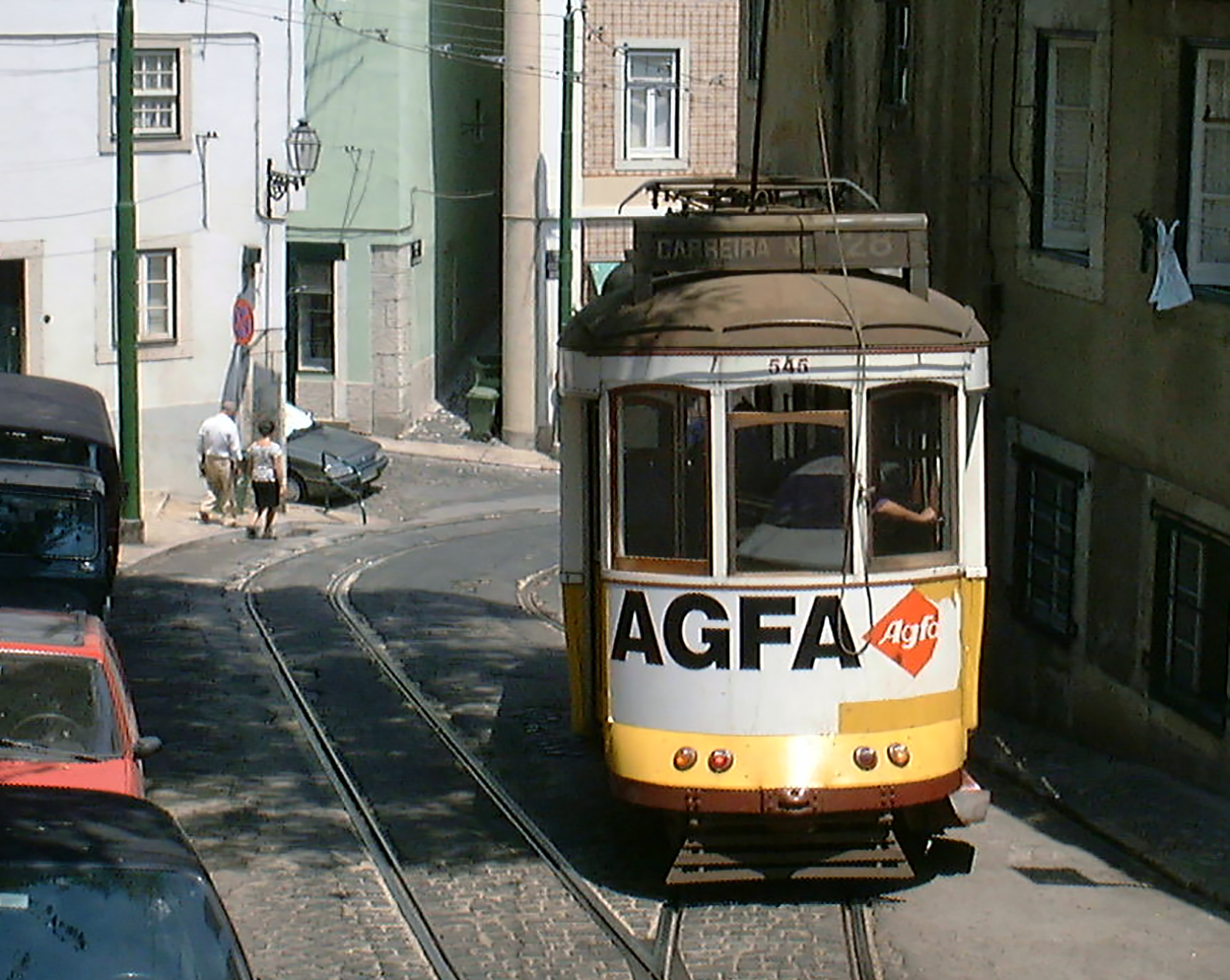
Lisbon Tram with Agfa advertising
Cameras: their origins and the production program
The origins of Agfa Camerawerk lie in the Optical Institute Alexander Heinrich Rietzschel founded in 1896. Rietzschel was born in Dresden in 1860 and completed an apprenticeship as a precision mechanic and optician at Carl Zeiss in Jena before moving to Munich in 1886.
There he first worked for the lens manufacturer CA Steinheil & Söhne, then for Rodenstock GmbH. In 1896 he finally founded his own optical business at Gabelsbergerstraße 36/37. The success of this venture was primarily based on the Linear 4.5 lens, for which Rietzschel received a patent in 1898.
A camera followed with the Clack 1900, whereby the company was renamed Alexander Heinrich Rietzschel GmbH, Fabrik Photographic Apparatus and Lenses and the company’s headquarters were at Schillerstraße 28. Camera production went so well that after one year the number of employees was 100.
A patent for all-metal camera housings from 1905 then brought even more success. Rietzschel cameras were hardly recognizable, they didn’t have a name tag, only the labeling of the lens indicated the manufacturer.
At the beginning of the First World War, around 200 employees worked at Rietzschel, but they could not be retained because no armaments were manufactured. In 1919, things continued with 100 employees, but it was difficult to finance the company. The company founder then looked around for a partner, which was heard about in the Munich sales office of Bayer AG and reported to the head office.
Bayer took over an 80% stake on March 1, 1921, but the existing product range and the Rietzschel name were retained, since the management had enough to do with guiding Bayer safely through the period of great inflation.
Bruno Uhl, a 26-year-old businessman who previously worked in the photography department at Bayer in Leverkusen, represented Bayer’s interested parties. He was able to increase annual production from 3,700 to 6,500 cameras, mainly thanks to increased exports. In 1924, Bayer increased its stake to 100% and appointed Bruno Uhl as director.
With the founding of I.G. Farben AG on December 10, 1925, all photographic activities came to Agfa, including the optical institute, which was renamed Agfa Camerawerk Munich, the cameras now of course wore the Agfa rhombus, only the lenses were still called Rietzschel for a while. Bruno Uhl went to Berlin as head of the “Photo Sales Germany” department, where he was responsible for sensational advertising campaigns. He was followed by Oskar Becker, who had previously worked as an operations manager in Berlin. Alexander Heinrich Rietzschel retired at the age of 66.
The camera market
Agfa sold 20% of all cameras on the German market. The biggest competitor was Kodak; This film manufacturer had also bought a camera manufacturer, the August Nagel camera factory.
There was also Zeiss Ikon with 15%. All other manufacturers had a significantly smaller share, they mostly served niche markets and sometimes only achieved a 1% market share.
Camerawerk Munich offered cameras in all price ranges, but the focus was on entry-level cameras. This set the course that the Camerawerk followed until it was closed. The films from Wolfen, papers from Leverkusen and photo equipment from Munich led to the slogan … everything from a single source! This principle was maintained until the Camerawerk was closed.
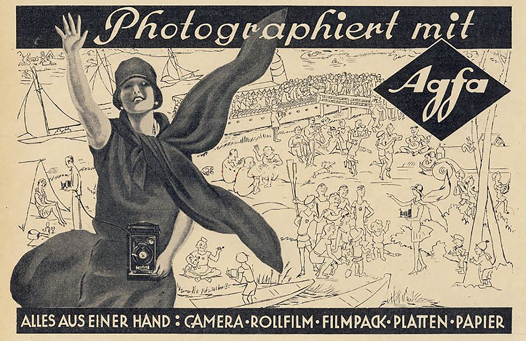
The production facilities
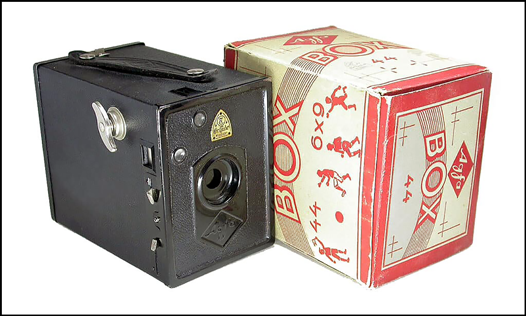
The legendary Agfa Box 44 (“Price box black for 4 Reichsmark”), built in 1932, with original packaging and operating instructions.
From 1927, cameras for the 6 cm × 9 cm format were manufactured on the new premises on Tegernseer Landstraße in Munich, followed a year later by film cameras and projectors for 16 mm small film, and then slide projectors, which were called “still projectors”.
In 1930 the first Agfa Box camera for 6×9 cm exposures on roll film was produced. In the following year it popularized photography in Germany by dumping the Box 44 for 4 Reichsmark, easily recouping its losses afterwards by selling Agfa 120 roll films.
The cameras now wore the Agfa rhombus, only the lenses were still called Rietzschel for a while. In 1935 the production of 16 mm sound film projectors began. At the same time, the manufacture of darkroom devices, enlargers and copiers for photographic laboratories developed. In 1937 the first 8 mm film camera followed as well as its first camera for 35mm film.
The export market
The I.G. Farben expanded its export business like no other German company in the 1930s, and AGFA was no exception. Attempts were made to reduce the dominance of US manufacturers in Asia and otherwise delivered mainly to the United States.
In 1928 the US division of Agfa entered a merger with Ansco Photo Products Inc., a company founded in New York in 1842, and over the following 15 years many models from the two companies were sold under the joint name Agfa-Ansco.
In the US market, cheap cameras were no business as Kodak had already flooded the market. As a result, one could not adopt the concepts for the German market and had to live with high initial losses. Since Agfa-Ansco officially acted largely on its own, there were no problems with government regulations.
In 1941, Agfa-Ansco was sold to General Aniline and Film Corporation (GAF), a company formed through a 1939 merger, which began its own film production afterwards.
Agfa introduced its modern colour negative still photography film and paper in 1942 as base of the Agfacolor films and papers that became competitors for Kodacolor after the war. After the war cooperation with Ansco was revived, but only on the camera sector.
- Isolar and Isolar Luxus (6.5×9 and 9×12 cm)
- Ninon (6.5×9 horizontal)
- Opal Luxus
- Agfa RPS 2024
- Standard (6.5×9 and 9×12 cm; also in sizes for roll-film – see below)
- Agfa Ansco View Cameras (field cameras in quarter-plate, 4×5, 5×7 and 8×10-inch sizes; strictly Ansco cameras)
cameras
- Superior (8×14 cm/3¼x5½ inch on 122 film; Agfa G6 size)
- Standard (6.5×11 cm on 116 film; also in sizes for plates and 120 film)
Folding cameras
- Automatic 66
- Billette
- Agfa Billy
- Agfa Billy-Clack
- Agfa Billy Compur
- Agfa Billy I
- Billy II
- Agfa Billy Jgetar 8.8
- Agfa Billy Record
- Agfa Billy Record II
- Isolette (or Jsorette, Jsolette)
- Isolette V
- Isolette I
- Isolette II
- Isolette III
- Isolette L
- Super Isolette
- Nitor
- Agfa Record I
- Agfa Record II
- Agfa Record III
- Standard (also made for 116 film, and for plates)
- Ventura 66
- Ventura 69 (Billy Record)
Rigid cameras
- Clack
- Click I
- Click II
- Isola
- Isoly various models, 4×4 images on 120
Box cameras
- Box B-2
- Trolix (also known as Box 14)
- Box 34
- Box 44
- Box 50 / Synchro Box
- Agfa Box I (model 54)
- Agfa Box-Spezial (model 64)
cameras
(Agfa/Ansco designations PB20 & PD16)
- Agfa PB 20
- Agfa PD 16 (folder)
- Agfa PD16 Clipper
- Agfa Billy 0 (Zero)
Folding cameras
- Karat
- Memo
- Solinette and Solinette II
- Super Solinette
viewfinder cameras
Fixed Lens
- Isoly 100
- Optima
- Optima Sensor 200 – 1969 series
- Optima Sensor 500 – 1969 series
- Optima Sensor Electronic – 1978 series
- Selecta
- Selecta m
- Selectronic Sensor
- Silette
- Agfa Registrierkamera
viewfinder cameras
Fixed Lens
- Parat I
- Paramat
- Optima-Parat
Rangefinder cameras
Fixed Lens
- Optima Sensor Electronic 1535
- Selectronic Sensor S
- Super Silette
Rangefinder cameras
Interchangeable Lens
- Ambi Silette
SLR-cameras
- Agfaflex I/II also known as Colorflex I/II
- Agfaflex IV
- Ambiflex also known as Agfaflex III/IV/V
- Selectaflex
- Selectronic – series
- Selectronic 3
TLR-cameras
- Flexilette
- Optima Reflex
cameras
- Iso-Rapid I
- Iso-Rapid IF
- Iso-Rapid Ic
- Iso-Rapid C
- Isoflash Rapid
- Isoflash-Rapid C
- Isomat Rapid
- Isomat Rapid C
- Moto-Rapid C
- Optima Rapid 250
- Silette Rapid I
- Silette Rapid F
- Silette Rapid L
- Optima Rapid 100C
- Optima Rapid 125C
- Optima Rapid 150
- Optima Rapid 250V
- Optima Rapid 500V
cameras
- Iso-Pak
- Iso-Pak C
- Iso-Pak Ci
- Autostar
- Autostar X-126
- Agfamatic
- Agfamatic X-126
- Agfamatic 126
- Agfamatic 50
- Agfamatic 50S
- Agfamatic 55C
- Agfamatic 100
- Agfamatic 108
- Agfamatic 200
- Agfamatic 208
- Agfamatic 300
cameras
- 1000/2000/… accepted magicubes.
- 508/1008/… accepted flipflash.
- The sophisticated models had a hot shoe for the Agfamatic Lux flash
- Agfa Mini
- Agfamatic 508 pocket sensor
- Agfamatic 1000 pocket sensor
- Agfamatic 1000S pocket sensor
- Agfamatic 2000 pocket sensor
- Agfamatic 3000 pocket sensor
- Agfamatic 3000 Flash Pocket
- Agfamatic 4000 pocket sensor
- Agfamatic 1008 tele pocket sensor
- Agfamatic 2008 pocket sensor
- Agfamatic 2008 tele pocket sensor
- Agfamatic 3008 pocket sensor
- Agfamatic 4008 pocket sensor
- Agfamatic 5008 makro pocket sensor
- Agfamatic 6008 makro pocket sensor
- Optima 5000 pocket sensor
- Optima 6000 pocket sensor
- Agfa Easy
- Autostar pocket
- Agfamatic 901 motor
- Agfamatic 901E motor
- Agfamatic 901S motor
- Agfa Tramp
- Agfa Traveller
- Snapper
cameras
- Agfa Futura
- Agfa Futura Af zoom
- Agfa Futura FF
- ActionCam (1995)
- StudioCam (1995)
- ePhoto 1280 (1997 0.7 megapixel)
- ePhoto 1680 (1998 1.2 mp)
- ePhoto 307 (1997)
- ePhoto 780
- ePhoto 780c
- ePhoto CL18 (2000, 0.3 mp)
- ePhoto CL20
- ePhoto CL30 (1999, 0.9 mp)
- ePhoto CL30 Clik! (1999, 0.9 mp)
- ePhoto CL34 (2001, 1.3 MP, Zoran Coach processor)
- ePhoto CL45 (2001; 0.7 mp)
- ePhoto CL50 (1999 1.2 mp)
- ePhoto Smile (0.3 mp)
Films
Black & white films can be recognized by a grey coded packing.
- Agfa PD16
- Agfa Vario-XL (C-41 chromogenic film)
- Agfacontour Professional film
- Agfaortho
- Agfapan 400[1]
- Agfapan AP (100, 400 ASA)
- Agfapan APX (25, 100, 400 ASA, now Rollei Retro 100, 400)
- Aviphot Pan (now: Rollei Retro 80S)
- Dia-Direct (reversal film)
- Isopan F8 [2]
- Isopan F17 [3]
- Isopan F – Portrait film
- Isopan Fine Grain
- Isopan IF
- Isopan Super Special
- Isopan ISS (Super Special)
- Isopan Record
- Isopan Super Special
- Isopan Ultra
- Scala (reversal film) (200 ASA)
- Superpan Press [4]
- Superpan Supreme
- Ultra-Speed
Films
Negative films can usually be recognized by a red or (earlier) yellow coded packing.
- Agfacolor CNS
- Agfa Futura II APS (100 ASA)
- Agfacolor Optima (100, 125, 200, 400 ASA)
- Agfa Portrait (160 ASA)
- Agfa APS Star (200, 400 ASA)
- Agfa APS Tura
- Agfa Ultra (50 [5], 100 ASA; now: Agfa Aviphot X400, Rollei Digibase CN 200 Pro)
- Agfa Vista (100, [6] 200,[7] 400, 800 ASA; now: Agfa Aviphot N800, Rollei RCN640)
- Agfacolor CN17 [8]
- Agfacolor HDC (100, 200, 400)
- Agfacolor Negative
- Agfacolor Pocket Special
- Agfacolor Portrait XPS (160)
- Agfacolor XR (100, 200, 400)
- Agfacolor XRC (100, 200, 400)
- Agfacolor XRG (100, 200)
- Agfacolor XRS (100, 200, 400, 1000)
(Slide) Films
Colour reversal films can usually be recognized by a blue coded packing.
- Agfacolor Neu (1936)
- Agfachrome CT 18
- Agfachrome CT 100
- Agfa CT Precisa (100, 200 ASA)
- Agfa Isochrom
- Agfachrome 50 S / 50 L
- Agfachrome 64
- Agfachrome 50 RS (1989)
- Agfachrome 100 RS (1989)
- Agfachrome 200 RS (1989)
- Agfachrome 1000 RS (1989)
- Agfachrome RSX
- Agfachrome RSX II (50, 100, 200 ASA; now: Agfa Aviphot Chrome 200, Rollei Digibase CR 200 Pro)
- Plenachrome (for Memox)
- Super Plenachrome
- Rodinal
- Eikonogen
- Amidol
- Diogen
- Diphenal
- Viradon
- Agfatronic electronic flash units
- Agfa flashbulb units
- Agfa flash lamp
- Light meters
Including, roughly in chronological order:
- Agfa Opticus 100
- Agfa Agfacolor 50 automatic
- Agfa Diamator series, like models H, m, 1500
Agfa produced many image scanners in the Arcus, DuoScan, SnapScan, StudioScan and StudioStar ranges. While they have all been discontinued and up-to-date drivers for them are not available from Agfa, Vuescan software supports many Agfa scanners on current computer operating systems.
- Agfa Varioscop enlargers
- Agfa Variomat print easels for automatic exposure
- Darkroom safety lights
- Agfa Rondinax and Rondix daylight developing tanks
Agfa papers
Agfa photographic papers were of very high quality; lines included:
- Brovira
- Portriga Rapid
- Lupex
The production of material identical to the last generation of fibre-based and resin-coated photographic Agfa Multigrade papers has been resumed by Adox.
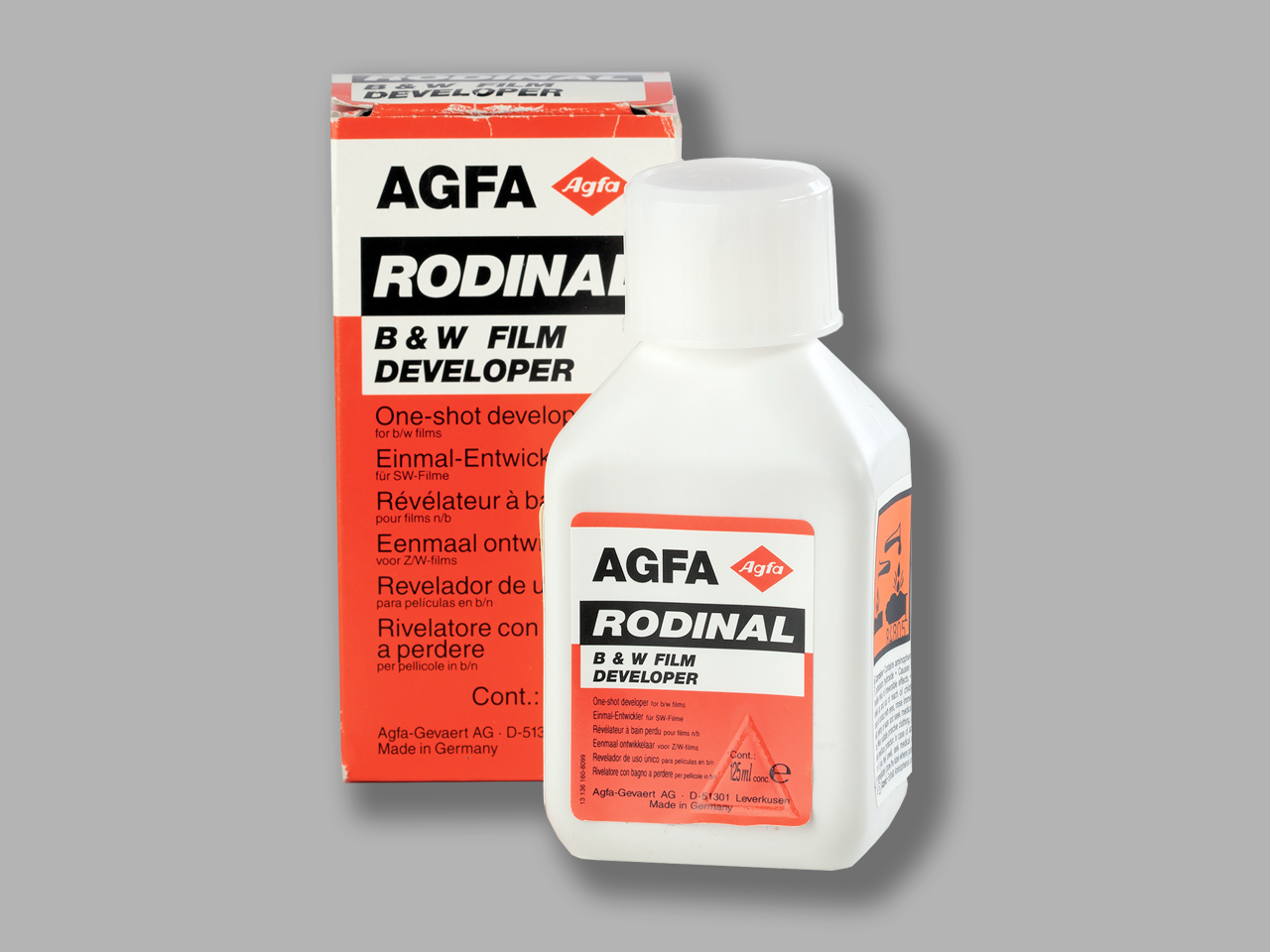
Agfa Rodinal film developer
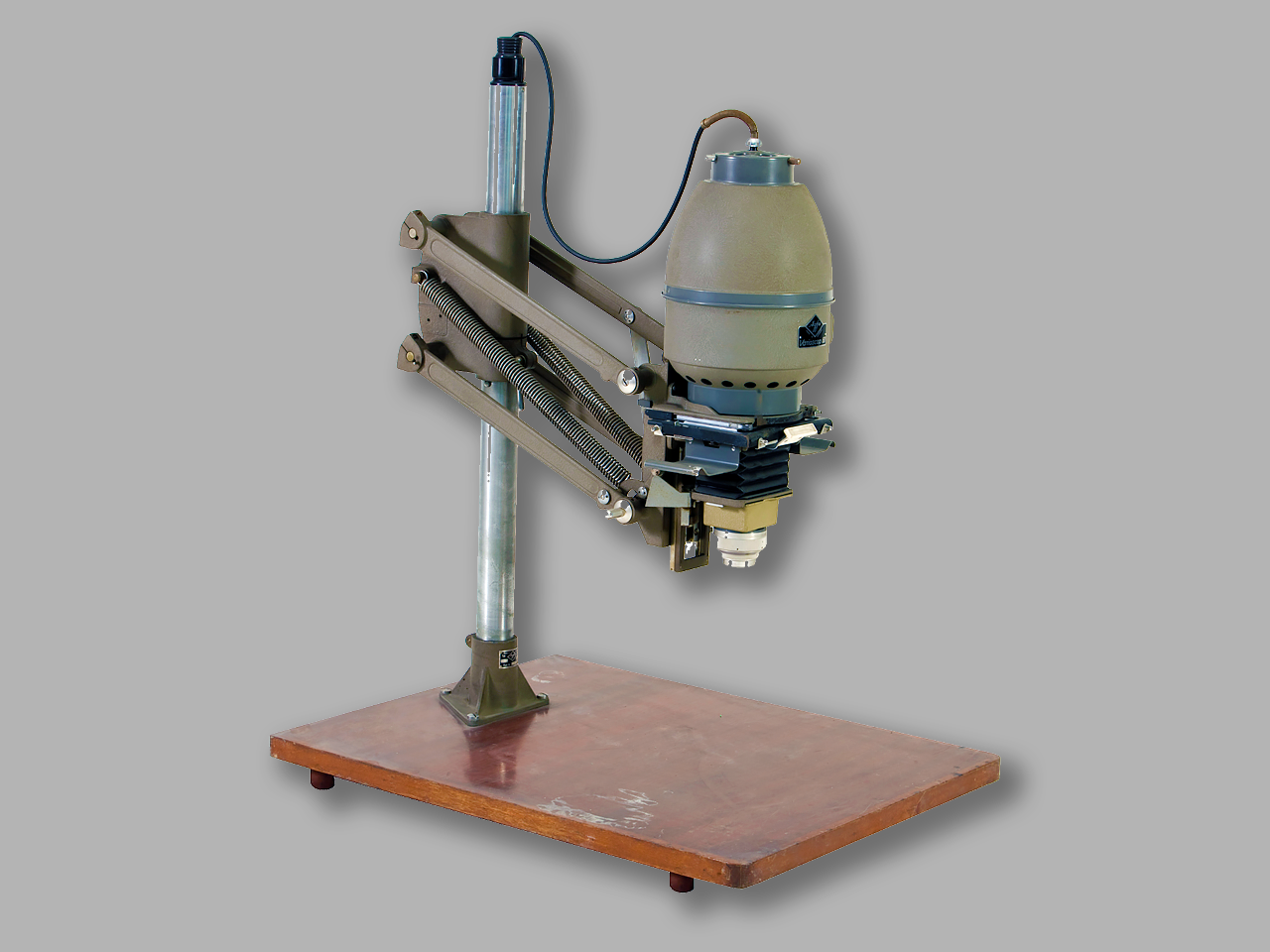
Agfa Variscop enlarger
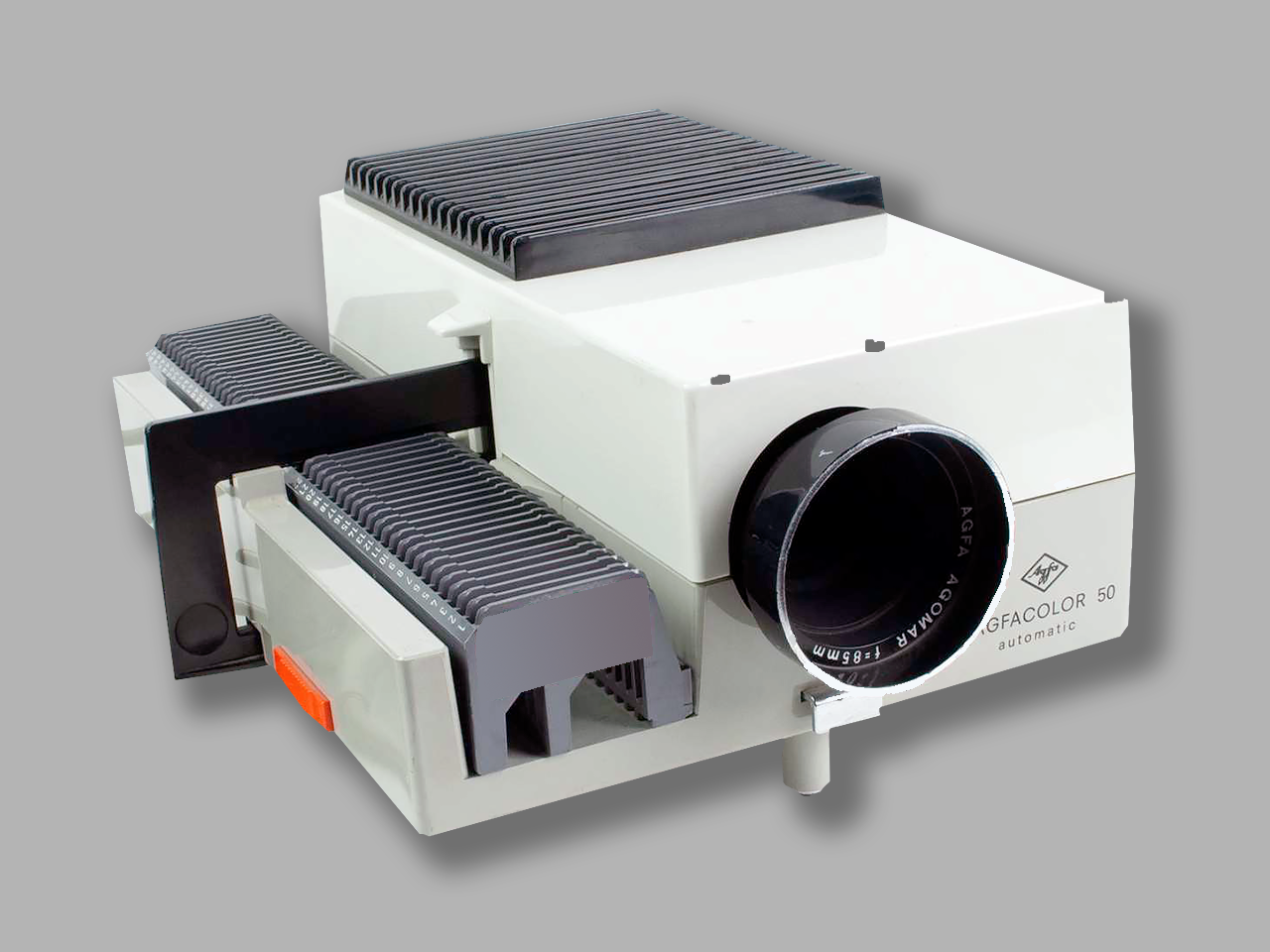
Agfacolor 50 automatic slide projector
FOUNDER: Richard Knoll
COMPANY NAMES:
1892: Photo Spezialhaus; 1904: Photographische Manufaktur Richard Knoll; 1927: it was taken over by Emil Hofert and later continued by Berthold Altmann; 1927: The company was renamed “Fabrik Photographic Articles Emil Hofert formerly Ing. Richard Knoll”; 1931: EHO-Kamerafabrik GmbH; 1935: “Eho” Kamera-Fabrik Emil Hofert GmbH, Inhaber Berthold Altmann; 1940: AMCA-Camera-Werk Berthold Altmann; 1941: Altissa Camera Werk Berthold Altmann; 1946: ALDO-Feingeräte-Bau GmbH; 1952: VEB Altissa Camera Werk; 1959: part of VEB Kamera- und Kinowerke Dresden; 1961: production of its cameras was ceased – Delivery of tools and individual parts to Yugoslavia > Licensed production of the “Yugo” Altix IV in Sarajevo.
COMPANY ADDRESSES:
1892: Leipzig; 1918: Augsburger Strasse 54 EG, Dresden; 1927: Eilenburger Strasse 6, Dresden; 1928: Augsburger Strasse 28, Dresden; 1936: Lortzingstraße 38, Dresden; 1947: Blasewitzer Strasse 17, Dresden.
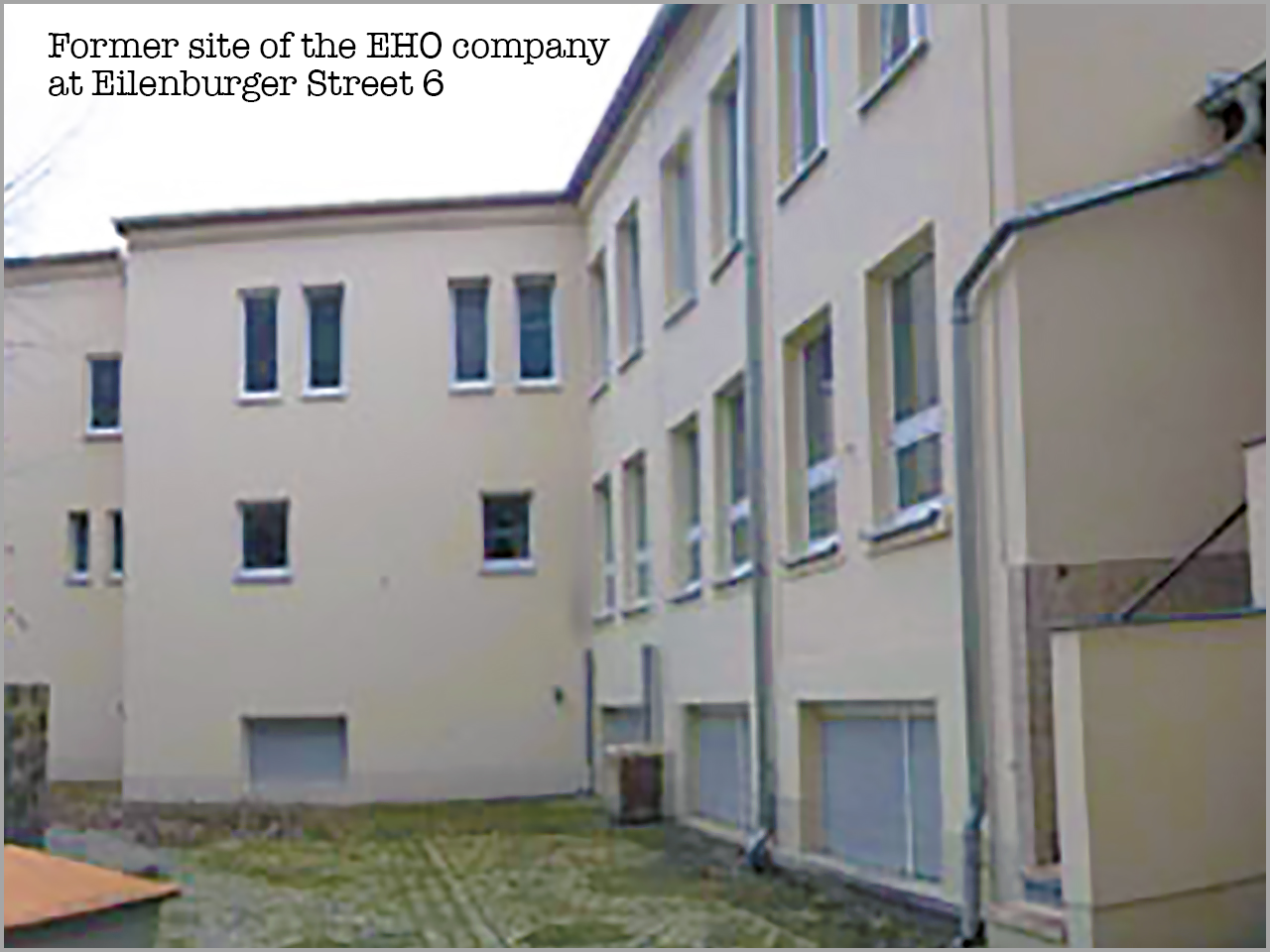
It all started with Richard Knoll. He was a merchant and founded his photo company as Richard Knoll’s “Photo Spezialhaus” in Leipzig in 1892. There is very little information online about what this company did for it’s first couple decades of existence. Almost every resource online recites the same story over, and over, and over. Since 1904 it started repairing and manufacturing cameras and photographic supply. He gave it the name “Photographische Manufaktur Richard Knoll” and retired after a year in 1905.
The important facts are that in 1910, the company relocated to Dresden, Germany, and then the company was taken over by Emil Hofert. Emil Hofert was actually the owner of a cigarette shop in Dresden and he also worked in his small mechanical workshop, not far from the large camera works in Dresden. He was so fascinated by the box camera that he took over Knoll’s company in 1926 in order to manufacture simple EHO-Box cameras himself.
The very next year, in 1927, the company was renamed “Fabrik Photographic Articles Emil Hofert formerly Ing. Richard Knoll”. The company headquarters is now a back building at Eilenburger Strasse 6; From now on, the construction of simple box cameras began increasingly.
From 1931 the company name became “Eho” Kamera-Fabrik GmbH, with “Eho” being a condensed version of the name Emil Hofert. The company has 30 employees and successfully produces simple box cameras.
In the following years, “EHO” boxes were sold both “unnamed” and under the following names: Adina (Kaufhof), AKO, Arto, Beier (Freital), Errtee (Errtee was a trademark/brand name of the Romain Talbot wholesaler in Berlin), Fotam, Fotka (Czech for ‘snapshot’), Hamaphot (Dresden), Hermax, Mantel, Mono (Magdeburg), Nebo, Rhaco (Frankfurt), RECORD, Rilo, Staufen and Wara (Frankfurt). As early as 1932, an Eho stereo box camera was part of the production program.
At the beginning of the 1930s, the mechanic Karl Heinrich Altmann joined the company and worked as a design mechanic. He broke new ground and designed a new generation of compact box cameras, which were produced for almost 20 years.
The first appearance of the name “Altissa” was around 1934 with the release of the Altissa Box No. 200. It was a compact all metal box camera with a straight through viewfinder unlike the reflex finders on most box cameras, and it shot 6 x 6 cm images on 120 film. It had a Rodenstock Altissar Periskop f/8 lens and a single shutter speed. The Altissa 200 proved to be very popular and launched several variants, including one that shot 6 x 4.5 cm images. Around 1938 it was renamed the Altissa Model A, but remained mostly unchanged. The Altissa 200 is also manufactured for special dealers under the names “JUWEL” and “FOTKA”.
The son Berthold of the mechanic Karl Heinrich Altmann completed commercial training in the “golden” 20s (including in England). The young Altmann, called Bobbi, was a very intelligent, diversely interested and fun-loving person. It was the time of coffeehouse music and big bands. Berthold played banjo and pianos in a Dresden music band.
Father Altmann’s influence in the company must have been very great at that time. So he brought Berthold into the company as managing director in October 1934, before Berthold took over the company in January 1935. The company name now takes place under the name “Eho”‘ Kamera-Fabrik Emil Hofert GmbH, owner Berthold Altmann.
In May 1936, Altmann acquired a new company site at Lortzingstrasse 38, which was then occupied by 60 employees. In addition to the boxes, its only twin-lens reflex camera Altiflex, and later the improved Altiflex II, was manufactured here from 1937. It is later also produced for special dealers under the names “Gehaflex”, “Hafaflex” and “Wirgin”. Unfortunately, Emil Hofert died in July 1936 at the age of 66, probably after a long, serious illness.
Possibly due to new leadership, the company set it’s sights on more advanced cameras than just simple box cameras, and several new designs were put into development including a Twin Lens Reflex called the Altiflex in 1937, and a compact 35mm camera called the Altix which was presented in 1939 on the Photo- and Kinemesse. It was a sophisticated 35 mm viewfinder camera for the 24 x 24 mm format with a fixed Laack Pololyt 3.5/3.5 cm lens. Later versions had a front lens mount that could be easily screwed out to allow for close-up focus shots. Even the simple Altissa box camera saw the release of a Super-Altissa model that came with a more advanced f/3.5 Altissar lens, and more advanced Prontor and Compur shutters.
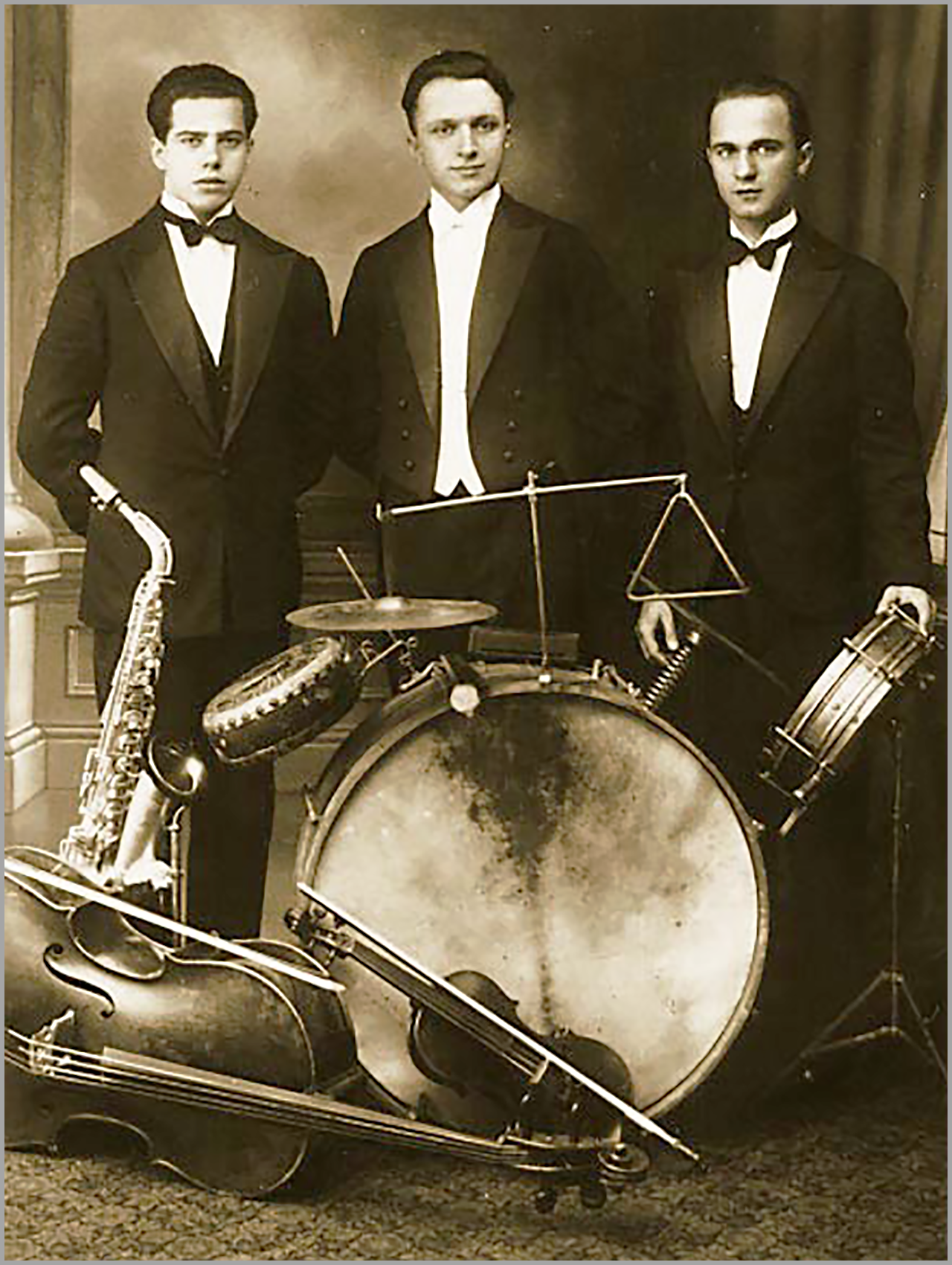
Bobbi Altmann played banjo and pianos in a Dresden music band.
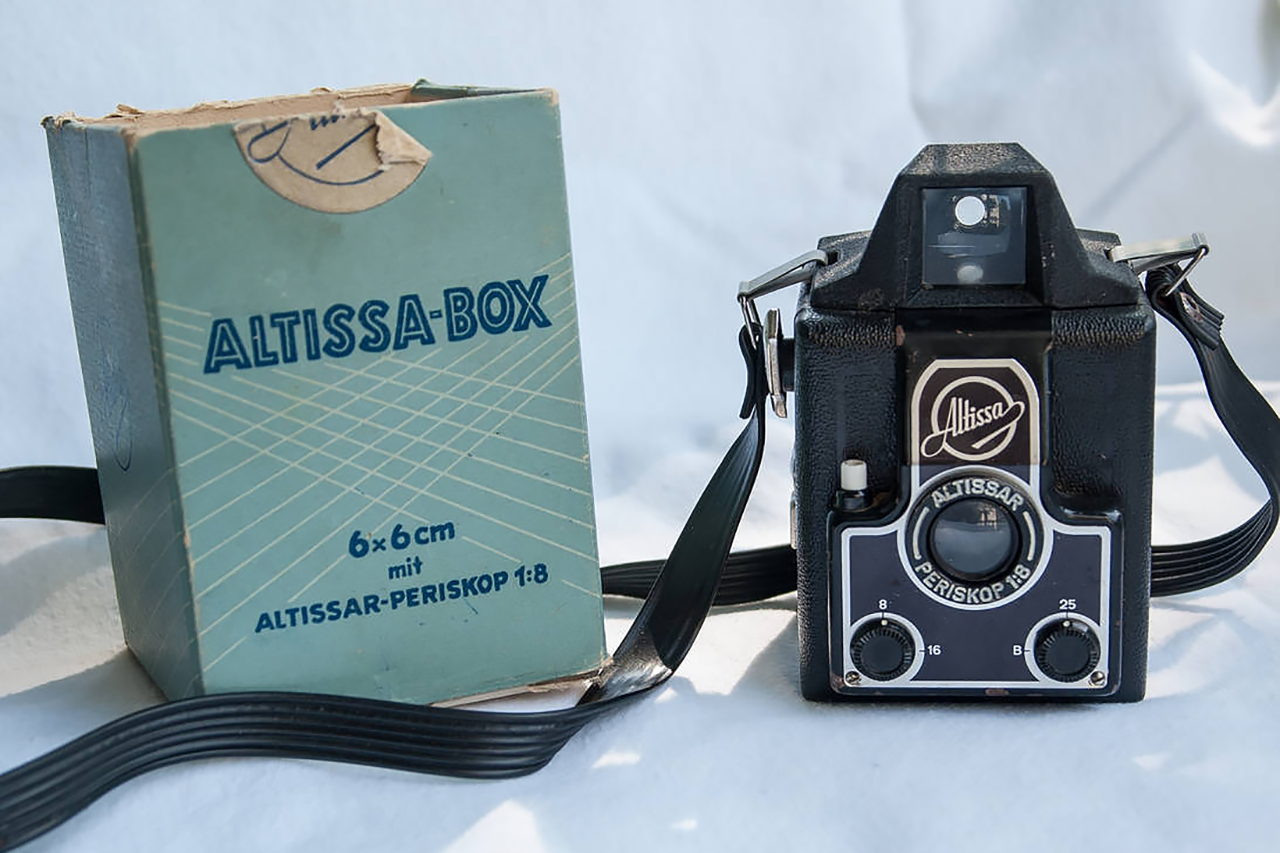
The famous “Pericopic” Altissa Box camera for 6×6 images on 120 film. Periscope comes from two Greek words, peri , meaning “around,” and scopus , “to look.” A periscope lets you look around walls, corners, or other obstacles.
Losing independence
While Altissa was able to continue making cameras, they likely had to obey certain restrictions and demands from the East German government. This proved to be a problem for Berthold Altmann, who in December 1950 fled East Germany with his girlfriend to West Germany, abandoning his company.
He was tried and found guilty of crimes under the Economic Penal Decree of 1948 and all of his assets, including Altissa were seized by the government and put under the jurisdiction of VVB Optik Jena. The company would in 1953 be renamed VEB Altissa Camera Werk, a name it would keep until 1959.
After his escape in December 1950, Berthold Altmann worked at the companies Ascania in Berlin, Isco Feinoptische Werke Osterrode, Wirgin in Wiesbaden, Monthanus in Solingen and Steinheil in Munich as a technical construction consultant. Shortly after his 68th birthday, Berthold Altmann died on March 15, 1975 in Frankfurt am Main after a serious illness. His grave is in Neuss.
The absentee sentence against Berthold Altmann was only overturned in 1992, 17 years after his death.
Like most German optics companies, World War II caused a lot of turmoil for the company. It seems that between 1940 and 1941, Eho would change it’s name two different times, once to “AMCA Camera Werk Berthold Altmann”, and then again to “Altissa Camera Werk Berthold Altmann”.
In February 1945, the bombing raids destroyed the company at Lortzingstrasse 38, and the tools for manufacturing the Altiflex were so badly damaged that this model could not be produced again later.
Already in May 1946, Berthold Altmann and Fritz von Dosky founded a second company, ALDO-Feingeräte-Bau GmbH (ALDO = Altmann & Dosky). The manufacturing program included ALDO-microscopes and ALDO-microscope cameras for the medical and technical sectors. In 1949 the ALDONAR-Kolibri, sometimes also called Mirror-Altix, was created in cooperation with Altissa.
Reconstruction of the Altissa Camera Plant began in 1947 at the new location at Blasewitzer Strasse 17. Progress was slow as the entire company had to be rebuilt from the ground up, including securing a new factory, equipment, and hiring employees. But, already in 1947, camera production would resume with a revised version of the original Altix with a new front plate and shutter assembly. This new camera would become known as the Altix II. Production of box cameras would also resume, including an all-new Altissa-Box. The Altix III with a new housing was built in 1949.
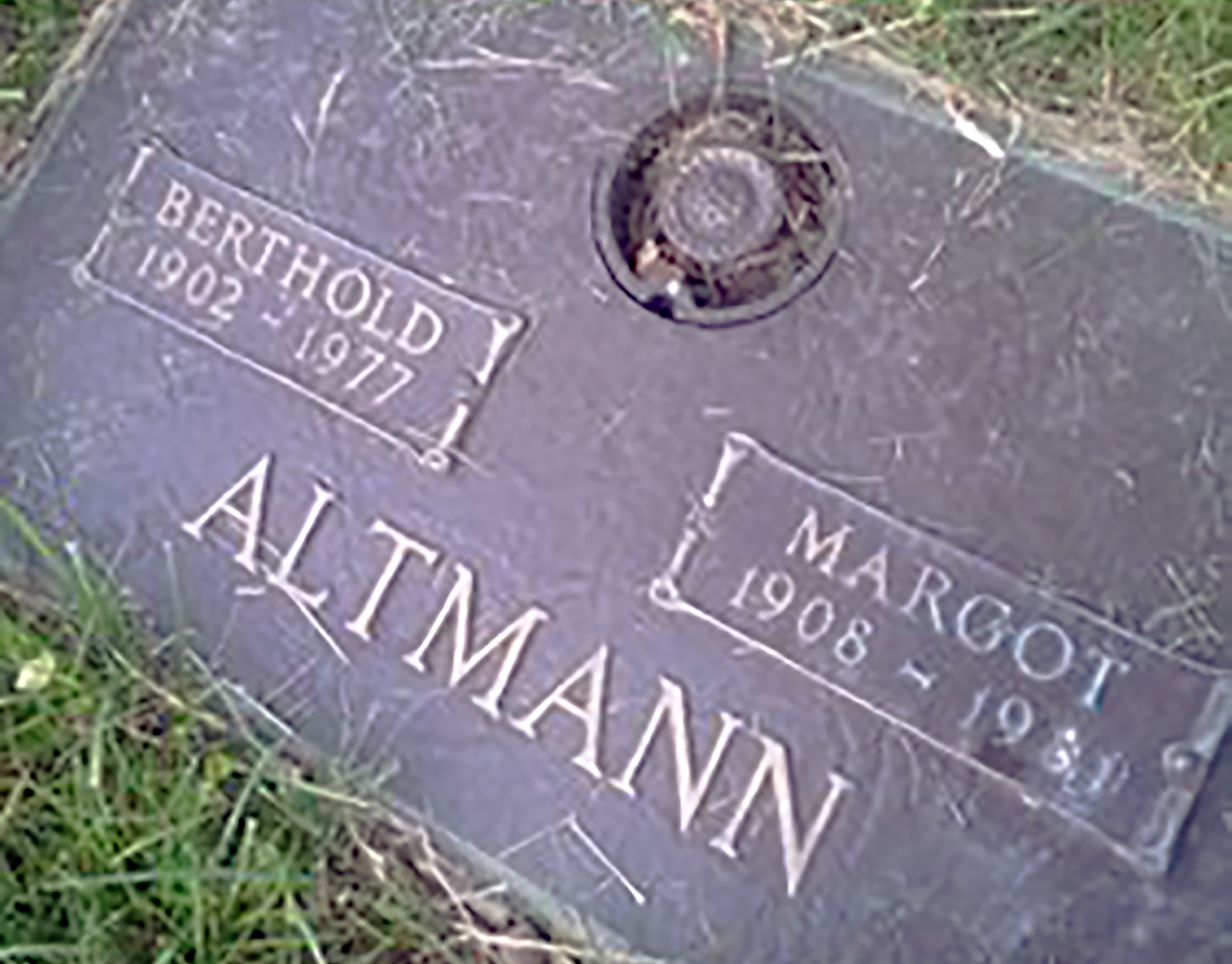
The grave of Berthold Altmann and his wife Margot in Neuss.

The new Altissa building at the Blasewitzer Street in 1947.
The final stage
VEB Altissa Camera Werk would continue to make several different Altix and Altissa cameras until 1959 when the company was merged into VEB Kinowerke Dresden, which was a conglomerate of several Dresden camera companies including Pentacon, Zeiss-Ikon, Reflekta, and several others. This ended the legal independence and the name Altissa was deleted.
All other Altissa cameras would be discontinued except for the Altix-n and nb models. These final two cameras would be produced at least until 1960, perhaps even 1961. In 1961 the production of its cameras was ceased and the buildings of the former Altissa were completely abandoned. After the final Altix models stopped production, the history of Altissa and all the various different versions of the company that preceded it would come to an end.
Despite this tumultuous time with the ownership of Altissa, the company did well. In 1950 it had 160 employees. The 35mm Altix and Altissa box cameras sold well. The Altix would continue to be refined, with the Altix III and IV released in 1950 and 1952 respectively, improving the ergonomics, shutter, and lenses of the camera. A variant of the Altix III called the Altix IIIA would abandon the original 24 x 24 mm frame size and switched to the international standard of 24 x 3mm.
The Altix IV (1952) would become Altissa’s best selling camera up until this point, staying in continuous production until 1959. For the first time an accessory shoe is available. It would be the first Altissa exported to western countries where it was sold there as the Classic 35. ZRAK Sarajevo would assemble later versions of the Altix IV in the former Yugoslavia.
In 1954, the Altix IV would be upgraded to have an interchangeable lens mount and would be called the Altix V. The Altix V’s mount was a proprietary breech lock mount that was unique to Altix cameras. Several high quality German lenses were available for the Altix designed by Zeiss and Meyer-Optik, which helped elevate the reputation of the Altix cameras to a much higher level than the earlier variants.
Finally, in 1957, the Altix would see it’s first major redesign, in a new model called the Altix-n. Featuring a squared off body with a flat top plate, the Altix-n had a much larger and brighter viewfinder, a lever wind, and a removable back for easier film loading compared to the bottom loading design of all previous models. The Altix-n used the same breech lock mount as the Altix V and was compatible with the same lenses.
There would also be an Altix-nb with an uncoupled selenium light meter. There are two variants of the Altix-nb with the exposure meter in different locations, both sold with the same name. The earlier versions had a top mounted meter that increased the overall height of the camera to accommodate the meter. Starting sometime in 1958, the Altix-nb’s meter moved to within the top plate of the camera making the top plate of the camera completely flat. At this same time, both the Altix-n and Altix-nb would receive another upgrade to the viewfinder adding projected frame lines for 50 and 90 mm lenses.
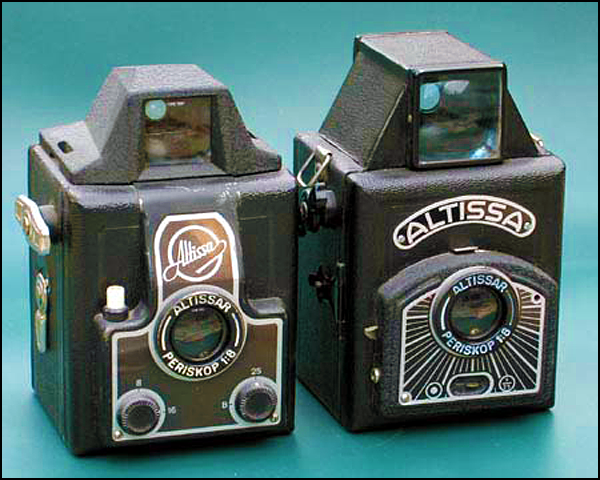
Altissa Box (left) and Altissa Box D are basically similar cameras. You can see the differences. The Altissa box D which is older (ca.1952) has a bigger viewfinder and because of the new design of the front part the shutter release knob of the newer model (ca.1954) is slightly easier to use.
Eho-Altissa Cameras and year of manufacture
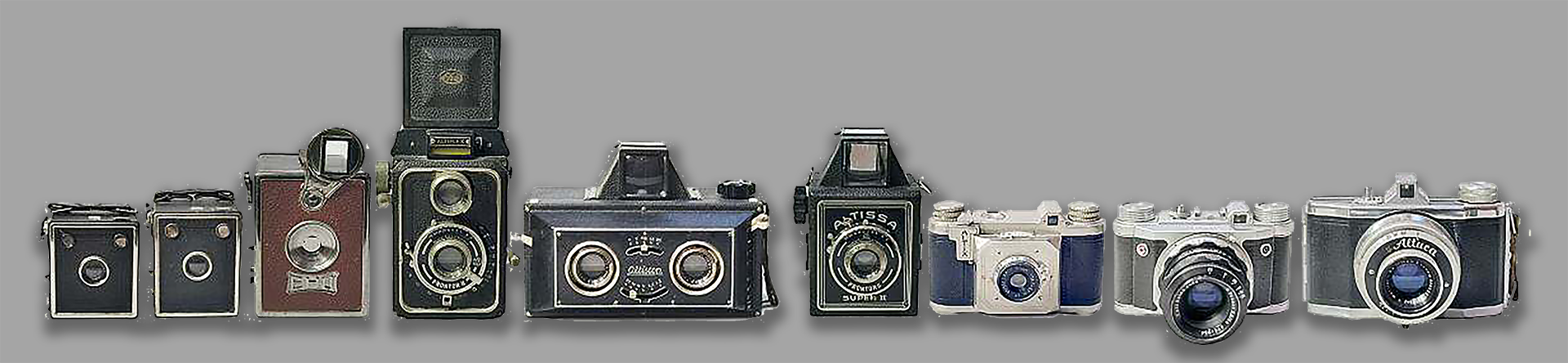
- Ako – c1937
- Altiflex – 1936-1937
- Altiflex II – 1936-1938
- Altiscop – 1936-1942
- Altissa – 1954-1957
- Altissa Box 200 – 1936-1938
- Altissa Box 210 – 1936-1938
- Altissa Box 240 – 1938-1939
- Altissa Brillant – 1939-1948
- Altissa D – 1951
- Altissa II – 1938-1939
- Altissa S – 1951
- Altix 1936 – 1940
- Altix I – 1947
- Altix II (black) – 1948
- Altix III – 1949-1953
- Altix III (24×36) – 1949
- Altix IV – 1952-1959
- Altix IV (export) – 1952-1955
- Altix IV (Sarajevo) – 1962
- Altix V (black) – c1954-1957
- Altix V (colored) – c1954-1957
- Altix-n (type I) – 1955-1957
- Altix-n (type II) – 1957-1958
- Altix-n (type III) – 1958-1959
- Altix-nb (1956) – c1956-1958
- Altix-nb (1958) – c1958-1959
- Altuca – c1949-1953
- Arto (black) – c1936
- Arto (green) – c1936
- Classic 35 – 1952-1955
- Eho Box (3×4, baby-box) – c1932-1939
- Eho Box (4.5×6) – 1931
- Eho Box (4×6.5) – c1934
- Eho Box (6.5×11) – c1930
- Eho Box (6×9) – c1930s
- Eho Stereobox – c1932
- Errtee (3×4) – 1932
- Errtee Box – c1930s
- Fotka – c1936
- Gehaflex – 1930s
- Hafaflex – 1930s
- Juwel – c1951
- Mantel Box 2 – c1935
- Record Box – c1938
- Rilo Box – c1945
- Staufen Box – c1933
- Super Altissa – c1938
- Super-Altix (prototype) – 1957
- Yugo Altix IV – 1961
- Adina (Kaufhof)
- AKO
- Arto
- Beier (Freital)
- Errtee (Errtee was a trademark/brand name of the Romain Talbot wholesaler in Berlin)
- Fotam
- Fotka (Czech for ‘snapshot’)
- Gehaflex
- Hafaflex
- Hamaphot (Dresden)
- Hermax
- Mantel
- Mono (Magdeburg)
- Nebo
- Rhaco (Frankfurt)
- RECORD
- Rilo
- Staufen
- Wara (Frankfurt)
- Wirgin
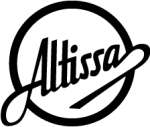
FOUNDER: Jaap van Beugen
COMPANY NAMES:
1929: Amaloco; 2008: Amaloco stopped production due to too high investment in environmental measures; 2009: original receipes and trademark rights go to Nordfoto Versand, Norderstedt, Germany.
COMPANY ADDRESSES:
1929: Nunspeetlaan 303, The Hague; 1948: Ferrandweg 12, The Hague; 1974: Industrial Area, Ommen; 2008: Amaloco stopped production due to too high investment in environmental measures; 2009: original receipes and trademark rights go to Nordfoto Versand, Norderstedt, Germany.
Amaloco was something like a dutch Tetenal. The only Dutch book on photochemicals had been written by the owner of Amaloco, Jaap van Beugen. Furthermore he wrote their Amaloco Doka-infokrant (info-newspaper). Last edition 2005/2006.
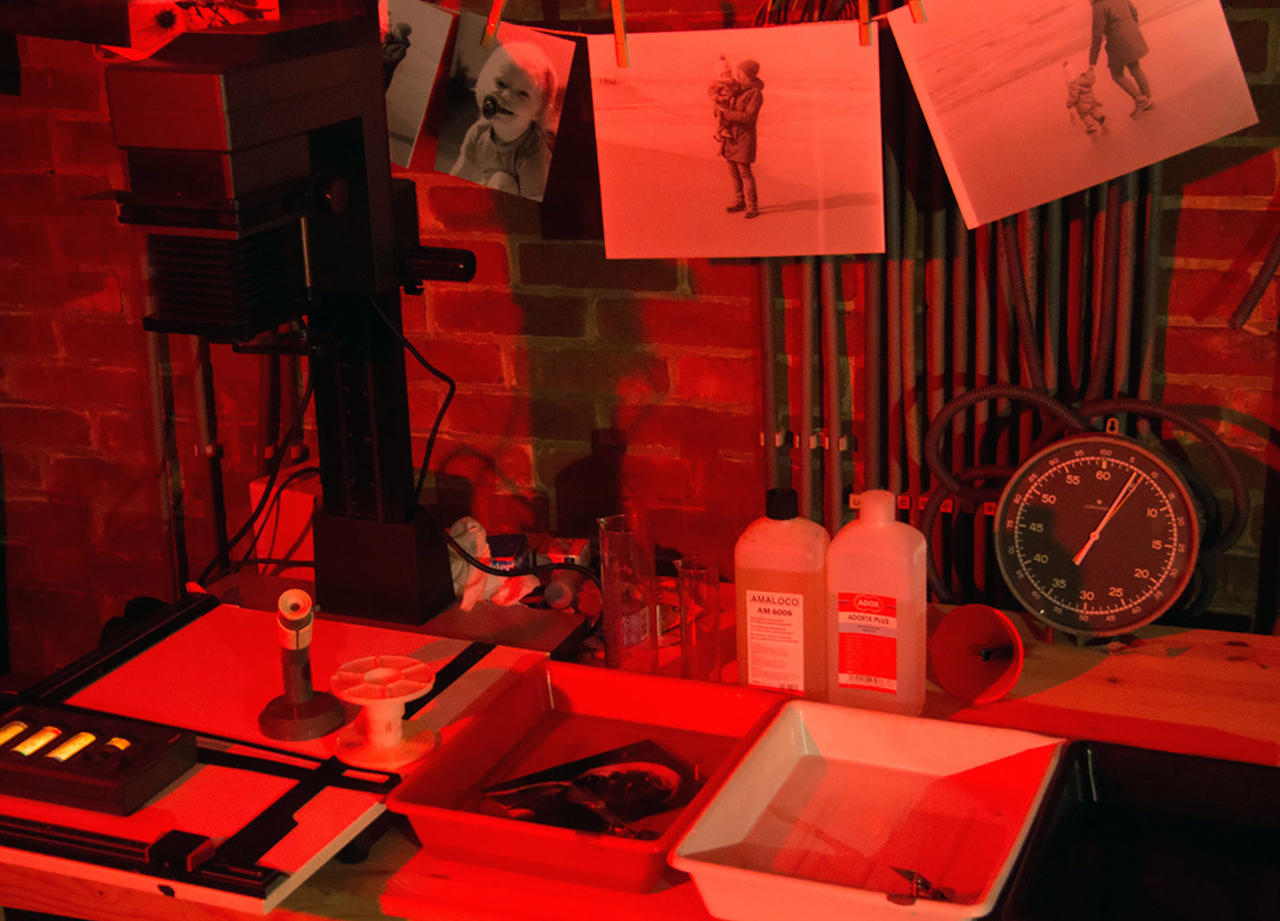
Amaloco’s working area: the darkroom of (often) the hobby photographer.
During his studies chemistry E. van Beugen already had his special interest in photochemistry in connection with his hobby photography. So, after finishing his study, he founded the first Dutch photographic chemical trading company Amaloco on April 1rst, 1929.
Initially, the company traded from his house in The Hague in photography books, fine balances for weighing chemicals, sensitive materials and photochemistry. Just to name a few: a bag with 25 grams of Metol, 100 grams of Hydroquinone, 1000 grams of sodium sulfite crystal and 25 gr. Potassium bromide, and so on, and so on.
In the mid-1930s, the company started at this address Nunspeetlaan 303, the production of, among others, S.W.S. This liquid product, based on Potassium Bromide and self-synthesized para-nitro Benzimidazole Nitrate, could be added by photo amateurs themselves to home-made developers. This led to considerably better and especially fog-free results of self-developed black&white negatives and black&white papers.
During the years of Worldwar II, the production of photochemicals was put on a hold. A switch was made to the production of (then) scarce, useful things such as soap and the like for the household. These products were often traded for food and wood or coal for the stove.
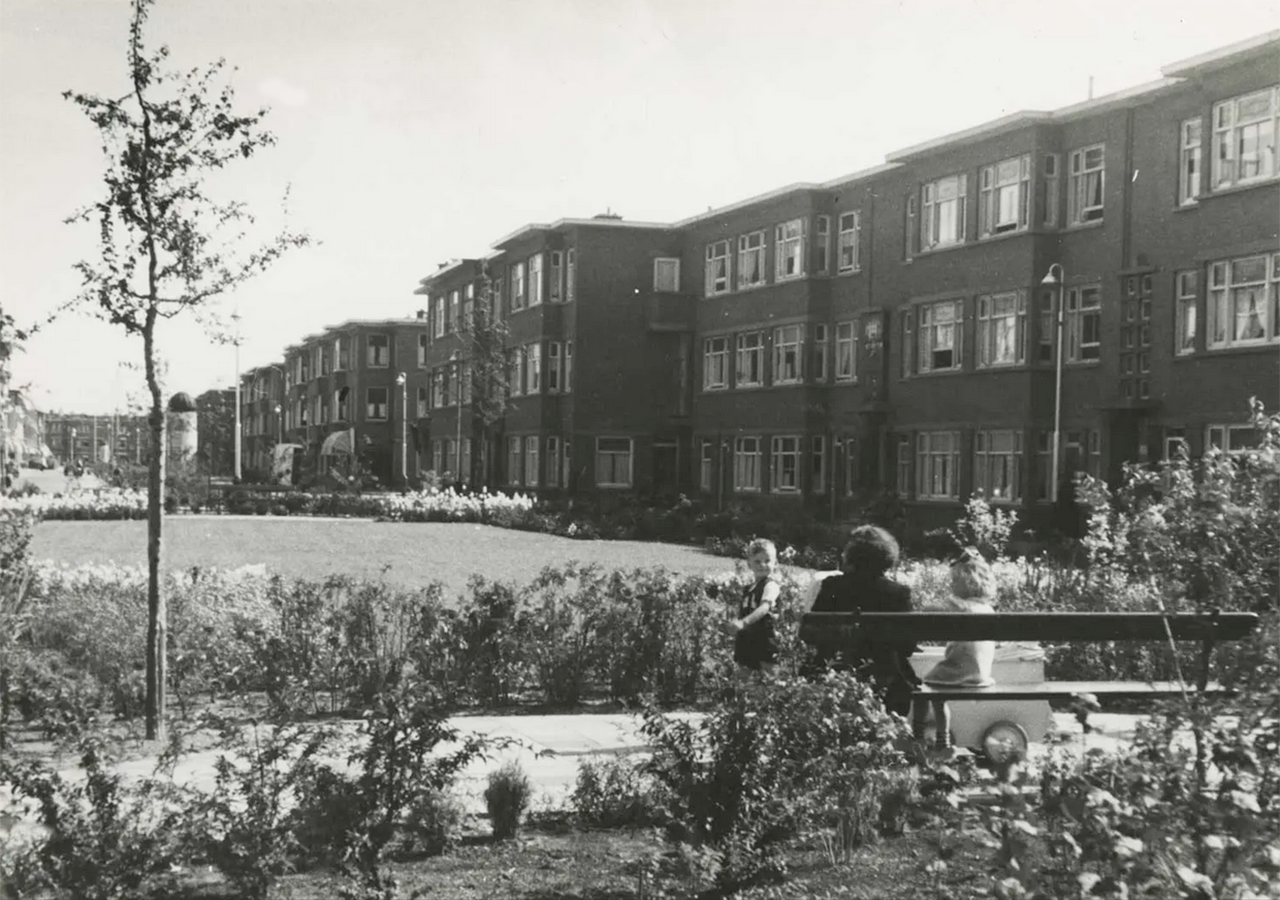
The company started out at Nunspeetlaan 303, ca. 1935.
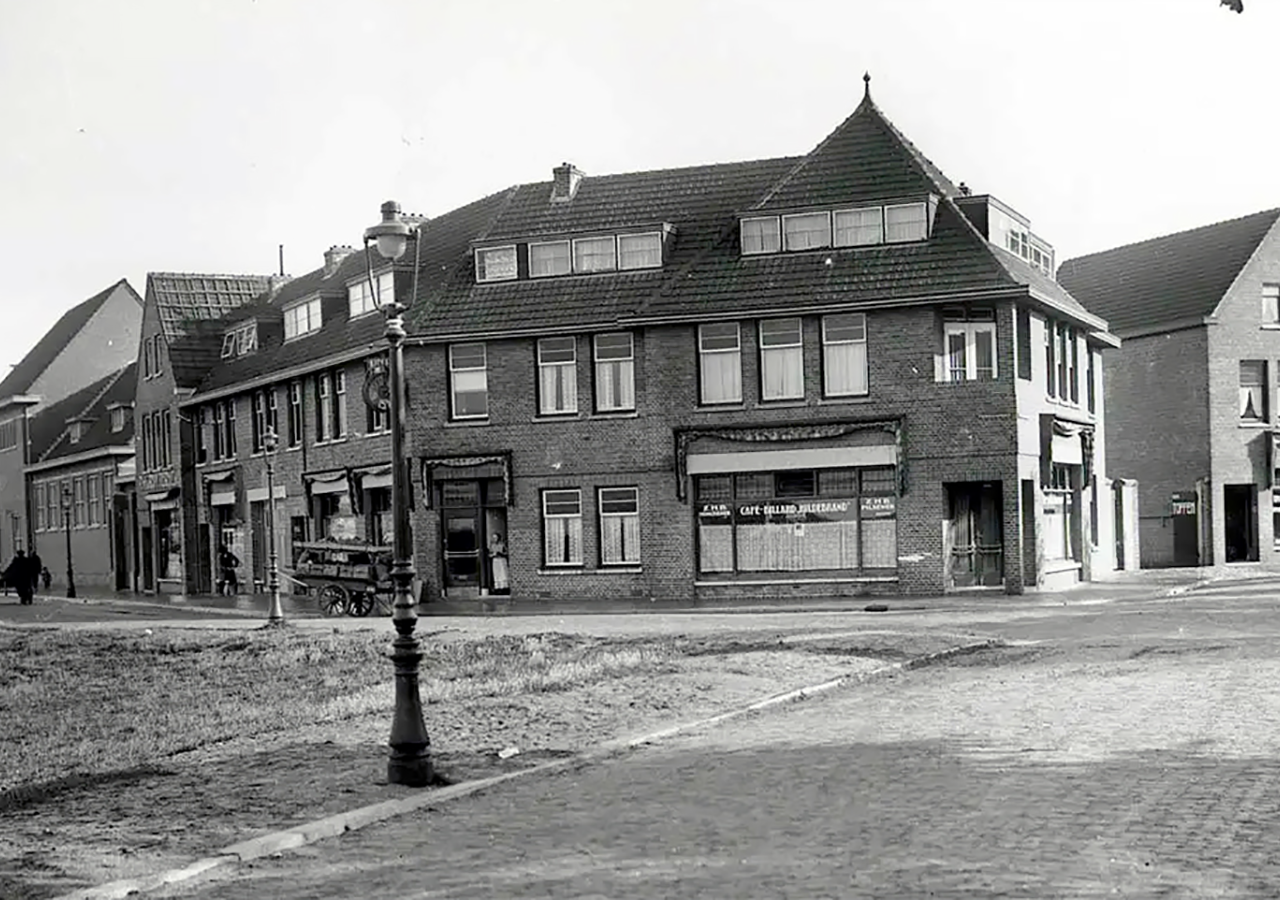
In 1948, Amaloco’s business activities move to Ferrandweg 12.
Post-war
After the war, the sales and production of photochemicals was picked up again. The program of ready-made developers and fixate was further expanded at the expense of the sales of loose chemicals such as Metol, etc. A complete range of developers was created based on Metol/Hydroquinone and fixate based on sodium thiosulfate.
The highlight was the development of a series of unique long-life liquid black&white negative developer with a high degree of dilution based on Pyrocatechin/Sodium hydroxide. This caused a lot of attention at that time. These developers are still sold successfully under the name AM 20 – Nivenool and AM 50 – Gammanool.
In 1948, the home address at the Nunspeetlaan 303 was abandoned and exchanged for a business premises elsewhere in The Hague, viz. in the Ferrandweg 12. Turnover continues to rise until the mid-1960s. The long-term illness of the founder of the company, E. van Beugen, was the reason for a standstill for some time of the developments and expansion of Amaloco. E. van Beugen dies in 1967 and one of his sons, Jaap, takes over the company.
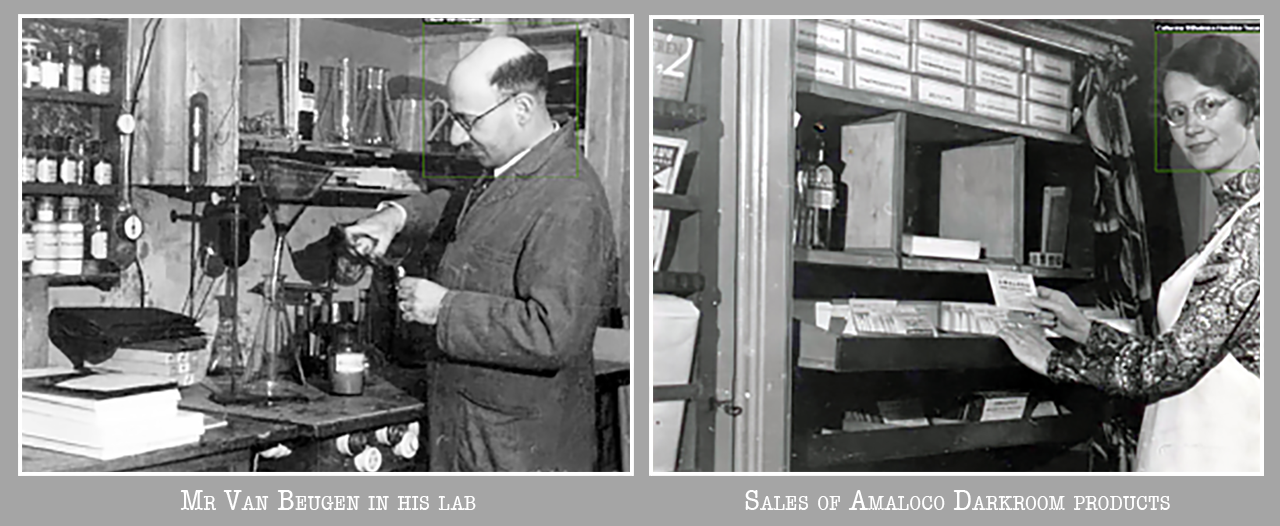
Amaloco under new management
An energetic start was made with the expansion of the black&white product programme. New products were for example, the H2 fast film dryer, H3 anti-film curling fluid, scale cleaners, H8 quick-coil, an improved H10 wetting agent and last-but-not-least H14 film cleaner.
In 1967 and before that date, the sales strategy was direct sales to photo shops and photo amateurs with their own darkroom. This strategy was abandoned from that date on. Sales in the Netherlands went then through wholesalers, among others Koninklijke Foto Film Fischel in Amsterdam. As a result of that, direct supply to photo amateurs stopped.
In 1970 Amaloco spread its wings across the borders of The Netherlands. Exports were made for the first time, mainly to Belgium. Therefore, a distributor was appointed in there.
A new product was introduced in 1971, S10 Odourless Signal Stopbath, based on citric acid. It was an immediate success, because with the help of S10 the always-annoying acetic acid smell in the darkroom belonged to the past. In 1972 production of the liquid fixers X40 and X25 based on ammonium thiosulphate started.
All in all, Amaloco’s sharp increase in turnover/production required more space and better logistics options than available in the Ferrandweg 12 in The Hague. So, in 1974 Amaloco moved to an industrial area with good facilities and excellent logistics in Ommen, situated in the eastern part of The Netherlands.
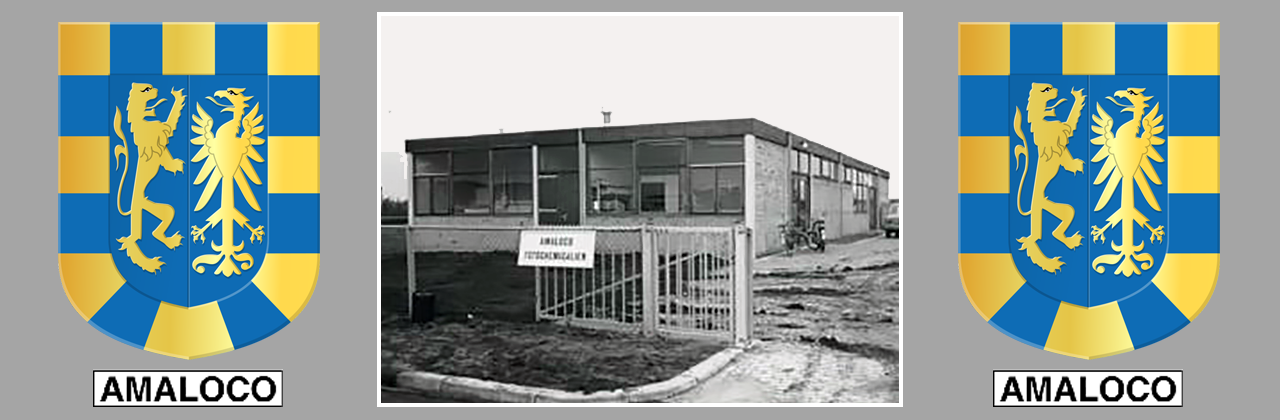
New operations building in Ommen, 1974.
The Ommen period
In Ommen Amaloco build a brand new building of 770 m² on a 2,000 m² site. Since then the black&white developers were modernized by the replacement of the basic ingredient Metol by Phenidone.
In 1974 the new black&white negative developer AM 74 was also introduced in the market. A black&white negative developer based on Phenidone/Hydroquinone and Carbonate with a semi-levelling character. A special feature of AM 74 was that ALL film sensitivities could be developed at 20°C in ONE AND THE SAME TIME OF 5 MINUTES. Up to this day, AM 74 is still the perfect developer for all Fuji Neopan, Ilford Delta and Kodak T-max films.
Between 1976-1979 Amaloco introduced a full range of colour chemistry for the EP2 and C-41 processes. The products were strongly focused on small-scale finishing methods.
To stimulate the colour finishing market, Amaloco introduced a colour measuring system in 1978 under the motto “Colour enlargement without a fuss”. The system kit consisted of a filter holder, 3 additive colour filters and a filter/exposure calculator. At that time, the whole kit cost less than fifty guilders. It was a success and more than 2000 of these kits have been sold.
In 1979 the colour chemistry program is completed with the R-3 process Amcolour. In the same year, Amaloco celebrates its 50th anniversary with a major photo contest with 661 photos submitted.
Amaloco in the eighties
In 1981, 7 employees work at Amaloco. Sales are made in The Netherlands through wholesalers and in Denmark, Belgium and Ireland through an importer. In Germany, Amaloco products are sold under the name Argenta.
In 1982 sales fell dramatically due to the economic recession. There were layoffs and Amaloco’s situation became difficult. It was decided to align the Amaloco products more to the professional market in general and to the press photography in particular. Under the name of Profselekt, a thorough technical upgrade of the complete black&white delivery program took place. Furthermore, Amaloco introduced 5 and 10 litre Cubitainer packaging with black&white developers, stop baths and fixer. From 1985 onwards, this new strategy began to bear fruit and sales started to pick up again.
The development of a complete range of toners was started in 1987. The range started with the T10-Sepiton, followed by the T20-Blue toner and then the T30-Copper red toner. A few years later the T40-Varioton, a variable brown toner, was added to the program.
During this period, a lot of attention was also paid to the health climate in the darkroom. In particular, the sulphur dioxide gas released from acid fixer was a subject of discussion. More darkroom workers than expected experienced this “fixing smell” as a nuisance. This was the direct reason for the development of X88 Odourless Fixate. In the beginning, sales started somewhat hesitantly, but then it turned out to be a bull’s eye, resulting in a much larger share of the fixing market. In 1989, exports to Austria started.
Amaloco in the nineties
In 1990 Amaloco introduced its own new colour chemistry for the RA-4 hot process under the name Rapidocolor/Rapidoblix. It replaced the old EP-2 processes Apécolor and Kolcolor. The new RA-4 process/paper was the breakthrough for self-colour enlargement with a cleaner, more stable and more economical process with fewer test strips.
The major initiator of the RA-4 process/paper is without a doubt market leader Kodak. In 1991 Amaloco buys the license for Mono-concentrate technology in RA-4 and C-41 processes from Kleinschmidt of Munich. The RA-4 cold process (20° C), which was based on this mono-concentrate technique, was improved by Amaloco and marketed in 1992 under the name Mono~Colour/Mono~Blix. It was the world’s fastest RA-4 process at 20° C. Only one minute of developing and bleach fixing in the tray was sufficient for beautiful colour enlargements with high colour saturation. The mono C-41 process was introduced under the name Mono-Negacolor.
The “Mono” products became a success in both the Netherlands and abroad. New export countries were added, such as Sweden, Germany and England. An additional advance was that these new export countries were also accepting Amaloco’s black&white products.
From 1993, based on the RA-4 cold process and by means of a Transformer kit, an R-3 cold process has also been brought on the market. This form of R-3 process was unique. It was also the world’s fastest R-3 process at 20° C. Finally, in 1994 K945- Stabi-AM comes on the market. It is a special stabilizer that makes rinsing colour photos more or less superfluous.
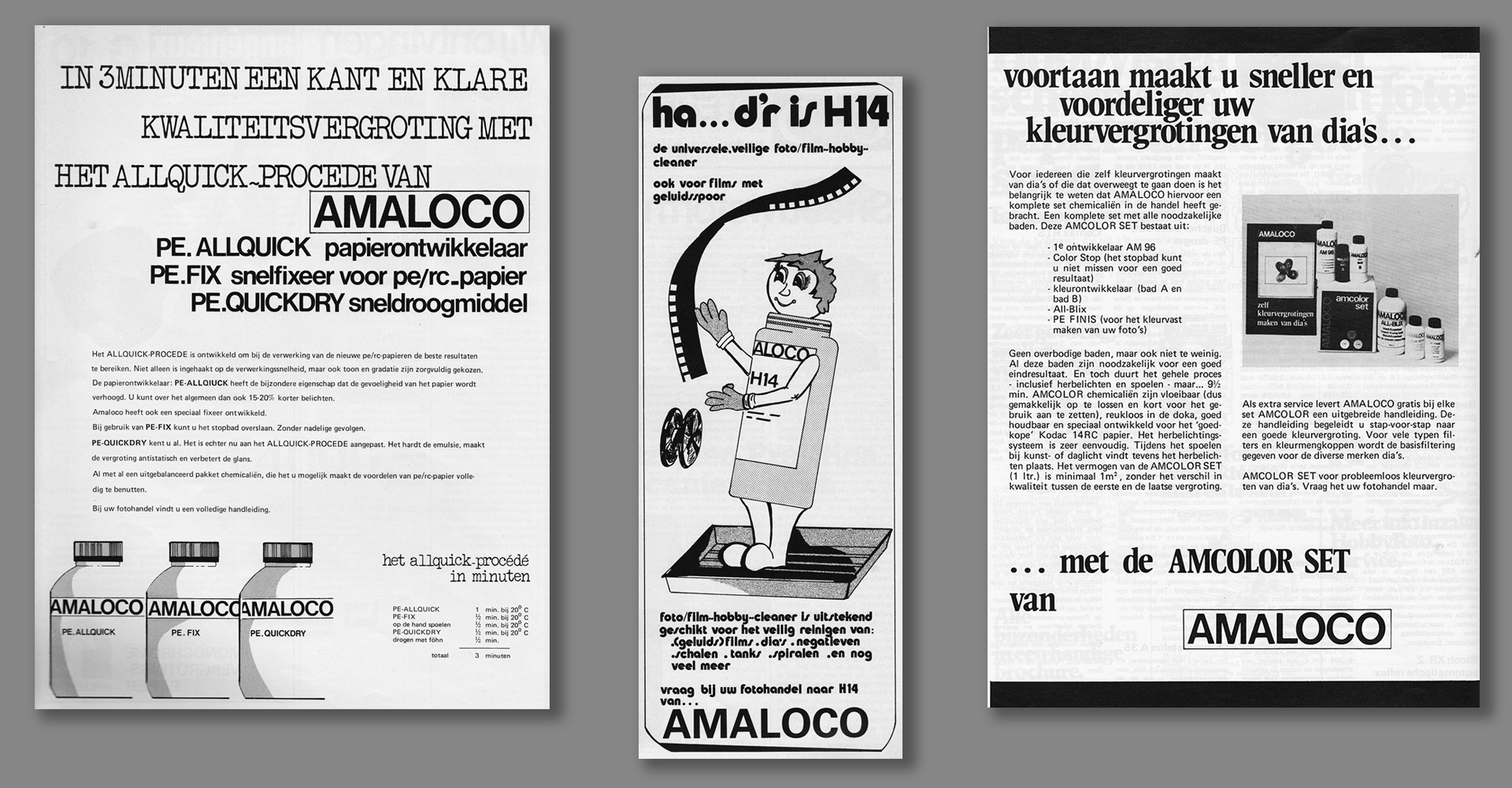
Amaloco regularly advertised in photo magazines at home and abroad.
Environmental safety
In 1994 the environment demanded extra attention. To obtain a new environmental permit, the company had to be thoroughly renovated with all kinds of new safety features. In the years 1995, 1996 and 1997 this renovation was realized. The total cost was more than € 150,000. Safety data sheets were also compiled in different languages for all products during this period.
Due to the sharp increase in exports, growth figures were recorded up to and including 1995. But in 1996 Amaloco also started to notice the influence of digital photography on its turnover. In the press photography market, for example, turnover became considerably lower.
An accidental discovery in 1996 enabled Amaloco to further upgrade the paper developers AM 3003 and later AM 6006 Extra Varimax. Another special development took place in 1999. Amaloco entered the market with T50 Extramax. It was a unique product that visibly increased the maximum density (blackness) of black&white photos on barite or PE paper after the development process.
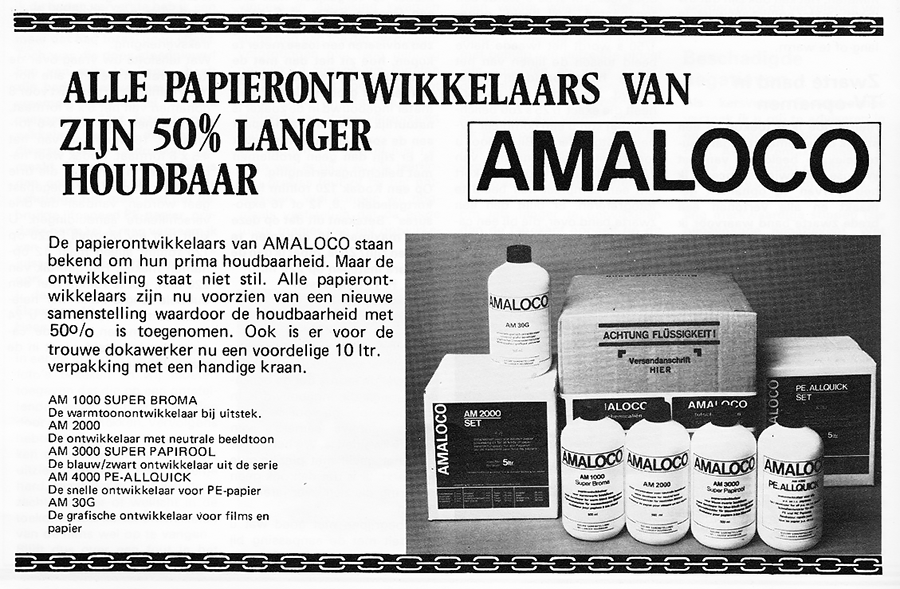
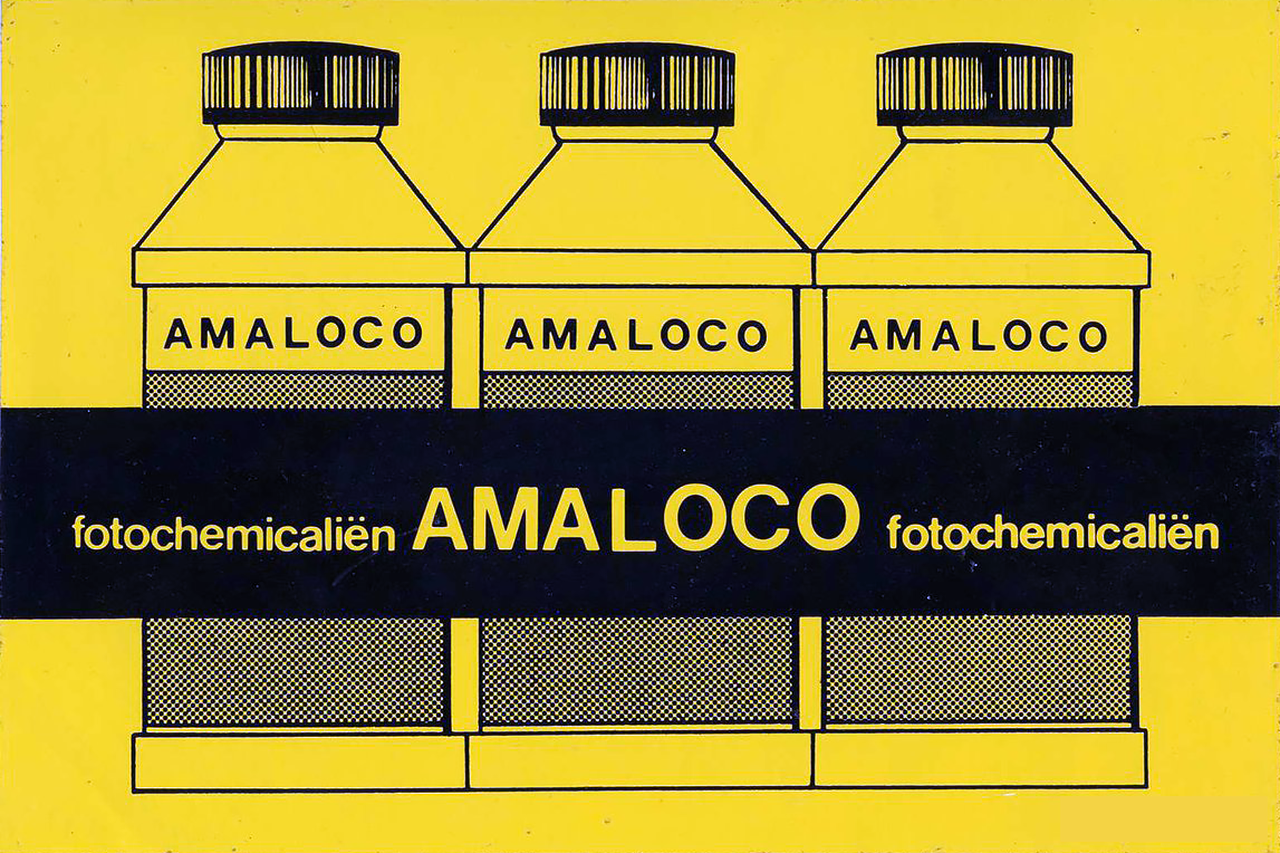
Sticker as used on Amaloco’s shipping packaging.
Amaloco in the 21rst century
In 2000, Amaloco introduced the black&white PE/RC paper Variprof Extra and Varimax under the motto “With expertise” and under its own label. These papers fitted in perfectly with the existing black&white chemistry programme. Initially, sales did not go smoothly, but since then it became an important part of the turnover.
In 2002 new products appeared on the market. An improved paper developer AM 2002 was henceforth called AM 2002 Extra Bromax. Furthermore, the successful X88 Odourless Fixate was replaced by X89-Extrafix. Besides the fact that it was odourless, this new fixate had more capacity and fixing speed too due to a higher content of Ammonium thiosulphate. The toner program was completed with T 60 Seleniton, a classic and traditional Selene toner at a competitive price.
In the fall of 2003, Amaloco launched AM 8008 ECOMAX; a Hydroquinone-free paper developer especially for Ilford Multigrade IV RC and Barite paper. This introduction should be seen in the context of further optimizing the health climate in the darkroom.
End of the amaloco show but…
From 2004 to 2008, Amaloco produced the successful black&white chemicals in the usual way, but had to stop production after 2008. There were more than one reason for this, but the main reason were the cost of the necessary investments in environmental measures at the Ommen site. Investing in these measures would have meant that further production there would no longer have been profitable.
From 2004 to 2008, Amaloco produced the successful black&white chemicals in the usual way, but had to stop production after 2008. There were more than one reason for this, but the main reason were the cost of the necessary investments in environmental measures at the Ommen site. Investing in these measures would have meant that further production there would no longer have been profitable.
The show goes on!
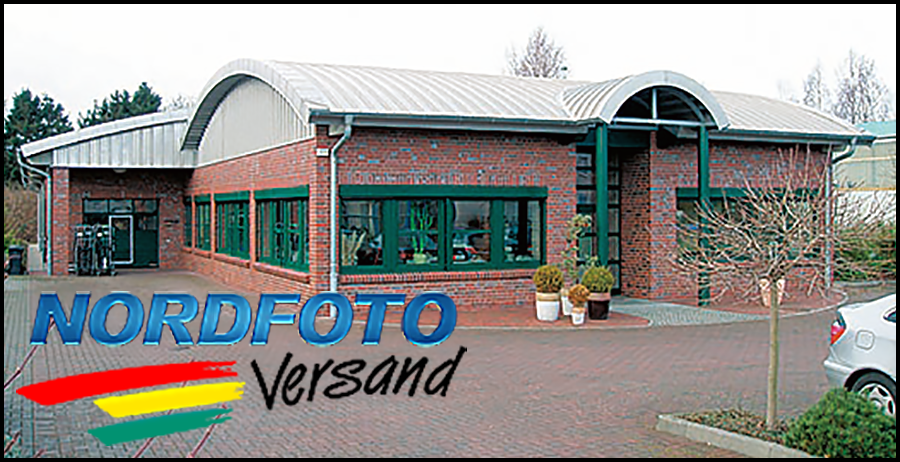
The fact that the popular and tried-and-tested black&white chemicals still exist today goes back to an initiative by Nordfoto Versand. This trading company for photo items in Germany was a sales partner of Amaloco for a long time and would have regretted it very much if these traditional photo chemicals had disappeared from the market.
For this reason, Nordfoto Versand bought both the trademark rights and the original recipes from Amaloco and produces now developers, stopping and fixing baths and wetting agents under the most modern conditions in Germany since 2009 and sells them worldwide from the headquarters in Norderstedt near Hamburg.
FOUNDER: Edward Anthony
COMPANY NAMES:
1842: E. Anthony & Co. (later E. and H. T. Anthony & Company, when Edward Anthony’s brother officially joined the business); 1901: Anthony & Scovill Co. after a merger with Scovill Manufacturing (Connecticut); 1928: Ansco merged with the German photo company Agfa to form a corporation named Agfa-Ansco; 1941: Agfa-Ansco merged with GAF (General Aniline & Film); 1943: Agfa-Ansco became Ansco; 1977: ceased production of consumer films; 1990s: The last Ansco cameras were produced.
COMPANY ADDRESSES:
1901: Binghamton, New York, USA; 1960: Vestal, New York.
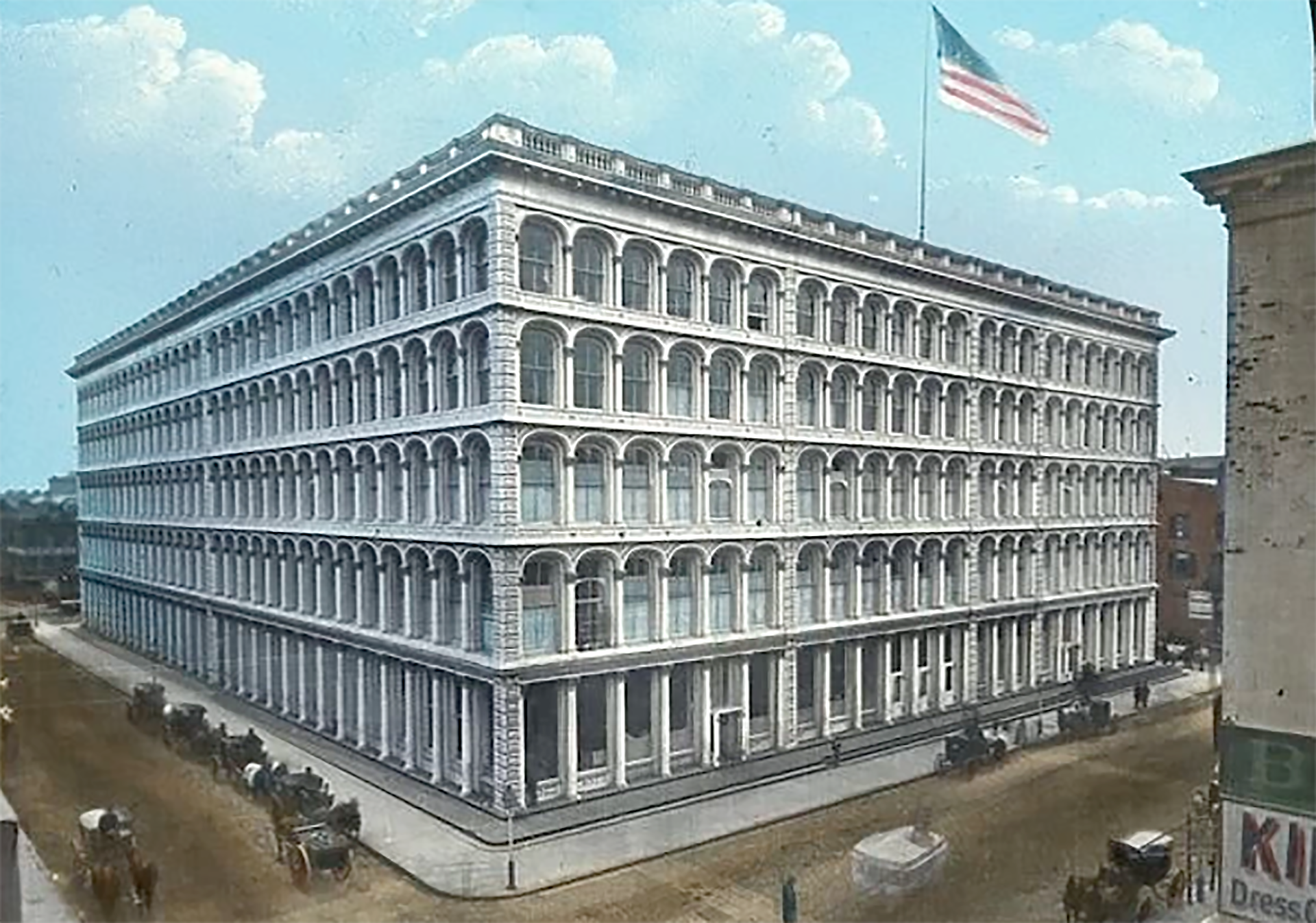
The fine office building of E. & H. T. Anthony & Company situated at 591 Broadway, New York, USA. Date: circa 1890.
The company was founded in 1842 (pre-dating Kodak in the photography business) as
E. Anthony & Co. (later E. and H. T. Anthony & Company, when Edward Anthony’s brother officially joined the business).
Company founder Edward Anthony, a Columbia College trained civil engineer who had studied photography with Samuel F.B Morse, started in the photography business in 1842 by opening a daguerreotype gallery in New York.
Five years later he opened a separate shop devoted exclusively to photographic supplies and as sales grew rapidly ceased operations in his Daguerrotypist gallery. In 1850 Anthony began the production of daguerreotype cases, camera boxes, and photographic chemicals. His brother, Henry T. Anthony, joined the business two years later in 1852.
The Anthony brothers’ factory was located at New York City’s Harlem Railroad Depot occupying 1/4 of the building by 1854 and advertised that their company was the largest manufacturer and distributor of photographic apparatus and material in the world. In 1859 Anthony added stereoscopic view cards, photographic albums, and gallery furniture and backdrops to the company’s product lines. The Anthony company also maintained a close business relationship with famed American photographer and portraitist Mathew Brady.
From February, 1870 until April, 1902 the company published a monthly magazine called Anthony’s Photographic Bulletin which included many photographs and illustrations as well as a wide variety of contributed technical, practical, and scholarly articles along with advertisements for the Anthony company’s products and other services. In the 1890s the company also developed and produced two consumer cameras of their own design—a camera-box called the “Buckeye” and a more expensive bellows-box type called the “Marlborough”—as well as an extensive line of photo cases and other products.
The firm’s name was formally changed to E. & H.T. Anthony & Co. in 1862 and in 1877 was reorganized as a corporation with Anthony as president, his brother as vice-president, and Colonel V. M. Wilcox as manager and secretary. After death of both brothers, Wilcox became president, Richard A. Anthony (son of Edward Anthony) vice-president, and Frederick A. Anthony the secretary. In 1883 the company produced the first commercially manufactured hand instantaneous camera, called the Schmidt Patent Detective Camera, in America.
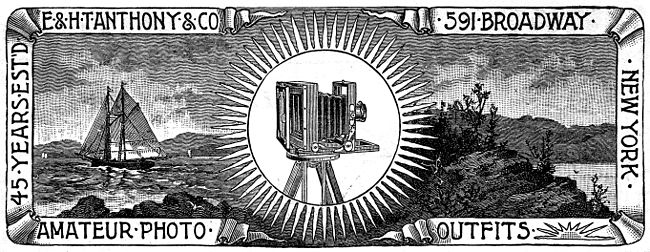
The company became Anthony & Scovill Co. in 1901, after a merger with the camera business of Scovill Manufacturing (Connecticut), founded by James Mitchell Lamson Scovill and William Henry Scovill. That year, the company headquarters relocated to Binghamton, New York. This was already a site of one of Ansco’s photographic paper manufacturing facilities.
In the Late 1880s ANSCO’s predecessor, Anthony and Scovill, bought the Goodwin Camera & Film Company. Hannibal Goodwin invented the flexible photographic film, which should have made Anthony Scovill the leader in the amateur photography business. But George Eastman copied the patented process. Just after that, in 1905 Ansco settled a landmark patent infringement case against Eastman Kodak, which had been violating the Goodwin flexible film patent (Hannibal Goodwin of Newark, New Jersey) held by Ansco.
The ruthless behaviour of Eastman nearly drove Ansco out of business, but a settlement in 1905 saved the company from bankruptcy. The settlement received from Eastman Kodak (5 million dollars), was very small compared to the damage done to Ansco, which already had financial problems as a result of business lost to Eastman Kodak. So, Eastman Kodak got away cheaply on this legal proceeding. Previously known as the largest suppliers and distributors of photographic supplies in the United States, Ansco was now in second place to Kodak’s first place.
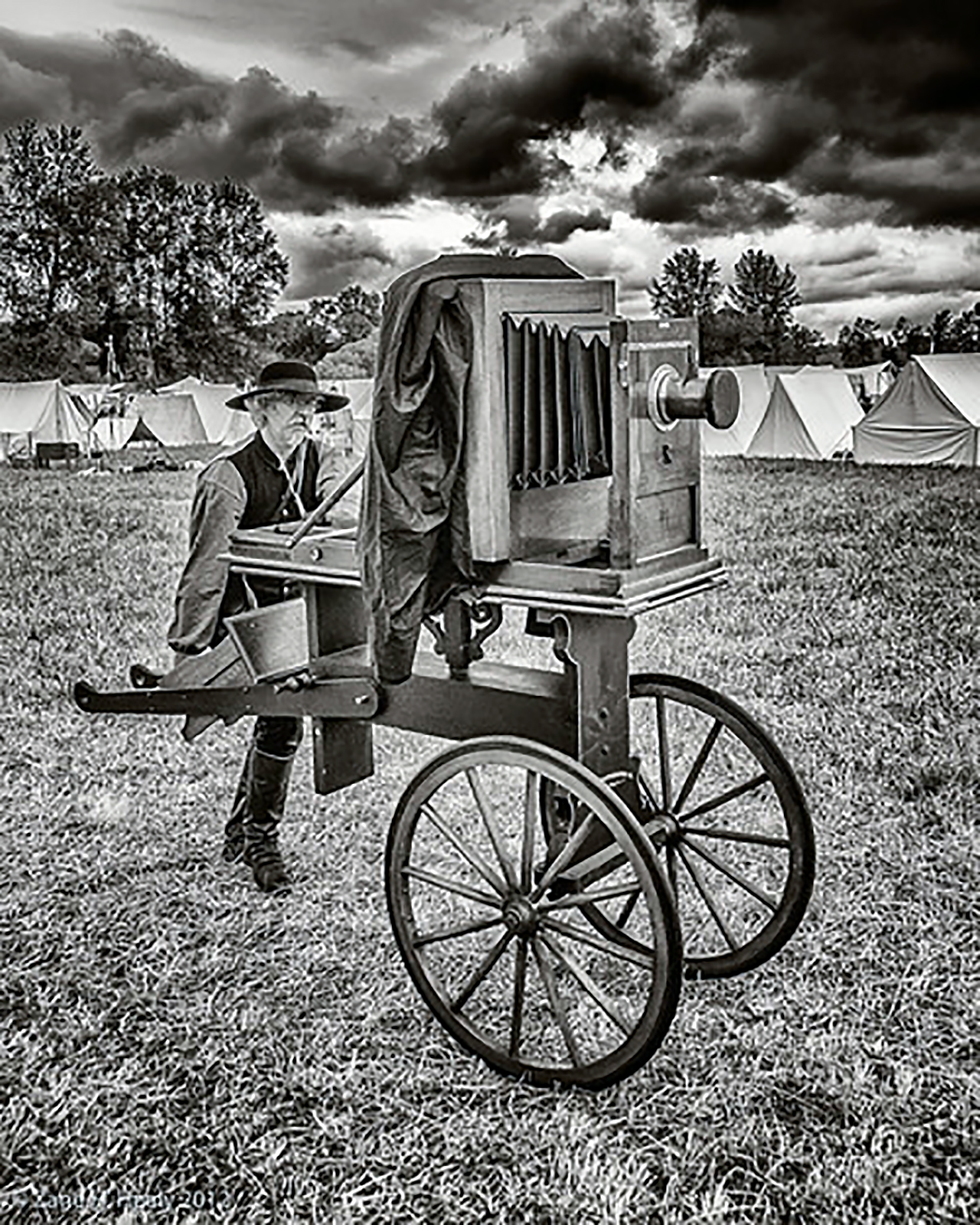
One of the first cameras from E. & H. T. Anthony & Company was the large field camera on wheels. Very different from the small subminiature cameras of a century later.
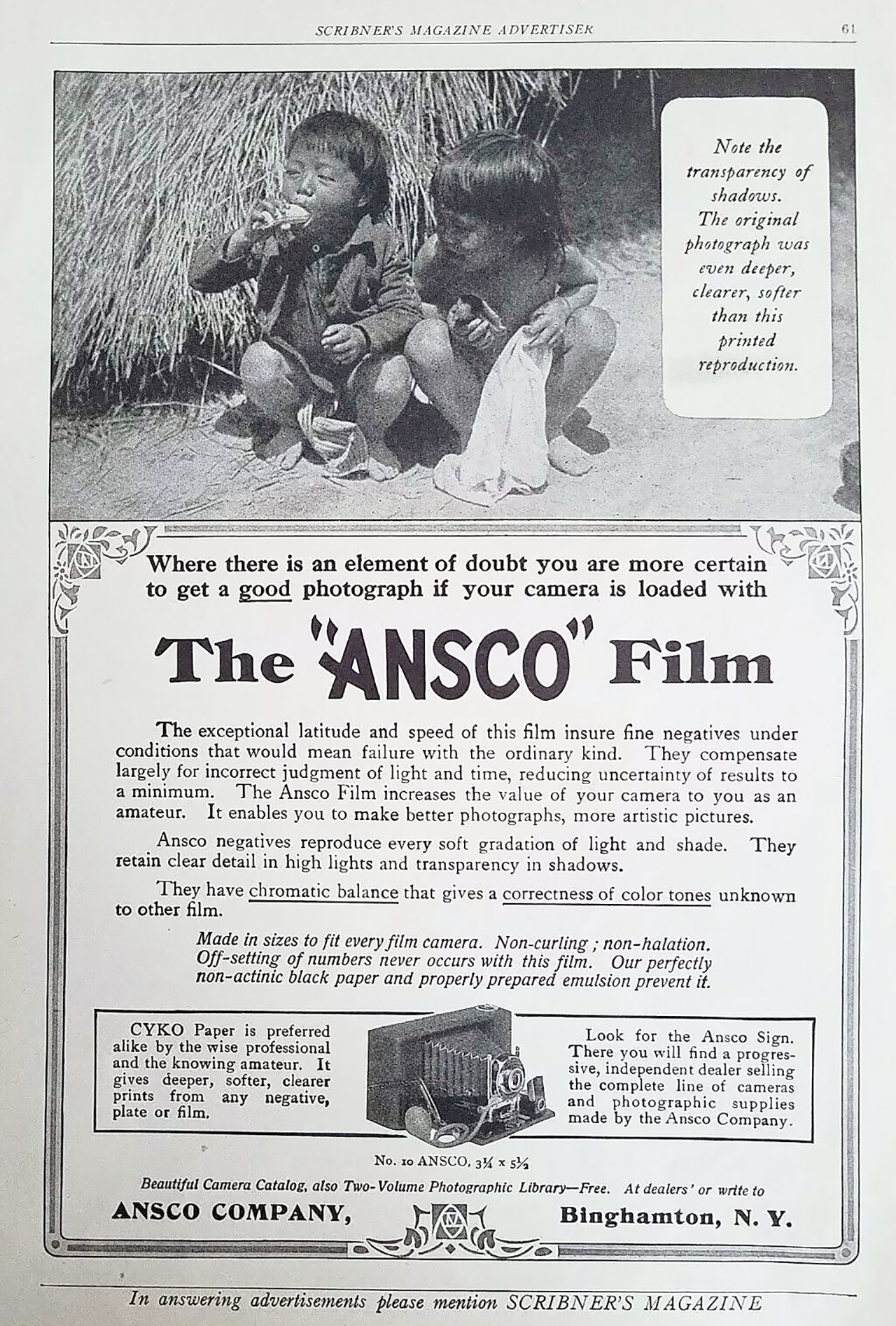
An advertisement for Ansco products in Scribners Magazine, ca. 1900.
Merger with Agfa
Despite an early start and a patent that should have secured their role in the marketplace, Ansco struggled for years to recover from the significant financial blow Kodak delivered when they entered the market.
That was one of the main reasons why Ansco merged in 1928 with the German photo company Agfa to form a corporation named Agfa-Ansco. The German parent of Ansco provided money, technical talent, and access to patents.
Later the same year, Agfa merged with other German-owned chemical firms into a Swiss holding company, Internationale Gesellschaft für Chemische Unternehmungen AG or IG Chemie, which in turn was controlled by the German chemical industry conglomerate, IG Farben.
Flush with foreign cash, Ansco expanded its production facilities. They built a new film production plant, a new camera plant and acquired buildings as part of unprecedented growth. During this same time, they won several awards for developing infra-red and high speed black-and- white films.
Ansco was on track to financial success, having two consecutive years of record earnings in 1938 and 1939. Efforts were under way in 1939, for instance, to increase earning power by fully merging with General Aniline & Film (which owned 81% of Ansco at the time). Despite its increased size, Ansco remained a distant second to Kodak. And the onset of World War II had a huge impact on Ansco.
The move to Binghamton also shifted Ansco’s focus from distributing all photographic supplies to focusing producing their own film, paper, cameras and accessories. The money to be made in the industry at the time was in film, paper and processing. Ansco produced and developed a number of well-known and respected films and papers at its Binghamton facilities, right up until they ceased production of consumer films in 1977.
Photography, as a new hobby and obsession, fell into two categories: amateurs taking snapshots and professionals who worked with large view cameras in studios. Ansco produced cameras for both groups. Their amateur line of cameras ranged from simple box cameras to inexpensive scale-focusing roll film and a fixed focus twin lens camera. Its studio view cameras were large wooden affairs that used 4”x5” and 8”x10” film and were well respected and widely used by professional photographers.
Their cameras, however, were usually one-time purchases. Professional photographers might purchase an additional lens or two but amateurs, with their fixed-lens cameras, had no such option. Ansco’s bottom line came from purchases after the camera: film, processing, prints and more film.
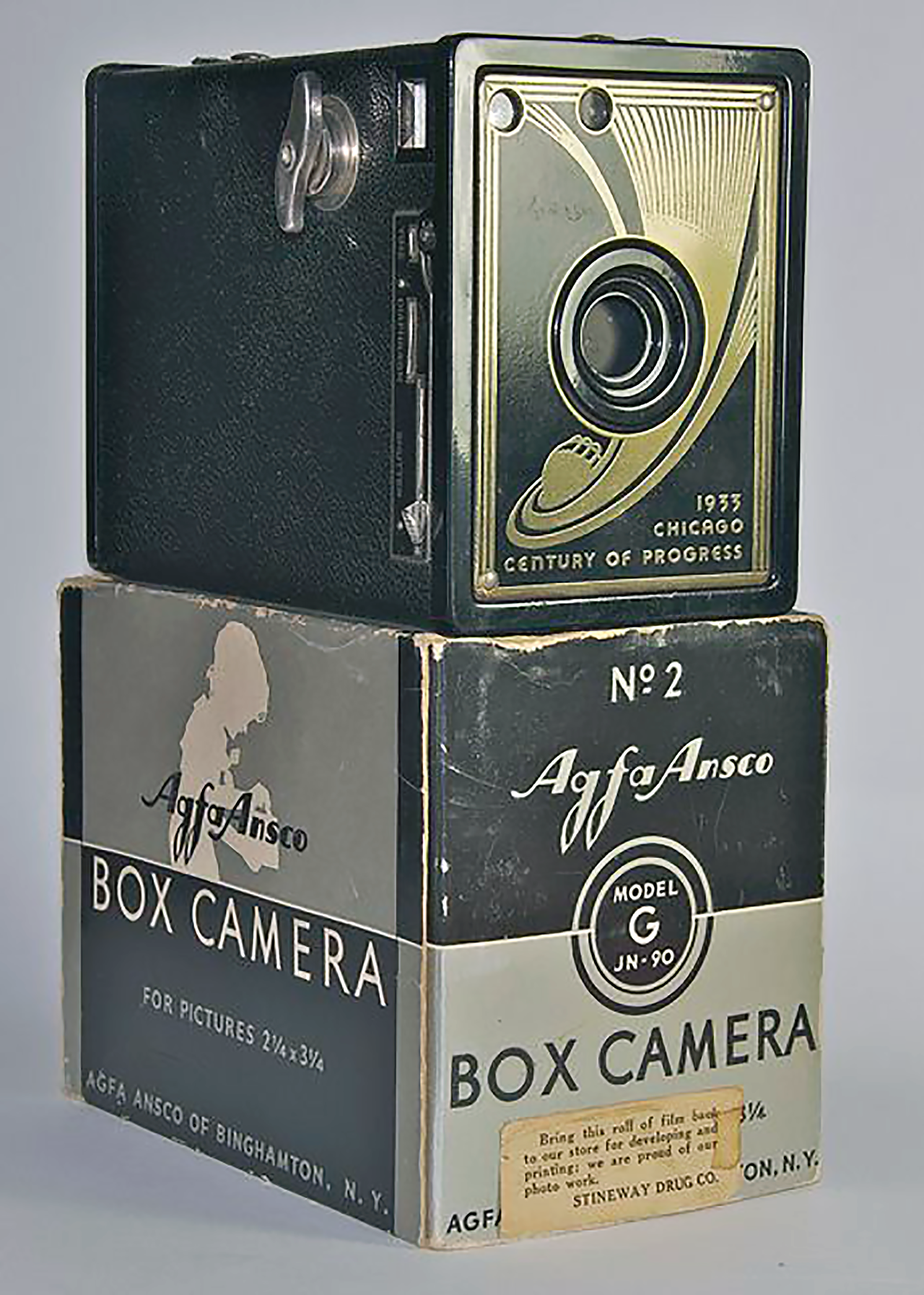
Agfa-Ansco No. 2 Box camera as introduced on the Chicago Worlds Fair of 1933.
Some older Ansco and Ansco-Agfa films.
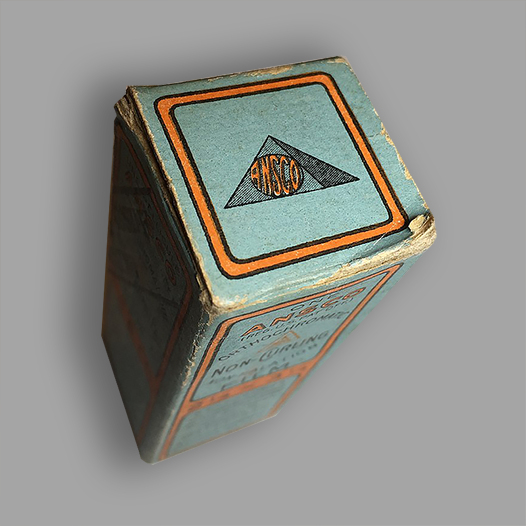
Ansco logo on a 120 roll film that expired in 1916.
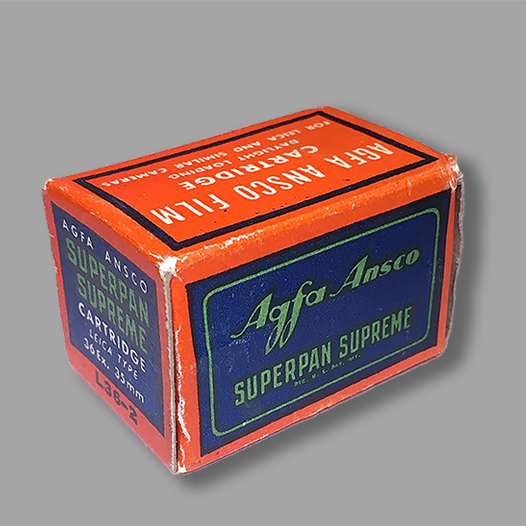
Box of Agfa-Ansco 35mm Film (expires April 1945).
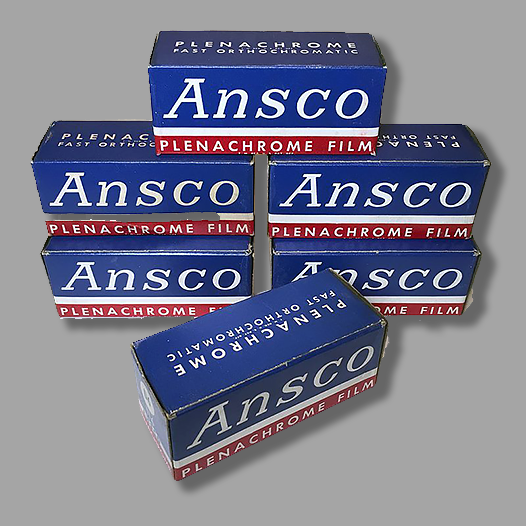
Boxes 35mm Ansco Plenachrome 116_Film which expired July 1948.
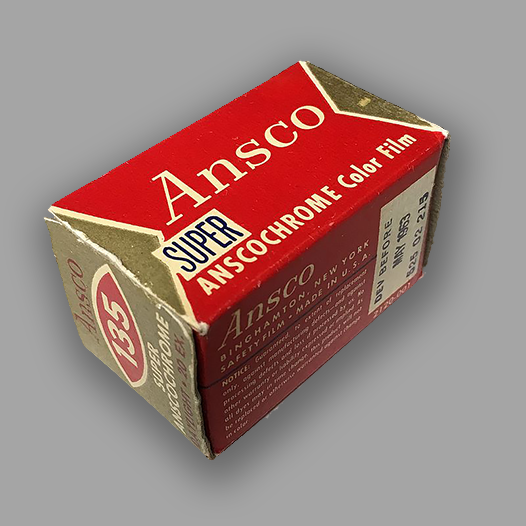
Box of 35mm Ansco Super-Anscochrome color slide film (Expired-May-1963).
General Aniline and Film, the American parent of Ansco, came under close scrutiny by the U.S. government with the Germany’s invasion of Poland on September 1, 1939.
Ansco saw the writing on the wall immediately: Ernst Schwarz, president of Agfa Ansco Corp., renounced his German citizenship and was sworn in as an American citizen at noon the same day. Over the next several years, General Aniline and its subsidiaries replaced German-born officials with native-born Americans in a vain attempt to forestall eventual nationalization. John Mack, a friend of President Roosevelt, replaced D.A. Schmitz, who resigned as president on Sept 23, 1941. In 1942, the US government seized and nationalized Agfa-Ansco as enemy property.
Like many other companies, Ansco produced bomb fuses, sextants, rangefinders, film, cameras, airplane instruments and other products for the US war effort.
In January 1942, Leopold Eckler, and American citizen since 1936, and four other executives were suspended by the Treasury Department because they “personified the domination of the company by the German dye trust (IG Farben).” Ansco workers were baffled by this move and petitioned the Treasury Department to reinstate Eckler, to no avail. A few weeks later James Forrestal was named acting manager of the Agfa Ansco Division.
By this point, General Aniline has lost nearly a dozen key employees through resignation or suspensions. Ultimately, their effort to “try to keep on rolling under [their] own momentum” failed. In 1943, Ansco dropped “Agfa” from their official name.
Prior to the war, Agfa-Ansco had marketed Agfacolor film made in Germany. To assist the war effort, the company experts used available information to develop a similar product, first called Ansco Color, later Anscochrome. After the war, Anscochrome was widely distributed, but met with limited commercial success in competition with Kodak products. An important marketing feature was its greater speed in comparison to Kodachrome. A second advantage was that users, professional or amateur, could process the film in their own darkrooms rather than having to send it away (as with Kodachrome) or use cumbersome re-exposure steps as with Kodak Ektachrome.
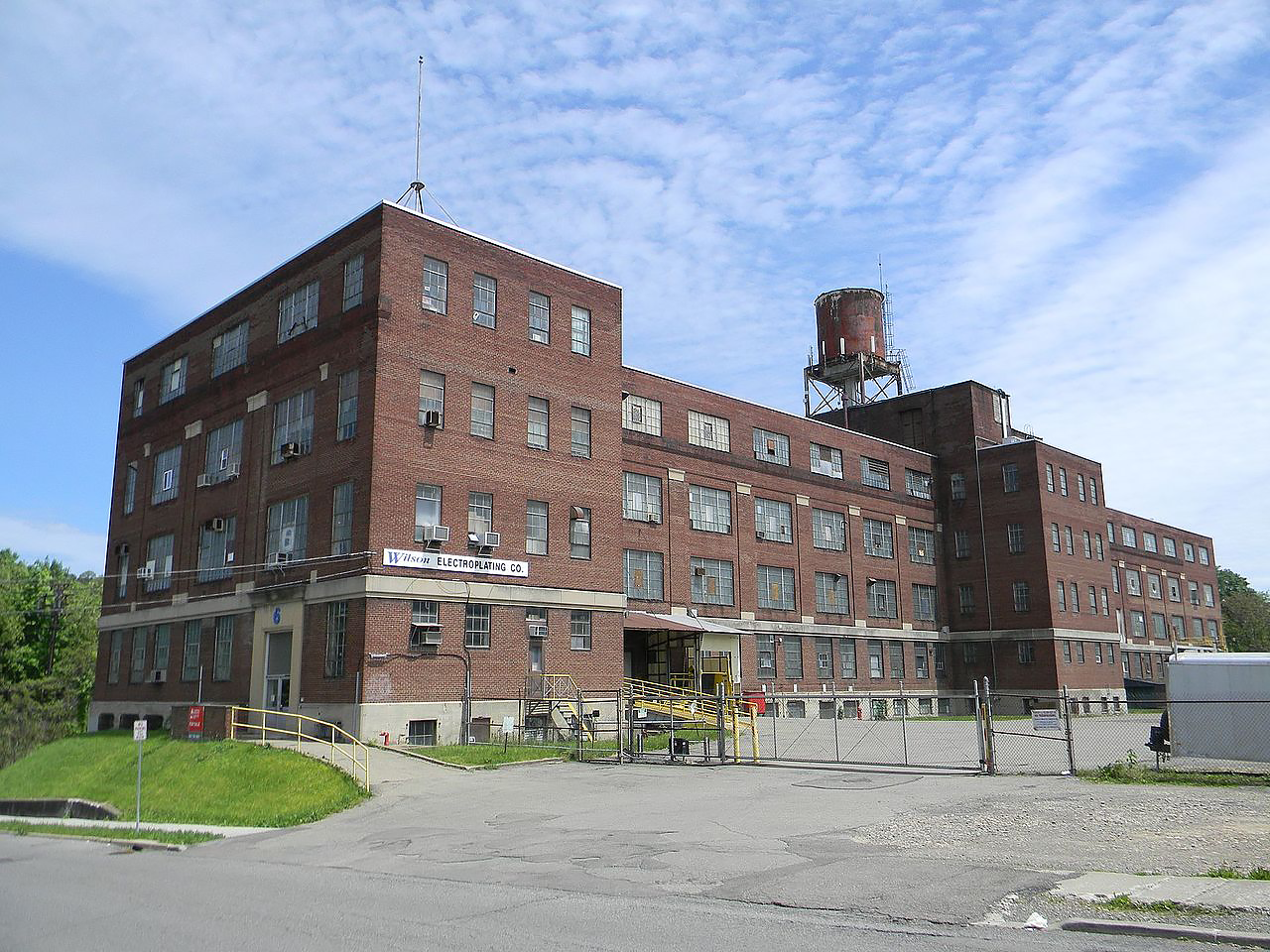
The ANSCO-Building
General Cigar Company–Ansco Camera Factory Building, also known as Agfa-Ansco, General Aniline and Film (GAF), and Anitec, is a historic factory complex located at Binghamton, Broome County, New York. It was originally built in 1927-1928 for the General Cigar Company; Ansco purchased the factory in 1937. The factory building is a four-story brick building with basement, five bays wide and 20 bays long. It has an intersecting four-story wing and two-story addition constructed in 1950. The buildings housed manufacturing operations of Ansco for cameras and photographic equipment. The factory closed in 1977.
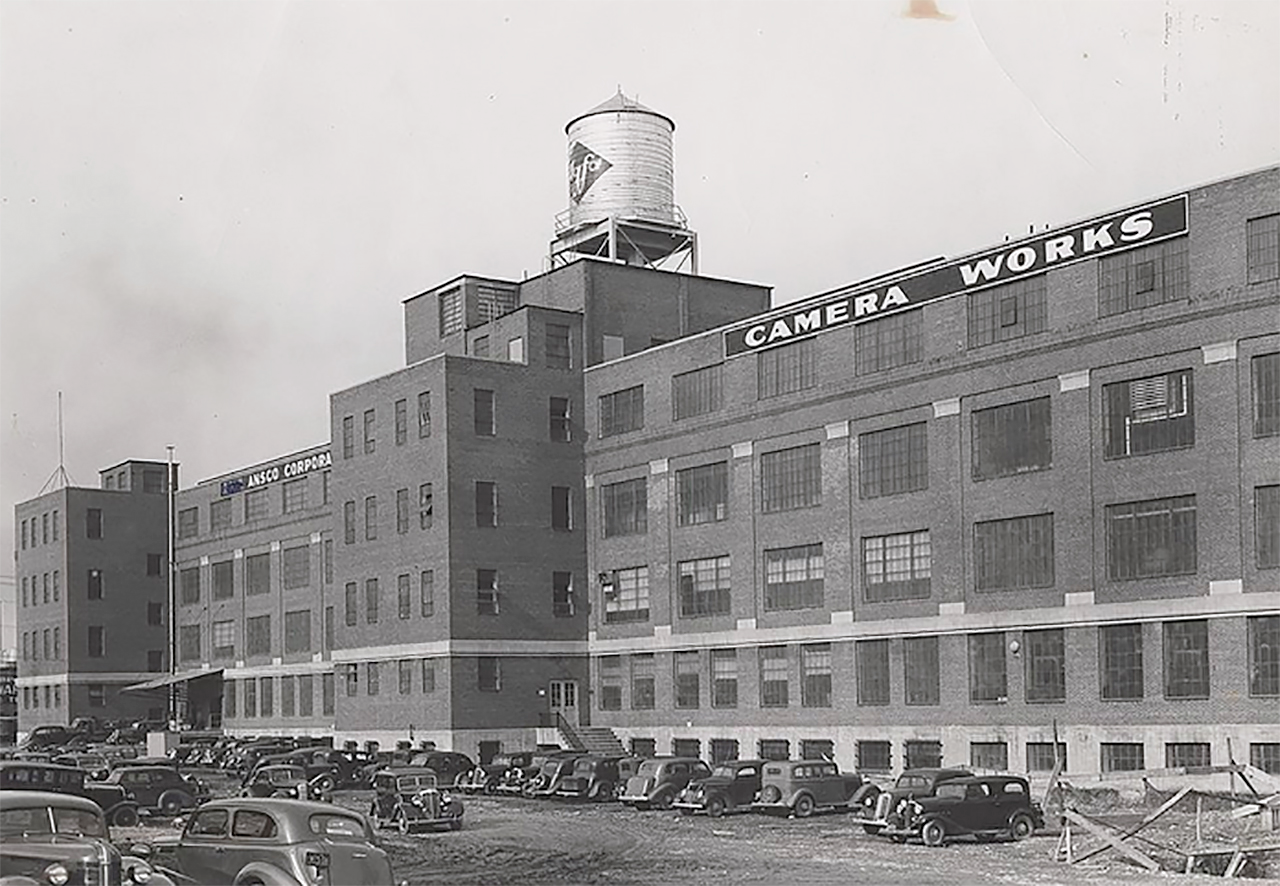
The former Ansco Camera Factory on Emma Street.
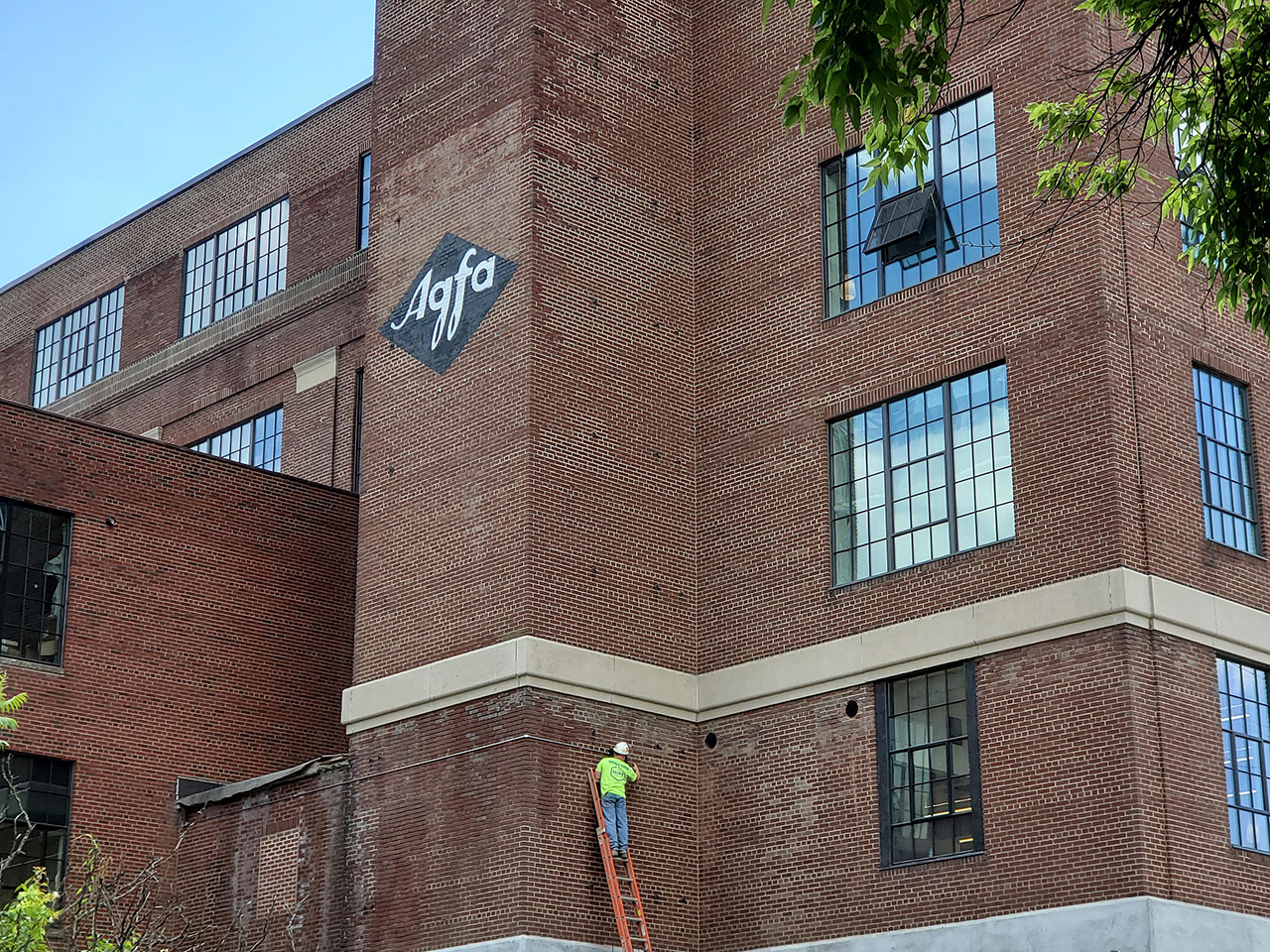
A worker on the north side of the former factory building on Emma Street on June 27, 2019.
At the end of the war, Ansco immediately announced the return of some of their popular, pre-war cameras (Cadet, Clipper, Viking 63, Speedex Junior and Speedex 45) along with two new models: the Reflex and the Panda.
The Ansco Reflex, as it was called in those early announcements, was promised after reconversion of the camera plant. Reconversion, however, was not a quick process. The camera plant, which had been retooled to produce military optical devices, needed new machinery and tooling to produce the Reflex.
Ansco faced significant competition in the marketplace. Kodak, their nearest competitor, had 27,000 employees even after post-WWII downsizing. Ansco, on the other hand, was one tenth Kodak’s size at 3,000 employees. Kodak was able to invest 100 million dollars in new factories and facilities in the years immediately following the war; Ansco invested only 5 million.
The biggest burden, however, was supervision by the Alien Property Custodian. Because they were owned by the government, they lacked ready access to equity capital. Further, what money they could secure, from insurance companies and banks, was “spent only after time-consuming study and deliberation.”
Given the significant challenges Ansco faced, it comes as no surprise that it was not until December 1946 that the camera plant was able to start production on the Reflex.
On top of all that, all photographic products faced a 25% federal tax, which hampered the return of the entire industry. Products had to be priced to make a profit; the tax drove those prices out of reach of many ordinary Americans.
Ansco’s management, their president and board of directors, were extremely cautious about making expenditures. Decision making took far more time than it did with their competitors: checks were more thorough and, in trying to avoid mistakes, they moved very slowly.
Ansco, by admission of Jack Frye, chairman of the board and president of General Aniline, was “never in the strict sense a camera manufacturer. It lacked facilities for grinding lenses, making shutters, and moulding cases.” It purchased component parts, like the Wollensak shutter and lens in the Reflex, from domestic manufacturers.
Ansco was under US government supervision for more than 20 years, until it was finally sold as enemy assets to American interests in the 1960s. At that time, a new headquarters was constructed in Vestal, New York, adjacent to the new college campus of Harpur College (now Binghamton University). This location is the one of two remaining pieces of Ansco in the Binghamton area and is currently occupied by the University.
The second production building is located at 16 Emma Street and is currently luxury apartments. The Vestal location continued to do business after World War II as Ansco until 1967 when the company adopted the parent’s name of General Aniline & Film (GAF), and a variety of cameras as well as films were sold under this name until the business was shut down in the early 1980s.
Briefly in the 1970s, it was the official film of Disneyland and at this time, actor Henry Fonda served as the company’s spokesman in television commercials including one that featured Jodie Foster in her first acting role. The last Ansco cameras were produced in the early 1990s by a Hong Kong business that bought the rights to the name.
ANSCO & GAF Cameras
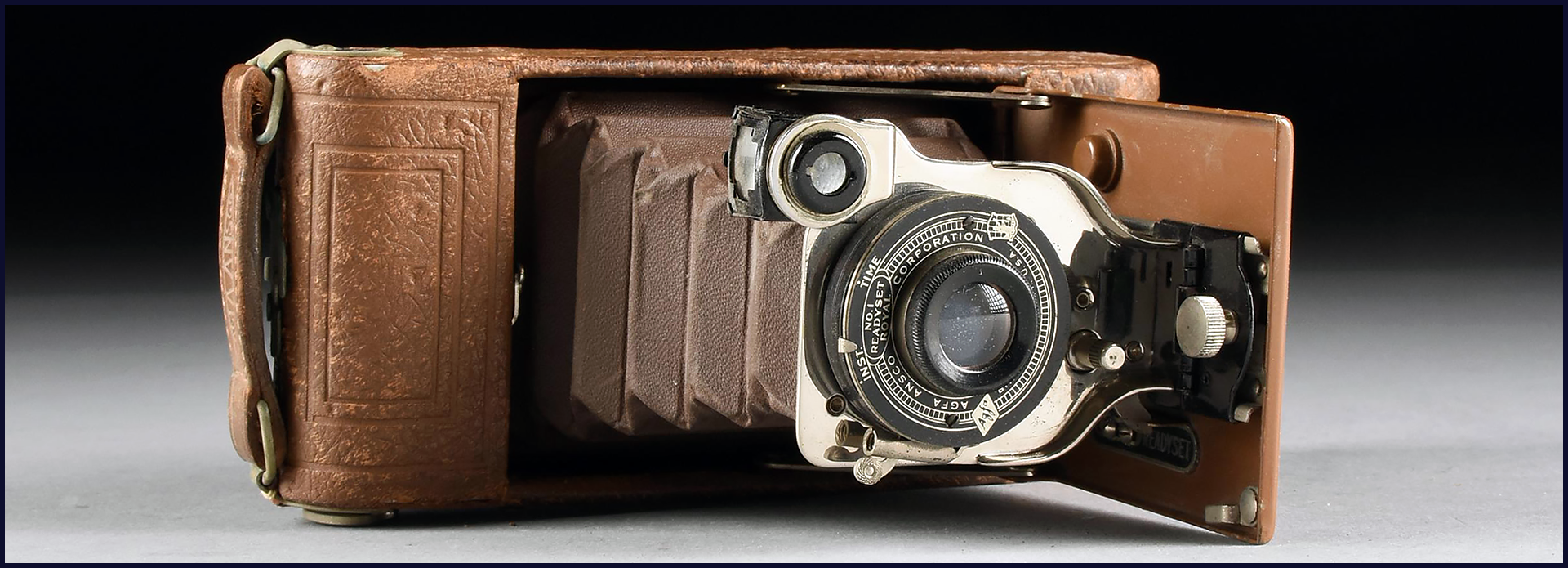
cameras
- Climax Portrait Camera
- Carte de Visite camera
- Solograph (stereo camera)
cameras
- Ansco 135 (Haking Halina 150)
- Ansco 1065 (Haking 35mm w/fixed focus 48mm f:8 lens)
- Ansco Anscomark M
- Ansco Anscoset, Anscoset II, Anscoset III (by Minolta)
- Ansco Autoset (by Minolta)
- Ansco Autoset CdS (Minolta)
- Ansco Memar
- GAF Ansco Memo II (half-frame, rebadged Ricoh Auto Half)
- Ansco Pix Panorama (by Haking)
- Ansco Regent
- Ansco Super Memar
- Ansco Super Regent
116 film No. 2A
BOX cameras
- 2A
- 2A Special
- 2A Craftsman
- 2A Buster Brown
116 film No. 1A
Folding cameras
- 1A Ready-set
- 1A Readyset Royal
- 1A Readyset Traveler
- 1A Junior
- 1A Folding
- 1A Speedex
- 1A Semi-Automatic
- 1A Automatic
- Ansco Junior Model A
- Ansco Shur Shot
118 film No. 3
Folding cameras
- 3 Junior
- 3 Folding
- 3 Speedex
120 film No. 2
BOX cameras
- 2
- 2 Special
- Ansco Shur Flash
- Ansco Shur Shot
- Ansco Shur Shot Junior
- Ansco Craftsman
- Ansco Craftsman Camera Kit
120 film No. 1
Folding cameras
- 1 Ready-set Juniorette
- 1 Junior
- 1 Junior de Luxe
- 1 Folding
- 1 Expert
- 1 Master Ready-set
- 1 Special Folding
- 1 Speedex
- 1 Super Speedex
- Ansco Arrow
- Ansco Commander (6×9)
- Ansco Isolette
- Ansco Marvel S-20 (made for Sears)
- Ansco Readyset Traveler
- Ansco Titan
- Ansco Speedex
- Ansco Super Speedex
- Ansco Viking 6.3
- Ansco Vest Pocket A
- Ansco Vest Pocket 2
122 film No. 3A
Folding cameras
- 3A Junior
- 3A Folding
- 3A Speedex
- 3A Folding Buster Brown
127 film
- Ansco No. 0 Buster Brown Special (box)
- Ansco Dollar Camera (box)
- Ansco Vest Pocket
- Ansco Vest Pocket Ready-set
- Ansco Cadet (127)
- Ansco Cadet II
- Ansco Cadet III
- Ansco Cadet Reflex
- Ansco Lancer
- Ansco Readyset
130 film
- Ansco No. 2C Junior
616 film
- Ansco Clipper
- (Agfa) Ansco Clipper Special
- Ansco Flash Clipper
- Ansco Pioneer (also badged as the “Ansco Jr. Press Photographer”)
620 film
- Ansco Admiral (variant of Rediflex)
- Ansco Anscoflex
- Ansco Anscoflex II
- Ansco Panda
- Ansco Plenax PB20
- Ansco Readyflash
- Ansco Readyset Special
- Ansco Rediflex
110 film
- Ansco 50 (made by Haking)
- Ansco 204
- Ansco 410
- Ansco 412
- Ansco 501
- Ansco 600 Flash
- Ansco Funpix 110
- Ansco Slim Pix
- Ansco Ultra Compact
- Ansco Vision Twin-Lens
disc film
Presumably all manufactured by Haking; equivalent Halina/Haking models may exist
- Ansco 105, Ansco 105 Telephoto
- Ansco 310
- Ansco 320
- Ansco 330
- Ansco 340
- Ansco 350
- Ansco 370
- Ansco 380 Telephoto
- Ansco 412 Tele-Flash
- Ansco Cadet 100
- Ansco Disc 103
- Ansco Fiesta, Ansco Fiesta Tele
- Ansco HR10, Ansco Memo HR10, Ansco HR10T
- Ansco HR15
- Ansco HR20
- Ansco HR25
- Ansco HR30
- Ansco HR40
- Ansco HR50
- Ansco HR65
- Ansco Ready Flash VR1
Non-Standard
35mm film
- Agfa Memo
- Ansco Karomat
- Ansco Memo
Sheet film
- Commercial View Camera
- Standard View Camera
- Universal View Camera
- Universal Junior View Camera
Solid Body
cameras
- Ansco Automatic Reflex
- Ansco Color Clipper
GAF-branded
35mm cameras
- GAF Ansco Autoset CdS
- GAF Ansco Memo II (rebadged Ricoh Auto Half)
GAF-branded
110 film cameras
- GAF 220 Instant Load
- GAF Personal Camera
- GAF Personal 2
GAF-branded
126 film cameras
- GAF Anscomatic 126
- GAF Anscomatic 326
- GAF Anscomatic 626
- GAF Anscomatic 726 (a rebadged Petri rangefinder)
- GAF Anscomatic Cadet
- Anscomatic Cadet Flash
- GAF Seventy Six instant load
GAF-branded
127 film cameras
- GAF Ansco 127
The Ansco Anscoflex is an unusual enamelled-metal pseudo TLR with a large lens cover which slides up to form the viewfinder hood. The viewfinder is almost 1:1 for the 6x6cm photos. It was built from around 1954 to a design by Raymond Loewy. It takes 6x6cm images on 620 film, wound by a large, ratcheted knob in the side. The Anscoflex II added two controls on the lower front panel: one is for close-focus and the other is a yellow filter.
The Ansco Shur-Flash was a basic box camera with flash attachment, introduced in 1953. It was a popular box camera with a water resistant fiber body covered in black imitation leather and a metal faceplate and viewer. It was capable of capturing eight 2 1/4 x 3 1/4 inch exposures on standard 120 roll film. The Ansco Shur-Flash camera was originally priced at $4.95 and the complete outfit with camera, Anscoflash Type III flash attachment, film and flash bulbs costs $9.75.
The Ansco Cadet features a large optical viewfinder, double exposure prevention incorporated in the film advance mechanism, red frame count view window in the back cover, wind film advance wheel on the bottom of the camera, drop out film compartment for easy film changing and easy color or black and white exposure setting. It was fitted with a fixed focus meniscus lens and film advanced loaded shutter with 1/50 of a second speed. The camera takes twelve exposures on standard 127 film.
The curiously alien-looking GAF Ansco 127 was produced after a 1967 adoption of the GAF trademark to supersede Ansco as the company’s camera brand. This model is a late and rather futile attempt to sell a simple snapshot camera using 127 film, given how rapidly the public had embraced drop-in loading 126 film cartridges, as used in Kodak’s wildly successful Instamatics. The 127 film is still advanced using a large knob on the bottom of the camera. Each roll yields 12 images 4×4 cm square.
FOUNDER: A merger of 7 companies
COMPANY NAMES:
1921: Amalgamated Photographic Materials Co. a merger comprising: the Rotary Photographic Co. Ltd, Paget Prize Plates Co. Ltd, Rajar Ltd, Marion & Co. Ltd, Marion & Foulger Ltd, A. Kershaw & Son Ltd and Kershaw Optical Co. Ltd.; 1929: the sensitive materials side of the company was reformed as APEM Ltd. (Amalgamated Photographic Equipment Manufacturers Ltd); 1929: the APeM company was sold to the Ilford company.
COMPANY ADDRESSES:
1921: London, Greater London, England; 1929: 3 Soho Square, London W.1.
A group of seven British companies made several of the well-known Bakelite cameras, including one of the earliest for roll film, the Rajar No. 6 folding camera (c. 1929).
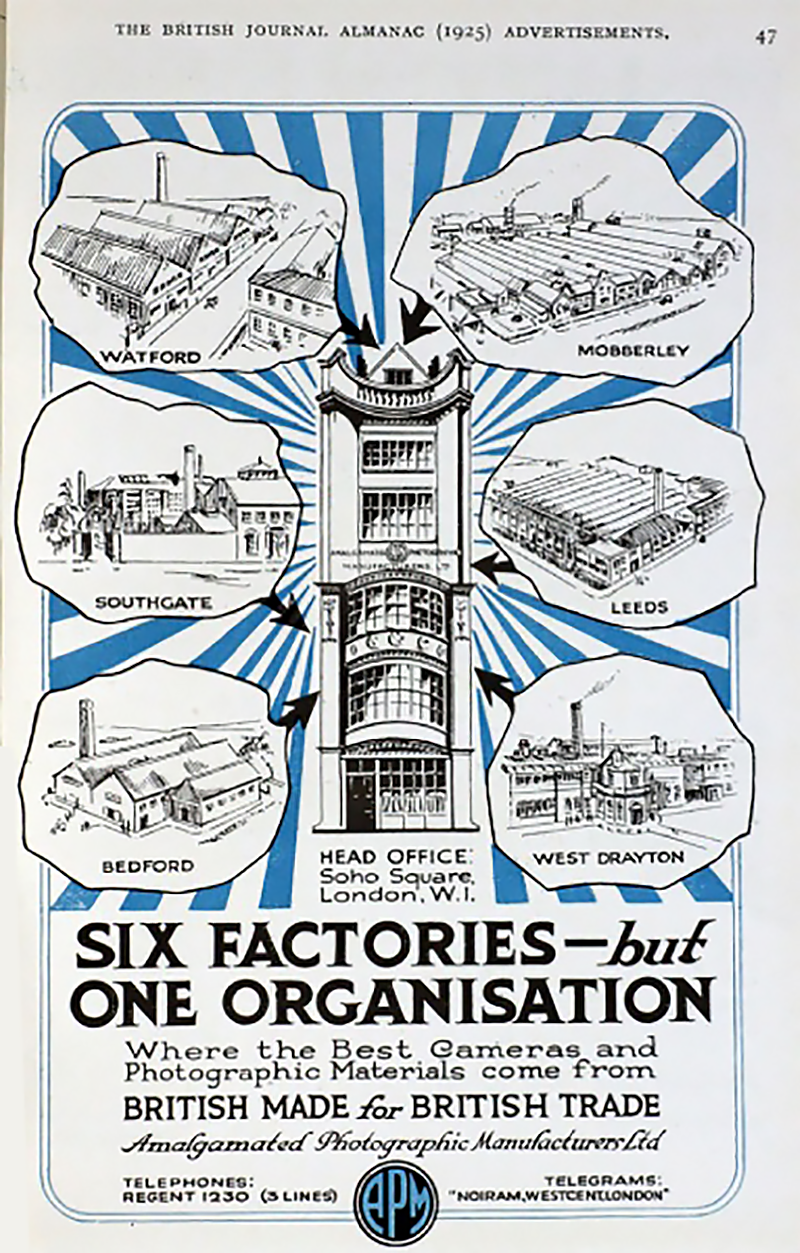
This advertisement in, among others, The British Journal Almanac drew attention to the APM merge.
In 1921, due to sharp competition and a desire to leverage the combined strengths of manufacturing and sales to pursue foreign and domestic trade, seven prominent British photographic and optical companies merged to form the Amalgamated Photographic Materials company (APM).
The original seven companies of the merger included:
- Kershaw Optical Co. Ltd.
- Kershaw & Son Ltd.
- Marion & Foulger Ltd.
- Rotary Photographic Co. Ltd.
- Rajar Ltd. (founded 1901)
- Paget Prize Plate Co. Ltd.
- Marion & Co. Ltd.
Later in the year of 1921, the firm took a leading shareholder position in Thornton-Pickard Manufacturing Co to combine the seven companies.
The company was capitalized with £1,100,000 (approximately $4,400,000) with a 10 percent stake being offered to the public.
In the 1922 BJA the directors are:
- E. Parke (Rajar, Rotary and Wiggins Teape, chairman);
- Abram Kershaw (Kershaw and Son, Kershaw Optical);
- Cecil Kershaw (Kershaw and Son, Kershaw Optical);
- L. Parke (Rajar, Rotary and Wiggins Teape);
- G. Pickard (T-P);
- C. Rich (Marion and Foulger);
- G. Thomas (Marion);
- George Sydney Whitfield (Paget);
- D. Whitfield (Paget);
- F.S. Rothwell (Rajar and Rotary, joint MD);
- Gerald M. Bishop (Marion, joint MD).
In early 1929 four of the seven, the ones which were in the film business, namely:
- Marion & Foulger Ltd.
- Marion & Co. Ltd.
- Rajar Ltd. (founded 1901)
- Paget Prize Plate Co. Ltd.
These companies became APeM Ltd. (Amalgamated Photographic Equipment Manufacturers). Shortly after this rebranding, the APeM company was sold to the Ilford company. The Watford premises remained in use by Ilford Ltd until 1962 and were finally demolished in the early 1980s.
The other part of APM were the camera manufacturers, which became the sales division for the manufacturing company of A. Kershaw & Son.
By 1942 Soho Ltd. was listed as a branch of A Kershaw & Son. Following the war, the Soho name re-emerged as Kershaw-Soho (Sales) Ltd. Around 1947 Kershaw-Soho was part of the J. Arthur Rank Organisation (through British Optical and Precision Engineers Ltd. a subsidiary of Rank).
The APM Program
- APM Altrex
- APM Box
- APM Beltrex
- APM Celtrex
- APM Feltrex
- APM Focal Plane Model A & B
- APM Focal Plane Model De Luxe
- APM Folding Plate Camera
- APM Folding Plate Camera Model Deluxe
- APM Laltrex
- Rajar No.6 (folding)
- Rajar No.6 (box)
- Rajar Betax (folding bed for plates)
- APM Reflex
- Soho Box
- Soho Junior Box
- Soho Studio Camera
- Soho Reflex
- Vest Pocket (early)
- Vest Pocket (127 strut folder)
- Vest Pocket De Luxe
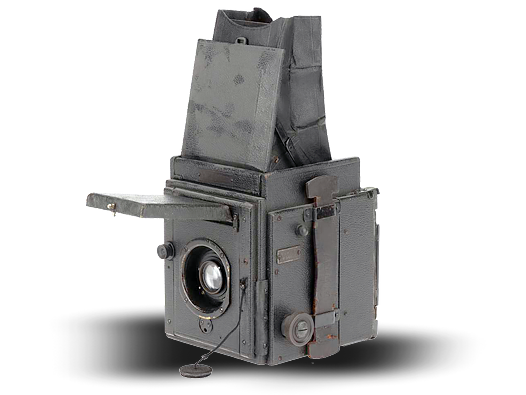
Large Format APM SLR Reflex-Camera.
FOUNDER: Charles Verschoor
COMPANY NAMES:
1931: International Radio Corporation (IRC); 1934: International Research Corporation; 1936: Argus Camera Co. as a subsidiary of IRC; 1944: Argus Inc.; 1949: Argus Cameras, Inc.; 1959: Argus was acquired by Sylvania Electric Products Inc; 1969: Sylvania company was sold and camera production suspended; 2003: Argus Camera Company, LLC as a subsidiary of Hartford Computer Group, Inc.
COMPANY ADDRESSES:
1931: 129 Fourth Avenue, Ann Arbor, Michigan, USA; late 1960s: South Carolina; 2003: Inverness, Illinois;
Argus was an American maker of cameras and photographic products. Argus is often credited for popularizing the modern 35mm film cartridge in the United States through its introduction of inexpensive but well-built cameras. Of all the American companies who produced cameras in the 20th century, Argus was second only to Kodak in terms of sales and brand recognition. If you consider that despite their tremendous success, Kodak was a film first company, whereas Argus largely stayed within the camera making business, so you could say that Argus was the most successful American camera company of all time.
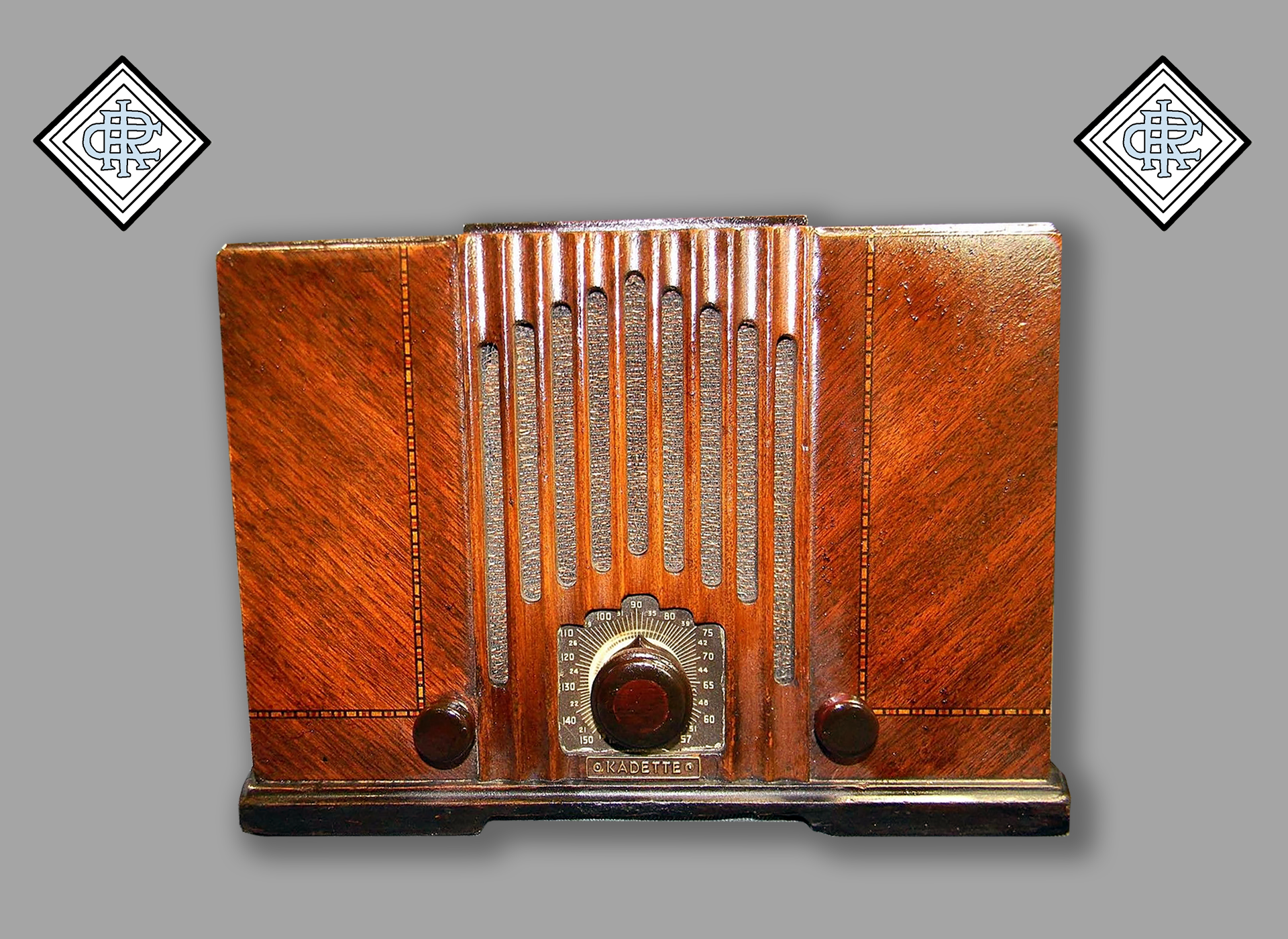
The Kadette Radio, made by IRC, 1933.
Argus was an American maker of cameras and photographic products, founded in 1931 by a group of 10 investors including Ann Arbor mayor, William Brown and businessman Charles Verschoor as the International Radio Corporation (later renamed the International Research Corporation) in the city of Ann Arbor, Michigan. The new company was located in the former headquarters of the Argus Furniture Company, located at 405 Fourth Street.
Back then, IRC made a variety of different radios, many of which had pioneering designs largely using Bakelite plastic, a relatively new material in the construction of radios and other electronic appliances. IRC’s products included the Kadette which was the first mass produced AC/DC radio. Bakelite was a very flexible product that could be made in a variety of colours, including a wood grain which gave it a look of a much more expensive radio. It sold extremely well and allowed IRC to release other Kadette products like the Kadette Jr, which was the world’s first pocket radio, and the Kadette Clockette which was one of the first clock radios.
In the first half of the 1930s, IRC’s radio business was so successful in that it was the only company in Ann Arbor that was able to pay dividends to it’s share holders during the Great Depression. Nearby Detroit was heavily hit by the recession, so in the entire state of Michigan, IRC was one of the few financial bright spots.
By the mid 30s as the depression dragged on, other competing radio manufacturers were able to make inexpensive radios that ate into IRC’s profits, so the company needed to find a way to diversify its product offerings. It was the middle of the Great Depression, and Verschoor, the president of the International Radio Corporation, was looking for that product that would keep his factory busy and his employees working during the slow periods of the radio business, which was highly seasonal.
On a trip to Germany, Charles Verschoor became familiar with a Leica camera and thought that with his expertise at making inexpensive items using Bakelite, that he could do for the camera industry, what he did for the radio industry: mass-produce a 35mm camera that could be sold cheaply yet was capable of making pictures of a quality suitable for the audience he had in mind.
So, Argus’s first product was the aptly named Argus A, a simple viewfinder camera that was one of the first non-Kodak cameras designed specifically to be used with Kodak’s 35mm daylight loading film cartridge (which has since become the international standard for 35mm film).
The Argus A was not a Leica. It didn’t have the fine machining or precision optics of the German miniature. But it didn’t have to. Like it’s radio division, the Argus Model A was an inexpensive Bakelite body camera that brought photography into a price range that didn’t have a lot of competition. The camera was ideal for the amateur market Verschoor envisioned.
The camera debuted with a list price of $ 10.00 (which meant it could be afforded by the average lower to middle class family) and more than 30,000 were sold in the first week. So successful was the model A, that the manufacturing building was called and addressed to as the Argus building. One of Argus buildings is Argus Museum holding permanent exhibition of Argus cameras.
Kodak’s position was seriously threatened
Eastman Kodak’s Kodak 35 model (a simple viewfinder camera and the very first camera designed for the 35mm cartridge) was losing significant market share to the technologically superior but much cheaper Argus C rangefinders.
Kodak hastily cobbled together a competing rangefinder camera in the shape of the Kodak 35 RF but it was simply too little, too late.
Despite being just a regular Kodak 35 with a rangefinder assembly, the 35 RF still ended up costing twice as much as the Argus C3 which continued to annihilate it in sales until Kodak gave up and ceased production of the 35 RF in 1948.
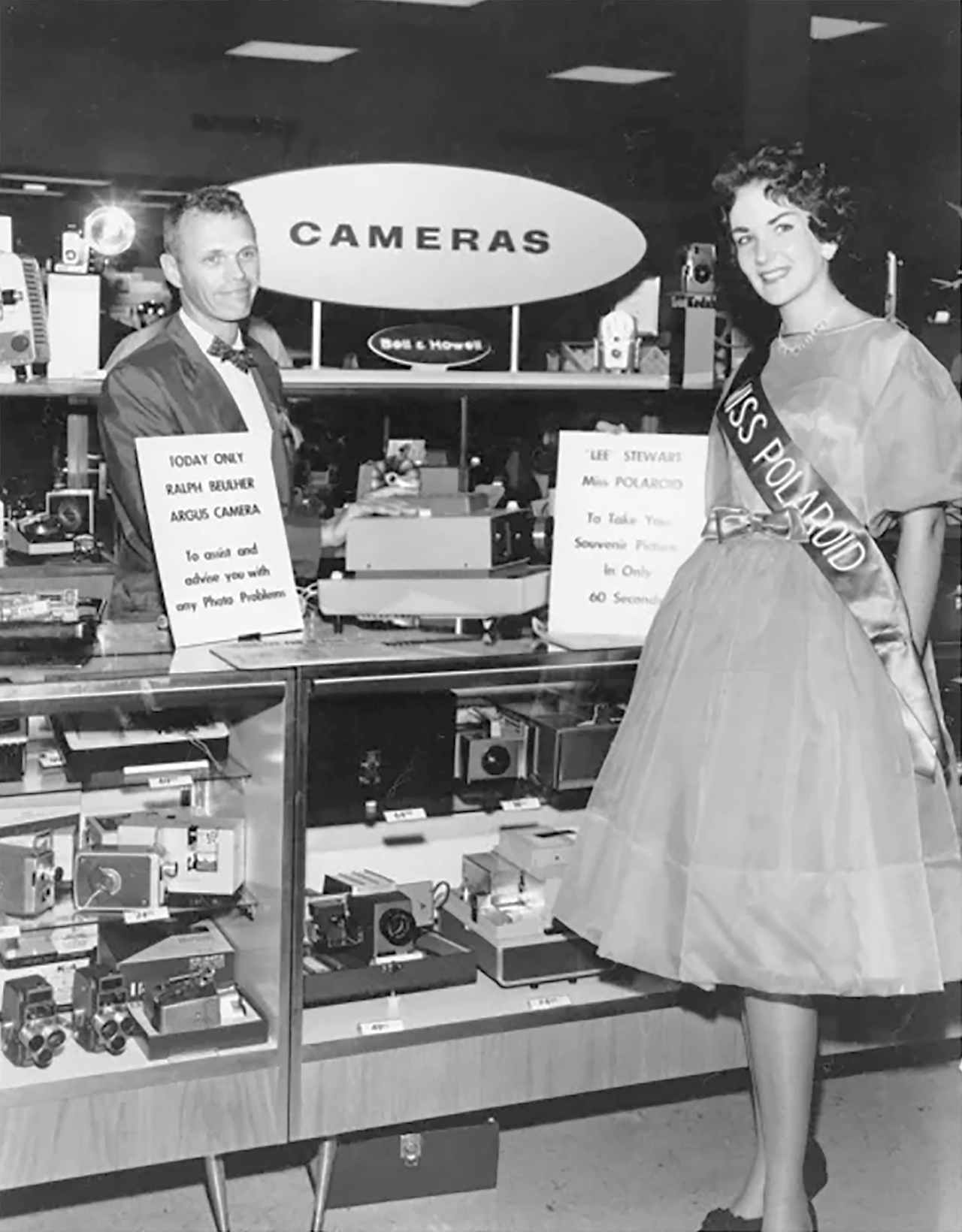
Shopping for Argus cameras in the thirties.
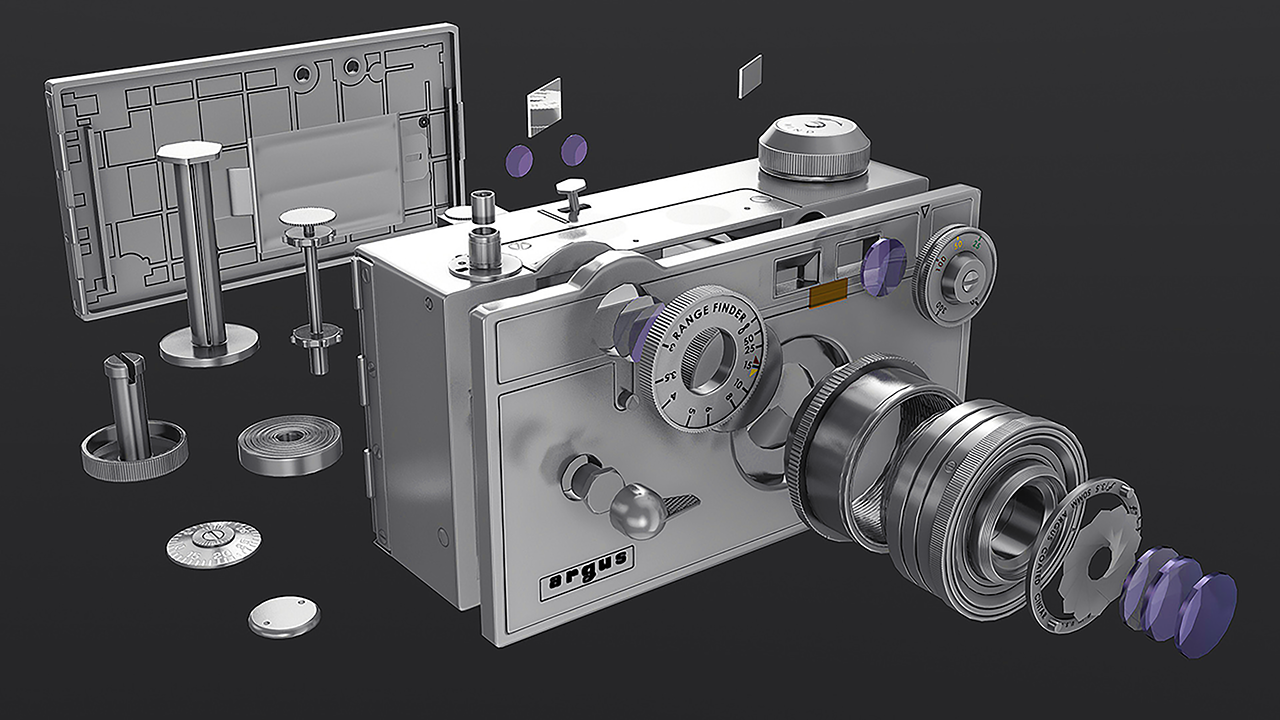
Exploded view of the Argus C3 camera.
The “Brick”
Argus’s new camera shared almost nothing with the earlier Model-A. Featuring a distinct brick-shaped Bakelite body with polished metal front and back panels, an interchangeable lens mount, and an uncoupled split image rangefinder, the Argus C was quite a step up from the Model A.
The Argus C-3, the venerable “brick”, would remain in production until 1966 and sell more than 3 million units in its three-decade life-span.
Perhaps the best feature of the Argus C was its price. Argus believed that the average American working family should be able afford a high quality and competent 35mm camera, so they priced the C at $25, which was the average weekly salary of a typical American family at the time. This price compares to $454 today which before taxes, adjusted for a 52-week year, compares to someone making $31,477 in 2019.
The Argus C saw several updates very soon after it’s release, the first being a redesign of the slow speed governor on the shutter. It was found that the original model’s “Fast/Slow” shutter was unreliable, and it was simplified to have a single shutter speed dial with speeds from 5 – 300 on it.
The C and C2 both debuted in 1938, with the C3 in early 1939. The original model was only offered one year, the C2 was produced through 1942, and the C3 was produced both before and after the war.
The new C-series was an immediate success and many were sold, but Argus was losing money as fast as they could make it. Company president, Charles Verschoor was a visionary businessman and keen salesman, but lacked financial prowess. A lack of proficient bookkeeping, overgenerous stock dividends, and elaborate corporate spending, caused the company to have a net loss, despite great sales. This resulted in Verschoor’s resignation from Argus in 1938.
From A to C
The design for the Argus Model A is most often credited to a Belgian designer, professor, and engineer named Gustave Fassin. Fassin was a bit of a freelance of sorts in the 1930s as a part time professor and designer for Bausch & Lomb, Kodak, Argus, and perhaps other companies.
The Argus A was the very first American made camera to use Kodak’s new 135 format 35mm film cassette.
The Argus A sold very well, so well in fact, that IRC decided to stop radio production altogether and focus entirely on producing cameras, slide projectors, darkroom equipment, and other photographic accessories. In 1938, due to the success of it’s cameras, IRC officially became known as the Argus Corporation and sold off it’s radio division to an entirely new company.
Sensing an even greater need to offer more competitive features in a camera at a low price point, later that year, Argus once again tapped Gustave Fassin for the design of their next camera. This later became the Argus C-3 in 1939, which would become the best selling 35mm camera in the world and possibly the most popular American 35mm cameras of all time. Although Fassin designed the camera, the shutter was built by Theodore M. Brueck, while working for the Ilex Optical Company of Rochester, New York.
Fun Fact: There actually was an Argus B produced in 1937, but it was just a variant of the Model A with a German Prontor II shutter and Argus 50mm f/2.9 lens. This model was produced for a very short time and only a couple hundred are thought to exist.
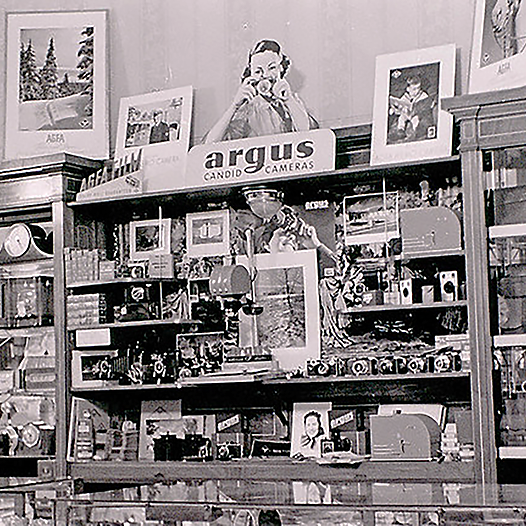
Argus cameras exhibited in a shop in the thirties.
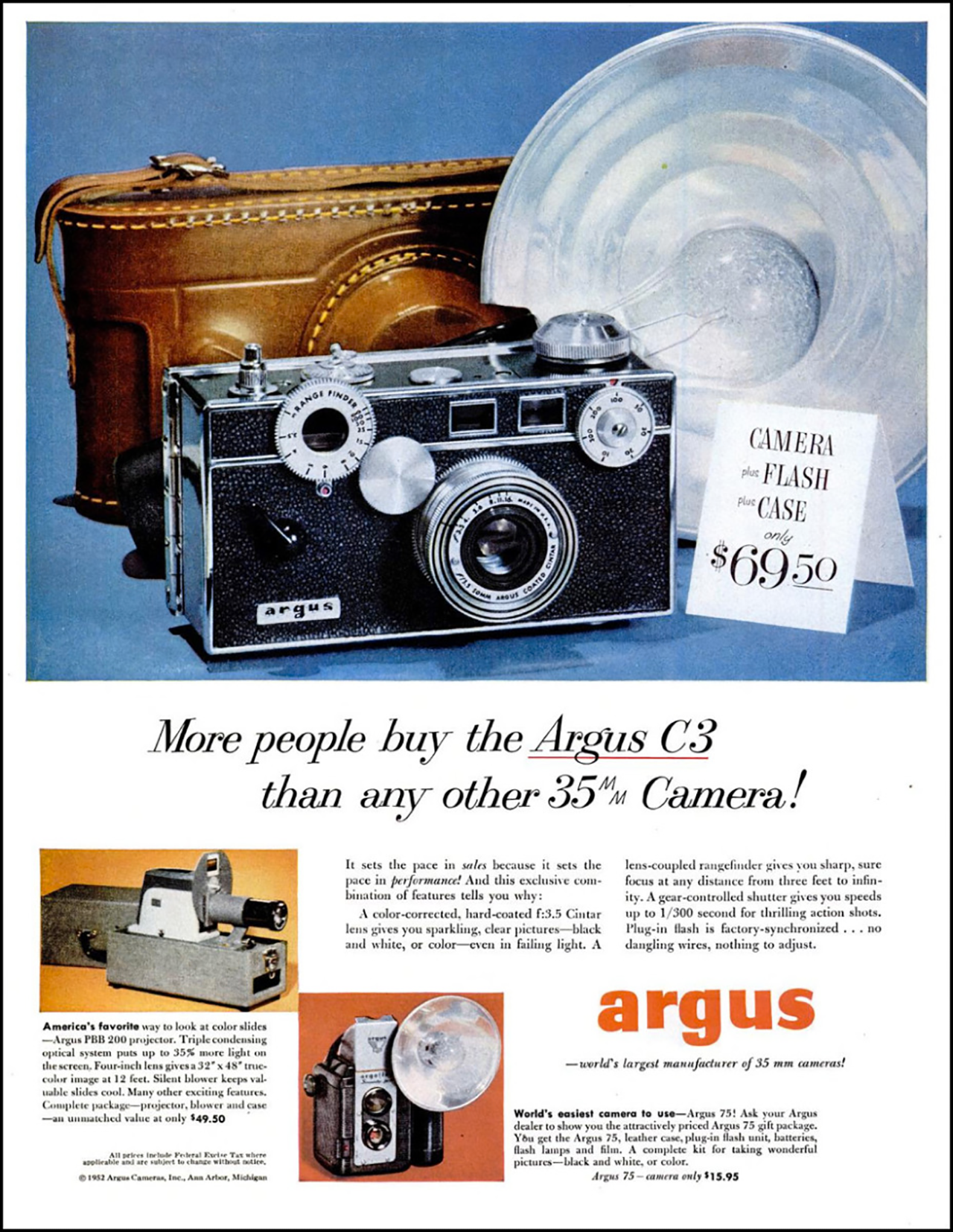
Argus-ad in LIFE-Magazine of May-5, 1952.
Argus in the fifties
The Argus C3 was tremendously successful in each year after the war through the end of the 1950s when sales started to decline. Although Argus never kept any detailed production numbers, we can reasonably estimate based on known serial number ranges that average annual sales during this time was somewhere around 150,000 cameras a year which is pretty incredible considering how long it was produced. Today, the Argus C3 remains one of the most iconic cameras ever produced. Not only is its appearance unmistakable, but it is a popular prop used in motion pictures which portray photography in the early mid 20th century.
By 1958, Argus was struggling to stay profitable and was on the verge of bankruptcy. Although they had released a few other, more advanced cameras such as the C33 and C4 series, people kept buying C3s, and Argus wanted to freshen up the design to make the camera more relevant, so that year, they released two new models, one called the C3 Standard, and the other the C3 Match-Matic. Both cameras got a redesigned Cintar lens with a more attractive and larger barrel, an accessory shoe on the top plate of the camera, a new shutter release, and came with an Argus selenium exposure meter for the accessory shoe.
The Match-Matic came with a unique black and tan body covering, and simplified the exposure system by eliminating any reference to shutter speeds and f/stops, replacing them with numbers on the shutter dial and lens that you were to add together to get an EV (exposure value). The included meter indicated its light readings using these EV numbers, so if for example, the meter returned a reading of 12, any combination of numbers on the shutter dial and lens that added up to 12, would result in a properly exposed image.
In 1959, Argus would be bought out by Sylvania Electric Products Inc. who themselves had merged with General Telephone to form General Telephone and Electronics (GTE). Under new leadership Sylvania started to outsource production of new Argus cameras to other German and Japanese companies such as Certo, Iloca, Petri, and Mamiya. The Argus V-100 was one such camera, which is just a rebadged Iloca Rapid IIL. By the mid 1960s, the Argus Match-Matic and Standard were the only Argus cameras still manufactured in the United States, and in 1966, after a run of 28 years, production came to an end. By the late 1960s, Argus would close up shop in Ann Arbor and relocate to South Carolina.
New management and military applications
Under new management led by businessman Robert D. Howse, Argus reinstated radio production and quickly turned to military contracts for the US war effort in Europe.
In the early 1940s, the International Research Corporation (which renamed itself as Argus Inc. in 1944 after its cameras) became profitable again producing binoculars, gun sights, radio power supplies, remote controls, telescopes for tank crews, and other products for the United States and its Allies.
They also increased capacity for the Argus C3 35mm rangefinder and started producing a medium format twin lens reflex camera called the Argoflex.
By 1942, business was very good for Argus, with profits up to $4.8 million from a net loss in 1938. After the war, Argus sought to remain dominant in it’s consumer camera divisions but planned to continue it’s work with American and foreign militaries, using its experience to continue to develop optical and radio products.
This was rather unique in the optics industry as most companies who turned to military production during the war, ceased all government contracts afterwards, but not Argus. Argus was so invested in the war effort, in 1945 they produced a propaganda video to showcase the company’s efforts in the American war effort. The video was digitized by the Ann Arbor District Library.
The aftermath of World War II caused a disruption in supply of cameras and other optical equipment from Germany which caused many American companies to take up the challenge of building all new models to compete for the American photographer’s buying dollar. Established companies like Kodak and ANSCO released new cameras in the late 1940s, as did some newcomers like Clarus and Vokar, but the Argus C3 remained a best seller.
When camera production resumed after the war, the Argus C3 immediately went back on sale in late 1945. Initially, the very first post war cameras were identical to the pre-war versions, but by July 1946, cameras were produced with coated Cintar lenses and other minor cosmetic variations. The price had gone up too.
The November 1949 issue of US Camera shows an ad for the C3 with case and flash unit for $78.08 after tax, quite a lot higher than the original $25 price tag of the first model. Of course the higher price wasn’t due to greed, rather inflation and a disruption of supplies were likely contributors.
In 1949, the company was renamed to Argus Cameras, Inc. Due to hard times and under the new management of Robert E. Lewis, all of the established camera lines were ended, including the ground breaking Model A, with the only exception being the popular C3 camera continuing.
With the ending of older lines new designs were slowly introduced to fill in the missing gaps. Among them was TLR Argoflex. However, competing with higher quality lines from Germany and cheaper lines from Japan, limited the market for Argus to recoup. Some products of other makers were sold under Argus brand name.
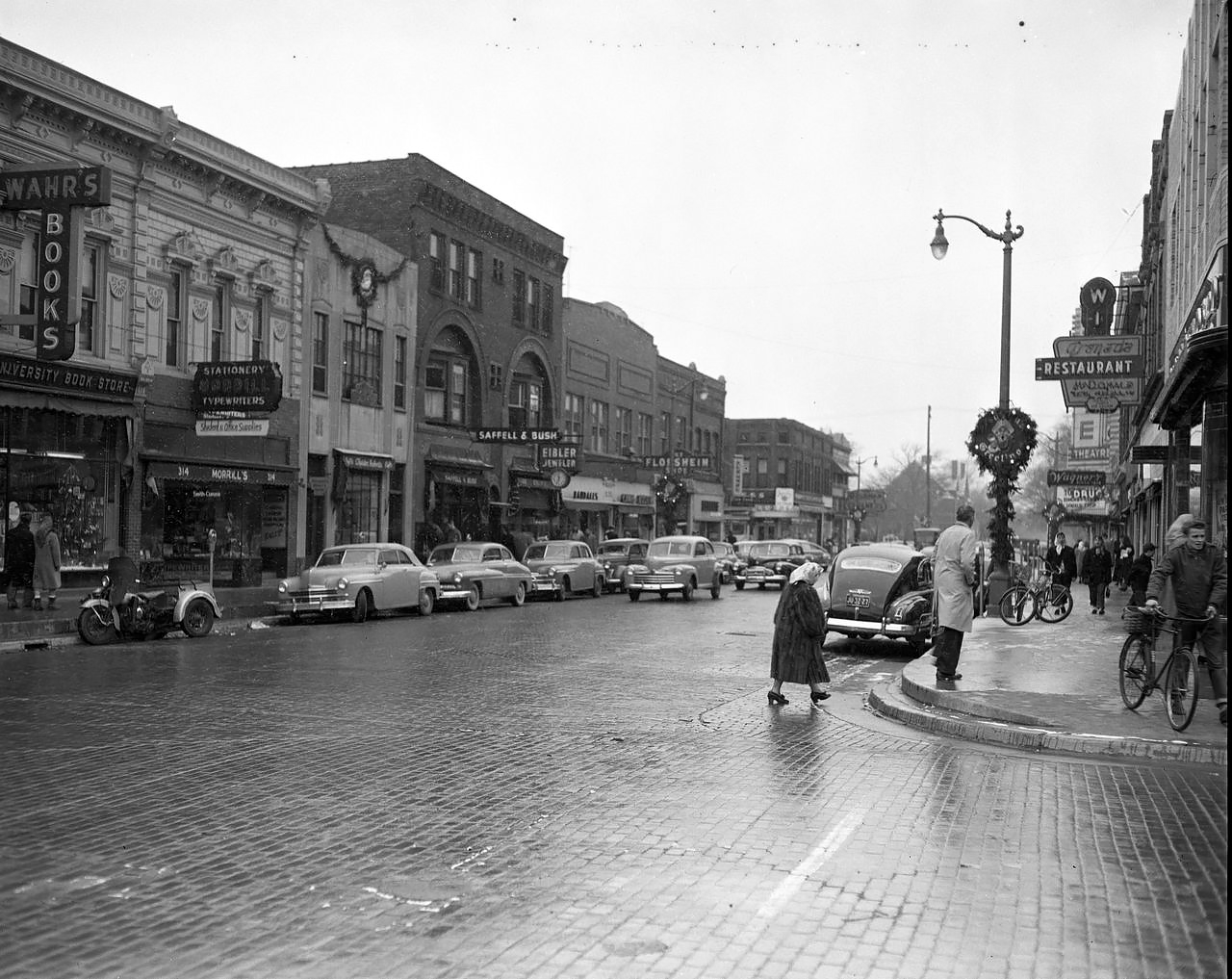
State Street in downtown Ann Arbor in 1949. Ann Arbor News archives courtesy of OldNews.AADL.org
Although rebadged cameras from other manufactures continued to be sold under the Argus name throughout the 1970s. The Argus name would continue to linger about for the next several decades as a badge applied to cheap Instamatic and pocket cameras. By the 2000s, it was even applied to some Chinese made digital cameras too, but nothing remotely that ever came close to the C3.
Argus did not truly return until it was re-established in 2003 in the Chicago suburb of Inverness, Illinois as Argus Camera Company, LLC as a subsidiary of Hartford Computer Group, Inc. The new Argus Camera Company, develops, manufactures, and markets digital photographic and video cameras in the United States. Its products include mega pixel carabineer digital photographic cameras, VGA carabineer photographic cameras, digital photographic cameras, and mega pixel digital video cameras. After its resurrection, Argus doesn’t appear to be selling any consumer products at the moment.
Argus had two cameras for children developed in partnership with TEAMS Design. The cameras, the Bean and Sprout, won a Bronze 2009 IDEA award from BusinessWeek and the Industrial Designers Society of America in addition to an Appliance Design 2009 EID award.
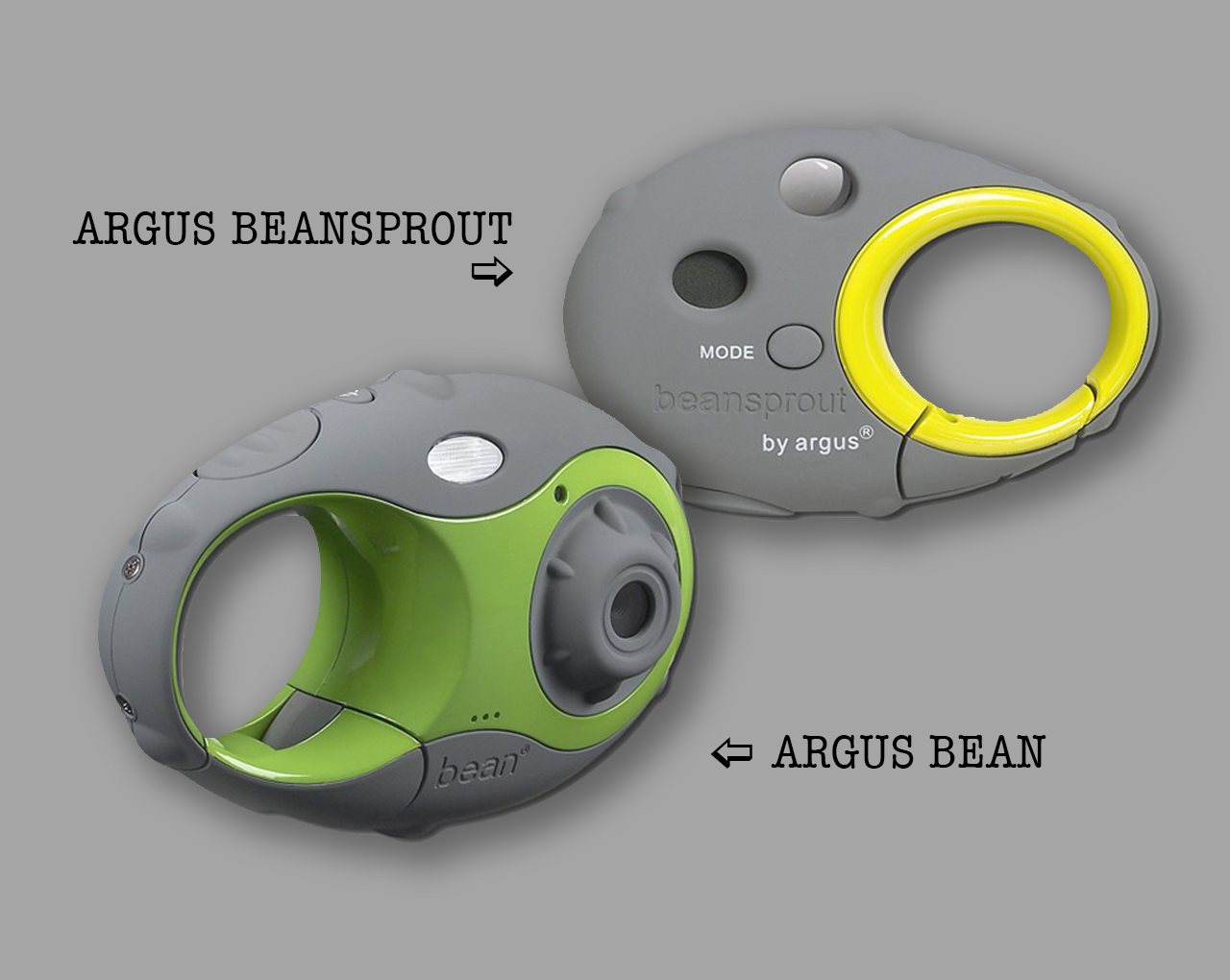
List of Argus Cameras
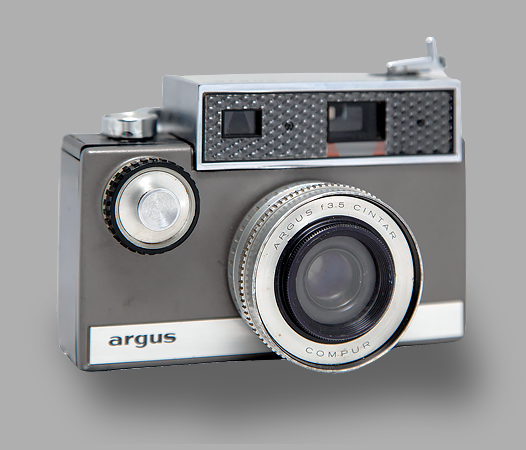
Argus Autronic 35
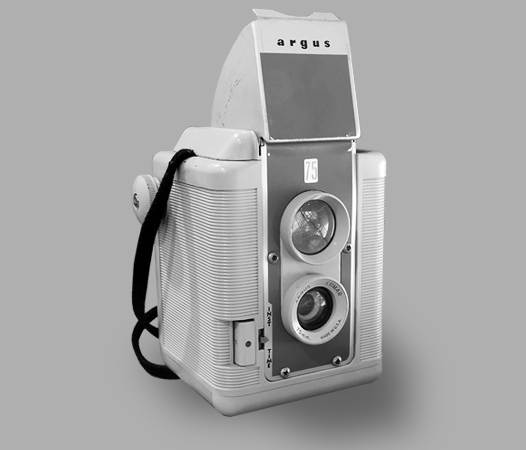
Argus Model 75.
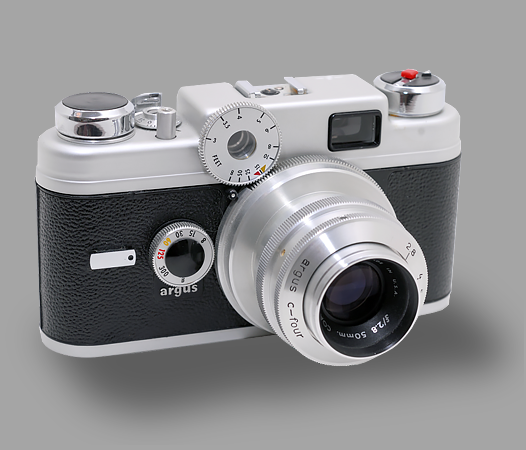
Argus CR4.
A-series
- Argus A
- Argus A2B
- Argus A2F
- Argus AA
- Argus A3
- Argus AF
- Argus B
- Argus CC
- Argus FA
Autronic series
- Autronic 35
- Autronic C3
- Autronic I
- Autronic II
Instant Load series
- Argus Instant Load 164
- Argus Instant Load 270
- Argus Instant Load 364
- Argus Instant Load 374
C-series
- Argus C
- Argus C2
- Argus C20 (C-Twenty)
- Argus C3
- Argus C3 Matchmatic
- Argus C3 Golden Shield
- Argus C33
- Argus C4
- Argus C4 R
- Argus C44
- Argus C44 R
- Argus Carefree
- Argus CC (ColorCamera)
- Argus CR 1
- Argus CR 2
- Argus CR 3E
TLR-series
- Argus 40
- Argus 75
- Argus Super Seventy-Five
- Argus Argoflex 40
- Argus Argoflex E
- Argus Argoflex EF
- Argus Argoflex EM
- Argus Argoflex II
- Argus Argoflex Seventy-Five
Other Factory series
- Argus 21 “Markfinder”
- Argus A-Four
- Argus C-twenty
- Argus Model K
- Argus Model M
- Argus M 3 Cinetronic
- Argus M 3 Matchmatic
- Argus SLR
- Automatic 8
Other Factory series
- Camro 28
- Delco 828
- Flash Sensor 235x
- Lady Carefree
- Minca
- Minca 28
- Minca C2
- Seventy-five
- Showmaster 822
- Solid State Electronic
- Tele- 600
Later rebadged cameras
- Argus 127 (Whitehouse Products)
- Argus/Cosina 35 Compact (Cosina)
- Argus (SLR) (Mamiya)
- Argus CR-1 (Chinon)
- Argus C2/C3 Electro (Haking)
Later rebadged cameras
- Argus C4M Electro (Haking)
- Argus CR-2 (Chinon)
- Argus CR-3E (Chinon autoexposure)
- Argus STL 1000 (Cosina; Petri)
- Argus/Cosina STL 1000 (Cosina)
- Argus/Cosina EC 2000 (Cosina)
- Argus V-100 (German OEM)
- Argus Auto 35mm (integral flash reflector; Mamiya)
- Argus Automatic 35 (“Electric Eye 35mm”)
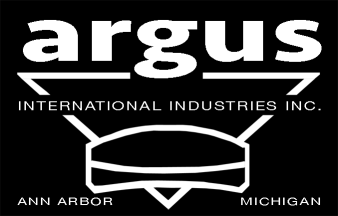
As a successful company, Argus became a major contributor to Ann Arbor’s economy and built several production facilities within the city. Several of these buildings still exist and now function as office space or as part of the University of Michigan.
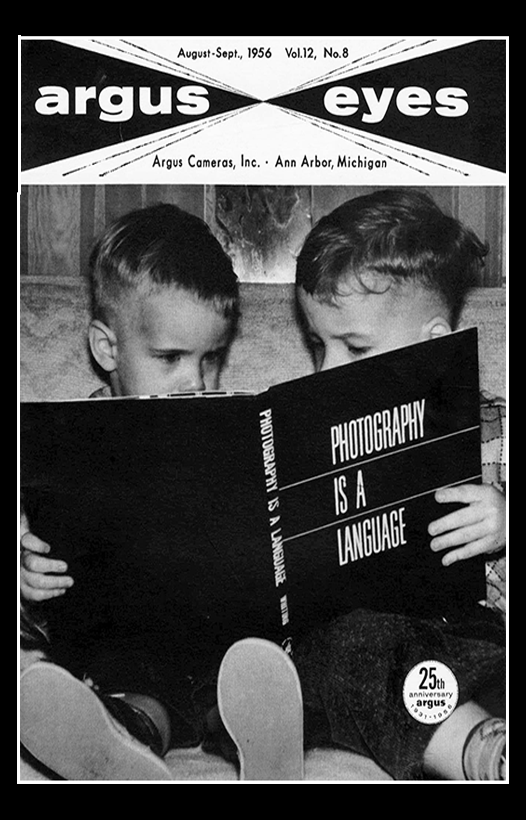
During the 1940s and 50s, working for Argus was a big deal. Thousands of employees from the Ann Arbor area worked for the company, receiving generous profit sharing incentives. The company had a newsletter called “Argus Eyes” that helped connect each employee with the direction of the company. Argus sponsored many athletic events, even having its own employee basketball and bowling teams. The company had elaborate Christmas parties and other social gatherings, often sharing news of marriages and child births in it’s company newsletter. It was a great honour to work for Argus during this time.
The Argus Museum, located on the second floor of 525 West William, Ann Arbor, Michigan, features products manufactured by the Argus camera company and tells the stories of the company, the people involved and showcases unique collections connected to Argus. The museum is housed in the Argus I Building, which was one of the facilities where Argus products were manufactured.
The mission of the Argus Museum is to collect and preserve Argus Camera Incorporated products (including those manufactured under its prior names), publications and history of the company and its employees, to research the products and the people who were involved in the development and manufacturing of these products, to insure these collections are available for others to research, and to interpret and display the collections for public viewing to promote knowledge and appreciation of Argus.
Established in 1987 with the acquisition of the Don Wallace Collection, the museum’s holdings include the rare 75, A4, C3 and C4 camera “giants” (large models used in trade shows), experimental model 12s, each with a different type of collapsing lens; and, various colours of the model A camera, favourites of collectors.
Variations of the Model C3 camera (often referred to as The Brick), a common model of which over two million were sold, are on view. Employee memorabilia, including profit-sharing documents, employee identification badges and items related to the many sports and activities that Argus sponsored are also on display. Products that were manufactured under the company’s names of International Radio Corporation, International Research Corporation, International Industries Incorporated, Argus Incorporated, and finally as Argus Camera Incorporated, are included in the displays. Many of company’s cameras, projectors, viewers, meters and accessories, as well as darkroom equipment, manufactured throughout its history are exhibited.
Through military artefacts, the stories of the company’s contributions to World War II and the Korean War, are told. Sighting devices, prisms and lenses are displayed. Included in the collection is a M72 Telescope used in Sherman Tanks, and a M18 sight used with Britain’s 57mm anti-tank gun (the Britain Six-Pounder).
The museum’s archives include photographs, documents, instruction booklets, advertisements, correspondence and manuals. However, probably the greatest wealth of information can be found in the Argus Eyes, the company newsletter.
Although articles on government contracts, profit sharing and new product lines are included, the majority of what is written involves personal employee milestones including births, marriages, deaths, retirements and anniversaries. Returning soldiers and those who were lost, social events, vacation reports, and humorous stories of the daily lives of Argus employees are often featured in articles.
The Argus I Building’s character lends itself to showcasing artwork. The museum presents photography exhibitions and features local and regional artists, particularly those who create images using film. The museum also hosts meetings, book signings, and an Argus Collector Group (ACG) Fall Conference.
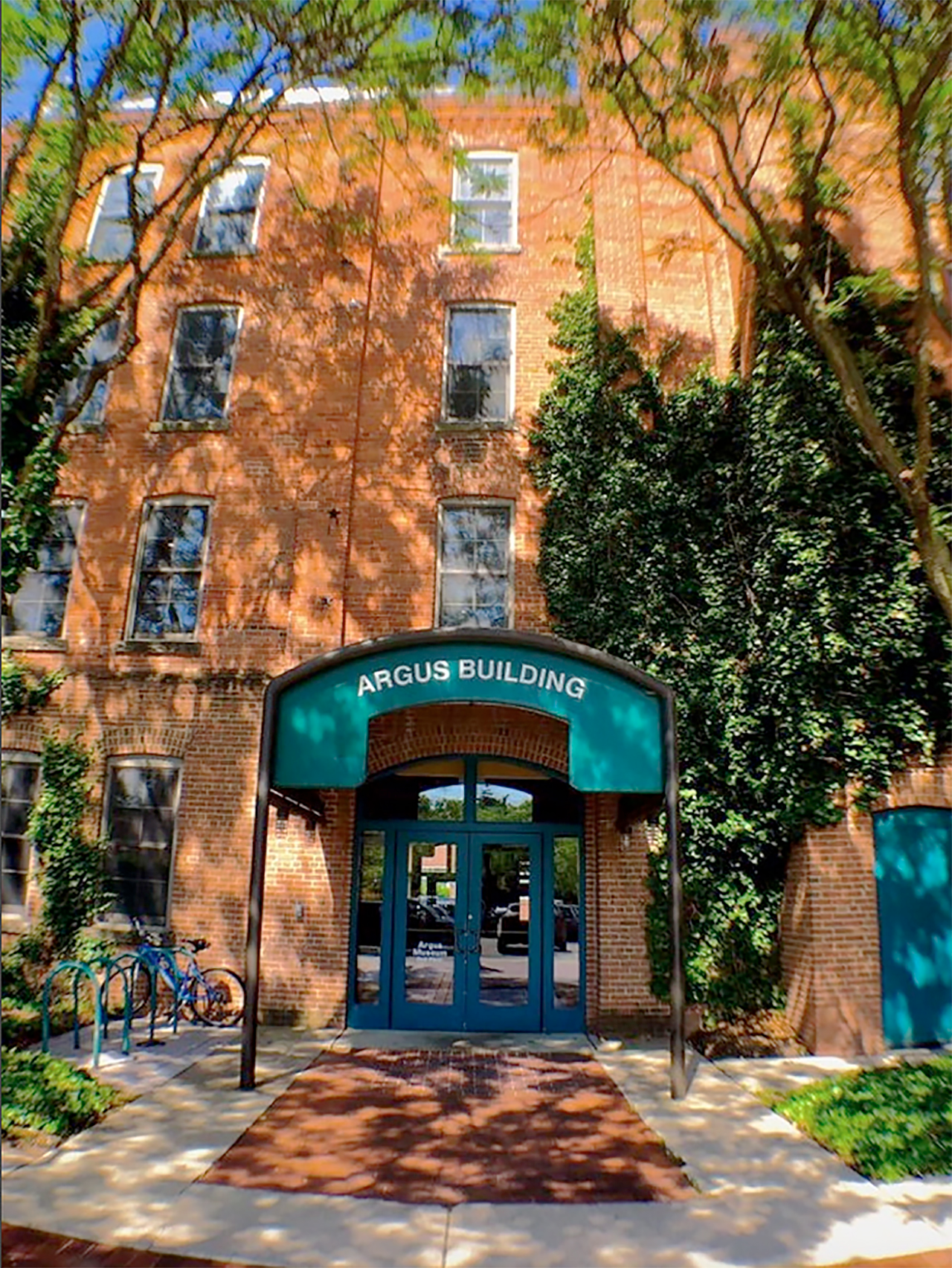
The Argus I Building, 535 West William Street, now an office building, is home of the Argus Museum.
Originally the building was a wood structure and built c.1866. It first housed a cabinet-making shop and then a furniture manufacturing company. A four-story brick building was erected in 1879. In 1881 the original wooden structure was veneered with brick and joined to a four-story brick building by a brick addition.
The International Radio Company (which would later become Argus Camera Incorporated), purchased the building in 1931. Several additions were constructed between 1940 and 1951 to accommodate increased business, particularly military contracts. In 1963, the University of Michigan became owners of the building. First Martin Corporation and O’Neal Construction purchased the building in 1983, and after rehabilitation, reopened the building in 1987.
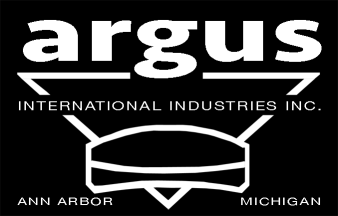
FOUNDER: Daniel Prenn
COMPANY NAMES:
1936: Artima Export Ltd.; 1948-1950: production of Arti-Six cameras came to an end.
COMPANY ADDRESSES:
1936: 121, Charlotte Street, London, W.1.
No matter how well I’ve searched, I can’t find anything on the internet about the company Artima Export Ltd. At least no other than their name on the leaflet of the Arti-Six camera. The information about Artima Export Ltd is limited here to some information about the camera and the company that manufactured the camera: Truvox Engineering Ltd.
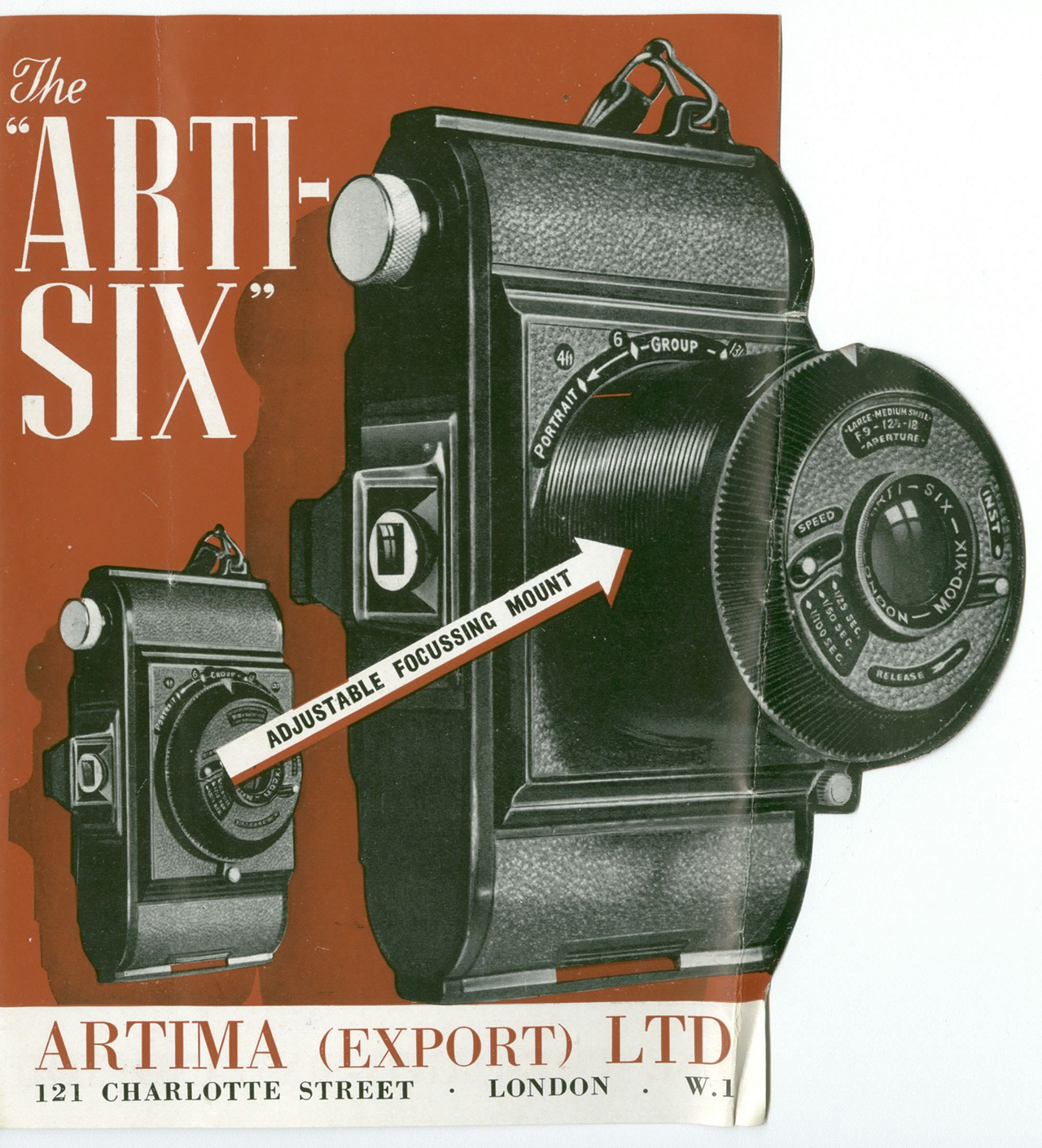
Daniel Prenn was a Byelorussian-Jew who studied civil engineering in Germany and became a world class, top-seeded, tennis player representing Germany in the Davis Cup during the 1930s before being exiled under the anti-Semitic Nazi regime, fleeing to Britain in 1933. He was ranked the World No. 6 for 1932 by A. Wallis Myers, and the European No. 1 by “American Lawn Tennis” magazine. He was a runner-up for the mixed doubles title of Wimbledon in 1930.
Later, as a prominent Jewish businessman, he nurtured other small Jewish- refugee businesses and over the next 50 years created one of Britain’s largest military electronics and communications ’empires’ through the merger of his Thermionic Products business with Racal Electronics, while his family-run Truvox Floorcare business became a leader in its own right.
The formative years of Truvox are still unclear, suffice to say the business was founded by Daniel Prenn, whose first business in Britain was assembling fountain pens. It appears he may have bought a ready-made company, Truvox Ltd, formed in October 1928, and the Universal Radio & Gramophone Co, of Kentish Town, from where Truvox originally operated. His more famous Truvox Engineering Ltd business was formed in June 1936.
Truvox pioneered plastic extrusions during WW2 and through the 1950s, with items such as gramophone pick-ups and loudspeaker housings, electrical appliances as well as this brief venture into simple moulded cameras, which from 1950 to 1956 included the Bakelite Wembley Sports Camera. It was named after Truvox’s address at Wembley, London. The Wembley Sports was launched at the British Industries Fair in 1950 and takes eight 6x9cm images on 120 film. It sold at an introductory price of £4 17s and 6d. The full story about Truvox is told on this site under “Truvox”.
Wembley, Arti-Six, Grand Manitou, Artima Photo-Magic, all children of one family
The Wembley Sports Camera was very similar to the Arti-Six and French Labelled Grand Manitou which were produced by Truvox for Artima Export Ltd. The two cameras have different lens apertures, but little else is different, apart from the embossed names and the Wembley Sports lacking a strap-lug which is present on the Arti-Six.
Focussing of the Wembley Sports Camera is achieved by turning the whole lens unit which screws in and out of the body (helical focussing) with click-stops marked on the camera body at 4ft, 6ft, 13ft and infinity. The lens screws into the body when not in use. It has a curved film plane which allows sharper focussing in the corners of the frame.
The lens is an 85mm f/11 London Sportar, stopping down to f/16 and f/22. The B/I shutter covers speeds of 1/25s, 1/50s and 1/100s. It has a reverse Galilean viewfinder. It is a fairly robust camera weighing in at 418g.
In 1948-1950 production of Arti-Six cameras came to an end. Truvox continued from 1950 to 1956 with the Wembley Sports using moulds and tooling from the production of the Arti-Six. Both these 120 rollfilm cameras bear a close resemblance to the smaller Artima Photo-Magic which takes 127 size film.
The Artima Photo-Magic was a viewfinder camera made almost entirely of Bakelite. The Art Deco style is shown by the stepped, curvilinear shape of the Bakelite body. The design first appeared in 1935 and was produced in France.
The French versions of this camera are identified by the letters ‘P'(Pose) and ‘I'(Instant) adjacent to the shutter release. The later (1950) British models had ‘T'(Timed) and ‘I'(Instant) adjacent to the shutter release and had British made inside the back. They were distributed by Boumsell who also sold the camera under their name. It was also manufactured in Bordeaux red.
It is a very simple design with a meniscus lens which is marked Photo-Magic and No 4065. The same markings are seen on all versions of this camera. There was also an identical Photo-Miami camera.
• Arti-Six – • Grand Manitou – • Photo-Miami – • Photo-Magic – • Wembley
FOUNDER: Kumao Kajiwara
COMPANY NAMES:
1919: Asahi Kogaku Goshi Kaisha; 1938: Asahi Optical Company, Ltd.; 1948: restart after WWII – Asahi Optical Company, Ltd.; 2002: Pentax Corporation; 2008: Pentax merged with the major optical company Hoya Corporation.
COMPANY ADDRESSES:
1919: Toshima, Tokyo; 1947: Magome, Tokyo; 2023: Ota, Tokyo.
Originally, Asahi Pentax produced lenses for several camera manufacturers. In 1951 the company began to manufacture its own cameras. The first of these, the Asahiflex, was also the first Japanese 35mm SLR. Many Pentax cameras were also sold under the ‘Honeywell’ name, by the Honeywell company, which was a distributor, not a manufacturer.
The ‘Pentax’ trademark was acquired by Asahi from Zeiss Ikon in 1957.
Although Asahi Optical Co. Ltd is noted for producing Pentax cameras and lenses, it did not, in fact produce a camera of its own until some thirty-two years after it was founded. The company was originally called ‘Asahi Kogaku Goshi Kaisha’, and it was established in November 1919, by Kumao Kajiwara, at shop premises in a suburb of Tokyo, called Toshima, in order to produce spectacle lenses.
In 1923 the company began to manufacture lenses for cine projectors for another maker. The following years saw further development of the lens making side of the business and, in 1932, Asahi commenced to make lenses for the Molta Camera Company, now Minolta, for a 6.5 cm x 9 cm folding plate camera, called the ‘Arcadia’. The following year, 1933, they began to supply Konishiroku, now Konica, with a range of single element and anastigmat lenses for their Pearl and Pearlette series of cameras.
In 1938 the old company changed its name to Asahi Optical Company Limited. At that time, it undertook government contracts to produce optical instruments, which it continued to do so up until the end of World War II. Shortly before and during the Second World War, production was entirely dedicated to the Japanese armed forces. Little is known about the products that were made during this period. It is believed that Asahi was the supplier of military optical devices, mainly for the Japanese Imperial Air Force, in much the same manner as Nippon Kogaku was for the Imperial Navy.
In 1945, most of the Asahi’s factory buildings in Tokyo were destroyed. This also caused the loss of many, if not all, documents describing the activities of the company during the Taisho Era (which lasted from 1912-1926) and pre-war and wartime Showa Era (1926-1945).
After the war, the company was forced to dissolve. This situation only lasted until 1948 when it started again as the Asahi Optical Company, Ltd. (Asahi Kogaku Kogyo Kabushiki Kaisha, the current official name), led by Mr. Saburo Matsumoto. Since Japan was still under strict US government control, Japanese companies were only allowed to produce consumer goods for the export. This earned hard currency which could be used to help purchasing imported food and medicine, essential to rescue Japan from starvation.
The company decided to start with the production of binoculars like the small 6×15 Jupiter Jr. series. They also continued their work as a subcontractor with the production of lenses and lens elements for other camera and binocular companies. This was almost a copy of the situation before the war, when Asahi produced lenses for Chiyoda Kogaku Seiko K.K (Minolta) and Konishiroku Shashin Kogyo K.K. (Konica).
At the late 40’s and early 50’s, the Asahi-employees were working very hard to produce 25,000 lenses per month for the Mycro series of “Hit” type subminiature cameras made by Sanwa Shokai Co., Ltd. At peak time, the lens elements for the Mycro camera were polished and coated in the Asahi factory at daytime and then brought to Mr. Saburo Matsumoto’s house at night to have them glued together with optical balsam.
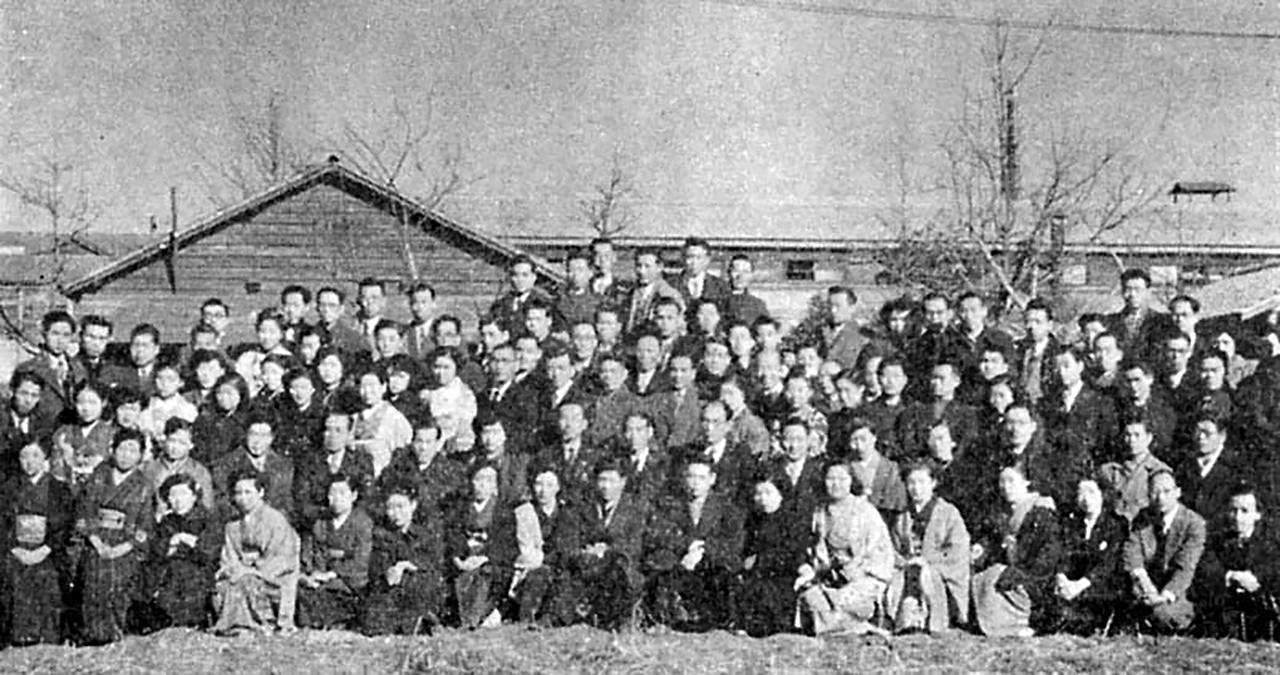
“Family shot” of Asahi Opt. employees at Tokyo factory in 1953. You can spot Mr. Matsumoto in the middle of the second row, with Ryohei Suzuki at his left and Nobuyuki Yoshida at his right.
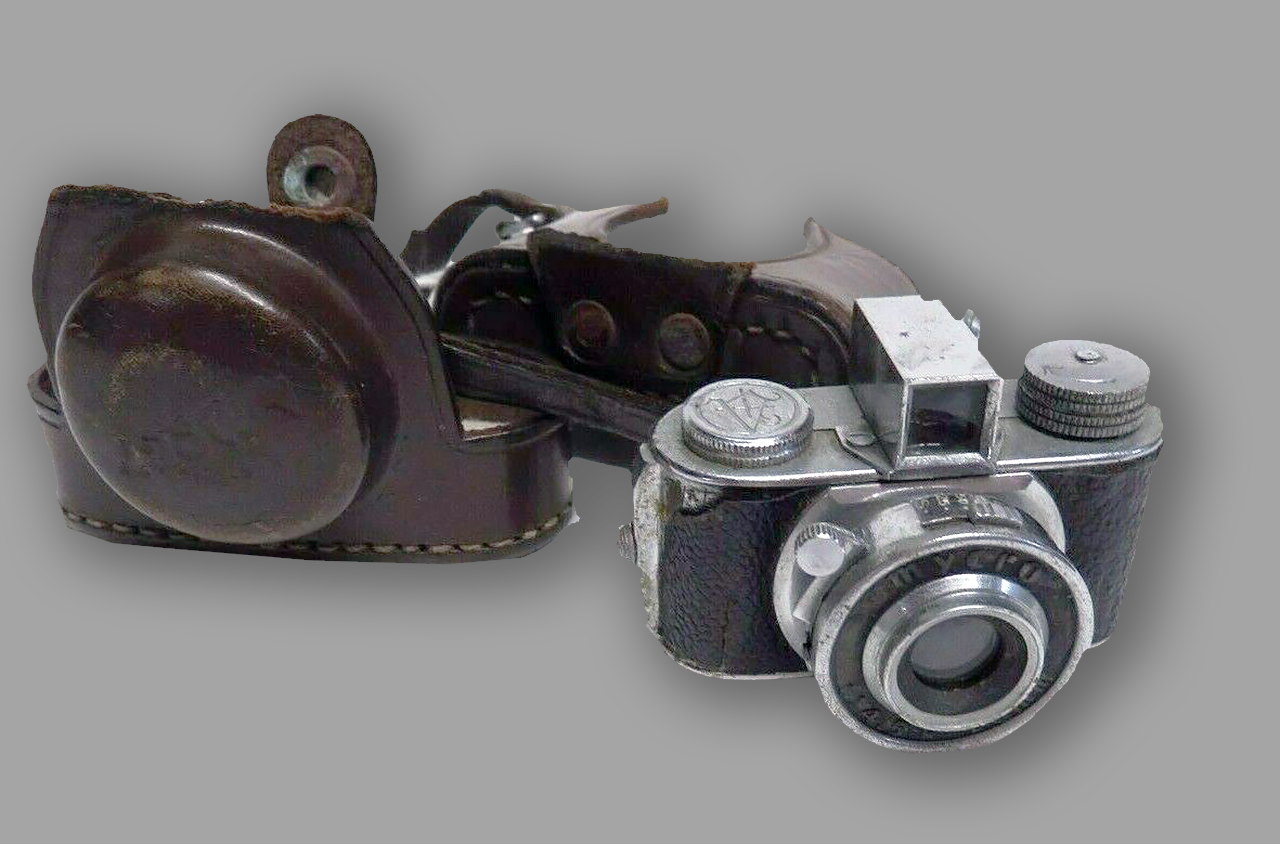
Very rare 1938 Japanese Mycro Subminiature Spy Camera.
The period around 1950 marked the return of the Japanese photographic industry to the vigorous level of the late 1930s, and its emergence as a major exporter. The newly reborn industry had sold many of its cameras to the occupation forces (having had far more disposable income than the Japanese) and they were well received.
The Korean War saw a huge influx of journalists and photographers to the Far East, where they were impressed by lenses from companies such as Nikon and Canon for their Leica rangefinder cameras, and also by bodies by these and other companies to supplement and replace the Leica and Contax cameras they were using. Around that time, Japan experienced a 35mm camera boom.
As these models steadily gained acceptance, the then President of Asahi Optical Company, Saburo Matsumoto, impressed by the overwhelming success of the 35mm cameras made by other companies like Nippon Kogaku K.K. (Nikon) and Canon Camera Company, soon decided that time was right to produce Asahi’s own consumer camera to make the best use of their experience in mechanical and optical processes.
However, he refused to follow other manufacturers who were making almost blatant imitations of Rolleiflex TLRs and Leica rangefinder cameras. Instead of doing that, Mr. Matsumoto was groping for an entirely new product. So it was no surprise that he finally set his sights on producing a 35 mm single-lens reflex camera, which he strongly believed was the future of photography. This was a very bold idea, because there were only a few cameras of this type known at that time (such as the Contax S).
The Pentax trio
The research on the Asahi camera was started in 1949. Time passed, and after several false starts there still was no camera ready for production. Mr. Matsumoto realized that he needed new skilful and imaginative persons to complete the project. But where to find them? As mentioned above, Asahi still produced lenses for other manufacturers. On one occasion, Mr. Matsumoto met Mr. Ryohei Suzuki, who worked since 1933 for a lens manufacturing company related to Konishiroku. They immediately became friendly with each other. Mr. Matsumoto asked Mr. Suzuki to help him to fulfil his dream to produce Japan’s first 35mm SLR camera. This was an offer Mr. Suzuki couldn’t resist.
Mr. Suzuki was very experienced with designing lenses, but he realized that he only had scarce experiences with designing cameras. To solve this problem, Mr. Suzuki introduced his former colleague Mr. Nobuyuki Yoshida to Mr. Matsumoto. Mr. Yoshida had also worked for Konishiroku, but he left that company to start his own camera repair business. He agreed to enter the design team, but he refused to enter the company at this stage. Needless to say, he also had no experience with manufacturing or designing single-lens reflex bodies. Nevertheless, they decided that Mr. Yoshida would design the body, and Mr. Suzuki would design the lenses.
Now that the design team was complete, they started with the construction and design of the camera. Their only reference was an old German 6 x 6cm Reflex-Korelle which Mr. Matsumoto got before the war. Although the trio knew about the existence of the Kine-Exakta and Contax S, they could not use them for reference purposes because these cameras were, at that time, never officially imported into Japan. Only a few Kine-Exaktas have been used by Japanese photography enthusiasts, but it was not known if any of these cameras survived the war. Due to these limitations, the design team had to start virtually from scratch.
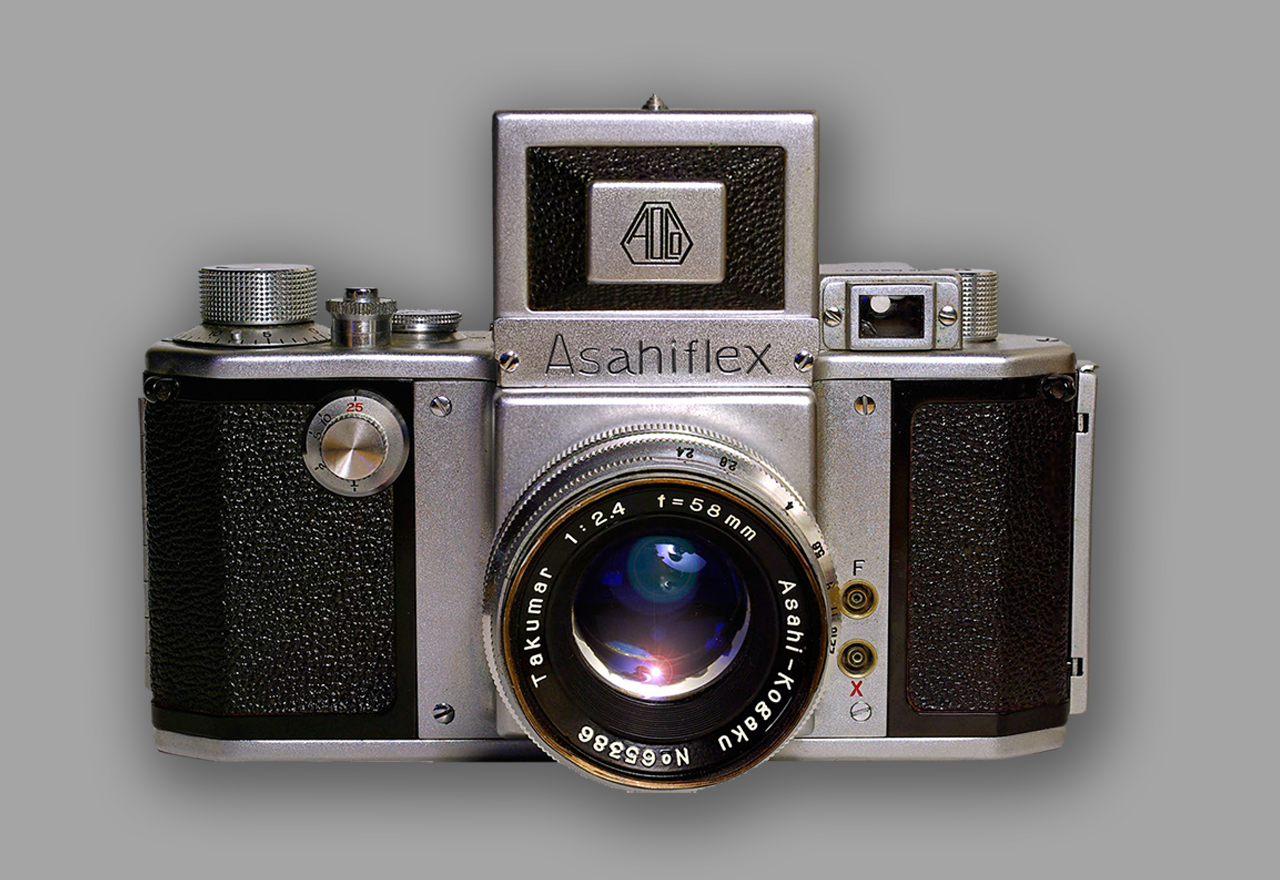
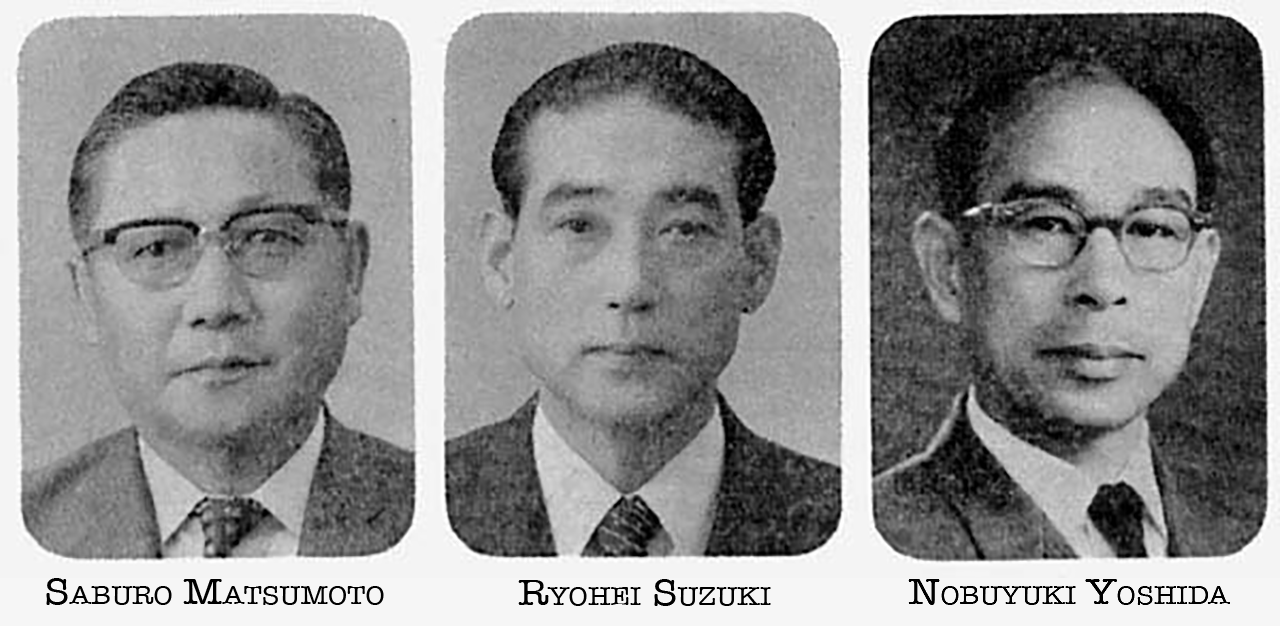
From left to right, Saburo Matsumoto, Ryohei Suzuki, and Nobuyuki Yoshida were responsible for the first Asahi SLR prototype, the Asahiflex in 1949.
Asahi’s first camera modeL
The design team encountered many problems during the design process, since there were no standard parts available. They had to make each single part by hand. It took six months before the first trial model of the Asahiflex was completed.
Mr. Suzuki and Mr. Yoshida showed the camera and one of the first photos that was taken with it to Mr. Matsumoto, who was so delighted with the results that he wanted to start the production at once. The only problem was that Mr. Yoshida had neither enough equipment, nor space for mass-producing cameras.
The trio gathered and it was agreed upon that Mr. Yoshida officially entered the company and that the camera would be manufactured at the Oyama factory of Asahi Optical Co.
It took another year before Asahi completed three fully working samples of the Asahiflex in October, 1951. They were looking for stores to sell the camera, but Mr. Matsumoto, who went to many stores to show and demonstrate the Asahiflex, was very disappointed because no-one seemed to be interested in the camera.
Finally, the optical division of Hattori Tokeiten K.K. (known as the watch manufacturer Seiko Corporation today) was very interested in the Asahiflex and this company decided to sell and distribute the camera for Asahi. Production of the Asahiflex I was started in February, 1952.
According to the company, the initial production rate was 200 units per month, and at a later stage this number was increased to 500 per month. The camera was surprisingly successful, but many of the early Asahiflex units were returned to the factory due to problems with the flash synchronization.
In May, 1953 followed an improved model, the Asahiflex IA. This model featured a mechanically improved shutter and an extra flash contact for X synchronization.
No more black-outs
In 1954 followed the most important improvement to solve a big drawback of the Asahiflex: the black-out in the viewfinder after the picture was made. There was a need for a quick return mirror. This feature, also designed by Mr. Nobuyuki Yoshida, marked the arrival of the second series of the Asahiflex in the form of the Asahiflex IIB.
The quick-return mirror is important because in the old situation the photographer never knows if he took a photo at the right moment. For all he knows, he may or may not have missed the situation. The only thing he knows for sure is that his viewfinder shows a black image (this feature was, quite funnily, called a “safety viewfinder” by manufacturers from Germany because the black viewfinder image showed that the shutter was not cocked).
The quick-return mirror was not a new feature (although Asahi incorrectly stated that in their advertisements and publications), because there were a few other cameras with this mechanism such as the Duflex from Hungary. However, these early solutions, ingenious as they were, were also often prone to mechanical problems and hard to manufacture in mass production. So Asahi could rightly claim that they developed the first reliable and commercially successful quick-return mirror.
The Asahiflex I series had a semi-quick return mirror which was directly coupled to the shutter release button. When the release button was pressed, the mirror flipped up and the shutter was triggered. The mirror only returned when the shutter button was released after a picture was made. This mechanism created problems at slow shutter speeds, because it is not unthinkable that the photographer could release the shutter button before the actual photo was made, resulting in a partially obscured photo.
An improved Asahiflex II
In the Asahiflex II instead, the mirror mechanism was coupled to the shutter mechanism and driven internally. In this situation, the mirror automatically returns to its resting position after the picture was made. This unique mechanism, which was in all aspects fault-free, was admired highly in the market and the Asahiflex II became relatively popular.
The importance of the quick-return mirror in the Asahiflex II was recognized widely. Other Japanese companies adopted it quickly, making it an industry standard, but German manufacturers were unwilling or unable to improve their products, a situation which also added up to the collapse of the German optical industry in the 60’s and 70’s. But that had still to happen in 1960, when Mr. Nobuyuki Yoshida received the second Science & Technology Agency Director’s Award for his invention and improvement of the quick return mirror.
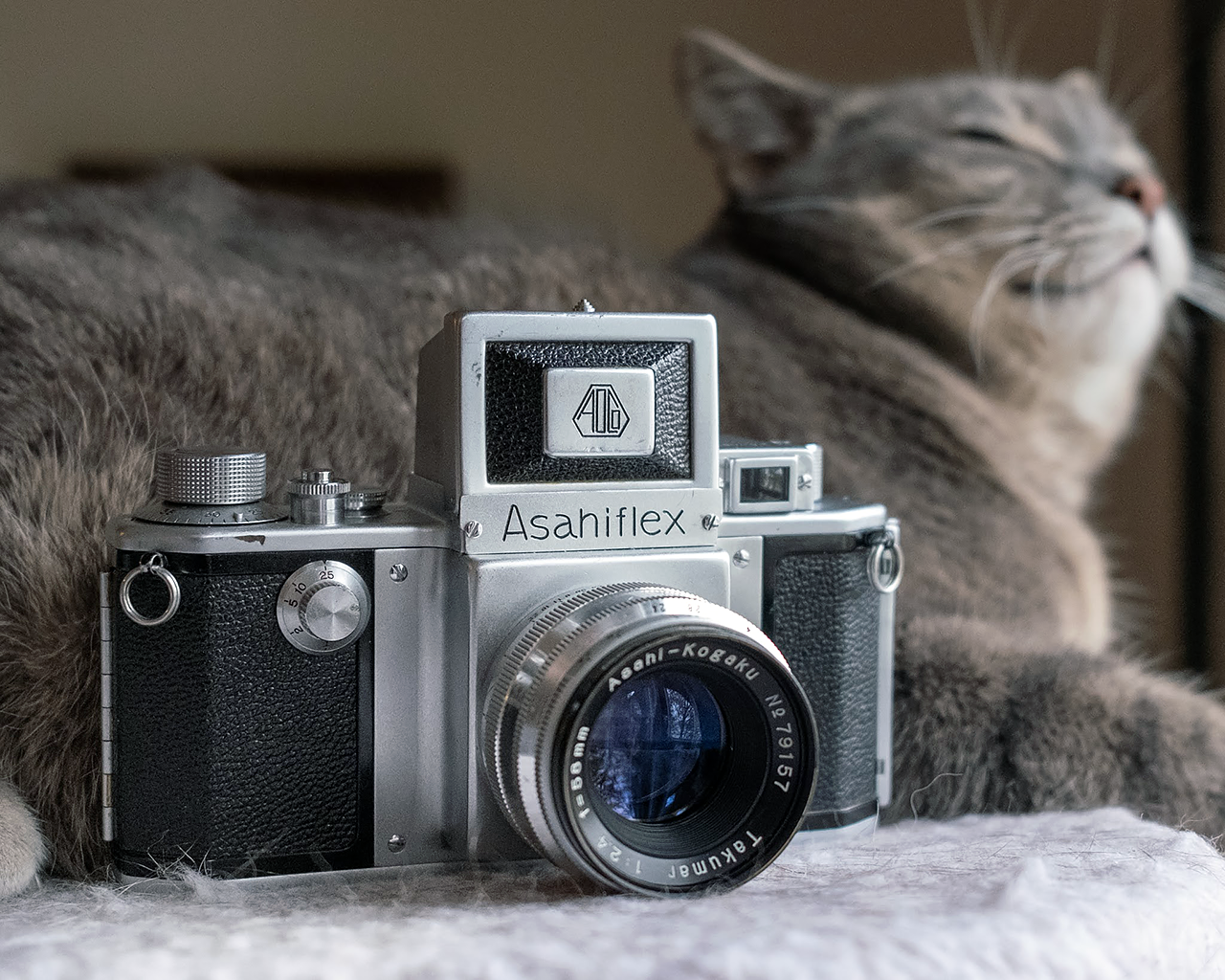
The Asahiflex IIA came out in 1955, and is a slight revision to the original Asahiflex, which came out a few years earlier in 1952. The 1955 IIA model has a few features the 1952 version does not, such as an instant-return mirror and slow shutter speeds.
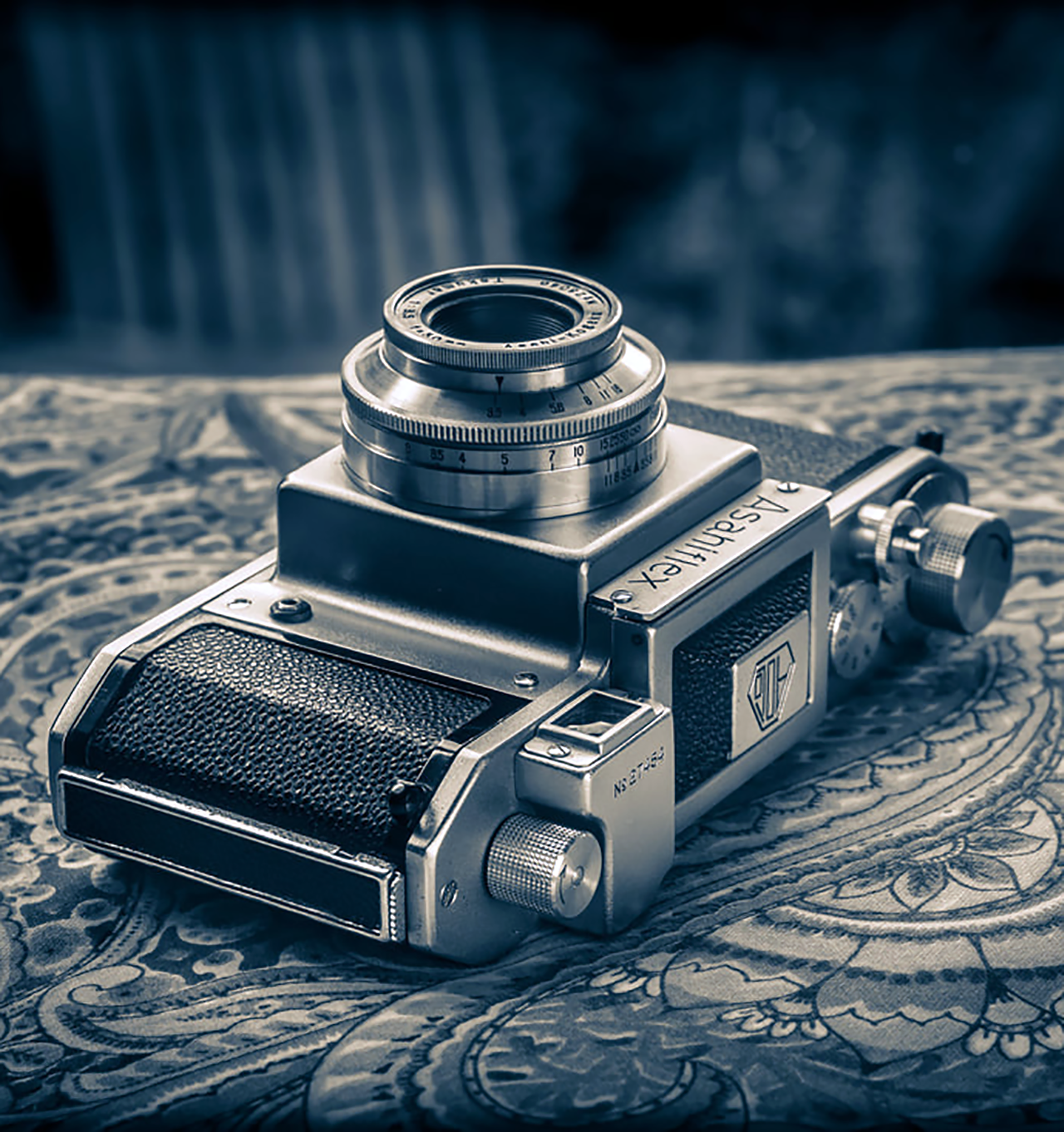
Asahiflex-1.
Another novelty: the pentaprism
The Asahiflex was a fine quality camera, but it was very difficult to use the Asahiflex in a vertical position and taking pictures of moving objects was almost impossible. The problem was recognized by Asahi, and in 1954 Mr. Yoshida made a prototype that featured a pentaprism.
That prototype was improved between 1955 and 1956, and in 1957 Asahi Optical Co. scored another success by introducing the Pentax, which incorporated a built-in pentaprism giving a bright focusing screen image, which was the correct way up and unreversed.
This model was the first Japanese SLR to incorporate a pentaprism system and as such heralded the dawn of a new photographic era. The days of the rangefinder camera were numbered.
The name “Pentax” was originally a registered trademark of the East German VEB Zeiss Ikon (from “Pentaprism” and “Contax”) but, as all Germans patents were annulled with the country’s defeat, the name “Pentax” was taken by the Asahi Optical company in 1957.
Since then the company has been primarily known for its photographic products, distributed under the name “Asahi Pentax” (equipment was imported to the United States from the 1950s until the mid-1970s by Honeywell Corporation and branded “Honeywell Pentax”). The company was renamed Pentax Corporation in 2002. It was one of the world’s largest optical companies, producing still cameras, binoculars, spectacle lenses, and a variety of other optical instruments. In 2004 Pentax had about 6000 employees.
The early pentaprisms were made by hand, so it was not a surprise that their price was very high. This would add up to the price of the camera, making it unreachable for the ordinary consumer which was, and has always been, the main target for the products made by Asahi.
However, it was clear that a pentaprism for a SLR camera was a must, or Asahi would surely lose their market share. This simple conclusion resulted in the Asahi Pentax Original from 1957. Asahi optical tried to keep the manufacturing costs as low as possible, but it wasn’t until the production of the Asahi Pentax S2/H2 that Mr. Tohru Matsumoto, son of Mr. Saburo Matsumoto, who followed a course at the Massachusetts Institute of Technology (MIT), invented a cost-effective method for mass-producing pentagonal roof prisms.
TTL-metering and entering the medium format market
The next breakthrough came in 1960, when Asahi Optical showed a prototype camera at Photokina, which took exposure measurements through the taking lens. The camera was called the Spot-Matic and caused a sensation at the show. With the standard 50mm lens fitted to the camera the exposure meter took a central 3 degree reading from the focusing screen of the in focus subject.
However, with their reputation for not introducing any development onto the market until it had been fully tried and tested under all possible conditions, the much changed, and slightly renamed Spot-Matic, was not put on sale until almost four years later in early 1964. Although Asahi had invented the TTL metering system, another manufacturer, Topcon, with the RE Super, went on sale in April 1963. The Topcon featured a semi-silvered mirror with the metering cell on the back of it.
In 1966 Asahi Optical had produced one million SLR cameras since the first Asahiflex of 1952. It took them another three years, until 1969 to reach two million, such was the popularity of the Pentax. Also in 1969 a radical change of direction took place, when the professional Pentax 6 x 7 was introduced. This new model looked like a king sized 35mm SLR, and handled almost just as easily. It could accept either 120 roll film or 220 roll film, and was an overnight success!
In 1975 another important change took place in the development of Pentax camera design. The 42mm universal screw mount had reached the end of its useful life with the Pentax Spot-Matic F and ESII models. No less than three new models were introduced at once in 1975. They all featured a new, wider lens mount designated K-bayonet.
The end of the story
In the fifty years that Asahi Optical Co. have been making cameras, they have produced about two hundred different models of single lens reflexes and compact cameras, including specialised types, catering for all photographers from professionals to absolute beginners. They have been the pioneering force behind many of the developments that today we take for granted, and quite rightly, are amongst the top five manufacturers. Their products have always been in great demand, both to use and to collect.
Over the years Pentax have always kept faith with the buying public and have never indulged in planned obsolescence. Indeed, lenses from the very first Asahiflex of 1952 can still be fitted to and used successfully, via adaptors, on their latest autofocus SLRs. No other manufacturer today can make that claim.
Pentax was once one of the largest manufacturers of cameras in the world, but these times are long gone. The company (which was then called Asahi Optical) began to lose ground in film times, and then hopelessly late with the transition to the “digit”.
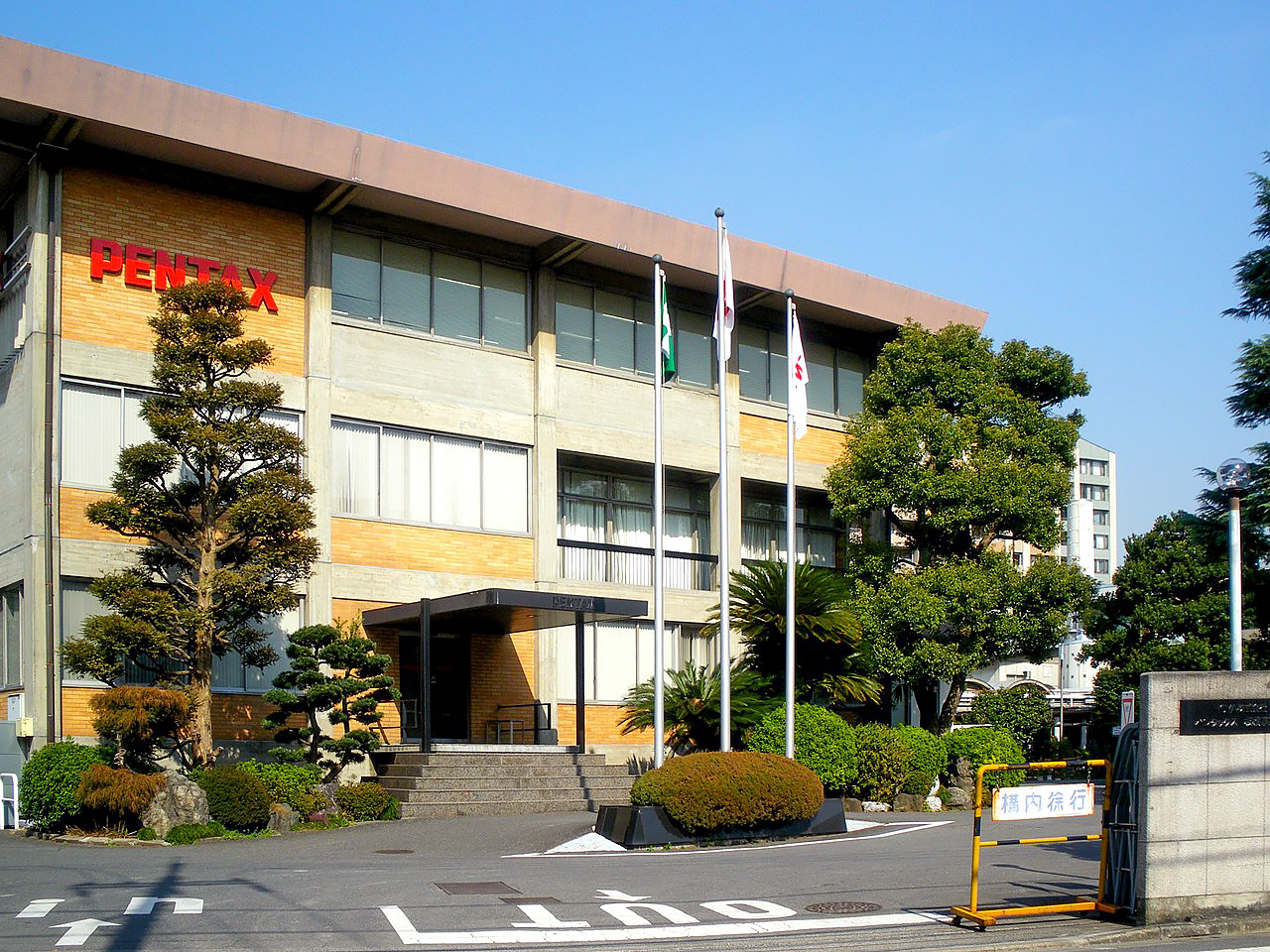
Asahi Pentax head office in Itabashi-ku, Tokyo 2009.
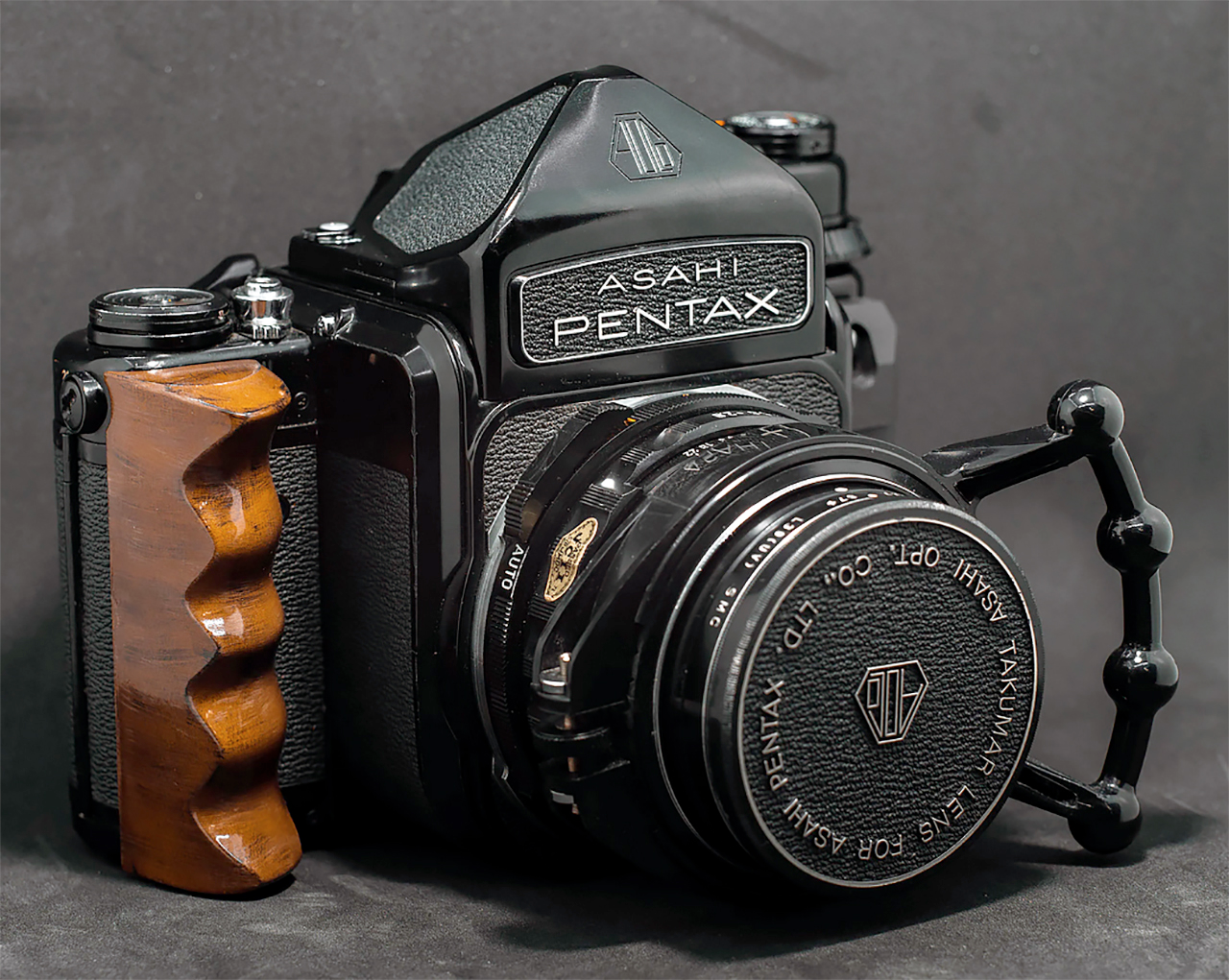
The Pentax 6×7 (called “Pentax 67” after 1990) is a SLR medium format system film camera for 120 and 220 film, which produces images on the film that are nominally 6 cm by 7 cm in size. It originally debuted in 1965 as a prototype.
Merger with Hoya
In December 2006, Pentax started the process of merging with Hoya Corporation to form ‘Hoya Pentax HD Corporation’. Hoya’s primary goal was to strengthen its medical-related business by taking advantage of Pentax’s technologies and expertise in the field of endoscopes, intraocular lenses, surgical loupes, biocompatible ceramics, etc. It was speculated that Pentax’s camera business could be sold off after the merger.
A stock swap was to be completed by October 1, 2007, but the process was called off on April 11, 2007. Pentax president Fumio Urano resigned over the matter, with Takashi Watanuki taking over as president of Pentax. However, despite Watanuki’s previously stated opposition to a Hoya merger, on May 16 it was reported that Pentax had accepted “with conditions” a sweetened offer from Hoya, according to a source familiar with the matter. Pentax was under increasing pressure from its major shareholders, Sparx Asset Management in particular, to accept Hoya’s bid.
On August 6, 2007, Hoya completed a friendly public tender offer for Pentax and acquired 90.59% of the company. On August 14, 2007, the company became a consolidated subsidiary of Hoya. On October 29, 2007, Hoya and Pentax announced that Pentax would merge with and into Hoya effective on March 31, 2008. Hoya closed the Pentax-owned factory in Tokyo, and moved all manufacturing facilities to Cebu, Philippines and Hanoi, Vietnam.
Ricoh Imaging Company
Japanese optical glass-maker Hoya Corporation stated on July 1, 2011, that it would sell its Pentax camera business to copier and printer maker Ricoh, in a deal the Nikkei business daily reported was worth about 10 billion yen ($124.2 million). On July 29, 2011, Hoya transferred its Pentax imaging systems business to a newly established subsidiary called Pentax Imaging Corporation. On October 1, 2011, Ricoh acquired all shares of Pentax Imaging Corp. and renamed the new subsidiary Pentax Ricoh Imaging Company, Ltd. Hoya will continue to use the Pentax brand name for their medical related products such as endoscopes. On August 1, 2013, the company name was changed to Ricoh Imaging Company Ltd. Currently, Pentax DSLRs are manufactured in Cebu, Philippines, while digital Pentax lenses are manufactured in Hanoi, Vietnam, under Pentax Ricoh Imaging Products.
The irony of the situation is that at one time Ricoh was the second largest (after Pentax) camera manufacturer with the Pentax K bayonet, so this corporate merger can be compared to the reunion of relatives who have long lost each other.
To its credit, Ricoh has to admit that it has begun to actively develop the Pentax camera and optics line, reviving the Pentax 645 medium-format system. Now the first Pentax digital full-frame SLR is being prepared for release. However, Ricoh makes the strongest emphasis on SLR cameras of the budget and middle class, providing them with features that are not available to competitors. That is why the Pentax K-S2 is one of the most interesting SLR cameras available on the market today.
ASAHI CAMERAS
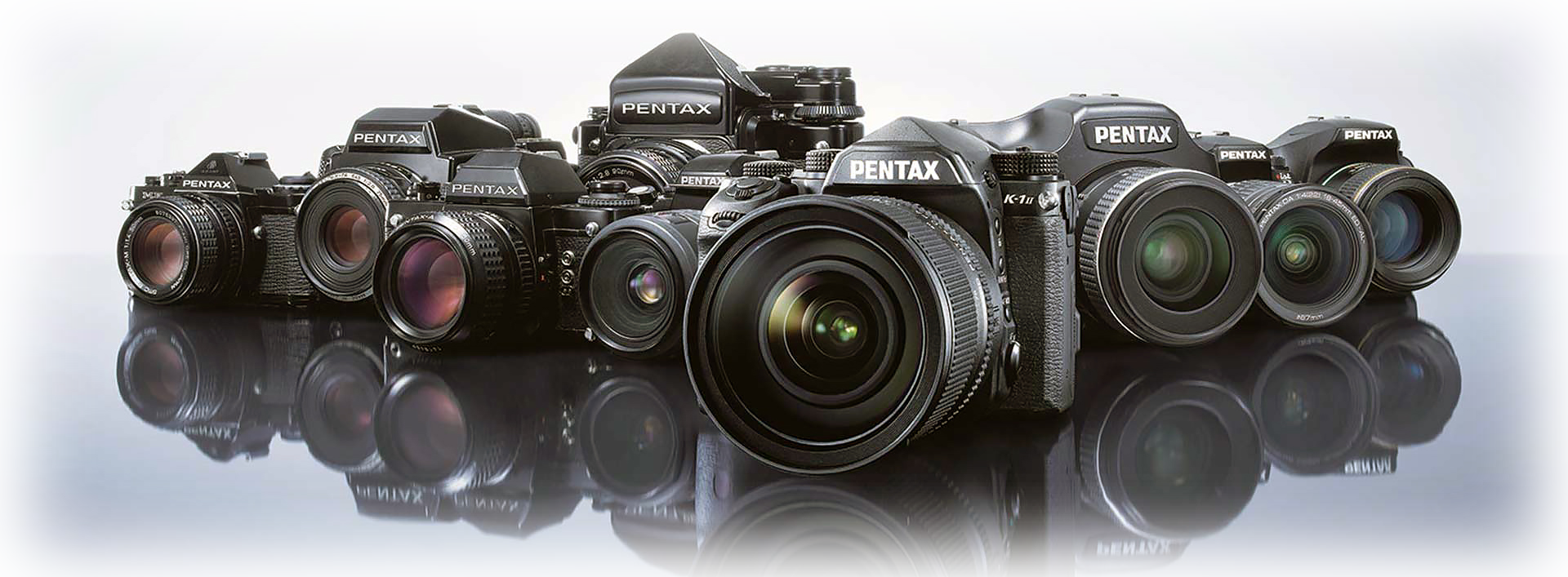
SLR K-mount
autofocus
- Pentax SFX (SF1) (1987)
- Pentax SF7/SF10 (1988)
- Pentax SFXn/SF1n (1989)
- Pentax Z-1/PZ-1 (1991)
- Pentax Z-10/PZ-10 (1991)
- Pentax Z-20/PZ-20 (1993)
- Pentax Z-50p (1993)
- Pentax Z-5 (1994)
- Pentax Z-5p (1995)
- Pentax Z-1p/PZ-1p (1995)
- Pentax Z-70/PZ-70 (1995)
- Pentax MZ-5/ZX-5 (1996)
- Pentax MZ-10/ZX-10 (1996)
- Pentax MZ-3 (1997)
- Pentax MZ-5n/ZX-5n (1997)
- Pentax MZ-50/ZX-50 (1997)
- Pentax MZ-M/ZX-M (1997)
- Pentax MZ-7/ZX-7 (1999)
- Pentax MZ-30/ZX-30 (2000)
- Pentax MZ-S (2001)
- Pentax MZ-6/ZX-L (2001)
- Pentax MZ-60/ZX-60 (2002)
- Pentax *ist (2003)
SLR K-mount
Manual focus
K, M, A, P Series
- Pentax K2
- Pentax K2DMD
- Pentax KX
- Pentax KM
- Pentax K1000
- Pentax MX
- Pentax ME
- Pentax ME Super
- Pentax ME-F
- Pentax MV
- Pentax MV1
- Pentax MG
- Pentax MF
- Pentax MF-1, scientific use
- Pentax Super A, Super Program (USA)
- Pentax Program A, Program Plus (USA)
- Pentax A3, A3000 (USA)
- Pentax P30/P3
- Pentax P30n/P3n/P30t
- Pentax P50/P5
SLR K-mount
Manual focus
Other Series
- Pentax LX
- Pentax ZX-M (MZ-M)
SLR Screw-mount
PENTAX
- Pentax AP
- Pentax K
- Pentax S
- Pentax S1 / H1
- Pentax S1a / H1a
- Pentax S2 / H2
- Pentax S3 / H3
- Pentax SV / H3v
- Pentax Spotmatic
- Pentax SL
- Pentax Spotmatic II
- Pentax SP500
- Pentax SP1000
- Pentax Spotmatic F
- Pentax Electro Spotmatic
- Pentax ES
- Pentax ES II
SLR Screw-mount
ASAHIFLEX
- Asahiflex I
- Asahiflex IA
- Asahiflex II
- Asahiflex IIB
Compact
Cameras
- Pentax Espio IQZoom series (e.g. Espio, Espio 928, Espio 115, Mini, IQZoom 135M Date)
- Pentax PC series (e.g. PC35AFM, PC-300 Date, PC-606W)
- Pentax Mini Sport 35AF (35mm, f/3.8)
- Pentax Pino series
- Pentax Sport (DX)
- Pentax Zoom 60 (38-60mm zoom)
- Pentax Zoom 70R (35-70mm zoom)
- Pentax Zoom 90WR (35-70mm zoom)
- Pentax Zoom 105 Super (aka Zoom 105-R)
1984-2010
Manual Focus
- Pentax 645
1984-2010
AutoFocus
- Pentax 645N
- Pentax 645N II
1969-2010
- Pentax 6×7
- Pentax 67
- Pentax 67 II
1979-1983
interchangeable
lens
- Pentax Auto 110
- Pentax efina
- Pentax efina AF50 (24mm, f/4.5)
- Pentax efina T